T he design and construction of fishing vessels has evolved over time, just like other modes of transport. But commercial vessels have a more complex and multi-faceted relationship with their users than do planes, trains and automobiles.
For instance, temporary living quarters are typically onboard for workers, making vessels both a home and office at sea. And with that being the case, commercial fishing vessels have a unique set of criteria when it comes to their design and construction. Free Cooling Chiller
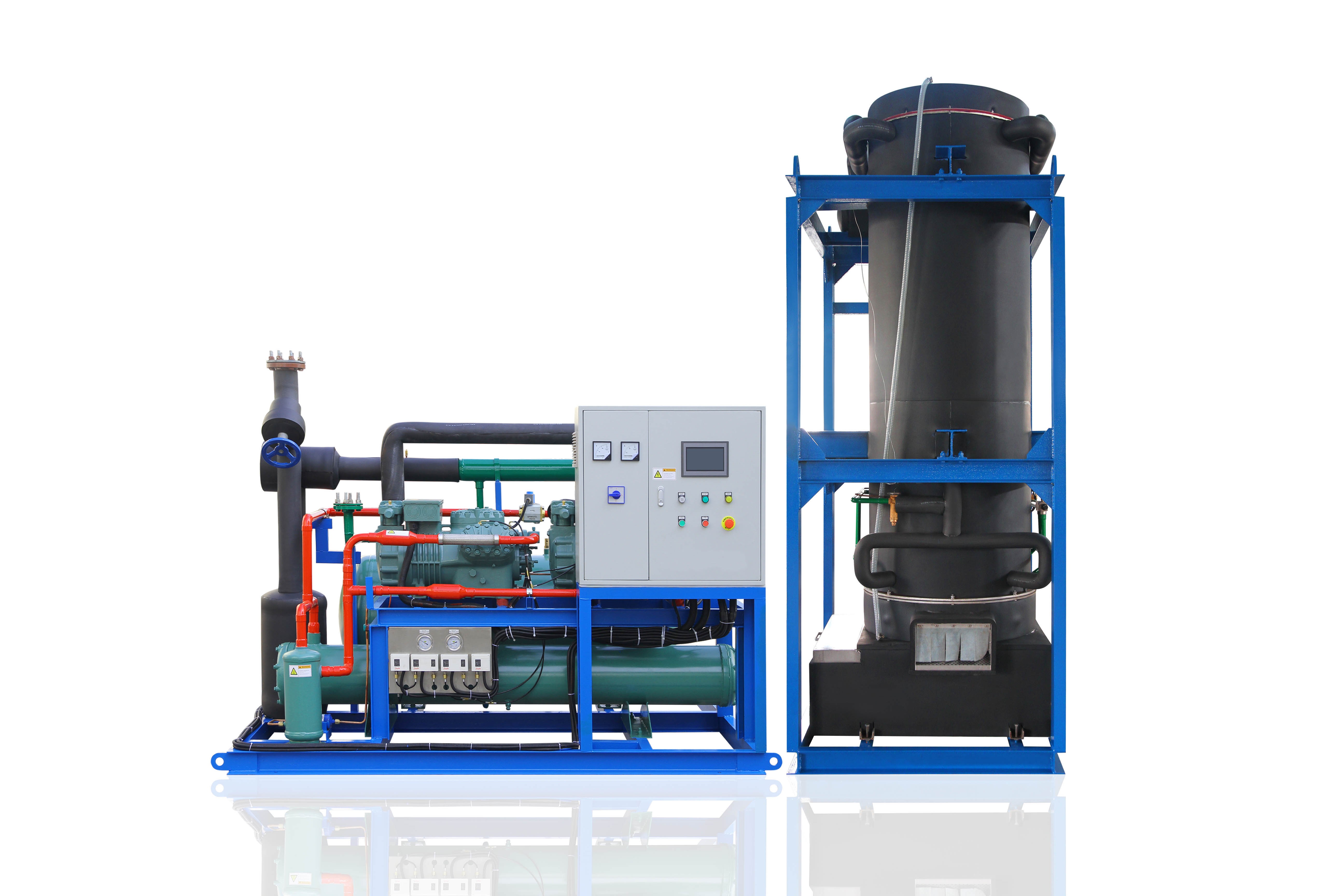
Whether it be automation, low emissions or even crew comforts, there’s a lot to consider when a vessel’s being designed, built or refurbished.
Fishermen’s News asked some of the notable companies on the West Coast and across the U.S. that offer fishing vessel design and construction services about current trends and developments in the industry. Here’s what they said.
Jim Towers, group principal and chief concept engineer with Elliott Bay Design Group, a Seattle-based marine engineering and naval architecture firm, said his company has seen a major push toward mechanization.
“We’ve been seeing a lot more automation, particularly on the big processing vessels,” he said. “That’s really the big change that we’ve seen in the boats we have been involved with as owner’s (representatives) or working on conversion work.”
Making cargo handling easier on crews is a goal for some boat owners, he remarked, but that also can result in the possibility of cutting crew numbers while also catching more fish.
Trending automized features, he said, include marine freezer plates on processor vessels, which transform freshly caught fish into frozen package-ready seafood. Workers use them to freeze flat products like fish fillets, packaging them into container blocks.
“The plate freezers, these used to be manually loaded and the panels were taken out manually once they were frozen. These are now automated so that the plate freezer crew is one person rather than four or five people,” Towers explained. “We’re seeing packaging get automated.
“There’s a move to palletize the cargo before it goes to the freezer hold rather than stowing boxes and then transferring the boxes ashore to be put onto pallets onshore,” he said. “So that cuts down turnaround times and it allows you to offload pretty quickly.”
Crowley Engineering Services Director of Projects Patrick Sperry said that the team has seen an increase in the general modernization of hull lines and upgraded equipment to support more efficient and sustainable business models.
“However, the proven equipment that has been a staple of fishing operations is still being employed,” he remarked. “Some improvements and efficiencies have been built into the trusted engineering baselines, and functionality and dependability remain key priorities.”
Robert Vorren, a chief designer with global technology, equipment and services company Kongsberg Maritime, said that another industry trend is a high focus on future fuel- and energy- saving capabilities.
“(A hull’s) hydrodynamic features (are) as important as ever,” he told Fishermen’s News. “Better tools as well as artificial intelligence (are) continuously helping us as designers to develop hull shapes with less resistance and therefore less power consumptions.”
“Different fishermen have different ideas about what new capabilities their next boat should have, but one thing that every new customer seems to agree on is that their new vessel should have more effective refrigeration than their old vessel,” said Mike Carr, an engineer/designer with Port Townsend, Wash.-based builder ACI Boats.
“All of our new builds for Bristol Bay have a 10-ton RSW (refrigerated sea water) system, whereas the old industry standard was 7.5 tons,” Carr stated. “Another feature that helps with product quality is the ability to chill the vessels 12 fish holds in three isolated zones. This is achieved using motorized valves and allows the operator to focus the vessels 10 tons of refrigeration capacity where it is needed rather than waste energy chilling fish holds that are not in use.
“It also allows for the fish to be floated in cold water, to prevent bruising,” he explained, “without requiring every fish hold to have slack water in it. This is a safety feature that the older generation of vessels typically doesn’t have.”
Towers added that the appearance of vessels also has changed a lot over the years.
“You go back and look at the vessels that were designed back in … the ‘80s and ‘90s for the processing fleet and the new vessels have a very different look to them,” he said. “I would say that they have become very much more stylish. There’s a lot more flow to the design.”
The larger processing vessels have a look that’s almost akin to a cruise ship, he commented.
What have vessel owners and operators been asking for recently as far as new and/or trendy features or add-ons to their fishing boats? The builders and designers Fishermen’s News spoke to had a range of answers.
Vorren: “They want their fishing boats to be efficient, cost effective, power saving and (have) nice designs. Fishing boats have always had engaged owners that want their vessels to look nice, but the trend we see lately is that the accommodation spaces and crew comfort must be top of the line to attract the best people as well.”
Towers: “We’ve seen a lot more electric deck machinery. The deck machinery used to be hydraulic, though some owners are still sticking with hydraulic deck machinery. So it’s kind of a split now.
“The electrics, they’re more efficient, but they come at a cost, and the reliability of the hydraulics is pretty good,” he continued. “So, some of the owners have elected to stay with hydraulic machinery, some have gone to electric.”
Sperry: “There have been significant advancements in crew comfort and technology integration to improve the quality of life and work for crew members while at sea. Owner-operators have been putting more thought into features such as shoreside communication technology and use, the convenience of charging arrangements, recreational equipment and providing well-provisioned space in general for their crew to utilize during their downtime.”
Carr added that wider vessels with more deck space are becoming increasingly common in Alaska due to the hazards associated with one specific aspect of the job.
“Some fishermen say that the most dangerous part of fishing in Bristol Bay is unloading,” he remarked. “This is usually done by unloading to larger vessels in open water and is often done in bad weather. The 32-foot length restriction in Bristol Bay has been compromising for the industry and modern advances in propulsion have made it practical to build very beam-y vessels.
“This allows for more deck space which not only makes it more efficient to work the gear, but also gives the crew room to stand safely out of the way of the bailer bags, that can weigh up to 1,000 pounds, getting lifted off the vessel by hydraulic crane,” he explained.
Are there any features or modifications for commercial fishing vessels that designers and manufacturers feel should be mandatory, or that they recommend to customers? Sperry said that across the industry, safety at sea is paramount and that newer vessel designs have moved the working decks of the vessels much higher above the waterline, providing increased shelter and greater stability.
“The new designs take safety and crew comfort to the next level along with greater efficiency in the equipment, making the industry even more sustainable with new assets being considered and designed,” he said.
Vorren added that he thinks vessels should have propulsion that enables them to use low power or less fuel when possible.
Carr observed that less than 10 years ago, many of the new vessels under construction for Bristol Bay were driven by a single propeller, but now, the vast majority of newbuilds are propelled by twin waterjets. These are the only types of vessels that ACI Boats builds for Bristol Bay work.
“Twin engines in propellor-driven boats have numerous drawbacks and were not popular in Bristol Bay,” he explained. “Twin waterjets offer far more advantages than disadvantages and the redundancy of twin engines can now be had without all the compromise.”
He also said that older Bristol Bay jet boats struggled with poor efficiency, but these days there are a lot more options, such as high thrust models and waterjets designed specifically for Bristol Bay.
“The correct waterjets—combined with the latest generation of high-output diesel engines—is giving the new generation of fishing vessels a capability to get on plane with a substantial payload of fish and travel four times faster than would otherwise be possible,” he remarked.
“The ability to travel fast allows fishermen to spend less time traveling and waiting to unload their fish and more time catching fish,” Carr added. “It also makes it possible for the fleet to spread out and cover more ground which helps reduce the crowded ‘combat fishing’ that occurs when hundreds of boats are competing over the same spot.”
Carr added that when it comes to new machinery, one of ACI Boats’ main priorities is “to sort the wheat from the chaff.”
“Some technologies can create new capabilities or provide a cost-effective alternative to older technologies, but it is easy to go astray,” he explained. “The wrong decisions can add unnecessary weight, cost, and complication that increases down time.
“It is of the upmost importance when designing and building a new fishing vessel to never lose sight of the goal of creating a cost-effective high efficiency and high performance new piece of equipment,” he said.
Towers said he thinks another thing that’s a big concern to the fishing fleet is the cost of replacement vessels.
“The capital cost of building replacement vessels in the United States is very high and most of the vessels have quite long lives,” he remarked. “You look at the processing fleet that’s working in the Alaskan, Washington and Oregon waters today, most of the boats were either converted or built in the late ‘80s, early ‘90s, and so you know, they’re reaching 35 years old.
“And it’s a challenge to the fishing owners—particularly the smaller boats, the inshore fishing fleet—it’s very difficult to justify building new vessels as quotas get shorter and stocks tend to dwindle,” he said.
Towers also said that one thing that’s liable to arise in the not-distant future is modifications to handle vessel emissions.
“Right now, almost all of the fleet is powered with diesel engines, running on fossil fuel(s),” he said. “There’s probably gonna be a push to look at alternative fuels. And that’s going to be a very interesting challenge.
“It hasn’t really started at this juncture, but we’re beginning to see it happening in the ferry industry, we’re seeing it in the offshore industry and we’re seeing it a little bit in the towboat industry, and I’m sure it’s going to come to the fishing fleet at some stage,” Towers said.
Towers has observed a big push to reduce emissions in the Pacific Northwest and elsewhere via legislation, regulations and other means.
“We’re seeing it in a lot of projects that we’re working on right now, (which) are aimed at reducing emissions,” he said. “We’re doing programs for Washington State Ferries, we’re working with the Waterborne Emergency Transit Authority in the Bay Area, so yeah—people are looking at this very seriously.”
Mark Edward Nero can be reached at mark@maritimepublishing.com
3980 Sherman St., Ste 100 San Diego, CA 92110
© 2021 Copyright Maritime Publishing. All Rights Reserved.

Liquid Nitrogen Tunnel Freezer Flipbooks are available to registered subscribers only. Subscribe now or log in for access.