During its Mobility Days in Austria, Engel and KTM Technologies debuted an all-plastic molded motorcycle seat base produced via a tape-sandwich process that can run in a standard molding process.
Development partners Engel and KTM Technologies introduced a “tape sandwich” process and design that the company’s say creates molded plastic parts with greater stiffness, less weight and low production costs. The aim of the joint development work, which is now commercially available, was to make a motorcycle seat base that’s more compact and lighter while retaining the same mechanical properties of its predecessor. Even in motorcycles, drivetrain electrification requires accommodation of an increasing number of electronic components. Belgium toolmaker Feronyl provided tooling for the project. Tpe Injection Molding
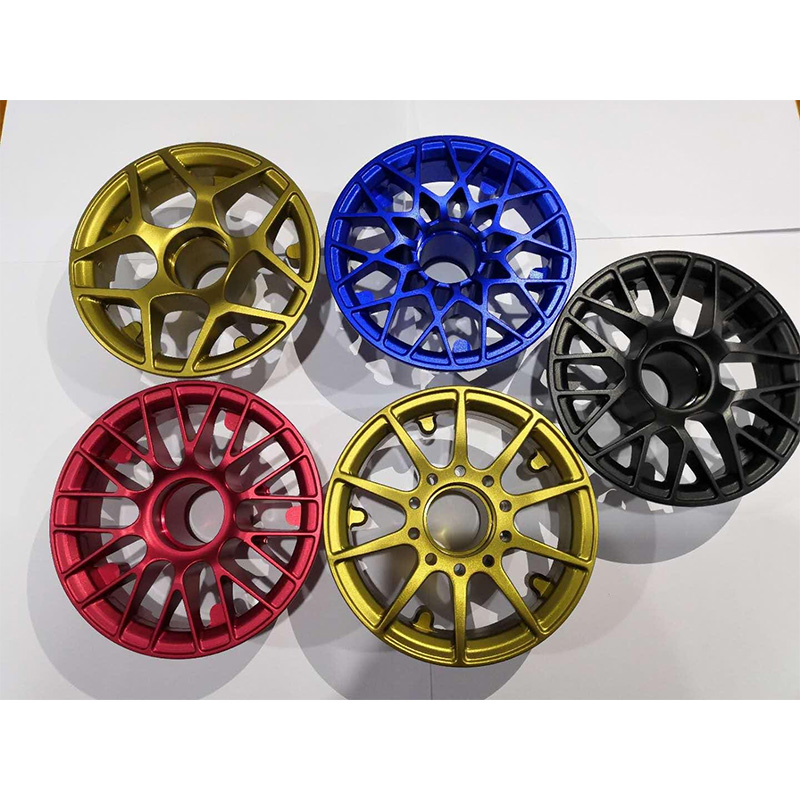
Engel and KTM Technologies introduced the sandwich technology at Engel’s mobility days event. Photo Credit: PT
This advance was shared at the two day Mobility Days event that Engel and KTM Technologies jointly organized. Bringing together more than 500 experts from the automotive, micro-mobility, aerospace and transportation sectors, the event featured presentations in Linz and machine demonstrations at Engel’s large-machine facility in St. Valentin, Austria.
Previous KTM seat bases were thicker molded components, featuring rib structures to boost rigidity, with thicker sections measuring in at 9 mm. To reduce the necessary installation space and create more room for electronics, KTM Technologies cooperated with Engel on a composite part utilizing tape-sandwich technology. The average thickness of this new part was just 2.5 mm.
KTM says the electrification of drives for motorcycles requires more space, forcing it to make room in new designs.
The tape sandwich process uses thin, single-layer reinforcement materials such as tapes and fabrics with a polypropylene matrix that are inserted into both cavity halves of the injection mold without preheating. The mold closes, polypropylene is injected resulting in a “sandwich” structure. The mechanical properties of this structure allow the parts to satisfy the stiffness required for motorcycle seat bases with a single-layer UD-tape. Compared to more conventional fiber-reinforced composite plastics processing methods, included preheating organosheets via an oven prior to mold insertion, this process uses less energy and applies a standard molding cell.
The seat bottom that was created provides identical stiffness, while reducing installation space by 66%, with weight reduction of 26% The companies note that the sandwich structure can utilize standard thermoplastics but still be exposed to high mechanical stresses. At end of life, using the same resins for the tape and the matrix allows the part to be more easily recycled.
In a press conference at Mobility Days, KTM’s Franz Füreder described the opportunity at hand in the changing mobility space. “New drive concepts and autonomous driving change mobility requirements profoundly,” Füreder said, “and they require new material and manufacturing concepts. This creates major opportunities for plastics. Polymer materials are lightweight by definition and support a sparing use of raw material and energy, processed by injection molding, this opens up mass markets.”
KTM’s motto is “ready to race”, which is the goal for the new sandwich composite technology.
One of the more prominent trends in processing is the need for higher plastic pressures to mold parts.
Flashing of a part can occur for several reasons—from variations in the process or material to tooling trouble.
Start by picking a target melt temperature, and double-check data sheets for the resin supplier’s recommendations. Now for the rest...

Prototype Plastic Molding © 2023 Gardner Business Media, Inc. Privacy Policy [Log On]