Swiss Federal Institute of Technology Zurich, Switzerland
Until recently, microscopic robotic systems have had to make do without arms. Now, a team at ETH Zurich has developed an ultrasonically actuated glass needle that can be attached to a robotic arm. This lets them pump and mix minuscule amounts of liquid and trap particles. Elesy Servo Drive
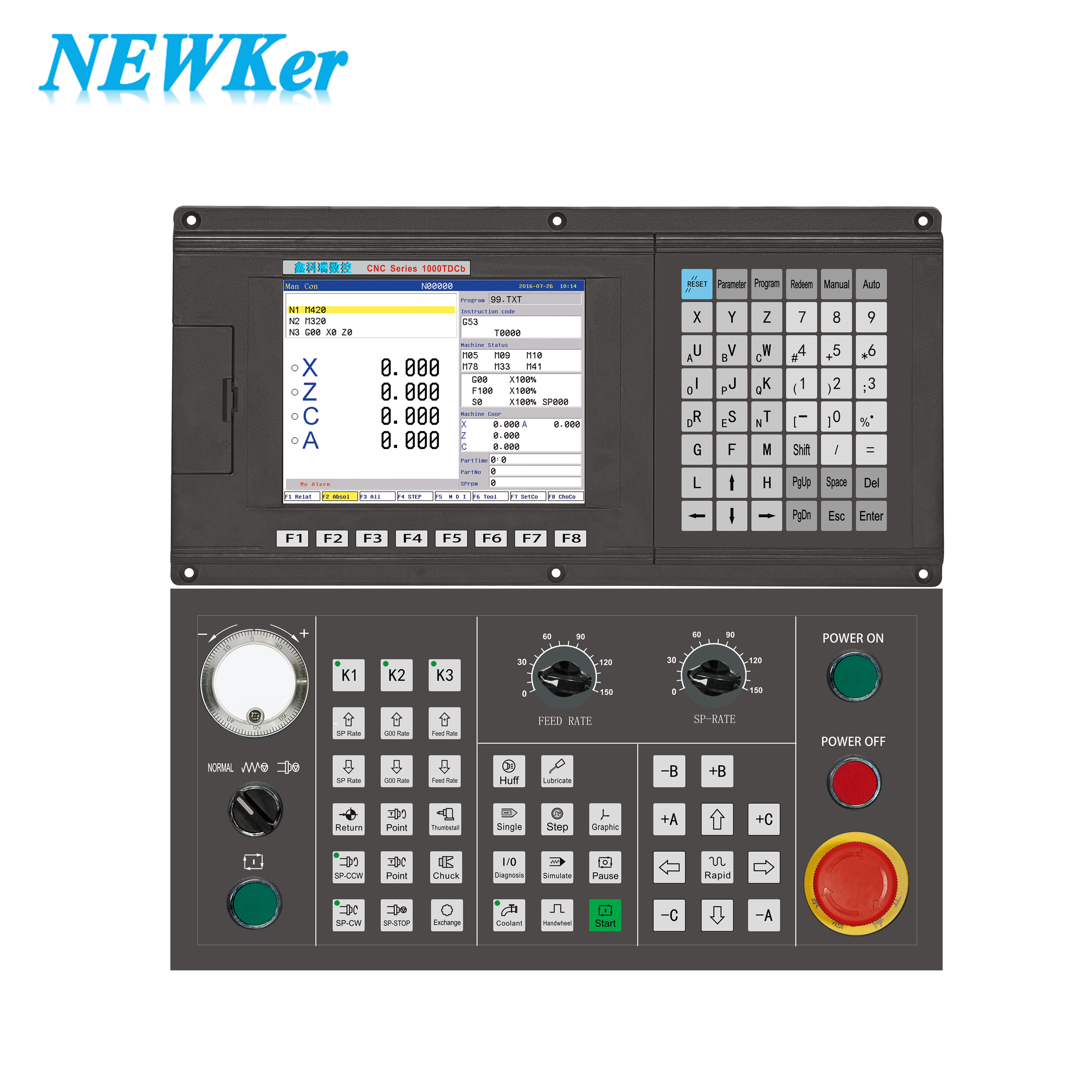
Prior to the team's breakthrough, miniature systems that transport miniscule amounts of liquid through fine capillaries have had little association with such robots. Such systems are known as microfluidics or lab-on-a-chip and generally make use of external pumps to move the liquid through the chips. To date, such systems have been difficult to automate, and the chips have had to be custom-designed and manufactured for each specific application.
The device, which was reported in Nature Communications, can be attached to a robotic arm, is suitable for performing a wide range of tasks in microrobotic and microfluidic applications, and can be used to automate such applications.
The device comprises a thin, pointed glass needle and a piezoelectric transducer that causes the needle to oscillate. It's akin to transducers used in loudspeakers, ultrasound imaging, and professional dental cleaning equipment. The researchers can vary the oscillation frequency of their glass needle; by dipping the needle into a liquid they create a 3D pattern composed of multiple vortices. Since this pattern depends on the oscillation frequency, it can be controlled accordingly.
The team was able to use this to demonstrate several applications. First, they were able to mix tiny droplets of highly viscous liquids.
“The more viscous liquids are, the more difficult it is to mix them,” said Professor Daniel Ahmed. “However, our method succeeds in doing this because it allows us to not only create a single vortex, but to also efficiently mix the liquids using a complex 3D pattern composed of multiple strong vortices.”
Second, they were able to pump fluids through a mini-channel system by creating a specific pattern of vortices and placing the oscillating glass needle close to the channel wall.
Third, they succeeded in using their robot-assisted acoustic device to trap fine particles present in the fluid. This works because a particle's size determines its reaction to the sound waves. Relatively large particles move toward the oscillating glass needle, at which they accumulate. The researchers demonstrated how this method can capture not only inanimate particles but also fish embryos. They believe it should also be capable of capturing biological cells in the fluid.
“In the past, manipulating microscopic particles in three dimensions was always challenging. Our microrobotic arm makes it easy,” said Ahmed. “Until now, advancements in large, conventional robotics and microfluidic applications have been made separately. Our work helps to bring the two approaches together.”
As a result, future microfluidic systems could be designed similarly to today's robotic systems. An appropriately programmed single device would be able to handle a variety of tasks.
“Mixing and pumping liquids and trapping particles — we can do it all with one device,” said Ahmed. This means tomorrow's microfluidic chips will no longer have to be custom-developed for each specific application. The researchers would next like to combine several glass needles to create even more complex vortex patterns in liquids.
In addition to lab analysis, Ahmed can envisage other applications for microrobotic arms, such as sorting tiny objects. The arms could conceivably also be used in biotechnology as a way of introducing DNA into individual cells. It should ultimately be possible to employ them in additive manufacturing and 3D printing.
For more information, contact ETH Zurich media relations at This email address is being protected from spambots. You need JavaScript enabled to view it.; +41 44-632-4141.
This article first appeared in the January, 2024 issue of Tech Briefs Magazine.
Read more articles from this issue here.
Read more articles from the archives here.
All-Liquid Iron Flow Battery Is Safe, Economical
Universal Controller May Lead to Breakthroughs in Robotic Prostheses,...
Flexible “Skeletons” for Soft, Muscle-Powered Robots
Autonomous Navigation Kits for the Army’s Palletized Load System
New AI Tool Can Predict People’s Vaccine Attitudes
What Can AI Provide for Unmanned Ground Vehicles?
Implementing New APQP and Control Using Electronic Workflows
Using a Holistic Approach for Integrated Optimization of Electric Powertrains
Using Data Analysis Software to Model Semiconductor Yield and Define Optimal Process Space
The Road to Zero Prototypes: Live from VI-grade’s ZERO PROTOTYPES Summit 2024
Maximizing Efficiency and Speed on the Factory Floor With Modern LiDAR Scanners
Transforming Transportation Manufacturing: Unlocking Growth with Sustainable Energy Solutions
New Octopus-Inspired Gripper Enables Versatile Soft Adhesion
A Breakthrough in Fast-Charging Lithium-Sulfur Batteries
Answering Your Questions: Lithium-Air Battery vs. Lithium-Ion
New Semiconductor Detector Shows Promise for Medical Diagnostics
Comparison Between Wave Soldering and Reflow Soldering
Printed Electronics: The Future Is Flexible
Treating Liver Cancer with Microrobots Piloted by a Magnetic Field
Polycarbonate Seen As Top Choice for LED Lighting
Flexible “Skeletons” for Soft, Muscle-Powered Robots
The Modern Industrial Workhorse: PID Controllers
The Basics of Encoder Selection
Building Bionic Jellyfish for Ocean Exploration
Smart Sensor Technology for the IoT
Networking the IoT with IEEE 802.15.4/6LoWPAN
World’s First N-Channel Diamond Field-Effect Transistor
Laser Beam vs. Electron Beam Welding Which process works best for what?
RISING STAR AWARDS 2024 - Nomination Form
Mechanical Carbon Materials for Aircraft Seal Applications
Brushless Motors for In-Tank Fuel Pumps
The Future of Hybrid and Electric Military Vehicles
Data Precision in Wearables: The Challenge of Accuracy
Autonomous Navigation Kits for the Army’s Palletized Load System
By submitting your personal information, you agree that SAE Media Group and carefully selected industry sponsors of this content may contact you and that you have read and agree to the Privacy Policy.
You may reach us at privacy@saemediagroup.com.
You may unsubscribe at any time.
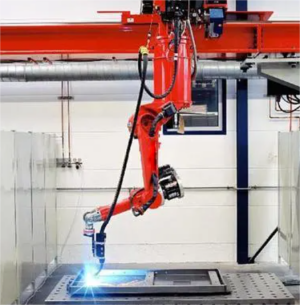
Electronic Arm © 2009-2024 SAE Media Group