BEND, Ore. (KTVZ) – The city of Bend is offering a free indoor water conservation kit, a timely effort to help homeowners conserve water at a time of year when it could lead to lower monthly sewer bills year-round.
The city calculates sewer bills for the rest of the year based on the water used during the winter, December through February. It’s average to determine the sewer charge. Front Control Arm Bushing
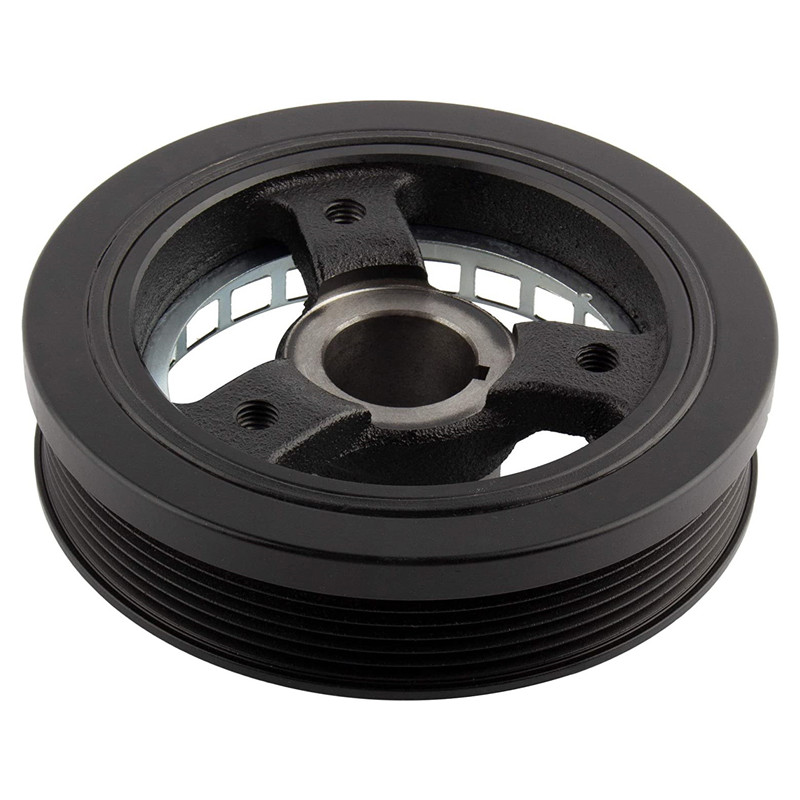
The free conservation kid includes a “water sense” shower head, faucet aerators, a pre-rinse nozzle and a shower timer.
The kids and other free resources and water-saving materials will be available at the city of Bend’s Utility Department at 62975 Boyd Acres Road between Monday and Friday, Jan. 9-13 from 7 a.m. to 4 p.m.
For more information, call or email the city’s Water Wise conservation program at 541-317-3000, extension 2, or email conservation@bendoregon.gov.
KTVZ NewsChannel 21 is committed to providing a forum for civil and constructive conversation.
Please keep your comments respectful and relevant. You can review our Community Guidelines by clicking here
If you would like to share a story idea, please submit it here.
KTVZ-TV FCC Public File | FCC Applications |
Do Not Sell My Personal Information
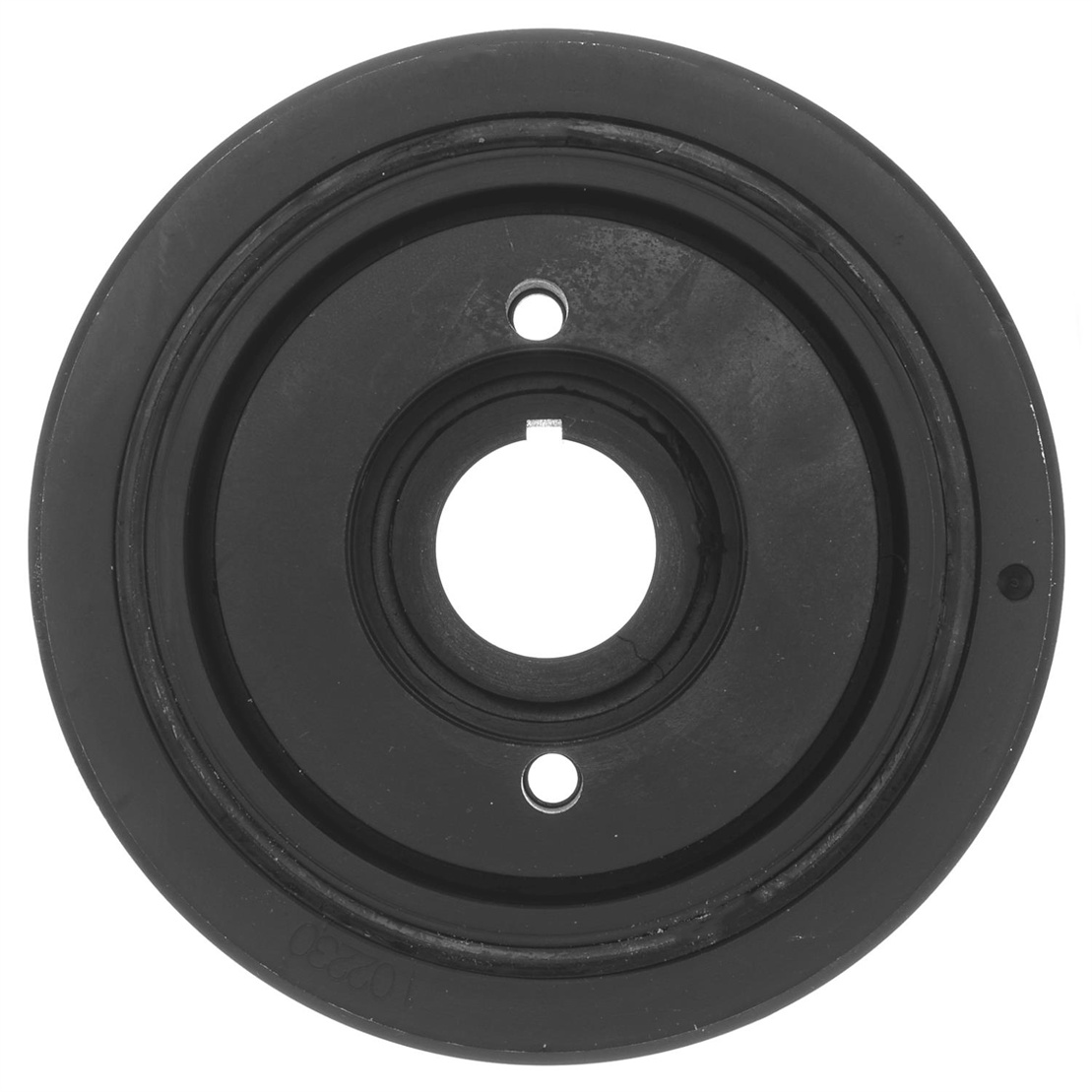
Romac Harmonic Balancer Breaking News Severe Weather Daily News Updates Daily Weather Forecast Entertainment Contests & Promotions