In the second of his two-part feature, Vince Sharpe reviews key elements of SAFed's new guidelines for the safe operation of escalators and moving walks aimed at the competent person carrying out thorough examinations
As explained in part 1 of the feature on safe operation of escalators and moving walks (Plant Engineer, March/April 2012, page 12), in May 2011 SAFed (Safety Assessment Federation) released important new guidelines, for operators, users, manufacturers and competent persons. These replaced HSE plant machinery documents PM34 'Safety in the use of escalators' and PM45 'Escalators: Periodic thorough examination'. Whereas our first article covered looked at issues arising from a design and operations perspective, part 2 here moves on to thorough examinations, largely covered in chapter five of the SAFed publication. With no fewer than 14 sections, this chapter covers an immense amount of detail, providing information not only on what's required of competent persons carrying out thorough examinations, but also guidance for inspection companies, in terms of assessing their own scope of thorough examination. That mission is spelt out in the introductory section, which starts by recommending that thorough examination take place at six monthly intervals or a period determined by the competent person. Any assessment, it explains, should be based on engineering judgement, cognisant of potential hazards and risks – and the process justified and recorded. Relevant plant and equipment issues include: age, type and features; condition of installation; usage of the escalator or moving walk; known problems with the equipment concerned; component manufacturers' recommendations; integrity of the supporting structure; and the extent to which steps and/or pallets require removal. The second section then deals with access to machinery rooms and spaces, guarding and barriers. It makes the point that access should: be safe and be free from tripping hazards and obstructions; be sufficiently illuminated; and have hand-holds and stepping points in good condition. The new guidelines also note that adequate and suitable guards must be in place, including for rotating shafts, sprockets, chains and exposed electrical equipment. Finally, in terms of safety of people in the equipment area, they specify that appropriate and effective barriers should be provided to guard areas where work is being carried out – commonly the entry and exit points. Preliminary examination Moving on, section three discusses the preliminary examination, emphasising first that a thorough examination should include both stationary and running checks. Dimensional checks can be made with the unit stationary, it suggests, noting that useful information can be acquired by doing so. Best advice is that an initial assessment of plant running be made by observing several cycles, listening for unusual noises that may indicate areas of concern. However, care should be taken on units that predominately run in one direction, given that reversing can cause damage. That said, SAFed's document reminds competent persons to include the area around the escalator or moving walk. They should assess everything from information signs to shop fittings, the interface between building handrails and the escalator or moving balustrades, access and egress to the escalator/moving walk, and lighting levels – which should be 50 lux. Electrical safety devices are covered in section four, which states that mechanical and/or electrical functions should be checked at every thorough examination. Where a functional check cannot be completed, the new guidelines advise that a supplementary test can be called for by the competent person. Then in section five, the subject of safety, in terms of effective earth continuity is discussed – the emphasis being on ensuring adequate earthing and bonding of all metalwork, including the truss, by visual verification. Again, the publication recommends that, when this is not possible, a supplementary test be requested. Incidentally, the guidelines recommend that earth continuity testing be carried out at least every five years. It also specifies that all metalwork enclosing electrical conductors have a maximum earth continuity resistance equal to or less than 0.5O. Operational and auxiliary braking systems are covered in section six – with the main recommendation that both (when fitted) be verified as in satisfactory working order, clean, secure and contamination free. The guidelines remind competent persons that linings should be adequate and that any brake monitoring must be functioning correctly. A functional check of the operational brake consists of comparing actual stopping distance with the distances specified in the manufacturing standards at every thorough examination. If an auxiliary brake is fitted then a functional check should be performed under no load condition when the escalator or moving walk is at normal running temperature. Again, when it is not possible for the competent person to carry out a satisfactory test, SAFed's document states that a supplementary test can be requested. Treadways, including steps/pallets, are the subject of the next section. In-depth detail of the checks to be carried out is covered in Annex 1 of the document, which also notes that a record of all checks should be made. In essence, it states that all clearances should be reported and compared with measurements at subsequent visits. A visual examination of the step or pallet cleats should also be undertaken for localised breakage, wear due to abrasion from normal use, or planing of treads, caused by metallic objects. Comb plates are next, with the recommendation including a visual inspection of plate condition, mesh depth and comb clearance. SAFed's publication suggests starting with the unit stationary and then running through the comb plates over several cycles. These checks confirm clearances and alignments to the design standard applicable at the time of installation, it explains. Any fractured, missing, shortened and/or badly worn teeth (such that comb engagement clearance exceeds the maximum) must be considered 'immediate action'. Combs and teeth If the problem is at the exit landings then the comb plate should be replaced immediately, it warns. However, at the entry landing, the comb plate should be replaced as soon as possible, and no later than the next service visit. Note that, if the unit is reversible this is not an option. This section also advises that, if two or more adjacent teeth, or three or more individual teeth, are missing or damaged, the duty holder should be advised to take the unit out of service until the comb plate can be replaced. Section nine moves on to the balustrade panelling and skirting, recommending a visual inspection at every thorough examination. Balustrade panels should be smooth, while butt joints and any others should not present sharp edges or trapping hazards. Specifically, balustrade skirting should be checked for scuff marks, scratching and indentations, and any permanent deflection investigated. All skirting should be vertical and smooth, and again, sharp edges and trapping hazards must be absent. Additionally, the competent person should check for total coverage of any low-friction coatings, as well as absence of contamination. The guidelines warn that skirting coatings are used to minimise friction between the skirt and footwear, so this material should be in good condition and duty holders advised if there is damage. Also the decking should be inspected for signs of damage – particularly any that results in protruding edges likely to catch clothing. The advice is that the duty holder be told of severe damage and the unit removed from service while awaiting repair. Rails and traps The next section discuss handrails, starting with visual inspection, looking for loose or worn beading, cracking, build up of particles and finger traps – between the rail and guide moulding and worn newel panel edges. The guidelines observe that checks should cover tension, slipping, speed synchronisation with steps/pallets and smooth operation. Entry guards should also be inspected at every thorough examination for correct position and integrity. Note that clearances should be as small as reasonably practicable without causing nuisance tripping. Further, if not equipped with electrical safety devices, fitment should be recommended in the competent person's report. Escalator skirt deflector devices are next, and the guide insists that, where these are not fitted, the duty holder be advised that provision of such devices should be considered. Where fitted, however, devices should be assessed to ensure that they are securely fixed, chamfered ends have sufficient clearance to minimise risk and also that no trapping hazards exist. Bristles on such devices should be intact along their entire length, while any damage to, or missing, parts must be considered a serious hazard requiring immediate action. Section 12 deals with surrounds, lighting and signage – also covering circulation areas around top and bottom landings. It advises that the latter should not be compromised, and states that machinery space floor plates should be checked for condition, tripping hazards, gaps, rigidity and security. Lighting levels should also be satisfactory (see earlier) and warning/advisory signs permanently fixed in conspicuous positions, legible and adequately lit. Moving on to the drive system, section 13 advises that the condition and security of the tracks, truss work and associated brackets be checked at every thorough examination. Checks should cover loose fastenings, broken welds, excessive wear, flexing, deterioration and cleanliness. Step chains should also be examined for signs of wear, which may be indicated by excessive clearances between steps/pallets. The guidelines also draw attention to examining for correct tension and carriage position, noting that problems may indicate chain stretch and wear. Any uneven adjustment or wear of chains – often associated with steps/pallets crabbing – should be closely investigated. SAFed's document states that, if there is any doubt about the condition of the step chains then a supplementary test can be requested, with a portion of chain removed and closely examined. As for the driving machine itself, this should be inspected for evidence of backlash, end float, gear noise etc, without dismantling. If serious concerns are uncovered, the competent person should request a supplementary test. Details of such tests can be found in annex A2. Finally, section 14 looks at the control panel, noting that internal parts should be reasonably free of dust and the enclosure complete, including doors and covers – and that these should be earthed. Beyond this, the guidelines advise that, where an electrical hazard exists, shrouds and covers should be in place. Also, where a person is exposed to direct contact when the door/cover is opened, warning signs should be posted, as a short term measure, and a shield fitted. Protection will also be required when the control remains live when the door or cover is opened. Checks should include correct operation of starting control devices and the test/hand control. For sequential units, checks should be made to establish that the upstream unit is shut down when the downstream unit is switched off. As for other specifics, fuses should be of the correct rating and not bridged, and competent persons should watch for phase failure, with thermistor units and overspeed detection units faulty and shorted out instead of renewed. Legislation, duties and responsibilities The new SAFed (Safety Assessment Federation) publication on the safe operation of escalators and moving walks provides legal commentary in chapter two, as well as guidance on duties and responsibilities in chapter three. Regulations first, and for those carrying out thorough examinations, section one points to primary legislation as the Health and Safety at Work Act 1974, which puts a duty on employers to ensure the health and safety of employees and others who may be affected by their activities. The main duties of the act are imposed on a 'so far as reasonably practicable' basis. They are not prescriptive, so following the document and legal obligations outlined normally demonstrates compliance. Then RIDDOR (Reporting of Injuries, Diseases and Dangerous Occurrences Regulations 1995) is covered in section four, with its requirements in terms of the enforcing authorities. Section five then reminds examiners of the need to consider the Management of Health and Safety at Work Regulations 1999, the Workplace (Health, Safety & Welfare) Regulations 1992 and the Provision and Use of Work Equipment Regulation 1998. This section also mentions the Supply Machinery (Safety) Regulations 2008, the Working at Height Regulations 2005 and the Health & Safety (Safety Signs & Signals) Regulations 1996. Now considering responsibilities, section three of chapter three singles out duties on competent persons, and their employing, companies carrying out thorough examinations. All thorough examinations undertaken should, it advises, be sufficiently thorough to assess the condition of the equipment and detect any defects that may pose a risk to people's health and safety. The guidelines recommend that competent persons prepare a report to notify the duty holder of any defects, even if none exist. All existing or imminent defects found during a thorough examination that are likely to affect people's safety, should also be notified to the duty holder, specifically including their urgency and advising if they need to prohibit use of the equipment. Note that, where deemed necessary, the competent persons may identify and call for supplementary tests. escalator step roller

Related Downloads 42652\Binder24-26.pdf
Related Companies Allianz Engineering Society of Operations Engineers
This material is protected by MA Business copyright See Terms and Conditions. One-off usage is permitted but bulk copying is not. For multiple copies contact the sales team.
IRISNDT buys James Fisher NDT
adi VT develops lift training
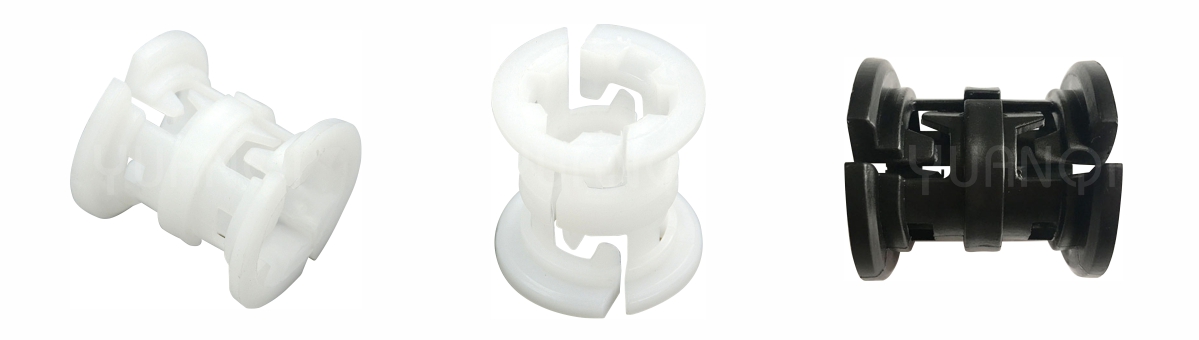
Parts Of Escalator System Legal Report: On the back foot