There are many clever ways to make stronger 3D prints, be they by the use of special slicing algorithms or by unusual filaments. [Brtv-z] has taken a more straightforward tack, by making glass-reinforced prints using painters fiberglass mesh tape.
It’s a laborious technique that involves stopping the print to manually place the fiberglass at each successive millimeter of print. The resulting test piece comes off the print bed festooned with fiberglass mesh, and once it’s been trimmed, he subjects it to some tests which you’ll see in the video below the break(Russian language, but there are subtitles). Fiberglass Mesh Fabric

The tests are fairly rough and ready involving a hammer (we winced at the hammering in a vice, but of course this piece isn’t forged steel!) and standing on a flat piece of print balanced between two blocks. As you’d expect, the reinforced piece appears the stronger, but these tests would benefit from a calibrated set-up to quantify the strength.
So if you’re of a mind to experiment, this certainly seems like an accessible if rather tedious way to make glass reinforced 3D prints. If you then want to characterize them, remember this can be done with a bit of farmyard engineering if you have nothing better.
Improving XY strenght while slightly compromising Z strenght is exact opossite of improvement needed for FDM prints. These are already strong in XY and weak in Z.
You’re right in a general sense, but there’s still merit in techniques like this.
There are certain applications where the absolute strength in one plane is more important than the layer bonding strength.
Plus it’s a well known phenomenon in 3d printed parts. You should be orienting your parts in a way that ensures that the force will be applied along the X/Y axis. When that’s not possible, it’s usually best to split the part up into subassemblies or use external reinforcement like screws/dowels/metal channel. Annealing is also an option, but that can be really tricky depending on part geometry and filament type.
You’re partially right, however: * This is why you bake prints so direction of printing doesn’t matter much * Some prints are used only in specific position and this is also the reson why we choose to print usually in opposite position so that Z is in 90° to the position exposed to stress * There are already few 3D printers with same Z resolution as for other axis so this problem is starting to disappear
There are many glass reinforced 3D filaments available. Some as cheap (?!) as $50 per kg, and some as much as $500 (!!!)
Pros and cons. Most fiberglass filaments are just finely chopped glass mixed into the plastic. Stronger, but not by much. There’s more exotic filaments that have a contiguous fiberglass core that gets laid parallel to the layers and is VERY strong, but most printers can’t use that sort of filament and most slicers don’t support it.
This method sounds like a great new alternative.
This is a great first iteration. Now somebody can automate adding the mesh!
That’s the future of 3D printing I’m so excited for: mixed tooling to blend techniques like this.
Check out the markforged. It has an extruder for the fiberglass, and can even pattern it between the layers. Super cool printer.
Great machines, have used 4 of them including the industrial X7. I used a lot of Kevlar reinforcements.
Markforge already makes a printer that automatically adds continuous glass fibers to a print. However it’s quite expensive.
This whole article comes across as condescending. I’d give examples, but they’re fairly obvious. You’re better than this. If you think it’s good enough to write an article about, don’t ruin it by looking down your nose at the project or person.
Condescending is excessive imo, the suggestions to improve testing came across to me as constructive criticism at best and subjective opinion at worst. This is probably one of those situations where your own thoughts and assumptions about the subject and author’s writing style color your perception of the author’s tone. In general it’s a good idea to give the benefit of the doubt in cases where text alone cant properly convey subtleties that can make things look different than the author intended.
For example it’s easy at face value to take your response as acerbically defensive, when that may actually not exactly have been the tone you intended, which may have been actual concern about articles sending positive messages to spread knowledge/inspire creativity instead of negativity in the vein of “not a hack”/etc parroted in the comments section of many articles.
I said what I said. Your tone may be gentler, but your response is much more defensive than you suggest mine was. You say ‘Condescending is excessive…’ but then you lash out with ‘acerbically defensive’ (yes, I’m aware you were contrasting ‘charitably vs harshly’ interpreting someone’s statements, but it was an obvious backhanded suggestion. Like if I called someone fat, and you said to me “Well I could call you ugly but I won’t”). One could argue (successfully) that you’ve proven, with your last sentence, that your perception of my tone is colored by your experience with the comments section here. Ascerbic seems to mean ‘sarcastic or cynical’. I don’t see sarcasm or cynicism in my comment (or in my intention), but the cynicism part is interesting, as that seems to be a pretty good description of the article itself. It’s easy to become cynical, and hard to see it in ourselves. You claim that it may just be ‘subjective opinion’ in the article that’s tripping my condescension radar, but wouldn’t that be dependant on context? Like, a political commentary is likely opinion, while a journalistic piece would ideally be factual, but there’s obviously room for some overlap. I simply disagree with the writer on how far that overlap should extend into negativity (unless that is in fact the intention).
Hey you wanna look for a fight, then you are gonna look for a fight. Just don’t be surprised when someone calls you out for your bs.
This has to be the most passive aggressive long winded way of saying a combination of “I’m not defensive, you’re the one who’s defensive!” and the whole “I’m rubber, you’re glue” diatribe
Yeah I think I had an aneurysm reading it… Then again, what did you expect would happen when responding to someone who reads things in the worst way they can?
The article doesn’t seem condescending to me at all. It’s merely point/counterpoint and I appreciate that he tries to be objective about the whole thing. It’s certainly better than some articles here have been, where really old or simple bits of science are enthusiastically passed off as “hacks”.
Very interesting. Note he is putting the mesh at the same angle. This gives a slicing plane. Suggest every mesh 45 degrees to the previous mash.
the mesh will work,but a set up with a TOTALY enclosed print chamber and chopped up fibers (pick your itch) blowing around and making a big sticky mess would yield a random fiber placment for the price of a big clean up the learning curve would involve getting the fibers of a size that one would add strength and two would loft in a light breeze and make a cloud that kept providing fibers to the fresh hot surface,random orientation would be a feature
Just brush them on in a solvent solution. Let dry.
Business idea: Ribbon Applicator of interlayer substrates. New layer; advance film; foam roller; dry period; print
Fiber reinforced filaments are not particularly expensive and offer FAR more versatility with equal or better performance. I could better understand it if he was trying to print something that actually offered a benefit, such as if for some reason he used copper mesh for electrical or thermal conductivity, but I fail to see the advantage to this otherwise.
If someone could come up with an automated way to weave some fibers under the fibers in layer N-1 and over fibers in layer N, then it’d really be something.
Ok, I know you can get fiber “reinforced” filament ready to use and there are all kinds of applications for it. There are also straight fiberglass additive manufacturing processes where fiber threads are impregnated with resin with various techniques as its laid down.
Several comments have stated that this sandwich technique doesn’t provide adequate z-axis strength.
So, just spit balling here but, would it be possible to get pleated fiberglass mesh then program the printer to take into account the pleats? You wouldn’t get great resolution but for this kind of application I would think sanding and an ammonia fog tank were already going to be needed.
Maybe if the printer fed a coil of coarse fiberglass thread into the extruder tip to wrap around the hot filament as its laid down? The idea being that an integrated coil would provide strength along all three axis. Might get some more goody out of the fiberglass if it was heated before entering the tip. God only knows what kind of specialized print heads and high temp filaments something like this would take. Preheaters and feed guides galore.
On the remark of people that you can get fiberglass reinforced filament: doesn’t that do damage to you nozzle and such? I mean it would be much more abrasive than regular filament right?
Not if you choose the correct nozzle, many options are available for common printers.
It definitely is. Many filament additives are abrasive, including some pigments like the titanium dioxide used some white filaments.
You can use a hardened steel or synthetic ruby nozzle to be more resilient against the wear, but I get brass nozzles for $0.25 each and discard them when they get clogged or worn.
I was going to leave a similar comment but then I realized I have no idea how much it costs to do the technique mentioned in the article and it might be just as accessible to get a hardened steel nozzle
I used this fibreglass scrim tape with a hot melt glue gun for a very effective repair to a polypropylene water butt. It is great stuff and I recommend it to the community :-)
Yes. the item is very solid
In the USA the length is measured in bananas. In Russia the weight is measured in Katerinas
PS. Stretched & squared up mesh is WAY stronger than mesh just placed on top.
Please be kind and respectful to help make the comments section excellent. (Comment Policy)
This site uses Akismet to reduce spam. Learn how your comment data is processed.
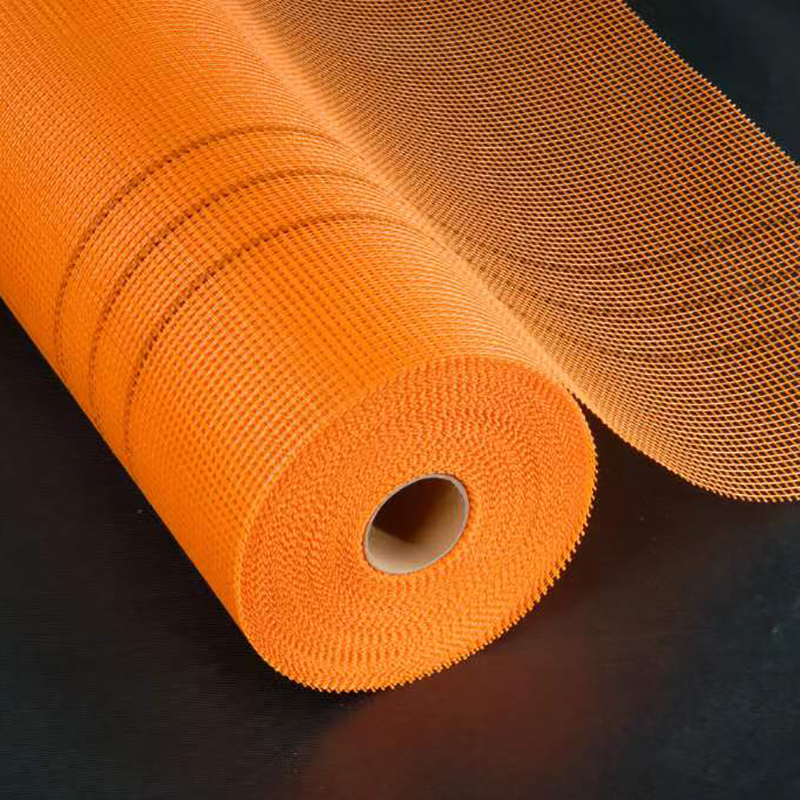
Vinyl Laminated Fiberglass Screen By using our website and services, you expressly agree to the placement of our performance, functionality and advertising cookies. Learn more