The global compliance landscape continues to evolve at an unprecedented pace. In addition to compliance becoming increasingly detailed and specific by machine, process, application, environment, etc., many countries are introducing their own specific regulatory requirements. Some of these country specific requirements are based on harmonized international standards, but many include additional specific clauses and requirements. There is a maze of certifications that companies must navigate as they strive to deploy safe, reliable, and proven solutions at facilities across the globe. Bently Nevada has over 50 years of experience achieving and maintaining a full suite of compliance. Throughout our history, we’ve served as an integral and trusted member on many of the associated standards maintenance and development committees to ensure we fully understand the intent and reasoning behind each standard. Our industry leading compliance solution has been developed and maintained specifically to meet the needs of our global machinery protection and condition monitoring customers
Hazardous Area & Electrical Safety Certification 07 Ac 91
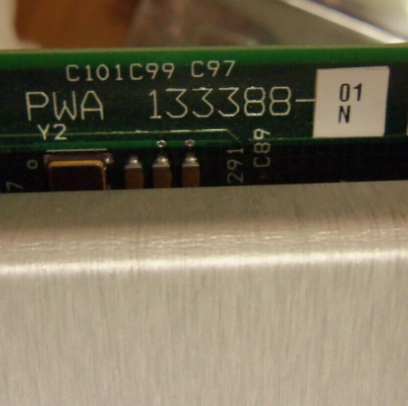
With the introduction of electrical power to general industry in the early 1900s came new risks. Sparking caused by simple lighting, passing of signals, and electric motors were the root cause of many explosive incidents in industries and applications where hazardous gases, vapors, materials, and dusts were present. This led to today’s hazardous area classifications and associated standards. Demand for more power and increased production capacity has produced larger power generating machines and industrial process machines with greater capacity to keep up with the demand. When operating, these machines are capable of generating tremendous amounts of energy and their rotating and process inertia represent an enormous hazard when uncontrolled. In an effort to protect the people, process, and environment these machines operate in and around, industrial safety standards have been created and adopted to govern minimum safety requirements.
Historically two hazardous area classification systems and sets of general safety requirements (originating in North America and the European Union) have been used globally. However, in the last ten years, the number of countries requiring certification and labeling to their own hazardous area and general safety standards has more than doubled and continues to grow. The flagship Bently Nevada 3500 machinery protection and monitoring system provides a fully 3rd party certified ATEX/IECEx zone 2 and CSA/NRTL/C class 1 division 2 and zone 2 solution which directly interfaces with our suite of transducers, cabling, and accessories. The sensors offer 3rd party certified options for use in hazardous locations up to ATEX/IECEx zone 0 and CSA/NRTL/C class 1 division 1 and zone 0 without requiring explosion proof and purged housings. The Bently Nevada product line also offers an extensive selection of country specific options in compliance with local certification and product marking requirements. This ensures that there are no costly local import fees or hazardous area inspection delays during commissioning or in operation associated with the Bently Nevada solution. As more countries harmonize standards to form the basis of their local regulations, adding their own clauses and labeling requirements, we will continue to add them as certified solution options.
Because of the catastrophic severity of some critical machine and process failure events, standards focused entirely on preventing and controlling the severity of dangerous failures have been developing since the early 2000’s. IEC 61508 is one such standard applicable to electrical, electronic, or programmable electronic equipment (E/E/PE) and provides detailed product design, deployment, operation, and lifecycle requirements which ensure an identified Safety integrity level (SIL) for safety instrumented systems and functions is met. It is common for safety critical scenarios, such as overspeed conditions, to require protective measures that meet SIL 3; whereas, protective measures for high vibration or temperature of rotating machinery typically demand SIL 1 or SIL 2.
Bently Nevada’s 3500 system and transducers offer 3rd party certified SIL 1 & SIL 2 components spanning from the sensor to the relay, for turbo machinery and reciprocating compressors covering a variety of measurements and protection architectures. The 3701/55 ADAPT ESD system provides 3rd party certified SIL 3 components for overspeed and other emergency shutdown applications. These products enable our customers to deploy a certified and compliant functional safety solution for a wide variety of machines and processes without the expensive and complicated addition of redundancy or additional separate protection systems and loops.
We are moving towards a more connected world, in which plants are equipped with networked sensors on their machines, providing big data to generate smarter analytics which can be reviewed remotely, allowing better operating decisions to drive greater business profitability. This high level of interconnection between the plant floor and management can increase the opportunity for cyber-attacks. Bently Nevada understands your need for network security, so provides a detailed 3500 hardening guideline, document 106M9733. This provides a comprehensive set of steps which can be taken for the 3500 system hardware, to mitigate any vulnerabilities and improve availability & reliability. For an additional layer of protection we offer Achilles communication certification level 1 (ACC L1) for our flagship 3500 system.
At the software application layer, to maximize the availability of diagnostic data at the business level while preventing unwanted access to critical protection configurations, we advocate the use of System 1’s database replication functionality. This allows for one-way data transfer through firewalls or data diodes.
Our continued focus on the security of our complete 3500 and System 1™ software solution ensures that our customers have access to the levels and layers of cyber protection that meet their needs.
Marine conditions are generally more severe than stationary environments, requiring machinery protection and monitoring systems that can withstand wide variations in physical vibration, temperature, humidity, electromagnetic, and other environmental conditions. Propulsion, on-board electric power generating systems, and process compression or pumping systems operating within harsh maritime environments and typically utilize gas turbines, steam turbines, or diesel engines. These critical machines have many of the same failure modes and extremely high consequences of failure as they do in land based applications. Maritime certifications provide users with added confidence that these critical machines are protected and monitored with instrumentation that is suitable for such service. The Bently Nevada 3500 system offers both DNV (Det Norske Veritas) and ClassNK (Nippon Kaiji Kyokai) maritime certifications, allowing our systems to be installed on-board marine vessels or mobile offshore platforms while meeting these stringent industry-standard certifications.
Protecting the environment from hazardous substances used and produced within industrial processes has been a point of focus and regulation for most of industrial history. As electronic systems have become more widely used in recent decades, regulations governing how they can be produced, used, and disposed of have also been developed. Since the early 2000’s regulations like Registration, Evaluation, Authorization and Restriction of Chemicals (REACH), Waste Electronic and Electronic Equipment (WEEE) directives, and Restriction of Hazardous Substances (RoHS), have initiated in the European Union and quickly been adopted by countries across the globe. These regulations aim to reduce the use of materials and substances that can be hazardous to human health and the environment and provide organized systems for controlling both the types and quantities of these chemicals that are permissible for electronic equipment and devices.
Bently Nevada is committed to maintain compliance of the 3500 system to these and other critical environmental regulations to ensure our global customers can continue to import, install, and operate these critical machinery protection systems.
As recent years have shown, when catastrophic incidents occur the costly machine and process consequences are minor compared to the potential environmental, brand, and personnel impact. These consequences pose not only serious threat to the people and communities directly involved but a near limitless liability exposure. Ensuring that people, machines, processes, and the environment are protected against catastrophic risks is essential and fundamental to the compliance landscape. The 3500 system provides this full compliance suite to ensure our customers receive the most reliable and industry accepted machinery protection which can be deployed in countries all over the world, in virtually any production environment, for a wide range of applications.
We follow closely the development and changes in these standards and continually demonstrate our capacity and commitment to be in sync with them as they change and evolve. This continued focus and investment in regulatory excellence ensures our customers don’t have to worry about deploying a non-compliant solution that may later require significant update or replacement. A compliance miss has the potential for exposure to catastrophic consequences, and also can lead to fines from governments and inspection agencies as well as impact on insurance rates and reputation. Bently Nevada is committed to continued compliance leadership and full regulatory excellence.
Bently Nevada has been synonymous with machinery protection and condition monitoring for more than 60 years. Our network of global experts is dedicated to helping customers solve some of their toughest challenges. From refineries and petrochemical plants to hydroelectric facilities and wind farms, Bently Nevada asset condition monitoring offers trusted and proven vibration monitoring equipment and a comprehensive services portfolio to help improve the reliability and performance of production assets like turbines, compressors, motors, generators, and everything in between.
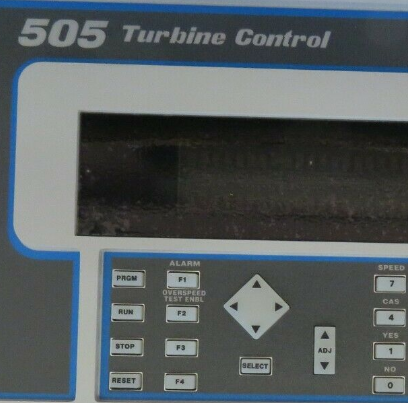
330425-02-05 Behind every suite of great products is a team of great people, and the Bently Nevada team is one of the most experienced in the industry. That experience translates into high-quality, flexible and scalable solutions coupled with a dedicated services team focused on providing proactive, consistent support throughout the lifecycle of your operations. Our domain experts can help you operate safely while maximizing plant uptime and efficiency.