Connect Read Watch Broadcast Contact
The advantages of changing from roads to rivers wherever it is possible are obvious: a ship can take much more payload and wouldn’t cause extra traffic on the roads. The use of a new material could even make ships greener Decoration Aluminum Foam
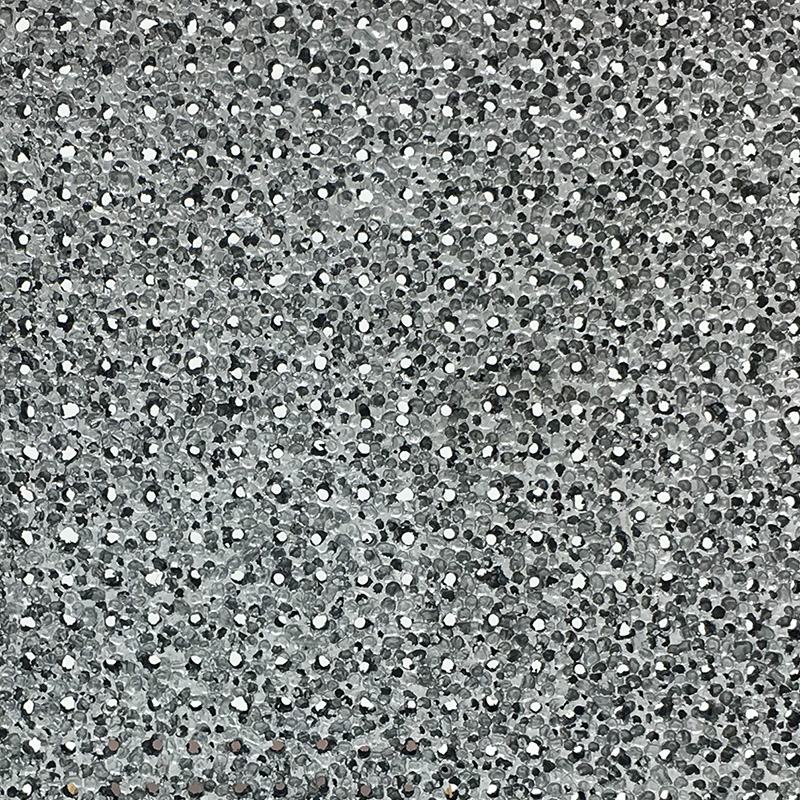
The vessel Hintsanen designed fulfils all necessary requirements: It has a capacity of over 5000 m3 and runs with natural liquid gas (LNG) to avoid any pollution in case of a spill. It is operable year around, has a draft of less than 2.4 metres and sufficient self loading and discharging capacities but the main aspect is its weight.
At the Fraunhofer Institute for Machine Tools and Forming Technology in Chemnitz, Germany, engineers work on ways to make this vessel much lighter. Their aim is to cut the weight by 30 percent. To reach this aim they want to replace some steel parts with a super light but stiff material: aluminum foam. Dr Thomas Hipke from the department of lightweight structures at the Fraunhofer Institute for Machine Tools and Forming Technology in Chemnitz, Germany is leading the tests with the material.
Have you already managed to attain your objectives, i.e. a 30% weight reduction? We are right now able to save at some parts of the ship 20 to 25 percent weight in the bottom section. At the side walls we gained a weight reduction of 27 percent comparing the old wall with the new one. Summing up the savings in weight for the whole ship there are several thousand tons that could be reduced.
Can you shortly describe how this new material works? Aluminum foam sandwiches are made with an aluminum powder that is enriched with a foaming agent: titanium hydride. The powder is pressed into bars and then placed between steel sheets. In our tests, a steel mould is filled with a couple of aluminum bars, the heat-resistant mould is then closed. The mould is placed inside an oven heated up to over 650 degrees Celsius. A couple of minutes later the aluminum in the mould expands like a dough. A lot of small pores are generated inside and the material gets a sponge like structure. After cooling down for a few minutes the aluminum foam becomes stiff. Its structure is similar to one of a bone: it combines a very light weight with a high stiffness.
Is the material strong enough? A crash test with the same weight has shown that the material doesn’t break. It is only deformed. A good attribute for a ship hull, especially in areas with ice in the cold months.
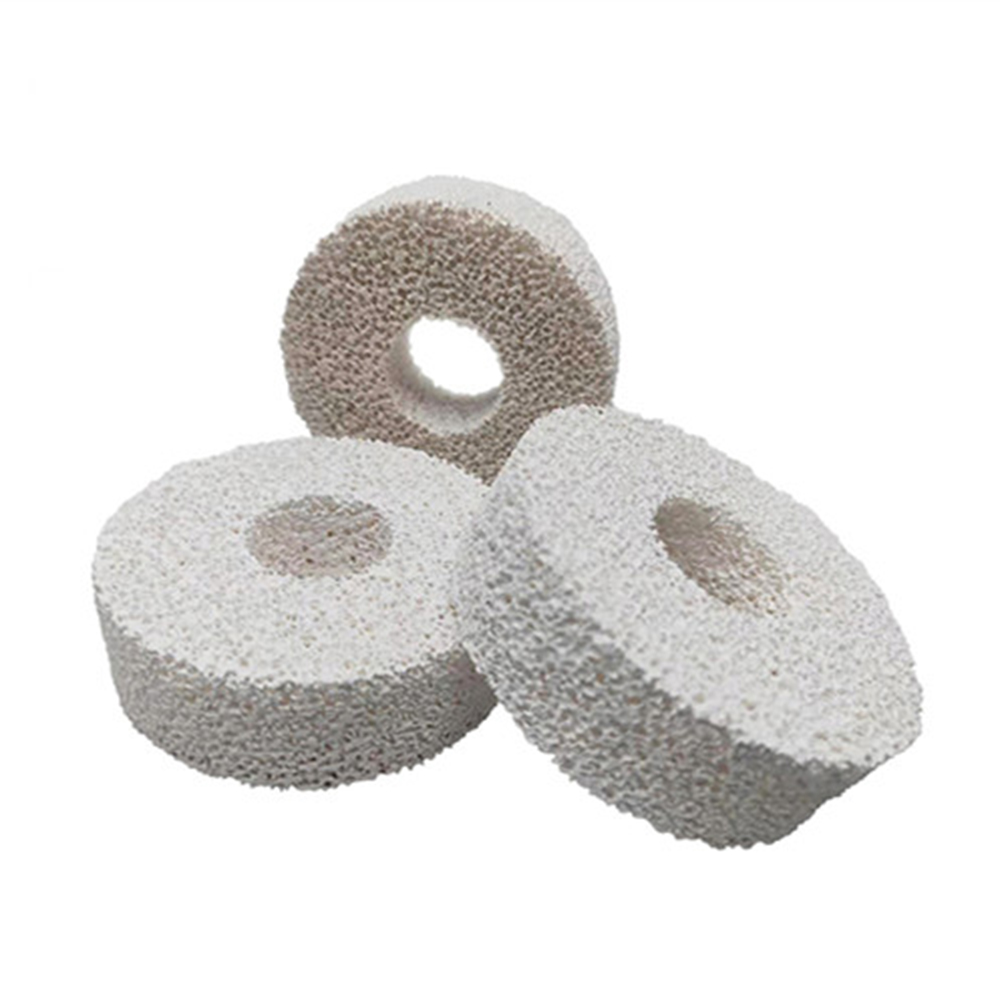
Steel Foam What are you expecting from the achievements of this research? We hope to create a new generation of lightweight construction ships that aparts us from competitors. We need such innovations in Europe. Only with innovative products we can sell something in the future and also live from that.