Hydro, an aluminum and renewable energy company, recently announced an $85 million investment in a new casting line to advance its aluminum recycling plant in Henderson, Kentucky, according to a press release .
The new line, backed by tax incentives from the Kentucky Economic Development Finance Authority (KEDFA), will become operational 2026. Ggg50
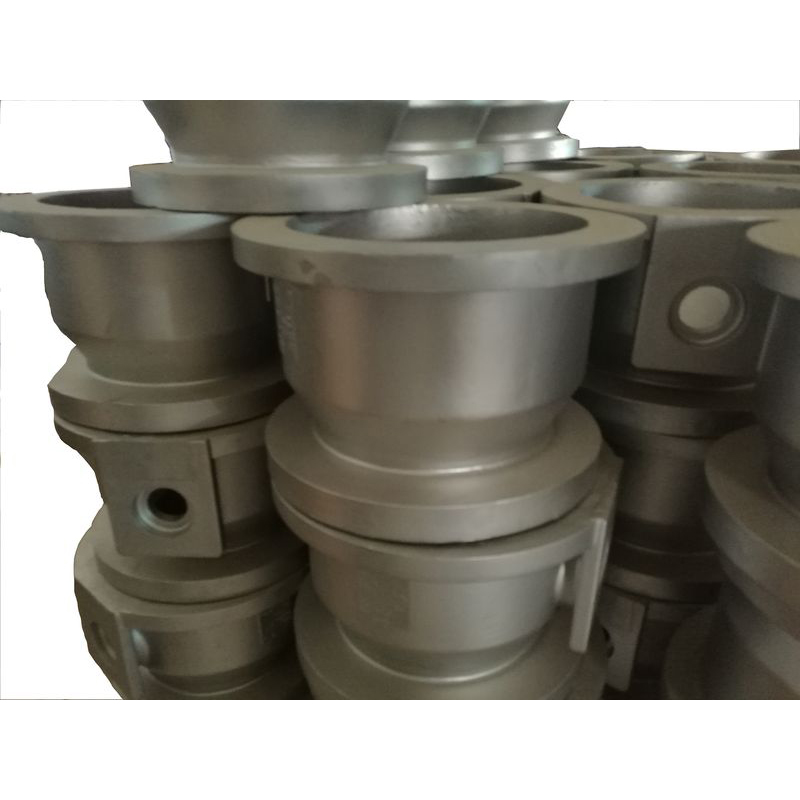
HyForge technology will be used on the new line, the release says. The company’s website says the low-pressure casting (LPC) technology offers a new high-quality forge stock by eliminating friction occurring on the ingot surface, resulting in a very smooth surface of the log.
“The inverse segregation zone is also eliminated,” the website says. “As a result, there is no need for further process steps like scalping, extrusion or machining. The HyForge™ material can be used directly in the forging process.”
HyForge material can be used on wheel suspension parts, drive train parts, brake systems, and pneumatic/hydraulic systems, the website says.
Once operational, the release says, the plant will serve the automotive market’s needs for smaller diameter, high quality billets that can be forged directly into high-quality automotive components.
“This means the number of processing steps from casthouse to automotive parts are greatly reduced, leading to cost efficiency and higher product quality compared to traditional processes,” the release says. “All benefits will come without compromising safety.”
The upgrades are expected to increase capacity by 28 000 tons (62 million pounds) of aluminum at the plant, the release says.
“Taking advantage of the new technology and expanded capacity cater to the specific needs of our customers within the automotive industry to create light weight car parts, helping reduce emissions from driving,” says Eivind Kallevik, company president and CEO, in the release. “This expansion significantly increases the use of end-of-life aluminum, cutting emissions from creating the products themselves, ensuring market leading sustainability performance for Hydro and our customers.”
Hydro previously implemented HyForge casting technology at the Hydro Husnes primary plant in Norway and the Hydro Rackwitz recycling plant in Germany, the release says.
“This investment is another step along Hydro’s journey to change the game in aluminum production,” Recycling more end-of-life scrap reduces emissions, strengthens security of supply and enables us to deliver new, cutting-edge products to our U.S. customers,” says Kallevik.
Hydro also previously announced a $15 million investment in a new baghouse and homogenization equipment for the Henderson recycling plant. The projects, which will allow the company to produce large volumes of advanced alloys using recycled, post-consumer scrap with a lower-carbon footprint, are near completion.
“Hydro Henderson has been at the forefront of producing recycling based automotive products for nearly twenty years,” says Kallevik. “We work closely with the automotive industry and introducing Hydro’s HyForge technology will provide Hydro and our partners with a greener advantage.”
Photo of Hydro’s aluminum recycling plant in Henderson, Kentucky/Hydro
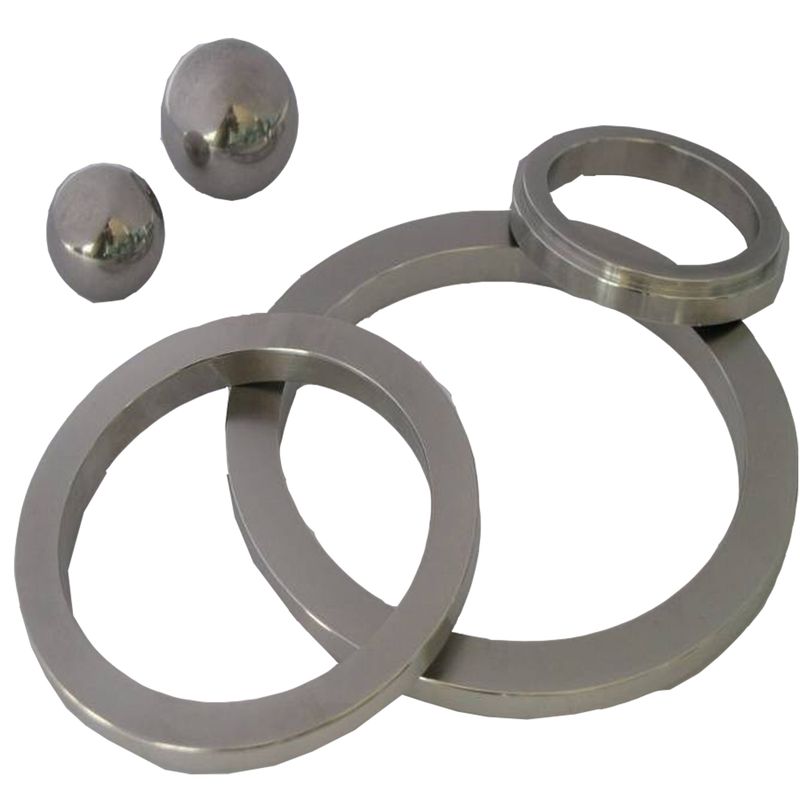
Copper casting © 2023 DRIVEN COMMUNICATIONS Inc. All Rights Reserved.