As one of the top producers of machine tools in the world, Taiwan has a long history of developing and supplying high-quality equipment to global manufacturers. And as the industry continues to recover from COVID-19 and recent economic challenges, Taiwanese companies are well-prepared with a host of cost-efficient machining solutions, including the latest automation and digital technologies, to help North American manufacturers improve their efficiencies and bottom lines, while exceeding customer expectations.
There are more than 1,500 machine tool and accessories manufacturers in Taiwan, and the U.S. is the sector’s second largest export market. Each company offers unique strengths, including the four highlighted here. China High Speed Vertical Machining Centers Manufacturers
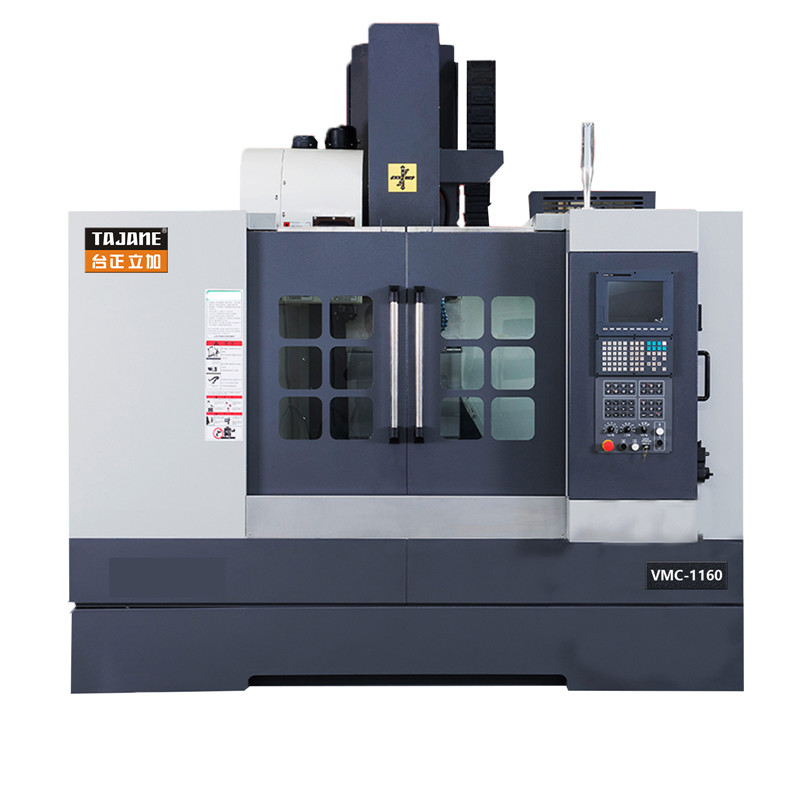
Victor Taichung (www.victortaichung.com) and its FORTUNE International subsidiary specialize in multi-tasking CNC machines, five-axis machining centers and horizontal turning lathes. The company showcased its latest innovations at the European Machine Tool Exhibition in Germany (EMO Hannover) in September, including the VMT-X260 multi-tasking machine with a Siemens SINUMERIK ONE five-axis control. The VMT-X260’s turning spindle is available with either a 10” chuck (3,500 rpm) or 8” chuck (4,200 rpm), along with a 12,000 rpm milling spindle with HSK-T63 tooling.
Meanwhile, the all-new Vturn-A260 with a belt-driven spindle features a 750-mm Z-axis travel that will be nearly doubled to 1,300 mm in 2024. The system has a FANUC control with a 10.4” screen, rotary operation panel, front pressure gauge and a built-in LED light.
Among Victor’s other competitive advantages are its high-level of vertical integration and automation expertise, notes Wayne Hsueh, the company’s sales director.
Victor is one of only two machine builders in Taiwan with its own foundry to make castings, and it has the ability to grind and machine critical components—such as the headstock, spindle and turret—to enable better control of the process and eliminate potential supply chain issues. The latest advances are demonstrated at the company’s Smart Factory that opened in 2020.
Faced with tight operating margins, manufacturers are increasingly turning to top-tier equipment suppliers for integrated solutions that meet exacting specifications. This is especially true for aerospace, medical and electric vehicle applications, according to Jerry Chen, GM for AccuteX Technologies (www.accutex.com.tw).
Originated from the research and development team in Taiwan’s Industrial Technology Research Institute (ITRI), AccuteX has more than 30 years of r&d experience in the field—offering in-house design for CNC controllers, linear motors and discharging power modules. The company is known for its wire electrical discharge machining (EDM), which Chen notes allows for thinner walls, small radii corners and greater part geometry flexibility with less material waste.
“Wire-EDM is the best way to cut Inconel and other advanced aerospace materials,” he says. And for EV battery pack components, AccuteX’s AP series provides tolerances within ±2 micrometers, which is more than twice as precise as the ±5 micrometers requirements for traditional automotive applications.
In addition to its expertise in new product development, AccuteX provides retrofit solutions to help customers extend the life of existing equipment. By replacing, repairing and updating key hardware and software components, Chen says manufacturers can realize as much as a 20% improvement in efficiency.
The company’s new AZ machines also provide greater automation and EtherCAT (Ethernet for control automation technology) capabilities. This allows for better cutting performance and untended multi-workpiece production as part of an Industry 4.0 environment.
High speed and high performance. That’s the philosophy behind Buffalo Machinery’s high-end AXILE line of 5X vertical machining centers. Short for agile axis, AXILE boasts high-speed, five-axis capabilities for what Buffalo (www.buffalo-machinery.com/en/) refers to as Smart Machining Technology (SMT) for integrated Industry 4.0 manufacturing.
Complementing the company’s main MICROCUT line, AXILE’s high-performance capabilities are geared toward high-speed milling machines and five-axis machining centers for aerospace, medical and die molding applications. AXILE also helps customer sustainability goals by reducing energy consumption.
Buffalo Machinery’s latest DC4i and G6i AXILE five-axis machines feature the company’s digitalized intelligent automation ART™ solutions that provide real-time monitoring and automatic control to boost production efficiency and reduce energy consumption.
The DC4 has a 400-mm table; the compact G6 is a gantry-type VMC with a table diameter of 600 mm and built-in spindle that moves along the X, Y Z-axis, while the table moves in rotary C-axis and swiveling A-axis. Buffalo plans to launch an all-new AXILE machine and digital service in 2024.
Strong technical support with knowledgeable service is always a good recipe for success. For Goodway Group (www.goodwaycnc.com), it’s part of the company’s DNA—throughout a product’s entire lifecycle.
“We still have customers using a 28-year-old machine, which we provide service and support for,” says Jeffrey Liu, vice president of Goodway’s Yama Seiki USA unit. In fact, he adds, Goodway maintains more than 100 machines and some 3 million spare part components at its U.S. warehouse.
Goodway ships more than 1,500 CNC turning machines per year to some 30 countries worldwide. The company’s Swiss-style turning machines range from 13 to 42 mm and include sub-spindles and back-end tooling systems.
But Goodway’s new GMT-2000 series offers the most flexibility. It teams the functional characteristics of turning and machining centers with nine-axis control and five-axis machining capabilities. In addition to reducing the number of machines and manpower requirements by two-thirds, the integrated system can cut workpiece time setting by 75% and the number of fixtures by 80%.
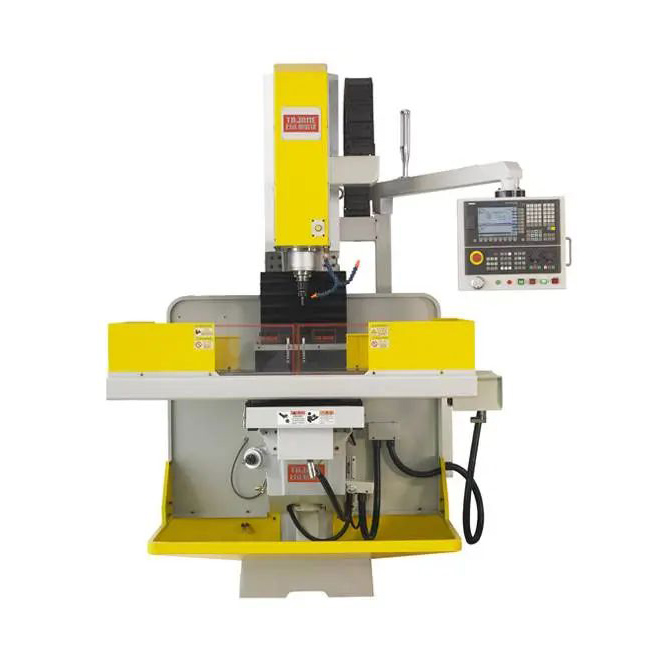
Manual Milling Machine Yama Seiki also has direct access to the Goodway Turning and Awea Milling r&d centers. This allows the company’s design engineers to access the latest manufacturing trends, quickly exchange information with customers and launch new products on a yearly basis.