A 360-degree look at resin conveying systems: types, operation, economics, design, installation, components and controls.
This Knowledge Center provides an overview of resin moisture and the drying process, including information on the best drying practices for your manufacturing facility. Ldpe Plastik
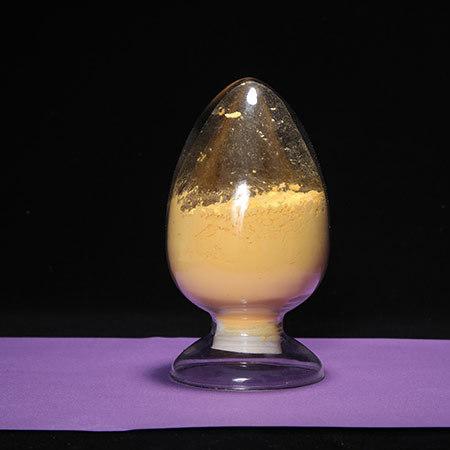
Combat the skilled labor shortage using this comprehensive resource to train your own plastics processing experts.
Deep dive into the basics of blending versus dosing, controls, maintenance, process integration and more.
This Knowledge Center provides an overview of the considerations needed to understand the purchase, operation, and maintenance of a process cooling system.
Learn about sustainable scrap reprocessing—this resource offers a deep dive into everything from granulator types and options, to service tips, videos and technical articles.
While the major correction in PP prices was finally underway, generally stable pricing was anticipated for the other four commodity resins.
Despite price increase nominations going into second quarter, it appeared there was potential for generally flat pricing with the exception of a major downward correction for PP.
First quarter was ending up with upward pricing, primarily due to higher feedstock costs and not supply/demand fundamentals.
Despite earlier anticipated rollover in prices for most of the volume commodity resins, prices were generally on the way up for all going into the third month of first quarter.
While price initiatives for PE and PVC were underway, resin prices had rollover potential for first two months of 2024, perhaps with the exception of PET.
Flat-to-downward trajectory for at least this month.
Resin drying is a crucial, but often-misunderstood area. This collection includes details on why and what you need to dry, how to specify a dryer, and best practices.
Take a deep dive into all of the various aspects of part quoting to ensure you’ve got all the bases—as in costs—covered before preparing your customer’s quote for services.
In this collection of articles, two of the industry’s foremost authorities on screw design — Jim Frankand and Mark Spalding — offer their sage advice on screw design...what works, what doesn’t, and what to look for when things start going wrong.
In this collection, which is part one of a series representing some of John’s finest work, we present you with five articles that we think you will refer to time and again as you look to solve problems, cut cycle times and improve the quality of the parts you mold.
Gifted with extraordinary technical know how and an authoritative yet plain English writing style, in this collection of articles Fattori offers his insights on a variety of molding-related topics that are bound to make your days on the production floor go a little bit better.
In this three-part collection, veteran molder and moldmaker Jim Fattori brings to bear his 40+ years of on-the-job experience and provides molders his “from the trenches” perspective on on the why, where and how of venting injection molds. Take the trial-and-error out of the molding venting process.
Mike Sepe has authored more than 25 ANTEC papers and more than 250 articles illustrating the importance of this interdisciplanary approach. In this collection, we present some of his best work during the years he has been contributing for Plastics Technology Magazine.
In this collection of content, we provide expert advice on welding from some of the leading authorities in the field, with tips on such matters as controls, as well as insights on how to solve common problems in welding.
Mold maintenance is critical, and with this collection of content we’ve bundled some of the very best advice we’ve published on repairing, maintaining, evaluating and even hanging molds on injection molding machines.
Thousands of people visit our Supplier Guide every day to source equipment and materials. Get in front of them with a free company profile.
NPE2024: Lowering barriers to additive manufacturing adoption in toolmaking.
Allegheny Performance Plastics turned to 1factory's cloud-based manufacturing quality control software for streamlined, paperless quality systems.
To design the best mixers for single screws, you must completely understand how polymer moves through a mixer channel or groove.
NPE2024: Focus is on additives for plastics including PVC and WPC industries.
At NPE2024, Novatec moves to rewrite the rules for material conveying with patent-pending smart-pump technology.
While the major correction in PP prices was finally underway, generally stable pricing was anticipated for the other four commodity resins.
With no minimum order and an impeccable record of on-time delivery, Precision Color Compounds is becoming a force in the color masterbatch business.
Thermosets were the prevalent material in the early history of plastics, but were soon overtaken by thermoplastics in injection molding applications.
After a six-year hiatus, this year’s show was a resounding success, with meaningful technologies on display that will help processors run their businesses more efficiently.
Key factors for the progress are innovative materials, advanced automation and precision engineering.
Topping five other entries in voting by fellow molders, the Ultradent team talks about their Hot Shots sweep.
Serendipitous Learning Opportunities at PTXPO Underscore the Value of Being Present.
Introduced by Zeiger and Spark Industries at the PTXPO, the nozzle is designed for maximum heat transfer and uniformity with a continuous taper for self cleaning.
Ultradent's entry of its Umbrella cheek retractor took home the awards for Technical Sophistication and Achievement in Economics and Efficiency at PTXPO.
technotrans says climate protection, energy efficiency and customization will be key discussion topics at PTXPO as it displays its protemp flow 6 ultrasonic eco and the teco cs 90t 9.1 TCUs.
Shibaura discusses the upcoming Plastics Technology Expo (PTXPO) March 28-30
Oerlikon HRSflow’s T-Flow HRS control has launched with three models that are configurable to multiples of six zones.
NPE2024: Dukane’s new Ultrasonic Thin Wall welding system is well suited for welding applications of PP to PP TD25 painted parts.
Series offers higher output, lower melt temperatures and energy savings.
Noting that geopolitical changes require new corporate strategies, European plastics and rubber machinery trade groups announced that incoming orders fell 22% in 2023.
System tracks, controls and saves everything from material recipes to process parameters, operator activity from logging on to start, to emergency stops and more.
Unit is designed to match the requirements of feeding low bulk density fillers and materials in the compounding process.
Mixed in among thought leaders from leading suppliers to injection molders and mold makers at the 2023 Molding and MoldMaking conferences will be molders and toolmakers themselves.
After successfully introducing a combined conference for moldmakers and injection molders in 2022, Plastics Technology and MoldMaking Technology are once again joining forces for a tooling/molding two-for-one.
Multiple speakers at Molding 2023 will address the ways simulation can impact material substitution decisions, process profitability and simplification of mold design.
When, how, what and why to automate — leading robotics suppliers and forward-thinking moldmakers will share their insights on automating manufacturing at collocated event.
As self-imposed and government-issued sustainability mandates approach, injection molders reimagine their operations.
August 29-30 in Minneapolis all things injection molding and moldmaking will be happening at the Hyatt Regency — check out who’s speaking on what topics today.
Get your clicking finger in shape and sign up for all that we have in store for you in 2023.
Molding 2023 to take place Aug. 29-30 in Minnesota; Extrusion 2023 slated for Oct. 10-12 in Indiana.
Join this webinar to learn about Conair's patented Conveying with Optimizer system, which utilizes artificial intelligence (AI) to overcome resin conveying issues automatically. Conveying with Optimizer uses valves, remote sensors and AI to eliminate conveying challenges that operators face daily throughout the plant. With this new fully-retrofittable solution, interruptions like clogged filters, air leaks, changes in density or distance, moisture changes, and operators making manual adjustments can all be eliminated with Conair's Conveying with Optimizer. Agenda: What exactly is Conveying with Optimizer? What are the benefits of using Conveying with Optimizer? What problems does Conveying with Optimizer overcome? How to upgrade your system
Cooling time is typically the longest step of the molding process. How can you make it more productive? Learn how cooling time can be turned into production time by running two molding processes simultaneously on a single molding machine. For longer cycles, this can mean twice the productivity. In this webinar, you'll learn more about the Shuttle Mold System and how to calculate its potential productivity impacts for your application. Agenda: Learn how the Shuttle Mold System can deliver value to your business See the recent technical updates made to the system Calculate the potential impact on productivity
Discover possible applications in large format printing including layup tools, transport modules, film fixation devices, design components and enclosures. These are used in various industries such as automotive, aerospace, architecture and many others. Agenda: Possible applications in large format printing: layup tools, transport modules, film fixing devices, design components and enclosures. Process reliability and component quality in component production Pros and cons of the technology Sneak peek into current development projects—What will the large format printing of tomorrow look like?
In this webinar, Cold Jet will discuss some of the ways processors use dry ice such as in-machine mold cleaning at operating temperatures, de-flashing or de-burring parts, improving OEE scores, extending mold life, cleaning parts before painting, post-processing 3D printed parts, lowering GHG emissions, and monitoring and reporting the process. Agenda: Cold Jet Overview & Dry Ice 101 Understanding the Process and Fine-Tuning Techniques Case Studies: Applications in Plastics Monitoring the Process Exploring the Importance of Dry Ice Cleaning in an ESG Era
Finding it hard to get technical talent? Experiencing the pain of a knowledgeable, long-term employee's retirement? Learn how plastics processors are training generative AIs on their operations and unlocking the value from their tribal knowledge. Plastics processors are training generative AI models on their operations — from machine manuals to tools, polymers, procedures, maintenance records and engineering projects. Applying generative AI in the right ways can lower plastics processors' costs, improve overall equipment effectiveness (OEE) and upskill teams. In this webinar, you'll learn how to deploy AI technical assistants to your teams, what works and what doesn't, and how to use AI to build an organization that never loses tribal knowledge and fosters inter-team collaboration. Agenda: What is generative AI and how can its cognitive abilities be applied to plastics? Case study: how an injection molder trained a large language model on manuals and maintenance records to reduce downtime Case study: using generative AI in engineering teams to improve product development Live demonstration of a generative AI deep-trained on plastics knowledge Looking to the future: five predictions for an AI-augmented workforce in plastics
Turnaround time can be as low as 24 hours, although two or three days might be more typical. Rapid prototyping like this is especially useful to quickly identify critical end-use part geometries that will work in the molding process. Key components include material choice, 3D printing technology selected, use of adaptable mold bases for the mold inserts and implementation of appropriate injection molding process conditions. This presentation will review work conducted toward the assessment of a high-stiffness, high-temperature-resistant ceramic modified urethane acrylate for injection molding inserts. Agenda: Guide for 3D-printed injection mold inserts Optimization of digital light processing (DLP) printing Compatibility with various thermoplastics Real-world application success stories
The Society Plastics Engineers (SPE) Extrusion Division and the SPE Eastern New England Section will co-host the Screw Design Conference-Topcon on June 19-20, 2024 @ UMass Lowell in Lowell, MA. This highly technical program will focus upon screw design principles for single and twin screw extruders with wide ranging topics relating to screw designs for feeding, melting, mixing, venting and pumping plastics products and parts. Areas of focus will include screw designs for melt temperature and gel management, gel minimization, bioplastics, recycled materials and foaming. In addition to the technical sessions, a tour of the UMass Lowel Plastics Processing Laboratories will be integrated into Day 2 of the event. This program is not just for screw designers, but to help anyone responsible for any type of extrusion operation to evaluate existing extrusion equipment; and also to prepare for future projects. Technical Chair: Eldridge M. Mount III, e-mail emmount@msn.com Corporate sponsorships - A limited # of corporate sponsorships (15) are available on a 1st come basis. Included is a 6’ tabletop display (must fit on table), denotation in all promotional activities, and 1 no charge registration. To become a sponsor contact: Charlie Martin, Leistritz Extrusion, e-mail cmartin@leistritz-extrusion.com, cell 973-650 3137 General information: A reception on Day 1 and a tabletop display area will allow the attendees to meet and discuss state-of-the-art screw technologies with industry experts. The SPE Extrusion Division will issue a “Screw Design Certificate” to all participants who have attended the program. Students are encouraged to attend and will receive a discounted rate. For additional information contact: Program Chair: Karen Xiao, Macro Engineering, KXiao@macroeng.com
Debuting in 2010, the Parts Cleaning Conference is the leading and most trusted manufacturing and industrial parts cleaning forum focused solely on delivering quality technical information in the specialized field of machined parts cleansing. Providing guidance and training to understand the recognized sets of standards for industrial cleaning, every year the Conference showcases industry experts who present educational sessions on the latest and most pressing topics affecting manufacturing facilities today. Discover all that the 2022 Parts Cleaning Conference has to offer!
Presented by Additive Manufacturing Media, Plastics Technology and MoldMaking Technology, the 3D Printing Workshop at IMTS 2024 is a chance for job shops to learn the emerging possibilities for part production via 3D printing and additive manufacturing. First introduced at IMTS 2014, this workshop has helped hundreds of manufacturing professionals expand their additive capabilities.
Formnext Chicago is an industrial additive manufacturing expo taking place April 8-10, 2025 at McCormick Place in Chicago, Illinois. Formnext Chicago is the second in a series of Formnext events in the U.S. being produced by Mesago Messe Frankfurt, AMT – The Association For Manufacturing Technology, and Gardner Business Media (our publisher).
For extrusion blow molders, challenges of price and availability of postconsumer recycled resins can be addressed with a variety of multilayer technologies, which also offer solutions to issues with color, processability, mechanical properties and chemical migration in PCR materials.
Monolayer PCR bottles in back are dull gray, while multilayer ReCo bottles in front show off coloring flexibility. Cross-sectional view shows how multilayer technologies can hide even very contaminated PCR. Source: W. Müller GmbH
With each passing year, governments worldwide enact new legislation dictating the extent to which postconsumer plastics must be recycled and how much of that PCR should be incorporated into new plastic products. This regulatory landscape presents a formidable challenge for converters who must navigate the complexities of acquiring and processing these materials.
At W. Müller, we are known for our production of extrusion heads for blow molding machines. What many may not realize is that we operate two technical centers that have provided us with early access to recycling materials in collaboration with material manufacturers and recyclers to conduct comprehensive tests under varying conditions. Over the years, we've evaluated more than 50 different recycled materials from over 15 manufacturers globally, testing them across all our technologies, from one to seven layers, in bottles from 70 ml to 1 L. This research has also enabled us to observe the evolution of commercially available PCR materials over time.
Despite advances, blow molders still face numerous challenges in processing these materials. This article explores key challenges such as processability, odor, topload strength, migration, drop-test results, black specks, differences in color and material availability. The relevance of these challenges varies greatly depending on the regional infrastructure for material separation, collection, sorting and processing.
W. Müller’s two technical centers have evaluated more than 50 different recycled materials from over 15 manufacturers globally, testing them in one to seven layers, in bottles from 70 ml to 1 L.
Some PCR materials stand out for their excellent processability. They are typically colored white, ivory or a very light gray. In our tests with those materials, we started molding virgin HDPE into bottles and then changed to the good-quality PCR. We continued making bottles, adjusting the die gap to achieve the same bottle weight. Processing was very easy, there were no parison length variations, and the process ran stable. Some bottles had a couple of dark specks, but nothing to worry about. These materials still had a characteristic PCR smell — however, it was more the smell of a not too overpowering cleaning agent. These materials ran well even in monolayer bottles.
Nonetheless, this high-quality PCR has two big problems: price and availability. A big effort goes into sorting, cleaning and removing volatiles from waste to make that PCR material. All this takes energy and resources, which are reflected in a high price per pound. If price is not an insurmountable obstacle, then you will face the next problem: After sorting so much waste out of the stream to get pure HDPE, the yield of high-quality material is relatively small. If everyone decides to make a 100% PCR bottle out of these premium PCR materials, there will only be enough material available for a few customers.
FIG 1 – On left is a monolayer bottle of 100% PCR whose contaminants caused foaming and bottle distortion. On right is a three-layer ReCo bottle with the same PCR in the center main layer, while inner and outer virgin layers provide processing and mechanical stability and aesthetic appearance. Source: W. Müller GmbH
Conversely, some recycled materials present formidable challenges. In one case, we tested a PCR material for a recycler. We started with monolayer construction. As soon as the material came out of the die, it was obvious that that was not a material for blow molding. It produced a foamed, black/green parison with a lot of fumes, a horrible smell and some sort of oil dripping out and sticking to the die, pin and blow pin. The bottle? Nonexistent. The rough foam structure would not allow a bottle to be formed. What was supposed to be a 1 L round bottle looked like an ugly flower vase instead (see Fig. 1).
Adding coextruded outer and inner layers did not contribute much. This PCR material had some nylon in it, which has a higher melting point than HDPE. The unmelted nylon, together with the rough foam structure, still caused big holes in the bottles. After many tries with drying, filtering and changing processing parameters, it was possible to make three-layer bottles with 50% of this material in the center layer.
The good news is that the average real-world scenario lies somewhere in between the best and worst case scenarios described above. However, if it was possible to make the worst case scenario processable with three-layer technology, then there is a lot of hope for most recycled blow molding materials out there.
Limited availability and high cost of the best quality PCR can be offset by using multilayer blow molding technologies.
There are many multilayer blow molding technologies out there. We often hear about coextruding 11 layers or more in the film industry. But in blow molding, seven layers is the practical maximum. It is possible to make a head with more layers, but we haven’t found an application that actually needs more than that.
FIG 2 – A variety of multilayer technologies are available to provide specific functions – aesthetic, functional and/or processing-related. Source: W. Müller GmbH
At W. Müller, we offer, in addition to our single-layer technology (Mono), a diverse array of multilayer technologies (Fig. 2). Among these are DeCo and ReCo, comprising two (DeCo) or three (ReCo) layers of an identical material type (such as all-HDPE with layers of virgin and PCR). Additionally, our portfolio includes CoEx technologies, which entail coextrusion of different material types to achieve specific performance functions or properties, such as coextruding HDPE with EVOH or nylon for UV barrier, chemical barrier or oxygen barrier.
Many of you hear “multilayer” and immediately think that multilayer is bad for recycling. That is only true if you combine different polymers with a fairly large proportion of the minor component — for example, more than 6% EVOH oxygen barrier in an HDPE bottle. However, W. Müller heads are capable of making bottles with EVOH layers under 6%, which give you a fully recyclable bottle with a barrier.
Furthermore, DeCo and ReCo are multilayer technologies that use only one polymer type (such as only HDPE or only PP), which makes the bottle 100% recyclable in any recycling stream.
DeCo and ReCo offer monomaterial multilayer solutions for processing PCR, ensuring recyclability while maintaining product integrity. DeCo consists of two layers, usually a thicker PCR inner layer and a thinner outer layer with virgin material and color masterbatch (Fig. 3). This enables you to color your bottle and hide the PCR while minimizing the use of masterbatch. The layers are easily customizable, so you can vary the thickness depending on your needs.
FIG 3 – W. Muller’s two-layer DeCo technology facilitates coloring the bottle at minimum cost while hiding the PCR layer. Source: W. Muller GmbH
ReCo is a three-layer technology with a thinner outer layer, usually virgin with masterbatch; a thicker main or center layer, usually PCR with regrind; and an inner layer, usually just virgin (Fig. 4). The goal here is to save masterbatch, cover the PCR material, avoid contact between your product and the PCR, and improve the mechanical properties of the bottle.
FIG 4 – Three-layer ReCo technology can save masterbatch costs, avoid contact between a bottle and its contents, and improve mechanical properties of the bottle. Source: W. Muller GmbH
The good thing is that if you have a machine running with monolayer, you can retrofit this machine with a new W. Müller head to process with DeCo or ReCo. With a multilayer head from W. Müller, you have the flexibility to run either multilayer or monolayer bottles with that same head.
Many customers have complained about stability problems while processing PCR materials. Changes in parison length can cause problems such as fluctuation in bottle weight and changes in the position of the thickness profile, which lead to poor topload results.
The goal was to recognize and capture these differences objectively, and see if it is possible to reduce them. This project was a cooperation between the additive producer Baerlocher, recycler PreZero (active in Europe and the U.S.) and W. Müller. Baerlocher provided the additive Baeropol RST, which is made from a combination of commonly used, nonantioxidant polymer additives that together support polymer stability. This additive was compounded into a batch of PreZero PCR HDPE material. Then, batches of PCR HDPE with and without additive were sent to W. Müller for testing.
On our lab machine, cameras were installed on the front and on the side to take a picture of the parison at the same point during each cycle, which software analyzed to calculate the parison length. The gross and net weight of each bottle were measured, and the melt pressure in the extruder was controlled.
The process with the least variation in gross weight, melt pressure and parison length was that of the virgin bottle. The process with the most variation was monolayer PCR material without additive. When comparing the process variation for the PCR with and without additive, it was observed that the additive reduced the process variation when using the monolayer and ReCo technologies. It was also noted that using ReCo improved process stability for both the stabilized and unstabilized material. The variation in the parison length and melt pressure of the stabilized ReCo bottle was only slightly higher than that of the virgin bottle. This means that processing PCR with three layers can improve the stability of your process when compared with processing monolayer PCR.
FIG 5 – When HDPE waste arrives at a sorting facility, white bottles are segregated into one stream that becomes white or ivory PCR pellets (left), while all other colors are combined into a stream that becomes gray pellets (right). Source: W. Muller GmbH
Have you ever thought about how materials are sorted and why a lot of PCR materials are gray? When used plastic arrives at the sorting facility, white HDPE bottles usually will be sent to the white HDPE stream and colored bottles will be sent to the colored stream. Because all colors sent to the colored stream are mixed together, the resulting color of this mixture is gray. Depending on the colors sent, you get different shades of gray, but gray nonetheless. Because of the different shades of white and natural-color bottles entering the white stream, the result is a whiteish ivory material (Fig. 5).
It is tempting to buy those ivory colors and then add some color to make a nice PCR bottle. This is not the best approach to close the loop because you are taking material from the limited white stream and on the next product life cycle returning it to the gray stream, which few will want. If you buy the ivory PCR and mix in some white, then the bottle will end up again in the white stream and the loop is closed.
The only way to achieve widespread circularity is to find a place for those gray materials in PCR bottles. Does that mean that on your next trip to the drugstore you will only find gray PCR bottles? Not with our ReCo technology adding a virgin layer with color on the outside to cover the gray PCR material. With the DeCo and ReCo technologies, it is possible to use those gray PCR materials in nicely colored bottles. How much PCR can you use in this way? It depends on the technology and regrind use, but normally up to 80% in DeCo without regrind and up to 70% in ReCo without regrind or about 60% with regrind.
It is of course possible to use a gray PCR material in a multilayer bottle and color the outer layer white. This is not recommended because the bottle would end up contaminating the white stream with gray materials.
Some of you might think you can just color the gray PCR materials. This is possible, but the resulting color of the bottle will be nowhere near your original color, even if you increase your masterbatch use level from 4% to 8%. You will have a colored bottle, but it will still have a grayish tone and you will be spending double the money on masterbatch. Better to make a three-layer bottle and just color the outside layer. You are free to increase the amount of masterbatch in the one layer; you will still be saving money. The best thing? Your color will be either the same as your original bottle or a lot closer to it.
FIG 6 – Compare colors of a monolayer PCR bottle with 6% masterbatch (left), monolayer virgin bottle (center) with the same amount of masterbatch, and ReCo bottles with different three-layer structures and equal or lower masterbatch levels in just the outer virgin layer. Source: W. Muller GmbH
Let’s compare monolayer bottles (Fig. 6). Suppose your bottle weighs 70 g and you used 4% masterbatch in your virgin bottle. If you double the masterbatch level to 8% when using a gray PCR, you will be going from 2.8 g masterbatch to 5.6 g. If you make that same bottle in three layers, where the outer layer is 20% of total thickness, and you add 4% masterbatch only to that layer, you will be using only 0.56 g of masterbatch. Even if you double the amount of masterbatch in that outer layer, it is still 1.12 g, which is 60% less than you had in your virgin bottle. Imagine saving 60% in masterbatch costs and still getting a better color match than using monolayer? And you have an added benefit when using ReCo: Any black specks are covered by the outer layer (Fig. 7).
FIG 7 – Monolayer PCR bottle (left) shows black specks, which are hidden in multilayer ReCo bottle (right). Source: W. Muller GmbH
For the topload test, three bottles were produced: a virgin monolayer bottle, a PCR monolayer bottle, and a ReCo three-layer bottle with 70% PCR in the main (center) layer. This same test has been done with different bottle geometries and sizes.
Depending on the virgin material and the PCR material being used, the virgin bottle will most likely have the highest topload strength and the PCR monolayer bottle will have the lowest topload. With the ReCo structure you will see an improvement in the topload strength.
This test was also performed with the bottles made with PreZero PCR HDPE material and the Baerlocher additive. The additive also improved topload. Interestingly, the topload for the three-layer stabilized bottle was higher than the topload of the virgin bottle. That means that the ReCo technology alone already improves the topload, but material stabilization together with the ReCo technology could help reach or even improve topload results while using PCR.
Also, when comparing results of using monolayer with PCR and regrind and ReCo with PCR and regrind, improved topload was observed on the ReCo bottles (Fig. 8).
FIG 8 – Topload strength comparison of virgin (left), monolayer PCR (center) and ReCo bottle with PCR (right). Source: W. Muller GmbH
These results depend highly on the virgin and PCR materials being used. Bottle size and geometry also play a role.
Some cheaper, more available HDPE PCR materials will have some PP in them. This comes from, for example, caps that were not sorted out properly. PP in HDPE will cause problems with the welding seam, which will not close properly. This will cause problems in the drop test, where the bottle will probably break at the welding seam.
A test was performed where a virgin bottle, a PCR monolayer bottle, and a ReCo bottle were each dropped a maximum of five times from 6.5 feet. The virgin bottle survived all five falls without breaking, while the PCR monolayer bottle broke after about two falls. The inner and outer layers of the ReCo bottle helped stabilize the bottle, and thus the bottle survived all five drops, just like the virgin bottle (Fig. 9).
FIG 9 – In drop tests, monolayer gray PCR bottle (left) split at the weld seam after two falls, while white ReCo bottle with PCR in main layer (right) survived five falls intact. Source: W. Muller GmbH
The Regulation (EC) No 1935/2004 is an EU legislation that governs the general requirements for materials and articles intended to come into contact with food. It establishes the principles and procedures for assessing the safety of such materials and articles, and includes provisions for labeling and traceability. Our tests were performed according to that legislation. They measure the migration of substances from the plastic material into the contents of the container. These results were evaluated for use in cosmetics containers.
One test measured global migration in a monolayer PCR bottle and a ReCo PCR bottle. Even though both bottles had a global migration under 10 mg/dm² (which is the legal limit), it is important to notice that the monolayer PCR bottle had a global migration of 4 mg/dm² while the ReCo bottle had a global migration under 1 mg/dm². This was repeated with a different PCR material, and the results were similar — the monolayer PCR bottle had a global migration of 3 mg/dm² while the ReCo bottle had a global migration under 1 mg/dm².
We also observed that fewer substances migrated from the ReCo bottle. Many of the substances migrating from the monolayer bottle could not be found in the test of the ReCo bottle. The substances that would still be found migrating from the ReCo bottle had, in most cases, a lower concentration. Only two substances were found in higher concentrations from the ReCo bottle than the monolayer bottle. These substances were additives that migrated from the virgin layer.
Migration tests with four different materials and two different bottle sizes/geometries showed that the migration in the ReCo bottles is under the legal limit and therefore safe to use in cosmetic products, both leave-on and rinse-off.
It is important to mention that the inner layer is not to be considered a functional barrier and will not allow you to use a non-food-grade PCR material for a food-grade application. However, it can help make your product safer. If you are making a cosmetic product and are using a substance that has a concentration limit, you would not want that substance to migrate from the PCR into your product in amounts sufficient to cause you to exceed the regulatory limit.
Depending on your chosen technology (be it DeCo, ReCo or CoEx), the required head and extruder setup can vary significantly. Furthermore, the selection of a head producer can significantly impact the outcomes of your operations.
When processing PCR, precision in the design of both the head and extruder is paramount to accommodate the necessary multilayer configurations. This precision ensures exceptional tolerance for MFI fluctuations, which is crucial when transitioning between materials and colors. Ensuring that settings remain valid across transitions minimizes downtime spent adjusting parameters, thereby maximizing productive output.
At W. Müller, our team meticulously optimizes the channels of the head to streamline plastic flow, preventing the accumulation of deposits and abrasions. Neglecting this crucial step can lead to the introduction of additional black specks that may be erroneously attributed to the PCR material itself.
To effectively reduce masterbatch and plastic consumption, it's counterproductive to utilize a head with prolonged color and material changeover times, as each transition results in waste. Rapid changes in color and material not only bolster flexibility but also enhance overall productivity.
When processing multilayer materials, achieving uniform material distribution is vital. Poorly designed heads lead to inconsistencies in distribution, which lead to variations in layer thicknesses, resulting in either overuse of more expensive materials or localized thinning of inner layers in the final product, potentially leading to increased migration risks. Therefore, meticulous attention to material distribution is essential to ensure both cost-effectiveness and product quality. This is achieved through the use of simulation software, which enables us to model the flow channels and identify potential design issues before manufacturing begins. By simulating the flow dynamics, we can pinpoint and address any problematic areas, ensuring optimal material distribution and minimizing the risk of uneven layer thicknesses. This proactive approach not only enhances product quality but also saves valuable time and resources by mitigating issues before they arise during production.
With multilayer technologies, it is possible to improve the mechanical properties of bottles while using PCR materials. A colored outer layer enables you to cover gray and black PCR materials, black specks and impurities, while saving in masterbatch and getting a color closer to your original color.
The inner layer can help you reduce the substances that migrate into your products. The easy adjustment of the layers, depending on availability of the PCR materials, can help you to stay flexible.
It is important to make an informed decision when switching to PCR. Therefore, it is helpful for you to send us your virgin and PCR material ahead of time. We can (depending on the size) help you adapt your mold to our machine, and we can sample and test the bottles for you. That way, you can pick the technology and materials that are best suited to your application.
Varinia Lück earned a bachelor’s degree in chemical engineering from Universidad del Valle de Guatemala and a master’s degree in product management from the University of Oulu in Finland. After internships at Colgate-Palmolive and A. Schulman (now LyondellBasell), Lück joined W. Müller GmbH in 2018, where she serves as head of the Technology Center. She is responsible for R&D, with a particular focus on circularity (using recycled materials and biomaterials), barrier technologies, color change and foaming. Contact lab@w-mueller-gmbh.com; mullerheads.com.
The Tier One automotive supplier with compounding and blowmolding machine capabilities adds the 50-yr-old molder and moldmaker.
Producing plastics parts with undercuts presents distinct challenges for molders.
Here are processing guidelines aimed at both getting the PHA resin into the process without degrading it, and reducing residence time at melt temperatures.
A new study shows how the type and amount of LDPE in blends with LLDPE affect the processing and strength/toughness properties of blown film. Data are shown for both LDPE-rich and LLDPE-rich blends.
Follow these best practices to minimize loss of time, material and labor during color changes in molding containers from bottles to jerrycans. The authors explore what this means for each step of the process, from raw-material infeed to handling and reprocessing tails and trim.
NPE2024: W. Müller shows off new screen changers in response to increasing interest in blow molding recylates.
MuCell technology gains new momentum in blow molded packaging through this partnership of a leader in physical foaming with supercritical gases and a leader in coex blow molding hardware and controls.
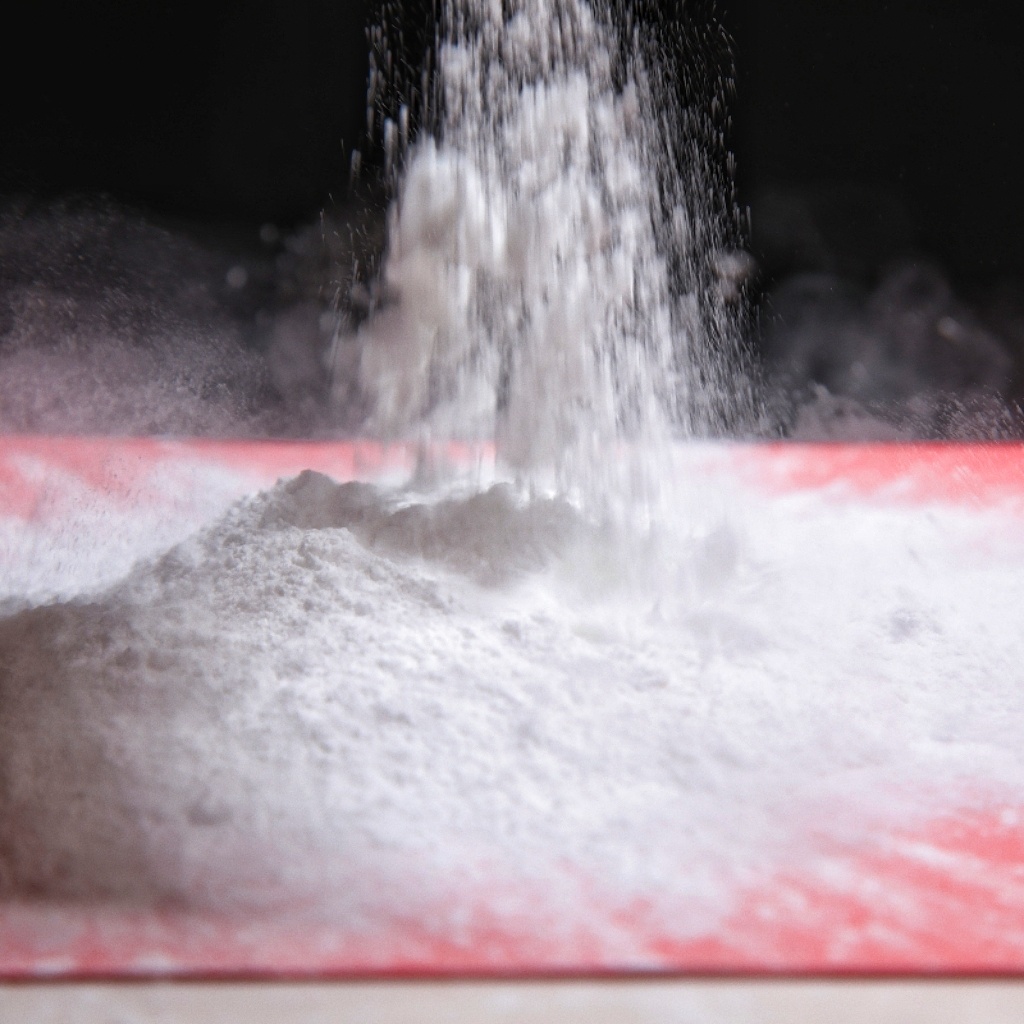
Meteorology Silicone, Plastics Technology covers technical and business Information for Plastics Processors in Injection Molding, Extrusion, Blow Molding, Plastic Additives, Compounding, Plastic Materials, and Resin Pricing. About Us