BestReviews is reader-supported and may earn an affiliate commission. Details
A bench drill design that offers a surprising capacity. CNC knee milling cutter
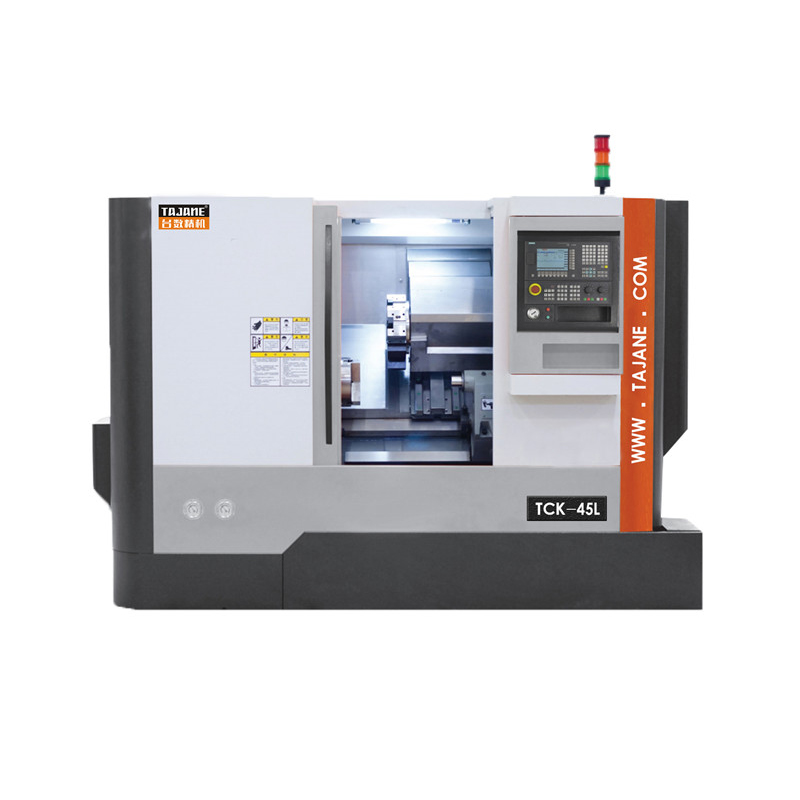
Good range of head and table travel. The large table supports 400 pounds. A few valuable extras make it an excellent value despite the higher price point.
Head rotates 360 degrees but does not tilt. Stand not included.
A precise machine that is great for beginners and experts alike.
The speeds can range from 100 to 2,500 RPM. The head and column can swing 45 degrees, allowing for more precise cuts. Its smaller design allows for it to be moved around if needed.
The size of the machine doesn't make it well-suited for bigger jobs.
A solid machine that works great for smaller projects.
All wires feed into a single box, allowing for easy controls. Can cut into metal, wood, and other materials you need. LCD touchscreen makes it easy to figure out precise settings. Easy to set up and move around.
Can only handle smaller bits, so medium-size jobs may be a hassle.
A decent product that will make cuts you need without hassle.
Belt changes are easy to undertake. Can cut most metals with ease. Adjustments to the angles and cuts are easy to make. The control panel is simple to understand. Emergency stop button is easy to press when needed.
Won't make as precise of a cut as the other products on the market.
An affordable choice that is perfect for hobbyists.
A rugged mill built for hobbyists and smaller jobs. Well-made for a variety of tasks. Jewelry makers love its control and precision for more intricate work.
Occasionally vibrates. Not intended for heavy-duty jobs or milling bulky materials.
We recommend these products based on an intensive research process that's designed to cut through the noise and find the top products in this space. Guided by experts, we spend hours looking into the factors that matter, to bring you these selections.
A milling machine can rip a two-inch groove through solid steel, performing tasks that are beyond the capabilities of even the most powerful drill. At the same time, a milling machine can also carry out delicate operations on the smallest of components. How can both statements be true? Because while a milling machine can be a machine tool weighing several tons, it can also be a delicate instrument used by miniaturists and jewelers.
With such diversity available, it's not surprising that you might face a few challenges when trying to choose the best milling machine for your own use. What you need is someone to cut through the chatter and get to the facts. If you're close to a buying decision, the products in the product list above are among the best milling machines we've found. If you need to know more about milling machines before deciding on a purchase, please read the following comprehensive milling machine report.
A milling machine is often simply called a mill. The market offers multiple types of mills: vertical, horizontal, knee, universal, fixed-bed, planner, floor-standing, benchtop, mini, and micro mills. Some of these names are used interchangeably. For example, the terms “mini mill” and a “benchtop mill” are (usually) used to refer to the same thing.
Large milling machines designed for factories or engineering shops can easily weigh several tons and cost tens of thousands of dollars. They're beyond the scope of this milling machine review.
What we're going to look at in this article are the three most popular types of milling machines found in homes and small workshops: free-standing vertical mills, benchtop (or mini) drilling/milling machines, and micro mills.
You may be wondering what the difference is between a drill press and a milling machine. In truth, the machines share some common characteristics. Both have a motor and gearbox that drive a rotating spindle. Both have a table to support the work. And both are pretty good at making holes.
In fact, many light-duty milling machines are beefed-up drill presses. Much of the time, these machines are called “milling/drilling” machines.
But a genuine milling machine uses tools that don't just cut at the tip like a drill; they cut on the sides, too. A milling cutter can make a hole, but it can also trim the end of a piece of material or cut a slot in it. That groove could have straight or beveled sides, or it could be at an angle.
In fact, there are literally hundreds of different milling cutters available, making a milling machine an extremely versatile tool. It’s arguably the most versatile tool in an engineer's armory.
The type of milling machine you need depends on the type of milling work you plan to do.
If you plan to mill steel components, you'll want a floor-standing vertical mill rather than a mill/drill. The raw material is heavy. The forces generated when machining are considerable. You need something that's absolutely solid, rigid, and capable of powering the cutters you'll use.
The floor-standing vertical mill mentioned above would also handle aluminum, brass, plastics, and composites.
However, if you're only machining these materials and not other materials (like steel), a mini milling/drilling machine would probably suit your purposes.
If you're looking for a hobby/model-making mill, the above considerations won't be quite so important because you'll be dealing with much smaller items.
However, rigidity always has an impact on accuracy, so being able to bolt your mill to your bench is a good idea.
Milling machines can weigh anywhere from 15 to 5,000+ pounds. A micro mill has capacities that are a fraction of those of a vertical mill, but regardless of physical size, accuracy is built on a rock-solid foundation. Usually this is provided by a general structure of cast iron. Not only does cast iron add to the milling machine’s solidity, but it actually dampens the cutting action, absorbing some of the machine’s inherent vibration.
The best micro mills have a cast iron base.
Top mini mills have a cast iron base but may or may not be supplied with a stand. Often, a mini mill comes with a steel cabinet. While not as good as cast iron, it should still be rigid and sturdy enough for the forces generated.
The table is another vital part of an accurate mill. On high-end milling machines, the table is made of hardened, precision-ground steel. Modest milling machines might have a table made of aluminum, which retains its flatness well but is more prone to accidental damage. T-slots are milled into tables to allow for the use of clamps or bolting down machine vices.
The physical size of the items you'll be machining should affect your product choice. Milling machines have several dimensions you need to consider.
On the types of milling machines we’re discussing in this review, the table is fixed, but the spindle (which holds the chuck or collet) goes up and down. This dimension is taken with the spindle at its high point, thus giving the largest gap between the two points. This gives a maximum height of the piece of material (workpiece) you can place on the mill.
In practice, there will be a further reduction, because you need to take into account the height of the chuck or collet and the tool you’ll be using.
A milling machine's table can travel from side to side (longitudinal) and back and forward (cross). These distances define the maximum working area you can use without needing to reposition the work.
It's possible to support a workpiece that's wider or longer than the table. It's also possible that at the furthest extent of travel, you would go past the table edges. However, an overhanging workpiece can make it difficult to operate the machine’s controls. It might affect stability, which would be very dangerous.
In addition, you'll usually want to fix a vise to the table or clamp your workpiece down, so overall table size remains a limiting factor.
The quill travel is a measure of the maximum depth of hole or slot you can cut.
Distance from quill to column is important on a drilling machine, because the table is fixed. On a milling machine it is not, so this dimension has less impact and is often not specified.
You'll also want to check the chuck/collet size. This determines the shank diameter of the tooling you can use.
While all of these dimensions will be vastly different on a micro mill than on a workshop mill, their comparative impact on your choice is the same.
A good micro mill won't have the capacity of a workshop mill, but its feature set should be very similar.
As we've already said, the forces generated by milling can be immense. As a result, powerful motors are needed.
For a mini mill, we wouldn't expect to see less than a one-horsepower motor. For a floor-standing tool, a two-horsepower motor would be necessary. Good micro mills have 100-watt motors, which translates to around 1/8 horsepower. That's quite a lot for a miniaturist tool!
Adjustable speed is a necessity because different materials are machined at different rates. Cutter diameter can also have an effect. Good mills have eight or more speeds available. A few milling machines offer variable speed, allowing you to choose whatever rpm you like (within the machine's maximum and minimum limits, that is).
Whether cutting along the table (longitudinally) or across it, the speed at which the cutter passes through the workpiece (feed rate) has an impact on the quality of the finished piece.
On most mill/drills and micro milling machines, feed is by hand; you turn the handles as quickly or slowly as you need. It's something that requires practice.
On commercial machines, table feed can be powered, as can quill travel (depth). It guarantees constant performance.
A few small workshop mills have powered feeds, but it's not common and usually comes at a premium.
A number of elements are necessary for good milling accuracy. We've already talked about rigidity and the solidity of the machine. Another important element is the accuracy of the controls.
Good milling machines make things easy by offering a choice of either coarse or fine movement on hand controls. A lever allows coarse movement. Release it, and you engage a fine screw thread instead. There will also be depth gauges and depth stops. Precise scales are usually provided and can be marked to 0.001 of an inch. However, actual machining accuracy is largely due to the skill of the operator.
Some premium milling machines have multifunctional digital readouts. While they don't make the machine more accurate, they do make it easier for you to be accurate! Digital readouts should not be confused with CNC (computer numerical control), however. CNC mills are programmable; you put in the cutting parameters and leave the machine to it. That's far more advanced than digital readouts, which give you precise feedback but do not control the milling process.
Materials like steel generate a tremendous amount of heat when being milled. This can distort the work, causing inaccuracies. The waste could burn you or start a fire.
Commercial milling machines have automatic coolant systems built in that pump liquid over the workpiece while the machine is cutting.
Separate pumps are an option that is well worth considering if you're going to do this kind of work.
Even the smallest milling machine requires caution. Always wear goggles and a face mask when milling.
Make sure any and all guards are in place before beginning work. Never be tempted to remove them.
Avoid operating your mill if you're feeling ill or otherwise unwell.
Make sure your work area is clean and uncluttered.
Coolants can cause skin irritation and dermatitis, so put on a barrier cream to protect your skin if you’re working with them.
Waste from milling metal is extremely sharp, so be careful with collection and disposal. Other materials have recycling value, so check with your local authority.
A milling machine is a complex, high-precision tool. You should expect to make a considerable investment. Cheap mills do exist, but we have serious doubts about their durability and ability to produce accurate results.
A good micro mill that would satisfy the demands of miniaturists and model makers will cost between $400 and $500. If you were to opt for something a little larger or with a digital readout, you could easily spend $1,000 on a micro mill.
If you're shopping for an entry-level mini mill – also known as a drilling/milling machine – you'll need in excess of $2,000. For a floor-standing milling machine, expect to spend $5,000 or more.
The good news is, you have a tremendous amount of choice when shopping for a milling machine. Think about the materials and sizes you'll be working with and the degree of precision you need. Use this milling machine guide to help you make your choice. If you choose wisely, the result will be a milling machine that should last you a lifetime.
Get emails you’ll love .

CNC gantry milling Machine Learn about the products you’re wondering if you should buy and get advice on using your latest purchases.