Please ensure that JavaScript is enabled in your browser to view this page.
While most makers are at least somewhat familiar with the concept of using a soldering iron to melt solder onto through-hole components, the world of surface mount is quite different. The process normally involves spreading a thin layer of solder paste onto the PCB's exposed pads, placing the components, and then reflowing, or melting, the solder paste to make the connections. This last step requires several temperature stages to be reached over the course of a few minutes which ensures solid bonding and prevents component damage. Type C Reflow Soldering Machine
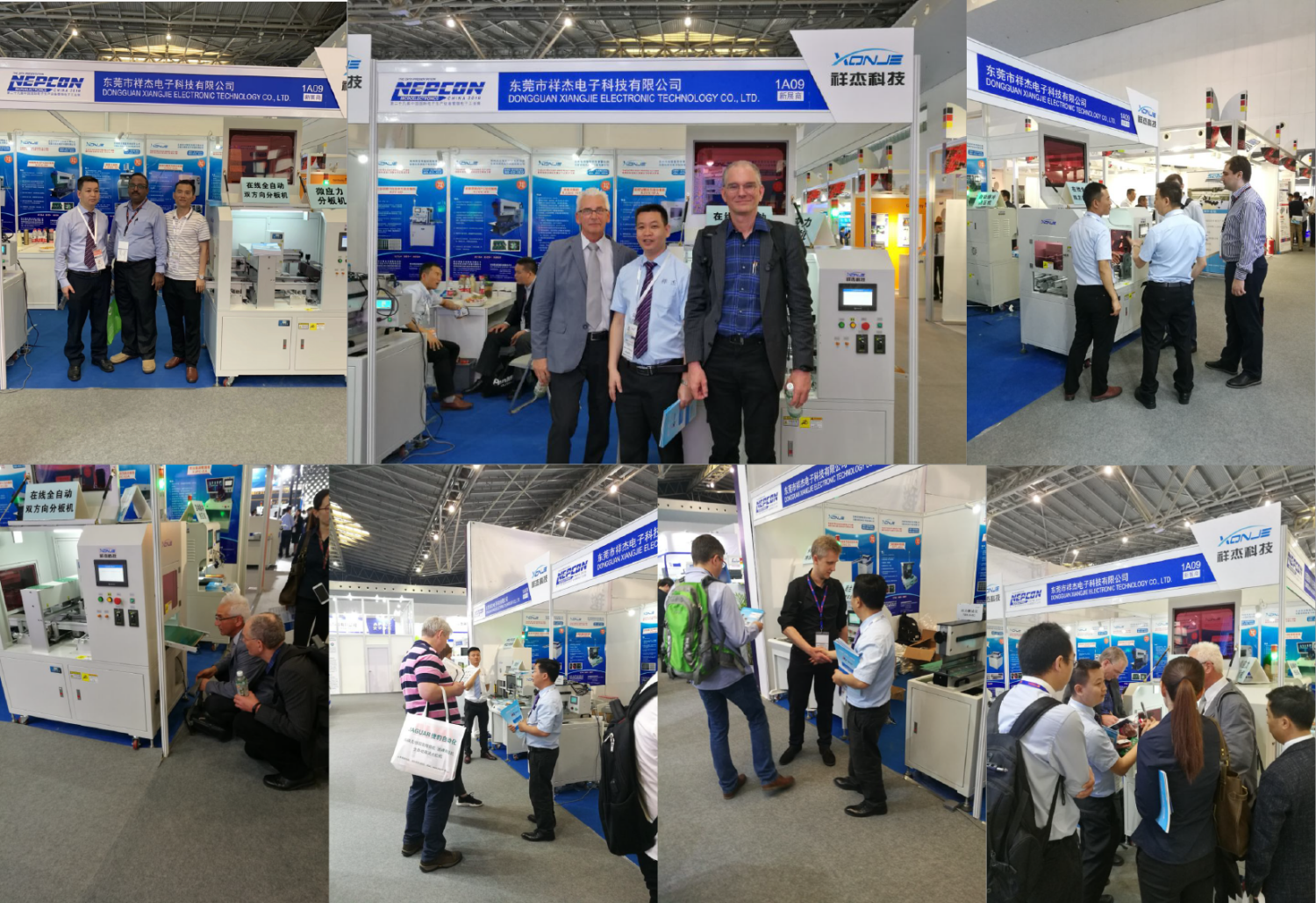
Some existing projects utilize repurposed toaster ovens with modified timing circuitry, but Crimson Dynamo wanted something that could be easily expanded to accommodate a wide variety of PCB sizes. His idea was to build a reflow hotplate that heats boards via direct contact rather than hot air- all while having intelligent profiles that are applied over time.
To generate enough heat, Crimson went with a pair of 400W, 240V heater plates along with a 10A relay, thermistor (temperature sensor), and steel plate for each. When current is applied to the plates through the closed relays, they are able to quickly ramp up their temperature which can then be tempered through a microcontroller and thermistor. A cut-out protector was also placed inline to remove power from the plates in the event of thermal runaway.
Based on an ESP32 Dev Kit V4, the user interface board is responsible for presenting options to the user via a 0.96" OLED screen and handling the selection. Once an option has been chosen with a rotary encoder, the microcontroller closes the relays and then switches them on or off depending on the current thermistor reading and the target temperature from the profile thanks to a PID loop.
The high voltages and temperatures involved in this project led Crimson to add several important safety features to his enclosure. First, the hotplates are raised with a series of standoffs from the ground, thus preventing them from heating their surroundings too much. Second, all of the high-voltage internals are recessed into a 3D printed plastic enclosure to help reduce shock risks. And finally, the metal structure inside is fully grounded as one more safety measure.
Crimson began by calibrating his thermocouples with a test mode he programmed which slowly ramps up the voltage being applied to the hotplates. It then allows the user to measure the real hotplate temperature with a thermometer and record the two values. This continues until degree values ranging from 25C all the way to 200C have been created and associated with each other in code. After calibration has finished, thermal profiles, or arrays of temperatures over time, can be loaded into the program and selected from the screen.
To read more about this smart hotplate reflow station, check out Crimson Dynamo's project write-up here.
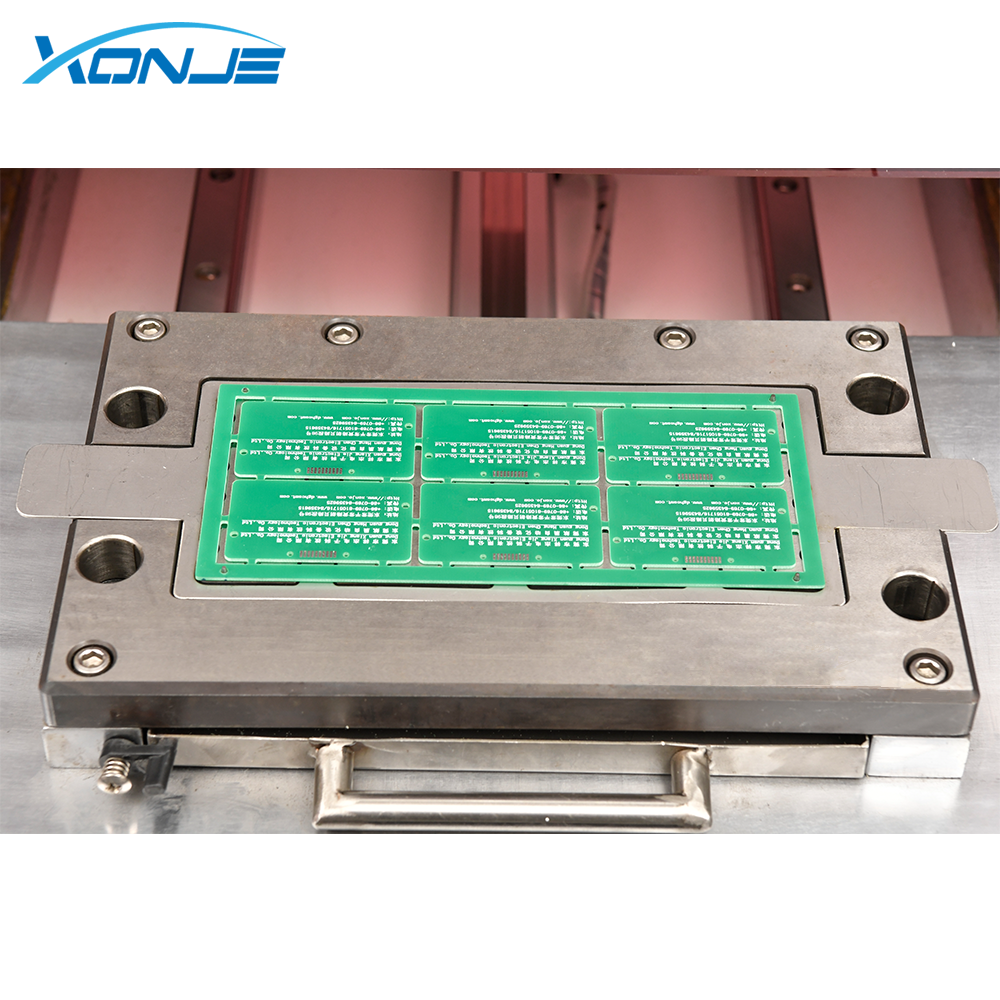
Type C Soldering Machine Hackster.io, an Avnet Community © 2024