Making battery packs is a common pursuit in our community, involving spot-welding nickel strips to the terminals on individual cells. Many a pack has been made in this way, using reclaimed 18650 cells taken from discarded laptops. Commercial battery spot welders do a good job but have a huge inrush current and aren’t cheap, so it’s not uncommon to see improvised solutions such as rewound transformers taken out of microwave ovens. There’s another possibility though, in the form of cheap modules that promise the same results using a battery pack as a power supply.
With a love of putting the cheaper end of the global electronic marketplace through its paces for the entertainment of Hackaday readers I couldn’t resist, so I parted with £15 (about $20), for a “Mini Spot Welder”, and sat down to wait for the mailman to bring me the usual anonymous grey package. 18650 Battery Nickel Strip
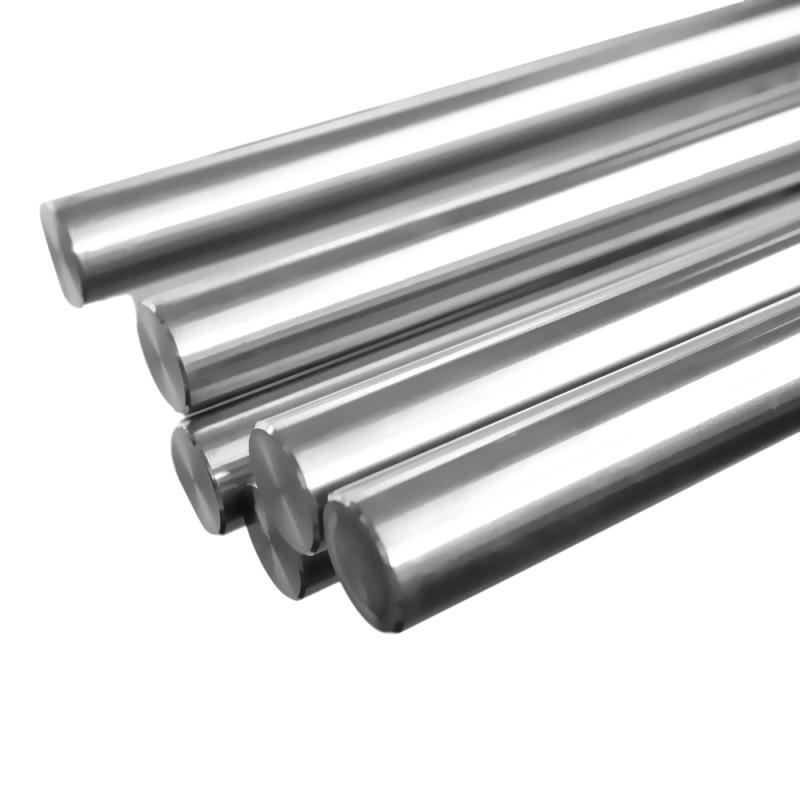
What arrived seemed promising, a “Portable Transistor Mini Spot Welder” along with a pair of battery cables and some cables terminated with spot welding electrodes.
The module itself is a sandwich of PCBs on metal standoffs, with a main board holding power electronics and a daughterboard with part-number-sanded microcontroller and small OLED display. There are some control buttons and a power switch on the board along with a socket for a foot pedal, and the main board has screw terminals, a row of hefty MOSFETs, and a large electrolytic capacitor.
Along with the unit was a set of leads, the welding leads being terminated in a set of insulated except for their tip copper probes and the battery leads being unterminated. I fitted a pair of crimp eye connectors to fit my battery terminals. Also in the box was a piece of paper advising on the type of batteries suitable for the task, which boil down to something close to a car battery. I had a suitable sealed lead-acid battery to hand as well as a few dubious 18650 cells of the extremely lightweight obvious fake variety, so taking a short piece of nickel strip I set out to weld cell and strip together.
Powering up the device and experimenting with the buttons, it became apparent that there were two modes: an Auto mode that would operate it when it detected something to weld, and a manual mode for operating it via a foot switch. I happen to have a foot switch from another piece of equipment, so opted for that.
Otherwise there’s a power setting calibrated in “E”, with no explanation as to what an “E” is. In fact it’s a measure of energy in terms of the length of the power pulse pulse delivered by the device, and on power-up it’s set to the low end of the range at 5E.
I first tried to hold the two probes in one hand and apply them to strip and cell with the other, but found I lacked the dexterity to pull this off. Reaching for a small bench vice, I was able to position them both such that I could hold cell and strip together against their tips and operate the welder via the foot switch.
Starting at 5E and setting out to find the point at which the device would do a successful spot weld, I increased the power in steps of 5E and tried a weld at each level. The lower levels made the two stick together but only to the point that I could easily pull them apart, so I continued. Sadly I never found the level at which it worked , because at 25E one of those MOSFETs failed to a short circuit with the usual magic smoke smell, and I was unable to continue.
The process of reviewing very cheap electronics of this type is something like playing a one-armed bandit. Sometimes you win the jackpot, but at other times the device turns out to be no diamond in the rough. It’s usual though for it to at least do the job albeit in an entertainingly bad way, so this case of it failing to destruction before I had even managed to get it to perform is particularly disappointing.
It’s evident that there is something in the idea of a battery MOSFET spot welder, but these cheap devices seem not to deliver. If you need to weld battery terminals find a more traditional spot welder, meanwhile as regards these battery ones: I bought one so you don’t have to.
i’ve no idea how you came to the conclusion that battery spot welders “don’t deliver” in general… kweld (the one you linked to as MOSFET based spot welder) works great and reliable since years. Started using it with batteries (hobbyking nano) which delievered >1000A, nowadays with their supercap based setup and a server power supplied.
As said, works great and reliable since years now, not a single bad spot weld (other than user error :D)
For 10x the price. https://www.keenlab.de/index.php/product-category/kspot-welder-kit/
which, of course, is still cheap af
Cheap, as in construction? Or Price? Amazon lists such welders for about twice the price of the kweld.
https://www.amazon.com/s?k=battery+welder&ref=nb_sb_noss_1
And since it is difficult to read emotion in these comments, I ask serious, not snark.
I mean price. The construction seems good quality, and the results I’ve seen look very good.
We have one at work that looks like this, only non-digital. No-name, bought off Amazon, same form factor so probably a similar design: https://www.amazon.com/Handhold-YaeCCC-Battery-Current-Display/dp/B07CV68VZD
It works acceptably well on AA/18650 size cells. So you don’t need to spend a fortune to get something that works.
https://www.keenlab.de/index.php/product/kweld-complete-kit/
Should NOT cost that much. That’s a zero too much. God damn.
I should just put on a nano and one of those cheap displays in the link and just sell upgraded k99s for that price. God damn. I’d make a fortune.
The components on that pic is maybe 30 bucks retail. And you can get a pcb printed to fit for 15.
I think it’s fair to say this specific instance of this model and perhaps even this specific model as a whole was a fail, but to extend that to say all cheap battery spot welders don’t deliver is stretching it a little thin. Difficult to extrapolate a general rule from a sample size of one. That being said it would be way more interesting instead of just ending with the conclusion that this one sucks, to look into exactly how it failed and how the design could be improved/modded to make it functional.
It takes an amazing amount of power to make a spot welder. The cheap type have severely limited power.
Unfortunately I had the same experience, it never took a wel but did smoke at…25E..yeeh.. together with my money :((
This spot welder board works really well. I am using two 20 amp hour Prismatic lithium iron phosphate cells and it works great. I am welding.3 mm nickel on power level 3 out of 6. I tried putting longer 4 gauge leads on it with a welding pen but it did not work. With the stock pens it works perfect. They are very short 10 gauge wire. This will eventually destroy the batteries. I am going to switch to a capacitor Bank with a dc power brick.
Is it possibly WORTH hacking it with better mosfets to see if it has any redeeming qualities?
Spot welding is a bit more complicated than these devices can supply.
Most of the resistance in the spot weld circuit is in the wires, not the welded metal, and so most of the energy is dissipated as heat in the wires. Modern spot welding therefore uses 2 pulses: the first one causes the metals to heat up a little, raising their resistance, and the 2nd pulse delivers enough energy to weld the heated spot.
Also, the claims of “>1000 Amp” are a bit misleading. In a weld circuit you get to choose the voltage (by winding the transformer, or choosing the input voltage), the circuit chooses the resistance, and the current is derived from that. Having a single winding on a microwave oven transformer gives you the *capability* to provide 1000 amps, but in reality the voltage/resistance of the circuit determines a much smaller current value.
So to provide better power you can use a higher voltage to overcome the resistance limitation in the welded plates. Using 12 winds on the transformer (at about 1 volt per winding) gives you 12 volts, power is proportional to the square of voltage, and adjust the pulse width as needed. It calculates out to much lower current, but much more *power* and therefore energy delivered to the weld.
To further adjust the resistance you can make the weld tips “pointy”, which makes the weld contact area much smaller, which makes a larger resistance, so most of the power goes to that point. Weld nuts and weld bolts take advantage of this by having 3-ish “points” on their contact surface which serve as weld starts. Also, sharpen the electrodes to a dull point (not a sharp point) for better welds, but it’s a trade-off with the point resistance noted above.
Finally, copper is used as the electrode and is relatively cheap and doesn’t weld, but it wears down quickly. You’re always pulling the stuck electrode out of the weld valley and resharpening the point. You can get copper rods of a special chromium alloy that have better characteristics and don’t erode as much as raw copper.
And then you can mill the copper alloy rods into special shapes to do interesting things, such as hollow to take a bolt, and then you can weld the bolt directly to sheet metal (think: standoff within a project enclosure), or welding ball bearings directly to sheet metal – and then weld supports at any angle to the welded bearings.
Dan Gelbart’s spot welding video will get your creative juices flowing on how to use spot welding creatively. They’re really quite useful for all sorts of applications.
https://www.youtube.com/watch?v=82Iil0fFN9Y
That reply had information on everything I was curious about after reading the write-up. Thank you!
I’m pretty sure if you can look at the part #’s for the MOSFET’s and track down the spec sheets, you will find they are not truly as robust as they could or should have been as in the selection for design and construction. I read a few posts about people testing these units and watched a few YOUTUBE’s also. There also videos about people repairing the welder units when a MOSFET fails.
I used a copper tungsten that was awesome, along withthe kweld and a 6 pk of 3000f super caps connected to a 12v wall wart to charge the caps and i was in resistive welding heaven. I stopped spot welding when i put this system together and started resistive welding…lol both the same but once you get you welder setup right you dont go back. These puny welder from china would melt, and ive melted a few before buying the kweld.
As an engineer, when designing widget (x), , you never design widget (x) to operate at 90% of it theoretical limit, it doesn’t work, iyou will fry that widget in no time. nstead, if your sending 1000a of current down those wires, then you design it to handle 2-3k amps, so that its a walk in the park for that widget, its the same as waking up in the morning and just hauling ass all day, as opposed to waking up and tip toeing through the tulips all day…lol
It’s not a problem with the mosfets, it’s a design error in the mosfet driver circuit that doesn’t fully turn them on, leading to overheating and rapid failure of the mosfets. Adding a capacitor to keep the microcontroller voltage stable during welding events fixes the issue.
There are also multiple revisions of this device out in the wild now; the one I got comes with the capacitor already included, but had another problem requiring a resistor swap.
Do you have a link to the newer design with the cap or the older version and the fix that’s needed?
Yes if one is good at desoldering / soldering surface mount components. Mine smoked too… and I pretty much did everything by the book, just like the author. Personally I think at the step down transformer based spot welders with the copper jaw electrodes are a good way to go (although probably won’t work for tacking nickel electrodes to 18650’s and 21700’s)
Thanks, i have been looking @ these for a while. Glad i never bought one.
Thank you for reviewing this for us. I wonder if this one, or any similar device can also be used for welding thermocouple wires together?
Most T/C wire is 20 awg or smaller (larger gauge TC wire is typically not intended to be used to form the junction, but for extension), so not much energy is required.
I use a large DC source, a switch, and a large electrolytic capacitor. The handle of large needle-nosed pliers are connected to one cap terminal, and a copper plate is connected to the other cap terminal. The power supply is set to charge to certain voltage, the switch is opened, and the twisted TC junction is touched to the copper plate using the pliers to hold the wire. If you counted the number of coulombs correctly, you will have a nice bead under 1mm diameter.
This process was observed and was accredited by several NRTL, NCB, SCC, and other third-party labs for use in data acceptance of Type Tests.
Thank you, we do use TC junctions around here (I haven’t used one so far) and when I asked, I was told we don’t have a TC junction welder.
I had to buy of them some weeks ago and was more lucky. It was indeed to weak at level 1, not yet good at level 2, but really OK at level 3 (on 5). Above, it was too much for the thickness of the strip I had. I rebuild a NiMh pack with 12 batteries, ie. 48 spots (+ at least 10 for training and mistakes) in a row, and it was OK. It was a model with LiIon battery included, a bit more expansive, but the core design is the same.
I was considering one of these after watching an effusively positive video, glad I waited and thank you for your service.
running it from a lead acid might also have something to do with it. Mosfets don’t generally like to be in the linear region and I bet the battery used strongly limits the power available, at least for the intended purpose.
…I probably would have used a 12 volt Lead Acid car/motorcycle battery as well… I’m not arguing your point, just writing what I would’ve done.
“Also in the box was a piece of paper advising on the type of batteries suitable for the task, which boil down to something close to a car battery.”
She didn’t have much to go on regarding the power source…
well.. LiFePO4’s are available in the market in almost any format
there was a design flaw in this welder, some dude on ytube did a few videos on how he repaired it and made it work, and it had nothing to do with the battery, as a matter of fact using too small of a power source will fry it faster than using a big one. So never mind what you hear, size does matter.
Add a two or three Farads worth of electrolytic capacitors, a couple of [four or five for speed] PP3 batteries and a switch, a couple of lengths of cooker cable, insulate it well and pretty much job done. Sure fancy current sensing and mosfet switching might be more efficient and it might be nice to have a pretty case, but spur of the moment and something you might only use for a single project or a quick fix when you’re out in the field somewhere, there’s still something to be said for a quick hacked together bodge.
I had been looking at getting one of these and did a little “homework” that lead me to the following: https://www.youtube.com/watch?v=Zk_ir69kB5Q
Apparently these boards fail when the (shared supply) voltage to the switching electronics drops too low. The MOSFETS don’t achieve full-on with low switching voltage and then overheat. The fix seems simple — add a cap so the voltage to the switching electronics is maintained.
I’ve only just ordered the parts, so I can’t vouch for this fix, but it seems reasonable.
Check out Adam Welch video. https://www.youtube.com/watch?v=Zk_ir69kB5Q He had the same issue and had to repair a blown mosfet, but he also applied a fix to the unit from Maker Fabio https://www.youtube.com/watch?v=fdnO0Z-scjA after that it worked.
For the full DiY / hacker experience I suggest building a MOT (microwave oven transformer) based battery welding rig. Basic recipe: Remove the big transformer from an old microwave oven and rewire the secondary. Add a $15 spot welder controller board and $3 foot pedal switch from aliexpress. Install it all in an enclosure (I used a cheap ammo can box from Walmart). Mine makes very nice welds on 18650 cells.
tried that, really pretty, but inrush current is skyhigh and will trip my breakers as soon as I press the pedal, must revisit someday
Didn’t try it myself, however driving the transformer through a SSR with zero cross detection might be a solution. The user press the pedal switch, it drives the SSR which doesn’t suddenly turn on the load, but waits for the mains wave voltage to reach zero before doing that, so the breaker will “see” the load increasing proportionally with the wave voltage.
Thats how I built mine – (Yes I did it with a 555 as a one shot) driving a Opto Isolated triac driver with zero crossing built in and a single 20A or so TRIAC. 3 Turns of welding cable as the secondary on the Microwave oven transformer.
I thought that was the opposite of what you’re supposed to do
https://www.te.com/commerce/DocumentDelivery/DDEController?Action=srchrtrv&DocNm=13C3206_AppNote&DocType=CS&DocLang=EN
“A zero-crossover solid-state relay may be the worst possible method of switching on a transformer or a highly inductive load. Evidence1 has come to light that zero-crossover turn-on of such loads can cause a surge current of perhaps 10 to 40 times the steady state current, whereas turn-on at peak voltage results in little or no surge. “
I think this article is a pretty good PSA for prospective spot-welding hobbyists. Last year, I ordered one of these $30 spot welders off of eBay in hopes of using it to rebuild an iBook G3 battery pack. It took absolutely forever (almost four months!) to ship from China, and when it arrived, I was dismayed to find that it was already broken. The hassle to get a refund was ridiculous, with the seller asking me to email photos of the broken machine in violation of eBay policy.
I then moved to build my own solenoid + lawnmower battery spot welder, which isn’t perfect, but actually works. I was able to use inexpensive parts from the hardware store, and it is far more powerful than the cheapest ones you can import.
I think my overall advice to people who want to tinker with spot welding 18650s is to just buy the right tools for the job, as expensive as they may be. I think that if I had just bought a > $100 machine like the kweld to begin with, I’d have better results than my DIY machine, or the budget contraption I imported. 18650s can be scary for beginners, and having the right tools makes life a lot easier.
Why not just solder the wires to the batteries? Why weld?
Because most welders would be used with Lithium cells which are just a bit finicky about heat, and tend to complain by catching fire at the first opportunity. Add to this that you can’t extinguish a Lithium battery fire with anything, so it becomes mandatory to avoid the cells any stress that could make them destabilize, like heat and electrical/physical damage. Welding does indeed heat the contacts, but it does it so fast that the temperature drops a lot before it can alter the internal chemistry.
There’s an excellent video on Utube showing the heat going into an 18650 when soldered, it doesn’t just stay on the end cap but penetrates the entire length of the cell.
Even if you’re not an electrical engineer, (I’m not,) it is not terribly difficult to build a resistive welder from scratch. It does take some digging around by looking at what others have done on line, and finding sources for various components. Here’s a conceptual overview and some practical info about how I made mine.
After a couple false starts finding a small enough 12 volt lead-acid battery and a solenoid that actually worked (Curiously, 2 out of 3 new solenoids I bought were bad), I succeeded in making an arduino-based spot welder suitable for making lithium ion battery packs.
Start with a small 12 volt battery in the range of 230-400 cold cranking amps. These are made for golf carts and motorcycles. A car battery is probably too powerful.
Commercial welders often deliver two or more pulses, which in turn resistively heat the metals to be welded. The first relatively short pulse preheats and prepares the materials for the longer welding pulse.
In code, declare the duration for the longer welding pulse, maybe around 25 milliseconds, then divide that by a factor of 5, 6, or 7 and use the result to control the duration of the preheating pulse and the inter-pulse interval. Use the delay() command to specify the durations of the pulses and the inter pulse interval.
The hardware is simple. Use an output pin on the arduino to drive the gate of a mosfet. This causes the drain of the mosfet to close and open, which applies a small current to the input of a motorcycle solenoid. The contacts on the output of the solenoid controls the large current supplied by the battery, which does the actual welding. When the output contacts of the solenoid close, the battery applies the full output current of the battery to the weld.
Don’t forget to include a “flyback” diode (google this) across the output circuit of the solenoid so as to absorb the kickback from the coil of the solenoid. Otherwise, the kickback current could damage various parts of your project.
When you test your project, wear rubber gloves and rubber soled shoes and work in a dry, well lit environment. Safety glasses are a must. Since this is a resistive welder, it does not generate enough heat to generate a damaging amount of ultraviolet light, so darkening lenses are not even required by OSHA. However, the welder likely will throw sparks from time to time, so again, make sure your eyes are protected!
Experiment with a combination of timings, starting at the shorter durations, and gradually building up to longer ones. Invest in some “pure” nickel foil strips for welding the lithium batteries together. Avoid the “nickel coated” variety, because the nickel-coated iron inside them can corrode rapidly in the presence of moisture. Experiment with applying different amounts of force to the things you are welding. Get a trickle charger so you can keep your battery in good shape. I have my 12 volt lead-acid battery secured to a hand truck, so I can wheel it to wherever I need to use it.
As a rule of thumb, the thicker the metals are that you are welding together, the more force may required to make a good weld. A friend of mine brought over a stainless steel measuring cup that had gotten separated from its handle, and even though the stainless steel was a lot thicker than the nickel foils I usually weld to batteries, we were able to weld them back together by increasing the durations of the pulses and also applying a significant amount of force using insulated vice grips to hold the two pieces tightly together to achieve a good weld.
Though relatively simple, this was a really rewarding project for me. Now when I can’t find a source for a dead battery pack, I’m often able to remove the old batteries and weld in new batteries and foils, or even make up a whole new battery pack from scratch.
If used improperly, lithium ion batteries can be extremely dangerous, so please learn as much as you can about how to care for them. When making battery packs, I do it in a dedicated space either outdoors or in a garage well away from anything that could short circuit the batteries and cause them to catch fire. I use a plastic nonconductive table top, with plastic rails that enclose and define the work space only for the battery pack under construction. I keep my metal tools outside the rails of the dedicated work space, and always set a metal tool down outside the work space when I’m momentarily done with it. This prevents me from ever setting down a battery pack on top of a metal tool and inadvertently causing a short circuit.
Be safe and have fun!
Back many years ago I worked for company that made precision wirewound resistors. We had dozens of spot welders made in house to weld the resistance wire to the metal caps on ceramic bodies. Our welders were pretty simple. A Variac, bridge rectifier and big electrolytic capacitor, big-ass mercury relay discharging into the primary of a filament transformer (6.3 volts secondary). Welding energy adjusted by the Variac. A foot operated switch pulled the spring loaded copper or tungsten electrode down onto the resistor cap. The operators, some of whom had been doing this for years chose the weld variable by pulling on the resistor wire and/or by visual inspection. Some of the alloy wire was as small as 0,0005″ and as large as 0,1″. We had special welders for the larger sizes. These simple ones ran for years making hundreds of thousands of connection. After the resistor was made and heat treated, the resistance, purposely made a little low, was adjusted into the right resistance by viewing on a sensitive bridge and gently stroking the wire with a fine sandpaper. Sounds crude, but it worked very well. Most of our products were 0.1% or better.
There’s a YT hack for this welder. Adam Welch shows it in a video titled ‘Repair Attempt’. A capacitor added…
I remember seeing friend try and use a fully charged capacitor from an camera flash once to spot weld but it was just far too much power far too fast. Not so much spot welding as explosive metal removal.
This spot welder isn´t that bad, just needs a small fix: add an additional cap for the controller board. Reason for failure: Controller supply voltage drops too low during welding -> MOSFETs are no longer saturated (changes to linear mode) -> boom. Good video: https://www.youtube.com/watch?v=fdnO0Z-scjA&t=0s
Agree I did this fix and works a charm.
I actually thought of that fix before that video was posted. I also did some other mods. Been over 10 months and mine is still working. You can see what I did here…
https://imgur.com/a/NT6eLsk
I see what you did there.
This is a known problem with this particular welder. A simple fix is suggested in Maker Fabio YouTube channel. I did this and have welded hundreds of batteries with no problem since. https://youtu.be/fdnO0Z-scjA
If you use a battery with too high an internal resistance… You will under drive the MOSFETs and burn them up
This is absolutely correct John. I have read reports and watched videos of this particular spot welder and if you use a battery that cannot deliver the starting current the mosfets will fail due to drop in gate voltage. Here is one suggested fix for this https://www.youtube.com/watch?v=u5khY6d3qds. I don’t have this particular spot welder, but I do have a one hande one I purchased from AliExpress and it works fine
There are a large number of these mini spot welders, some have issues that need to be corrected.
Here is a video detailing a number…
https://www.youtube.com/watch?v=RSrlXqFxhp8
I think one of the problems with low cost import power electronics is the cascading of inflated specs. You buy a device rated at 50A, and open it up, and it has power devices rated at 35A, so they may be able to give you a very brief 50A spike, or just short out. But, the 35A output devices are from the same country, and while the part number should be good for 35A, they use a smaller die that is really more like a 20A part, and again you may be able to get a brief 35A pulse out of it. This happens with a lot of parts, so you wind up with something that will probably work if you de rate it by about 75%.
I have a BIFRC brand spot welder that is a bit more expensive at about $50, but has worked well for me.
One critical trick that is not mentioned in the manuals: press with the corner of the probe, not the flat face. Otherwise the contact pressure will be too low and area too high to get a good weld.
Car battery, automobile starter solenoid, adjustable timer module along with MOSFET switching module to close starter solenoid for desired interval.
Still do not understand why you cannot solder those batteries. You scrape the metal clean, use flux and hot iron. Takes only few seconds.
Heat from soldering damages the cells. After soldering the capacity of the cell can be diminished, not that much, but some. Also people don’t often have the high thermal mass soldering iron that should be used for such a job, trying to do it with a standard electronics soldering iron is not a fun time.
User error. I’m been running one of those for years. All modded up . I only set it to E4 and it welds right through 2 strips of nickle to the battery metal. never had a problem. Actually the best spot welder I own. Even better than $300+ models
Actually, these cheap spot welders have come a long way over the past couple of years. I tried the car battery with a relay, I tried the microwave transformer. In both cases, with my absolutely crude setup the leads ate holes in my nickel strips and sometimes even the battery. It wasn’t until a friend of mine showed me his cheap spot welder and was successfully using it that I realized what the difference was. It’s just pressure. Think of any time you accidentally shorted out a powerful battery, like a car battery. Typically, when you accidentally touch the leads or piece of metal across you are often left with two big chunks of metal missing from where they made contact. This in contrast to say having something on purpose shorting out the battery with solid contacts leaves the surface of your leads perfectly fine. So when using these cheap welding machines, it takes a little practice, but what you have to do is touch, not push, touch the leads to your nickel strips, just enough so that the nickel make a weak contact to the battery and the result is enough resistance and the sudden rush of massive amps going from contact lead down through both the nickel strip and the battery and up to the other lead welding both sides.
that is the exact opposite of a video i watched showed, he said you have to apply pressure so the current penetrates to the battery instead of just arcing across the nickel. that’s why the pens they sell have springs. mine just needs a power supply so i’m gonna build one with a microwave i kept after it stopped working.
Please be kind and respectful to help make the comments section excellent. (Comment Policy)
This site uses Akismet to reduce spam. Learn how your comment data is processed.
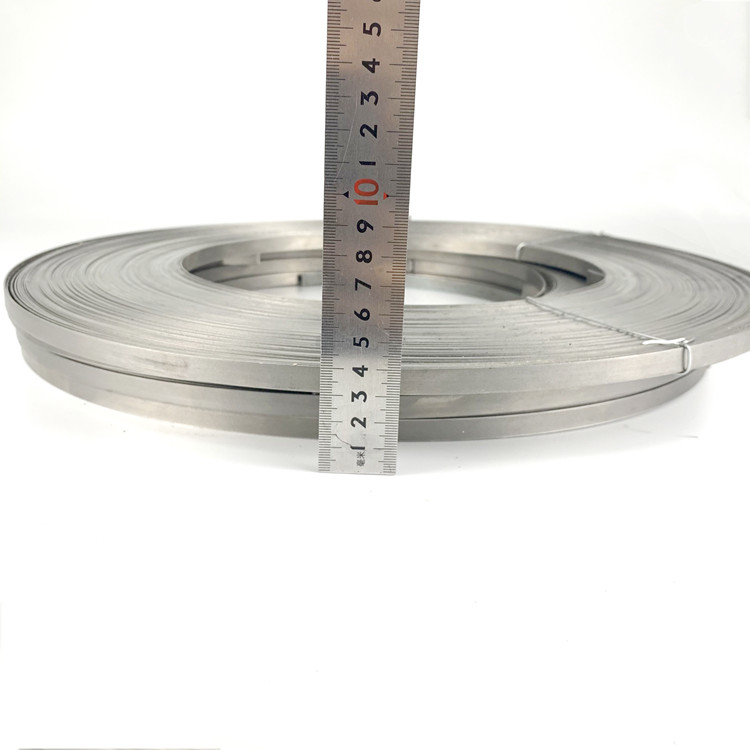
Nichrome Rods For Ceramics By using our website and services, you expressly agree to the placement of our performance, functionality and advertising cookies. Learn more