As global populations grow and age, demand is increasing for all sorts of medical devices, from wearable fitness and condition monitors to lightweight and easy-to-use therapeutic and drug delivery devices. Wearables include smart watches and fitness trackers, wearable blood pressure monitors and pulse oximeters, and a growing range of bio- and virus-detecting sensors. There are also testing and therapeutic products including blood-glucose testing devices and wearable continuous glucose monitors, epinephrine and insulin pens, and implantable insulin infusion-delivery devices.
Taken together, health and medical devices constitute a substantial waste stream and pose costly disposal challenges for manufacturers, health providers and consumers. Many of these devices are powered and contain valuable components that can be recovered and reused, such as batteries, specialized circuitry and logic, precious metals, plastics and more. Today, however, few such devices are subject to recovery, reuse or recycling. Plastic Bumper Welder
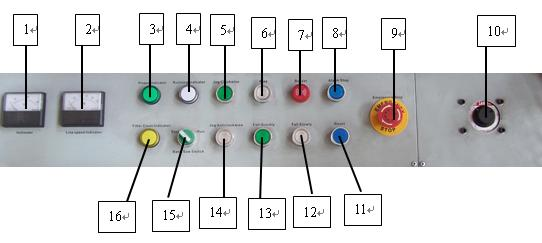
READ MORE: Laser Plastic Welding Technology
Obviously, any method of closed-loop recycling that could recover and reuse valuable components and materials could pay off handsomely for a device manufacturer’s bottom line. Thus, medical devices designed for use in a circular economy are getting a lot of attention.
Consider the structure of a typical “smart” medical device: Typically, it is a collection of components—power, electronics, readout, sensors—that are sealed into a compact, wearable or portable plastic case. Examples include a wristwatch or monitor on a wrist band, a handheld monitor, a sensor on a pendant, a finger-clip oximeter or a blood pressure cuff with a compact inflator/readout unit. Because ultrasonic and laser welds can economically and permanently bond durable plastics, they are often crucial to protecting sensitive device components.
But “permanent” welds are a double-edged sword. Should any devices fail performance tests during manufacturing, permanent welds (ultrasonic, laser etc.) cannot be opened without destructive disassembly. This makes it difficult for manufacturers to conduct failure analysis and can be challenging to recover valuable internal components for future use. So, as a practical matter, failed devices and all their valuable components become process waste. And that is a loss for manufacturers.
READ MORE: Choosing the Right Automated Joining Solution for Your Assembly Application
With an eye toward designing medical devices that serve the circular economy and reduce waste streams, device makers are taking increased interest in product designs and assembly technologies that can better support closed-loop recycling. The first and most obvious step in this process is to reduce and eliminate manufacturing waste by effectively reusing available components.
In response to inquiries from device makers, Emerson experts have developed a Branson plastic welding process that can safely and nondestructively “unweld” plastics commonly used in the bodies and cases of common medical devices and wearables. The process, which is now in commercial trials, employs the patented Simultaneous Through-Transmission Infrared (STTIr) laser welding technology developed by Emerson, together with product-specific disassembly tooling.
Using the experimental unwelding technology, device makers are successfully opening up plastic device cases, enabling nondestructive failure analysis and recovery of valuable, functional parts (such as wireless transmitter/receiver components, printed circuit boards, electronic subassemblies, displays and batteries) for assembly into new devices. Even the plastics from the disassembled devices are available for reprocessing or recycling.
This new unwelding process represents a substantial first step for manufacturers seeking closed-loop medical device reprocessing or recycling. It offers a means to maximize product yield and utilization of available components and materials—all the while minimizing waste and disposal costs associated with the manufacturing process—helping manufacturers pursuing UL 2799A, the Standard for Environmental Claim Validation Procedure (ECVP) for Zero Waste Classifications.
READ MORE: Finger to the Wind: MD&M West 2023 Exhibitors Call the Trends
While the immediate manufacturing benefits are potentially significant, the greater promise of this unwelding-disassembly technology may be found in the circular economy of the not-so-distant future. What if manufacturers, faced with high volumes of post-consumer medical devices, could safely and successfully disassemble them, recover high-value components and reprocess them for use in new devices?
What if, in the case of biohazardous wastes, such as dialysis care devices, they could perfect a way to disassemble, remove and segregate biohazardous components, then divide the remaining components—typically 90% or more of the device’s volume—for reprocessing, recycling or disposal?
Both of these scenarios offer almost unlimited potential, opening the door to large-scale recovery and reprocessing of millions of components and devices. In addition, the waste and cost-reduction potential alone is enormous, since the disposal of regulated medical waste costs 50 to 100 times more than the disposal of ordinary waste.
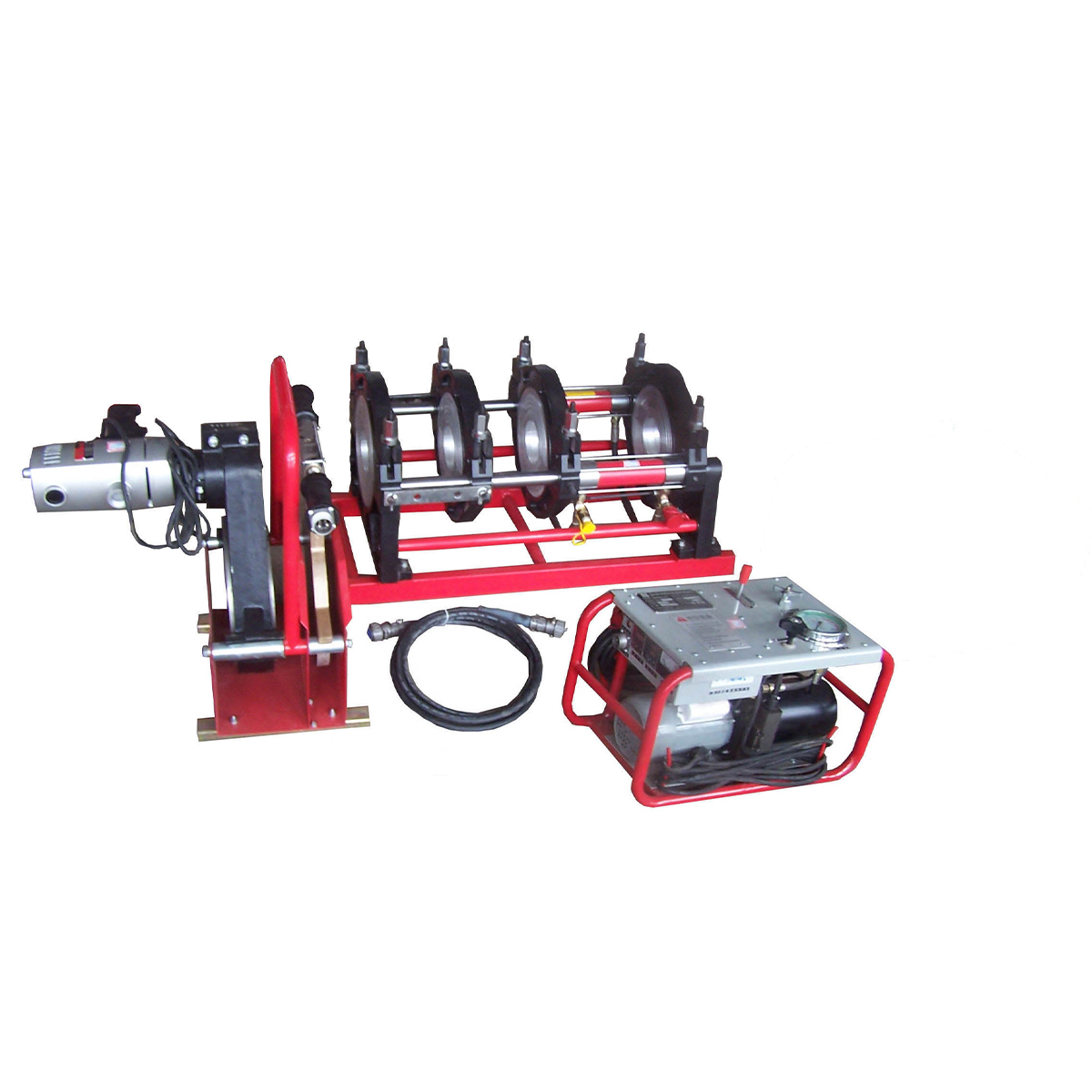
Plastic Air Welder Tom Hoover, medical business development manager–Americas, is based at the Emerson facility in Brookfield, Conn. He has in-depth medical industry experience in all aspects of product development and regulatory compliance.