www.contractormag.com is using a security service for protection against online attacks. The service requires full cookie support in order to view this website.
Please enable cookies on your browser and try again. Smart Water Heater

www.contractormag.com is using a security service for protection against online attacks. The service requires full JavaScript support in order to view this website.
Please enable JavaScript on your browser and try again.
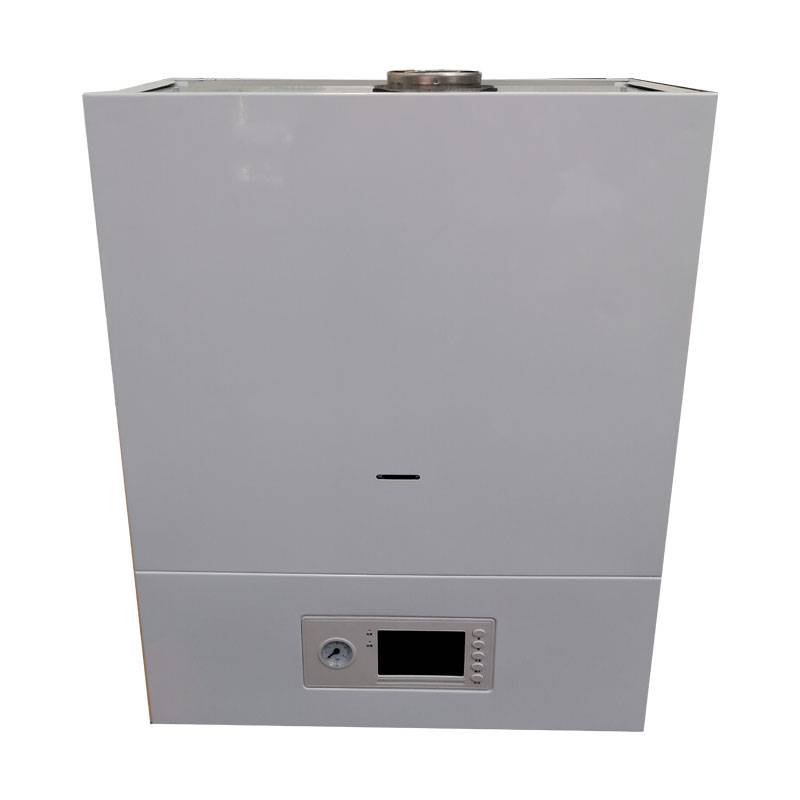
Wall Gas Boiler Water Heating www.contractormag.com is using a security service for protection against online attacks. This process is automatic. You will be redirected once the validation is complete.