www.laserfocusworld.com is using a security service for protection against online attacks. The service requires full cookie support in order to view this website.
Please enable cookies on your browser and try again. Handheld Fiber Laser Welding
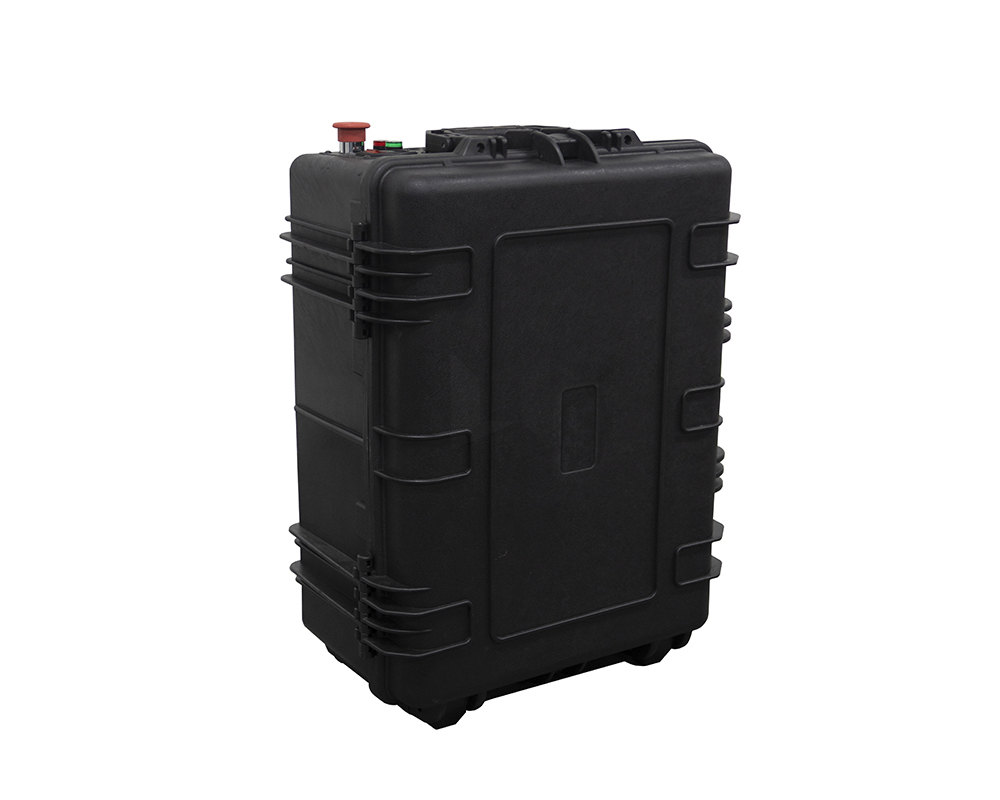
www.laserfocusworld.com is using a security service for protection against online attacks. The service requires full JavaScript support in order to view this website.
Please enable JavaScript on your browser and try again.
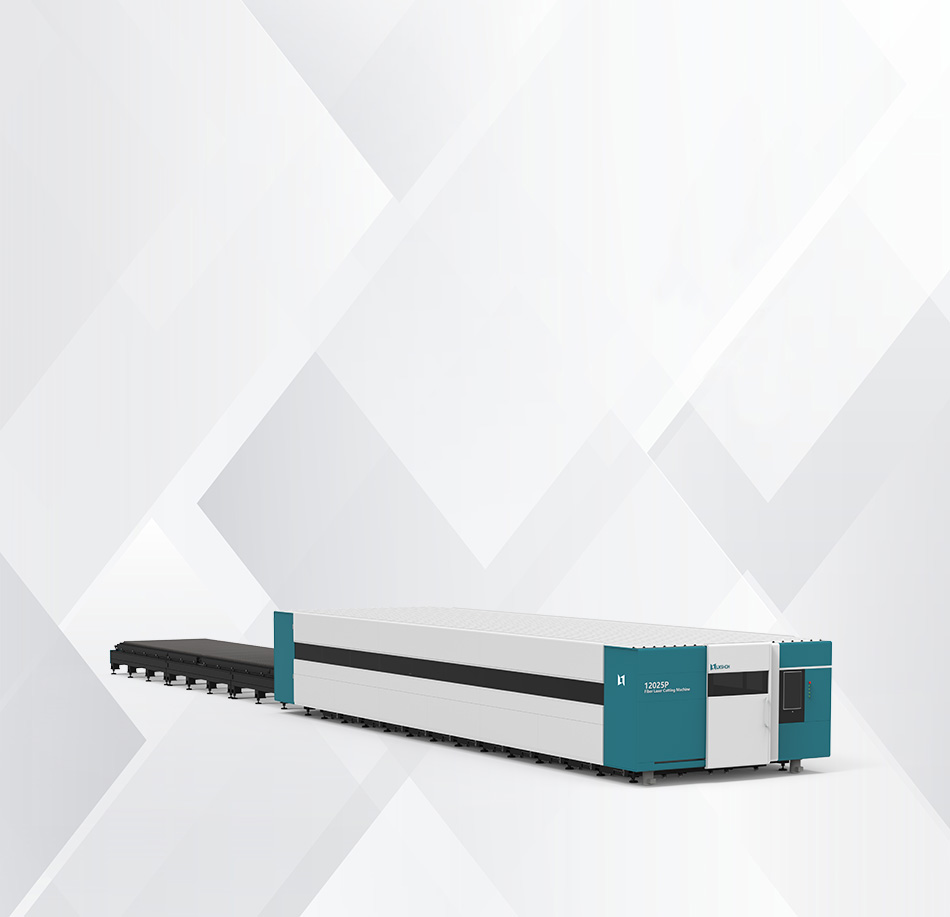
Laser Welding Near Me www.laserfocusworld.com is using a security service for protection against online attacks. This process is automatic. You will be redirected once the validation is complete.