Mold manufacturers need to be able to differentiate themselves from the crowd, and that often means getting mold designers and engineers information on new materials and processes.
Mold manufacturers need to be able to differentiate themselves from the crowd, and that often means getting mold designers and engineers information on new materials and processes. Cnc Mill Projects
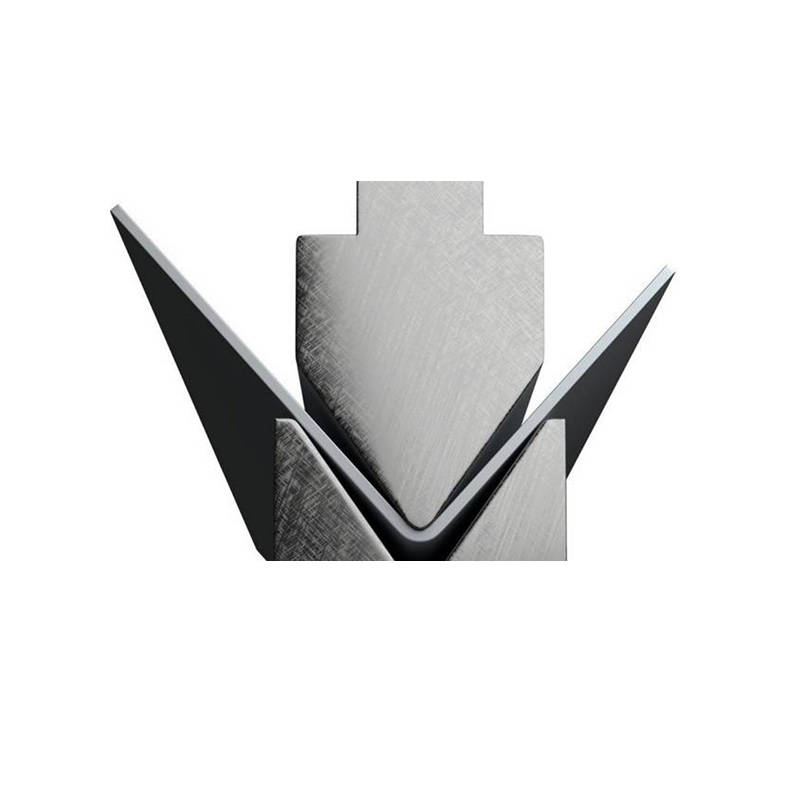
(Top) Proper Group's moldmakers are trained in the latest mold making technologies, such as 5-axis machining. (Below) A Proper Group moldmaker inspects mold components on a CMM.
In fact, it can be argued that mold designers and engineers need to understand new processing and materials technology as much as they do the actual molds. One way that mold manufacturers have found to educate their tooling designers and engineers is by working in collaboration with materials and processing machinery suppliers. Recently, officials of Trexel Inc., suppliers of the MuCell microcellular foam technology, announced that training for the initial class of MuCell-certified tooling engineers and designers was recently completed at Proper Group International.
Proper Group is headquartered in Warren, MI, the heart of the North American automotive manufacturing region, and specializes in molds primarily for the automotive market. The company also has a molding facility in Anderson, SC, and a mold manufacturing facility in Shenzhen, China, to serve the automotive markets in those regions. "The Proper Group is an ideal partner for the MuCell technology as we look to accelerate penetration of the MuCell process in the automotive market," said Steve Braig, president and CEO of Trexel. "They're a technology leader with an established track record."
Joe Grippe, VP sales and marketing for Proper Group Intl., said that like most manufacturers, "We're trying to make things faster, cheaper and lighter. MuCell is a part of that effort, and is a key to our strategy." But unlike most mold manufacturers, he said, "We're on the leading edge of a number of technologies, so MuCell is a natural for us. It helps us differentiate our company by bringing something innovative to our customers."
Proper's management is very proactive in seeking out new technologies - not just mold building technology, but to implement and optimize technology for its customers as well. "For our customers to get the full value of the technology, our designers and engineers have invested the time to become educated about the process so they can make better molds that in turn make better products for the end customer, which makes this partnership critical," explained Grippe. "It's about more than plugging MuCell onto the mold. Without a true collaboration the optimization of the mold and process won't happen."
Trexel announced the formation of a strategic partnership with Proper Mold at the K2010 trade fair in Düsseldorf, Germany, last October. Grippe said that the training program was a part of that strategic partnership. "We've gone through the stages of learning - the macro view of MuCell's technology and benefits - into a program that involves everyone at Proper Group," said Grippe. "The mold designers, the sales force, process engineers, and product development people have all been engaged in the training process from Mucell, how it works and what it takes to optimize the entire process from the product design, mold design and engineering to the processing to take advantage of the technology."
For these strategic partnerships to be effective, they must be mutually beneficial. Grippe said that his company's suppliers are more open to new ideas from the moldmakers as well. "We're working from the OEM and the large supplier level," he explained. "The automotive makers are used to the Tier One suppliers bringing new technology to them. We're getting more involved with the automotive OEMs but also getting more involved with the Tier Ones. We're trying to invite them into our collaboration. We're trying to find the best fit for what Mucell has to offer."
For new technology, such as MuCell, to work, everyone throughout the supply chain has to understand the technology. "With Mucell we have to deal with those who are running the technology - the processors," Grippe commented. "We can't leave anyone out so we're educating everyone. The Proper and Trexel relationship depends on educating the supply chain. We'll show them, prove to them, invite them to see the MuCell technology, and then ask how it can benefit them. Faster, cheaper, lighter is a good idea but how will it work for their product application - or why it won't work. It has to be the right application for the technology."
Trexel's Braig added that a "significant number" of the Proper Group's mold designers have acquired the know-how to design tools that maximize the benefits of the MuCell process. "This newly adopted competency combined with multiple MuCell technology-equipped machines installed in their tech center provides OEMs and Tier 1 molders with an excellent, local process development capability," Braig said. "They are now able to design the tools to bring leading-edge MuCell applications to fruition as quickly, efficiently and in as cost-effective a manner as possible. Between our two companies we're not able to work with our automotive customers on new MuCell development programs, from initial part design through to tooling, trials and demonstration programs."
Proper Group also has a partnership with machinery supplier KraussMaffei, in a strategy inked last summer. The expanding demand for polyurethane tooling in the North American market resulted in KraussMaffei outgrowing its Novi, MI, facility for PU tooling. The company moved into a new 50,000-square-foot facility, the North American Polyurethane Tooling and Technology Center, located adjacent to Proper Group's headquarters and Tooling Technology Center.
According to KraussMaffei, the facility will have the capabilities to design, build and validate foam tooling, punch tooling, perform spray skin trials, as well as the new multi-component process, "SkinForm." The "SkinForm" process is two-shot molding technology in which a thermoplastic material is injected first and then overmolded with polyurethane in the same tool.
Grippe explained that Proper Group's partnership with KraussMaffei integrates reaction injection molding (RIM) and standard thermoplastic injection molding. "Proper's tooling engineers are working closely with KraussMaffei in a real integration strategy," he said. "It's a bit different than most partnerships, but the goal is to bring a new technology to the market and support the benefits of this technology to our customers."
The various relationships that Proper has initiated help to make these technologies work in real-world applications and optimize them. For example, KraussMaffei decided to aggressively target new applications and use Mucell technology wherever it can. That works with Proper Group's culture, one of collaboration in which designers collaborate with sales people and engineers. It is a culture that is management driven throughout the organization. "Geoff O'Brien, our president, sets the pace for this and he's created a company that thrives on these challenges," states Grippe.
O'Brien commented that, "Our strategic partnership with Trexel is working. We now have MuCell-trained engineers along with multiple MuCell-enabled machines now in operation. We expect to enhance our value proposition for our customers on new tools that will be designed specifically for the MuCell process."
Mold manufacturers who provide more than just molds and "push the envelope" are finding new ways of working with technology that will not only benefit customers but also will drive new business and grow the company. "We are more of a solutions provider," said Grippe. "At the end of the day we still deliver a mold, but it's more about delivering a solution-based system. If you're not aggressive and willing to embrace new technology and make it a priority, you limit your value to your customer base."
Until she retired in September 2021, Clare Goldsberry reported on the plastics industry for more than 30 years. In addition to the 10,000+ articles she has written, by her own estimation, she is the author of several books, including The Business of Injection Molding: How to succeed as a custom molder and Purchasing Injection Molds: A buyers guide. Goldsberry is a member of the Plastics Pioneers Association. She reflected on her long career in " Time to Say Good-Bye ."
BASF CEO to Present Keynote at NPE2024
Breaking News in Flexible Packaging February 2024
Leaving the Automotive Sector Was the Best Decision This Custom Molder Ever Made
New Awards Program Celebrates Sustainable Packaging
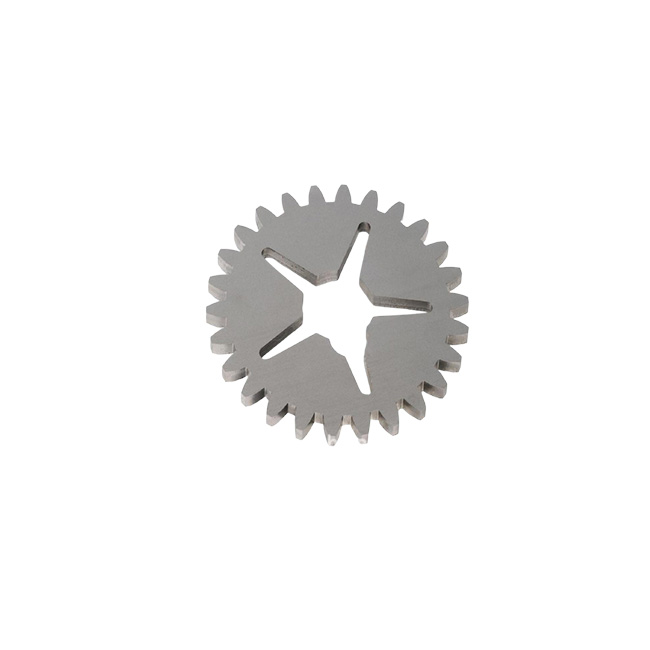
Molding Process Copyright © 2024 All rights reserved. Informa Markets, a trading division of Informa PLC.