A significant increase in the price of nickel, coupled with its reputation for low maintenance, has spurred unprecedented demand for power plant components to be made from fiberglass reinforced plastic (FRP).
A significant increase in the price of nickel, coupled with its reputation for low maintenance, has spurred unprecedented demand for power plant components to be made from fiberglass reinforced plastic (FRP). Because FRP has been used in power plants for more than 30 years and can be employed in numerous applications, it provides power engineers with a less costly construction material for their projects without sacrificing reliability. Plastic Cable Duct

A record global demand for stainless steel drove nickel prices sharply higher in 2006. This trend continued in the first half of 2007, with nickel rising from $15 a pound to a high of $24 a pound. Consequently, traditional construction materials containing nickel used in power plant applications have become more expensive as supply has tightened. In contrast, the price of FRP has remained relatively stable and supplies are sufficient for the current demand. Other materials used in flue gas desulphurization (FGD) may be cost competitive with FRP, but history shows these alternatives require more maintenance, resulting in higher life cycle costs.
In 2006, the use of FRP in the power industry increased dramatically. As a result, a number of companies such as AEP, Dayton Power & Light, Duke Energy, Santee Cooper, Southern Company, TVA and We Energies turned to FRP to reduce cost without sacrificing reliability. FRP met these needs and cost less than half that of nickel alloy-clad steel. More than 30 years of case histories have demonstrated that FRP is low maintenance and reliable.
The total installed cost for FRP ranges from about $125 to $150 a square foot in North America. Prices may vary in other countries. It is very competitive with acid brick-lined or rubber-lined carbon steel (see Table 1) and less expensive than alloy clad carbon steel. Although FRP is more expensive than resin-coated carbon steel, it has a lower life cycle cost than resin-coated carbon steel and other materials noted in the table.
FRP gained prominence as a construction material following World War II. In the early 1950s, the chemical process and pulp bleaching industries began using FRP based on polyester resin to replace more expensive or less suitable chemical resistant materials such as alloys, rubber lined steel and wood. In the 1960s epoxy vinyl ester resins were introduced. The new resins increased the service life of FRP because of improved chemical resistance and toughness. The introduction of various resins, including high-temperature epoxy vinyl ester resins, not only enhanced the use of FRP in those industries, but made further inroads into the power and pollution control industries possible.
Long-term FRP success in industrial applications involved much more than resin improvements. More than three decades of industry guidelines and standard developments significantly improved quality and reliability. Furthermore, years of experience taught engineers and industry leaders that guidelines and standards alone were not enough to insure FRP success. Overall success requires that FRP buyers employ best practices in operation. It is equally important for them to adopt best practices in material selection, design, specifications, fabrication, inspection, shipping and installation.
Temperature and pressure also are parameters that must be considered in the systems where FRP is to be used. In power plants with gas and fume handling equipment, the operational temperature limit for FRP is 380 F under most circumstances. However, for short periods FRP can withstand dry gas up to 600 F. For most liquid environments found in a power plant, the operating temperature limit is 210 F. In hot/wet mix zones, FRP lined with borosilicate block can be operated up to 500 F.
The other parameter to consider is pressure. The operating pressure limit for most FRP tanks, scrubbers and other vessels is 15 lb/sq inch. Smaller diameter pressure vessels can be operated up to 50 lb/ sq inch depending upon thickness. The operating pressure limit for typical FRP pipe is 150 lb/sq inch.
The use of FRP in power plants dates back to the 1970s. FRP has been used extensively in piping systems and in stack liners. Other applications include absorber vessels, cable trays, coal conveyor covers, cooling towers, ductwork, grating, pumps, storage tanks, thickener tanks and vacuum filters. In power plants, the most common use of FRP has been slurry piping in wet FGD systems. With an abrasion-resistant liner, FRP pipe based on Ashland’s DERAKANE 411 epoxy vinyl ester resin and HETRON 922 epoxy vinyl ester resin has been used in more than 150 plant sites dating back to 1972.
The largest volume use of FRP in North American power plants is for stack liners and ductwork. From 1977 to 2005, a number of FRP stack liners were installed and most are still in service today. In 2006, 63 FRP stack liner contracts were awarded for construction at 49 power plant sites. With more than three million square feet of laminate, this is the largest use of FRP for stack liners in power industry history. The 63 FRP stack liners awarded in 2006 generated unprecedented demand for FRP ductwork to transport scrubbed flue gas to those stacks. Such FRP ductwork has been successful dating back to the 1970s.
Absorber vessel shells and internal components comprise the third largest use of FRP in power plants. The most common FRP absorber vessels are known as jet bubbling reactors (JBRs). A JBR is part of a limestone slurry FGD process that has all the chemical reactions taking place in one vessel to produce high quality gypsum. One of the largest FRP scrubbers in North America started up in June 2007 at a power plant on the Ohio River. The JBR installation is 88 feet in diameter and 77 feet tall. The JBR is already removing 99 percent of the sulfur dioxide from high sulfur coal flue gas. Many of the JBR internal components are also made from FRP, including the mixer shaft and blades.
Cooling towers afford another use of FRP in power plants. While wood has been the predominant material used for these towers, FRP is fast becoming the material of choice. The primary reason is that FRP structures are anticipated to last more than twice as long as wood structures (50 years-plus versus 25 years for wood). FRP requires little or no maintenance over its lifespan while wood towers often require a considerable amount of maintenance. FRP is not subject to internal deterioration or biological attack and it can withstand almost any chemical exposure if the right resin is used. Because FRP structural members can be manufactured in lengths of 60 feet or more, labor costs are reduced compared to lumber, which requires splicing in 20-foot lengths.
Chemical and wastewater storage tanks present another opportunity for FRP use in modern power plants. A dozen tanks have been installed at a power plant in the Northeast made of HETRON 980 epoxy vinyl ester resin. The tanks contain hot wastewater and have a design temperature of 200 F.
FRP made with DERAKANE epoxy vinyl ester resin or HETRON epoxy vinyl ester resin is a suitable and economically attractive construction material for a variety of power plant applications. Proven performance at a lower cost, especially when compared to that of high nickel alloy-clad carbon steel, makes FRP a material of choice for highly corrosive pollution control applications such as absorber towers, ductwork, limestone slurry piping, stack liners and spray headers. The growing list of applications made from FRP include cable trays, coal conveyor covers, grating, pumps, thickener tanks and vacuum filters. FRP has become an option to lower cost materials of construction for improved life cycle cost that includes less maintenance and longer service life.
Author: Don Kelley is a senior staff development chemist with Ashland Performance Materials. He joined Ashland’s Composite Polymer business group in 2004 after 34 years with The Dow Chemical Co. He has extensive experience in the development and promotion of corrosion resistant composites in industrial applications for more than 22 years. He specializes in chemical process, mining and power applications. He is a member of NACE, SME and ASTM and has a M.S. degree in Chemistry. This article is copyright Ashland Inc.
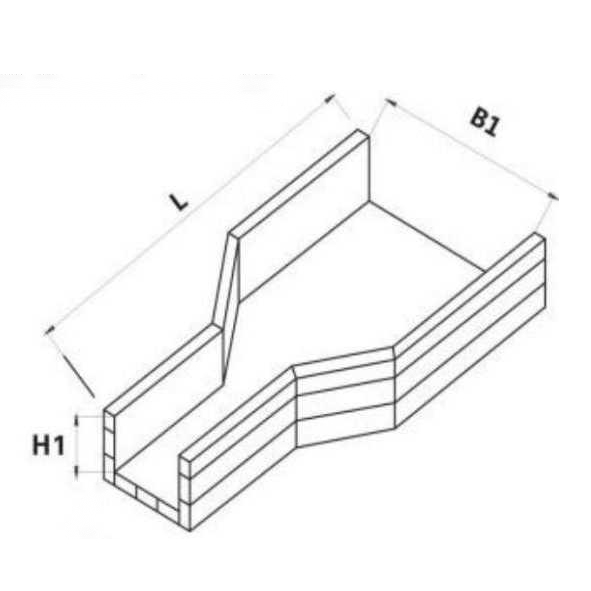
Pregalvanized Cable Tray Power Engineering®️ is the voice of the power generation industry including news, exclusive articles, and in-depth reviews. Subscribe today to receive critical information and industry updates to remain competitive in today’s market.