Queen Mary University of London, United Kingdom
Muscle contraction hardening is not only essential for enhancing strength but also enables rapid reactions in living organisms. Taking inspiration from nature, the team of researchers at Queen Mary’s School of Engineering and Materials Science has successfully created an artificial muscle that seamlessly transitions between soft and hard states while also possessing the remarkable ability to sense forces and deformations. High-Performance Gantries
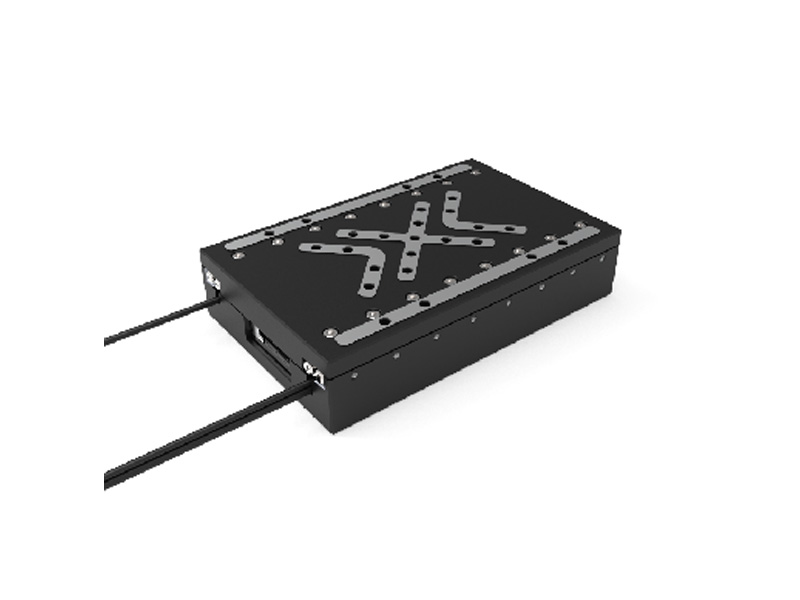
Dr. Ketao Zhang, a Lecturer at Queen Mary and the lead researcher, explained the importance of variable stiffness technology in artificial muscle-like actuators. “Empowering robots, especially those made from flexible materials, with self-sensing capabilities is a pivotal step towards true bionic intelligence,” said Dr. Zhang.
The artificial muscle developed by the researchers exhibits flexibility and stretchability similar to natural muscle, making it ideal for integration into intricate soft robotic systems and adapting to various geometric shapes. With the ability to withstand over 200 percent stretch along the length direction, this flexible actuator with a striped structure demonstrates exceptional durability.
By applying different voltages, the artificial muscle can rapidly adjust its stiffness, achieving continuous modulation with a stiffness change exceeding 30 times. Its voltage-driven nature provides a significant advantage in terms of response speed over other types of artificial muscles. Additionally, this novel technology can monitor its deformation through resistance changes, eliminating the need for additional sensor arrangements and simplifying control mechanisms while reducing costs.
The fabrication process for this artificial muscle is simple and reliable. Carbon nanotubes are mixed with liquid silicone using ultrasonic dispersion technology and coated uniformly using a film applicator to create the thin layered cathode, which also serves as the sensing part of the artificial muscle. The anode is made directly using a soft metal mesh cut, and the actuation layer is sandwiched between the cathode and the anode. After the liquid materials cure, a complete self-sensing variable-stiffness artificial muscle is formed.
The potential applications of this flexible variable stiffness technology are vast, ranging from soft robotics to medical applications. The seamless integration with the human body opens up possibilities for aiding individuals with disabilities or patients in performing essential daily tasks. By integrating the self-sensing artificial muscle, wearable robotic devices can monitor a patient’s activities and provide resistance by adjusting stiffness levels, facilitating muscle function restoration during rehabilitation training.
“While there are still challenges to be addressed before these medical robots can be deployed in clinical settings, this research represents a crucial stride towards human-machine integration,” highlighted Dr. Zhang. “It provides a blueprint for the future development of soft and wearable robots.”
For more information, contact the Press Office at This email address is being protected from spambots. You need JavaScript enabled to view it..
This article first appeared in the September, 2023 issue of Tech Briefs Magazine.
Read more articles from this issue here.
Read more articles from the archives here.
Medium-Voltage Converters Can Replace Grid Transformers
Polyphase Wireless Power Transfer System
Starliner Completes Successful Uncrewed Return to Earth
Artificial Muscles Propel a Robotic Leg to Walk and Jump
A Shape-Shifting Metamaterial Inspired by Push Puppets
Boom Supersonic Completes Second Flight of XB-1 Demonstrator
Automotive Hardware Security Modules: Functionality, Design, and Applications
Protecting Advanced Technologies With Conformal Coatings
The Benefits and Challenges of Enabling Direct-RF Sampling
Modernized Condition Monitoring With Next-Generation Sensors and IoT Platforms
The Testing Equipment You Need to Keep Pace with Evolving EV Batteries
New Patch Can Help Control Robotic Exoskeletons
Engineering Soft Materials that Mimic Neural Tissue
Artificial Muscle Kits For The Classroom
New Light-Reactive Material for Smart Curtains & Light-Driven Motors
Is that a Smartphone or Microscope in Your Pocket? It's Both!
Using Mushrooms to Control Robots
Answering Your Questions: Lithium-Air Battery vs. Lithium-Ion
How Much Do You Know About Battery Technologies?
Comparison Between Wave Soldering and Reflow Soldering
Printed Electronics: The Future Is Flexible
New High-Performance Ultrafast Lasers That Fit on a Fingertip
Polycarbonate Seen As Top Choice for LED Lighting
The Modern Industrial Workhorse: PID Controllers
The Basics of Encoder Selection
Solving The Doping Problem: Enhancing Performance in Organic Semiconductors
Smart Sensor Technology for the IoT
Networking the IoT with IEEE 802.15.4/6LoWPAN
Announcing the Winners of the Rising Star Awards 2024
Laser Beam vs. Electron Beam Welding Which process works best for what?
Rising Star Award Winner 2024: Automotive/Transportation
Mechanical Carbon Materials for Aircraft Seal Applications
Brushless Motors for In-Tank Fuel Pumps
The Evolution of Precision Drug Delivery
Streaming Video Over Legacy Military Tactical Networks
AI's Role in Advanced Medtech Manufacturing
By submitting your personal information, you agree that SAE Media Group and carefully selected industry sponsors of this content may contact you and that you have read and agree to the Privacy Policy.
You may reach us at privacy@saemediagroup.com.
You may unsubscribe at any time.

High-Performance Gantries © 2009-2024 SAE Media Group