How has 3D printing become a game-changer in producing spare parts for trucks?
Daimler Truck has been a pioneer for industrial 3D printing in the automotive sector for years, ever since it first began focusing on the potential of the digital production technology in 2016. Since then, its Omniplus service brand has designated around 40,000 bus and touring coach spare parts from its Mercedes-Benz and Setra brands as suitable for 3D printing. Thus far, the key focus for 3D printing deployment for Daimler has been on spare parts. Auto Parts

Daniela Rehm, Product and Marketing Manager at Daimler, discussed the merits and achievements of the company’s 3D printing adoption at Formnext, Europe’s largest additive manufacturing (AM) trade show. “3D printing is a game changer,” she said. “We have come all the way from rapid prototyping to direct manufacturing of high strength component parts, customised spare parts, printing licenses and so on. With 3D printing, we have achievements on both the ecological and economical sides. On the economical side we have experienced cost savings through scrapping storage costs and tooling costs, and time savings which is closely connected to on-demand production. With AM, we can reduce parts to the right amount at the time that we really need. On the ecological side, there is one main important point, which is less waste.”
Initially, Daimler’s 3D printing pipeline started small, but has since grown significantly. “We currently have more than 600 different spare parts that are released and produced only with AM,” Rehm said. “Of these 600 parts, we have more than 70,000 installed in our Mercedes-Benz SR buses. With the implementation of AM, we have been able to cut costs in tooling and storage, and this has given us annual savings from inception. And we are expanding our digital warehouse continuously. With additive, we have transitioned from a physical to digital spare parts business model.”
Daimler’s digital warehouse includes both regularly required spare parts as well as rarely required parts for special customer requests. The virtual warehouse forms the basis for 3D printing license management, which has further optimised the rapid availability of spare parts for the company’s customers.
“Combining the datasets for digital parts to create part digital twins gives us the recipe for printing,” Rehm added. “Through the digital warehouse, you can upload data files for parts, analyse features, introduce branding and so on. Parts can then be ordered directly from the digital warehouse. Not only is the digital warehouse important when we’re talking about moving fast, but we can also create new business models to realise decentralised production.”
Last year, Daimler introduced a new license management for spare parts to enable owners of Mercedes-Benz and Setra buses and coaches to produce spare parts quickly and cheaply at their own premises. All the user needs are a certified 3D printer, a one-off registration process, and a license for the required part in the required quantity to create their own ‘mini parts factory’.
“3D printing licenses offer our customers the opportunity to buy a 3D printing dataset in combination with the recipe of how to print the parts, so that they can print their spare parts themselves,” Rehm explained. “This offers several advantages, such as faster availability, cheaper prices, and the reduction of transport costs and times. We also offer our additive manufacturing solutions consulting unit which provides different services to customers alongside our centre of competence. We can offer individual services and workshops to fit the needs of our customers, as well as sharing our failures and learnings so that they can improve AM adoption within their setup.”
And Daimler’s work on AM adoption doesn’t stop there. “AM is the future of our company,” Rehm added. “And this is the case not only for Daimler, but for a lot of other companies, too. 3D printing enables us to be more flexible, producing parts in the amount that we need and in the time required. We can react faster, because we can realise the possible delivery of parts, and of course, there are many cost saving advantages. We are also working in a more environmentally-friendly way as 3D printing is a more sustainable technology from the beginning. The digital twin and warehousing innovations are helping us to realise many benefits for our customers.”
To receive our free weekly NewsBrief please enter your email address below:
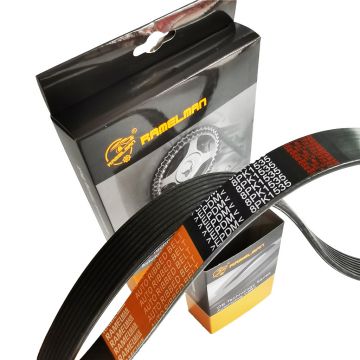
Excavator Engine Fan Parts Belt © Setform Limited 2019-2024 | Privacy policy | Archive