Nikon’s New Metal 3D Printer Uses 3D Scanning for Part Repair and Quality Control
AML3D’s Ohio Expansion: Capital Infusion and Defense Contracts to Boost U.S. 3D Printing Operations Spherical Ceramic Sand
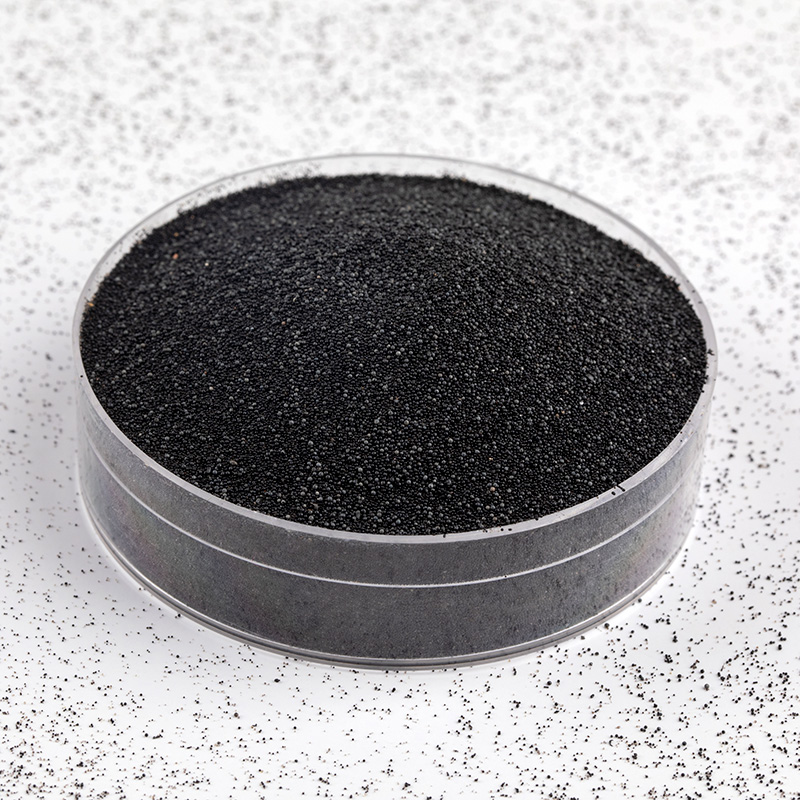
Micronics to Offer $2,999 SLS 3D Printer—Is it Real?
3DP/AM Market Insights: Q4 2023 & Annual
3DP/AM Market Insights: Q4 2023 & Annual
Additive Manufacturing in the Energy Sector: Market Analysis & Forecast
Additive Manufacturing for Military and Defense: Market Analysis and Forecast
3DP/AM Market Insights: Q4 2023 & Annual
Dig Deeper, Search Our Message Board 3dprintboard.com
Feature Your Job Posting Here
A curated collection of industry and product deep-dives.
Videos, podcasts, product reviews and free downloadable resources.
Nikon’s New Metal 3D Printer Uses 3D Scanning for Part Repair and Quality Control
AML3D’s Ohio Expansion: Capital Infusion and Defense Contracts to Boost U.S. 3D Printing Operations
Micronics to Offer $2,999 SLS 3D Printer—Is it Real?
Nikon’s New Metal 3D Printer Uses 3D Scanning for Part Repair and Quality Control
AML3D’s Ohio Expansion: Capital Infusion and Defense Contracts to Boost U.S. 3D Printing Operations
Micronics to Offer $2,999 SLS 3D Printer—Is it Real?
Tesla (Nasdaq: TSLA) is trying to master the art of casting large, complex car parts in one go. If it succeeds, it will change how cars are made, making it faster and cheaper to produce electric vehicles (EVs). According to a Reuters report, five people familiar with Tesla’s plans revealed that the company aims to revolutionize the traditional, complicated, time-consuming, and expensive process of creating large components like a car’s underbody, which typically requires assembling numerous smaller pieces.
To overcome these challenges, Tesla is looking into 3D printed sand molds, which are much cheaper and quicker to make than traditional metal molds. This way, they can test new designs without spending a ton of money. Reuters sources revealed that the carmaker is also experimenting with special types of metal that work well for these big, one-piece castings. The goal is to speed up how cars are made and make electric vehicles more affordable.
According to insiders who spoke to Reuters, this seemingly simple shift in material choice could be a game-changer for the entire industry. Traditional molds made from metal are expensive and time-consuming to alter. For example, a dashboard mold alone can cost between $100,000 to $150,000, while a mold for a bumper might range from $50,000 to $100,000. Engine component molds can start at around $20,000 and go up to $80,000 or more, depending on the complexity and material.
A single tweak in the design of these molds could cost as much as $100,000. But when it comes to creating an entirely new mold from scratch, the costs can soar up to $1.5 million, especially for large, complex structures like a car’s underbody. A sky-high figure like this accounts for detailed design work, specialized machinery and labor, rigorous testing to meet quality and safety standards, and the cost of durable materials required for casting. Such high costs make Tesla’s exploration of 3D printed sand molds a potentially revolutionary development in the automotive manufacturing industry.
In contrast, 3D printed sand molds offer a far more flexible and cost-effective solution. Engineers can easily revise designs using a digital design file and 3D printers, and a new sand mold can be printed within hours at a fraction of the cost. This dramatically shortens the design validation cycle from as long as a year to just two to three months, allowing for more rapid innovation and adjustments.
Moreover, Tesla leverages the flexibility of 3D printing with sand to experiment with intricate designs previously considered too risky or expensive. For instance, Tesla’s engineers can now include hollow subframes in their one-piece castings to reduce weight and improve crashworthiness. Engineers place 3D printed sand cores within the molds to create these hollow structures. After casting the metal, they remove the sand, leaving the desired hollow spaces behind.
Tesla prefers in-house solutions and tends to be secretive about its production techniques. Despite this, the company has embraced 3D printing for various purposes. A Forbes report revealed that Tesla’s applications of this technology range from creating door handles to prototyping entire chassis. For Tesla’s specific need to create 3D printed sand molds, binder jetting technology would be the go-to method. These printers rely on layering, spreading sand on a tray, and then selectively applying a liquid binder to shape the mold according to the digital design. The machine repeats the process layer by layer to complete the mold and then removes the unbound sand to reveal the finished product.
According to one Reuter source, the cost of “the design validation process with sand casting, even with multiple versions, is minimal – just 3% of doing the same with a metal prototype.”
While Tesla has been exploring this technology, other players in the industry, such as BMW and Cadillac (for its ultra-luxury EV CELESTIQ), have already embraced binder jetting for their applications. Interestingly, they have teamed up with voxeljet (Nasdaq: VJET), which uniquely offers sand printers large enough for such large-scale applications. Although other companies like Desktop Metal (NYSE: DM) and its recently acquired ExOne also offer binder jetting machines tailored for this type of application, Tesla could follow the steps of competitors. It’s worth noting that voxeljet currently faces some financial challenges, with a market cap of just $10 million, less than a year of cash runway, declining earnings over the past five years, and recent share price volatility. Given Tesla’s inclination for in-house solutions and voxeljet’s specialized capabilities, Tesla’s acquisition of voxeljet printers could provide financial stability to the 3D printing brand.
Earlier this year, CEO Elon Musk unveiled Tesla’s larger “unboxed” manufacturing strategy, which aligns with the company’s decision to use 3D printed sand molds. The approach aims to streamline production by creating large car sub-assemblies, snapping them together like building blocks. By mastering the art of casting large, complex structures in one piece, Tesla not only simplifies the manufacturing process but also stands to reduce production costs substantially.
Tesla has been a disruptive force in the automotive industry since its inception, revolutionizing multiple facets of EVs. From pioneering long-lasting lithium-ion batteries to developing a proprietary network of fast-charging stations, Tesla has consistently broken down barriers to EV adoption. Unlike traditional automakers, Tesla also introduced over-the-air software updates, enabling real-time improvements without requiring a trip to the service center.
Furthermore, Tesla’s groundbreaking massive Gigafactories have scaled up battery manufacturing to unprecedented levels, significantly lowering the cost of batteries for EVs. This is a departure from traditional manufacturing, which often lacks the scale and integration to drive down battery costs effectively. In addition, Tesla employs highly automated assembly lines, contrasting with the less automated and more labor-intensive processes commonly found in traditional manufacturing. These assembly lines use robotics and advanced software for increased precision. Tesla also engages in in-house component manufacturing, giving them greater control over the quality and efficiency of the production process, a contrast to the reliance on external suppliers typical of traditional automakers.
If successful, implementing 3D printing technology for sand molding represents just one facet of Tesla’s multi-pronged strategy to revolutionize the automotive industry. However, its potential impact could be enormous as a catalyst for accelerated EV production and a benchmark for future manufacturing innovation. If Tesla succeeds, it will not only fulfill its goal of producing cheaper and more accessible electric vehicles but may also set a new standard for car manufacturing worldwide.
Stay up-to-date on all the latest news from the 3D printing industry and receive information and offers from third party vendors.
CDFAM Returns to Berlin for Second Annual Symposium
Nikon’s New Metal 3D Printer Uses 3D Scanning for Part Repair and Quality Control
A startup called Micronics has recently unveiled a desktop powder bed fusion system priced at a mere $2,999. The team highlights the inclusion of its proprietary slicing software and the...
Japanese machine tool leader Sodick, a company with $400 million in revenue and 3,500 employees, has upped the ante into the additive manufacturing (AM) sector by investing in Prima Additive,...
In 3D Printing News Briefs today, we’re talking about an FDM 3D printer on Kickstarter, advancements in artificial eye creation, and 3D printed solenoids for electromagnets. Then we’ll move on...
As detailed in a previous post, metal 3D printer manufacturer Meltio launched its latest wire-laser metal deposition (LMD) machine, the Meltio M600, at its headquarters in Linares, Spain. There, I was...
Upload your 3D Models and get them printed quickly and efficiently.
Networking & Intelligence Summit, February 4-6, 2025
3D Printing jobs around the world.
Subscribe to Our Email Newsletter
Stay up-to-date on all the latest news from the 3D printing industry and receive information and offers from third party vendors.
© 2016 - 2024 3DR HOLDINGS. ALL RIGHTS RESERVED.
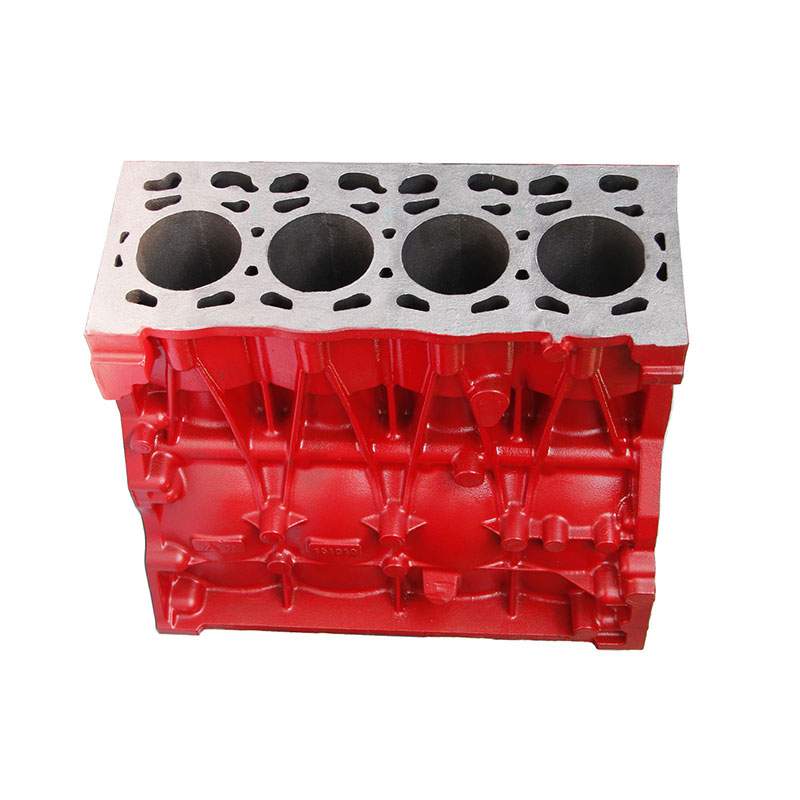
Aluminum Sand Register to view and download proprietary industry data from SmarTech and 3DPrint.com Questions? Contact info@3dprint.com