Robotic technologies often captivate human attention for their broad—and still growing— autonomous operating capabilities. They also attract our attention because we can see how they’re changing the very face of industrial operations.
Like the first two installments in our Peer-to-Peer FAQ series (on sensors and cybersecurity), this FAQ begins with an overview of the technology in focus and then shares insights from system integrators and your end user peers across industry. 7th Axis Linear Track
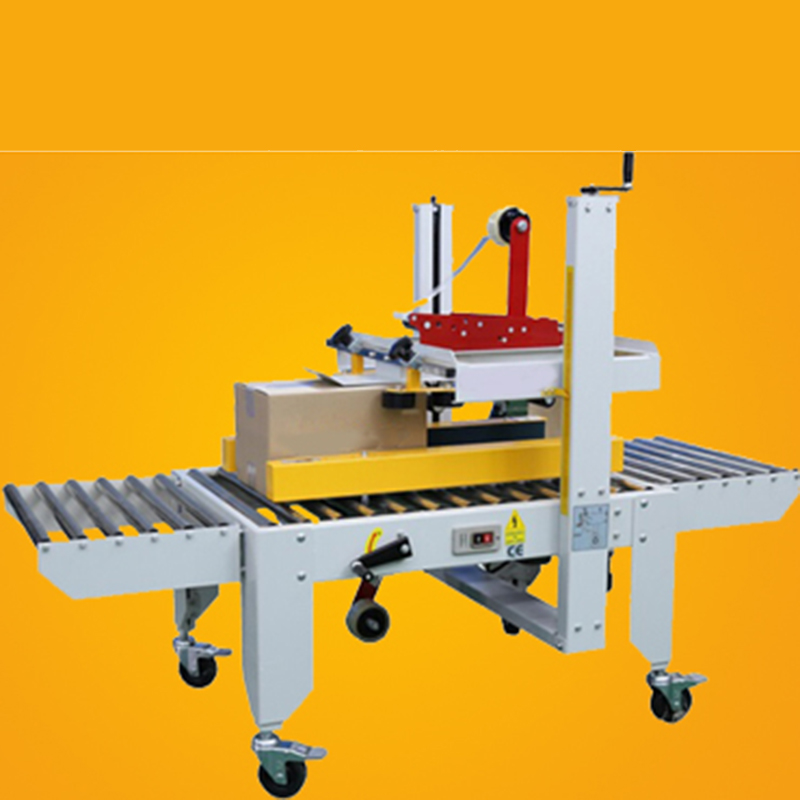
While this general description has long been used to denote the difference between industrial robots and cobots, that line is becoming more blurred. Today, some industrial robots possess aspects of collaborative capabilities as outlined in ISO standards 10218-1 and 10218-2. These collaborative capabilities—safety monitored stop, hand guiding, speed and separation monitoring, and power and force limiting—can all be achieved using sensors, control systems, and peripheral devices, some of which may already be integrated within a robot upon purchase, while others can be retrofitted to an installed industrial robot.
A description of ISO’s four collaborative robot capabilities:
End user and integrator insights Few advanced technologies are as associated with automation as robotics. In fact, for many, the two terms—robotics and automation—are synonymous. But the truth is, robots are just one example of an automated system, albeit an often complex and highly flexible one. As such, robots are increasingly part of the automated ecosystem that comprises modern manufacturing. And with the advances being made to robots that make them more flexible, more capable, and more easily programmed, we’re now seeing a level of robot adoption that surpasses that of the robot adoption heyday in the automotive industry in the 1980s.
To better assess the state of industry’s current attitudes toward robots, we surveyed nearly 60 industrial end users and system integrators that work in every vertical manufacturing industry—discrete manufacturing, batch manufacturing, and continuous processing. Most respondents were, of course, in the discrete and batch manufacturing industries (96%), as robots are not as widely used in the continuous process industries due to the nature of their often enclosed (i.e., within pipes) production operations.
Respondents indicated that, of the robot types used in their production operations, 73% are industrial robots, 39% are collaborative robots and, surprisingly, 30% are autonomous mobile robots (AMRs). Editor’s note: Respondents were allowed to select all the robot types used in their facility, thus the total amounts exceed 100%.
Interestingly, 83% of readers said they are looking to add robots—or more robots—in the next two years. Helping drive this figure is the fact that 29% of respondents currently don’t use any robots at all, and only 13% note that more than 50% of their production operations involve the use of robots.
Of those end users applying robots in their production operations, industrial robots have been in use at their plants for an average of 11 years, while cobots and AMRs have been in use for an average of six years.
End users also noted the main drivers behind their decision to use robots. When asked to rank the issues affecting their use of robots, 45% noted labor issues as the primary factor, while 30% said speed/throughput, and 20% cited quality as the main issues driving their decisions.
Though integrator respondents largely agreed with the numbers noted by end users, the integrators said interest in cobots over the past five years has grown by about a third, though most end users still prefer industrial robots. In fact, integrators note that 33.3% of their clients currently prefer cobots, with the remainder preferring industrial robots.
This insight about preferences for industrial robot over cobots could lead to faster, more widespread adoption of new industrial robot control technologies now coming to market. These technologies, which can transform industrial robots into cobots, apply capabilities such as speed and separation monitoring to help industrial robots move outside the caged or otherwise protected environments they’ve traditionally operated within. We’ve seen this demonstrated with both large palletizer robots as well as smaller industrial pick-and-place robots.
Most integrators (60%) responding to our survey say that it’s still too early to tell if these new robot control capabilities will reduce the recent upsurge in interest for cobots. However, given industry’s existing preference for industrial robots over cobots, any technology that could enable industrial robots to operate as cobots has a lot of built-in upside potential. This doesn’t mean that cobots will disappear, of course, but that their use will become more targeted at the types of applications for which they are best suited, i.e., those applications in which an industrial robot could be considered overkill.
Mobile robots on the rise While much of the attention on robot technologies in industry tends to focus on articulated robots that can grasp and move objects, autonomous mobile robots (AMRs) have also been gaining a great deal of attention. In fact, 100% of the integrators responding to this survey said they have seen an uptick in interest for AMRs among their clients over the past five years.
Two factors tend to figure into the increased interest in AMRs:
Integrators noted that interest in AMRs among users is evenly split among the discrete and batch manufacturing industries, comprising about 80% of the market looking to use AMRs.
Though industrial robots and cobots still lead the way in terms of the type of robots end users are looking to implement, at 78% and 44%, respectively, 22% of end users are looking to implement AMRs in the near term.
One end user respondent said the most important piece of advice they can share is for users to understand the importance of their own production processes before installing a robot. “If a robot is bought without a good understanding of the technology or the maintenance requirements for converting a manual process into a robotic method, this can lead—in many cases—to the robot ending up in a corner and not being used.” To avoid this outcome, this respondent recommends conducting a study before purchasing a robot to help direct the correct implementation of that robot to ensure it will deliver the expected results.
Another respondent suggests that, prior to any robot purchase, users should create and run a realistic simulation of the application to ensure it works as envisioned. “Check with the manufacturer to see how realistic their simulation software is and also check for cycle times,” said this respondent. “Integration and communication with third-party components is also an important factor in making a final decision.”
“Take baby steps when integrating [robotic] automation into legacy manufacturing operations and perform a ‘design for automation’ assessment in the early stages,” advised another respondent.
A few other key pieces of robot selection and application advice from end users include:

Gantry Palletizer Leaders relevant to this article: