Within the textile production process, dyeing has an outsize environmental impact, representing about a quarter of the total energy used from fiber to final product. It also leaches harsh chemicals into water, visibly coloring bodies of water in major production hubs. It is estimated that dyeing and finishing processes account for roughly 20 percent of global water pollution.
Contributing to change and a lower impact textile industry, wood-based fiber manufacturer Lenzing has been innovating with dope dyeing (also known as spin dyeing), which moves the dyeing process from the yarn, fabric or garment stage to the point of fiber production. After the wood pulp is dissolved into a liquid solution, pigment is added before the fibers are extruded through spinnerets. This can halve water use and reduce the carbon footprint of dyeing by 60 percent compared to conventional methods1. “Because you’re skipping the dyeing step, there are significant resource and energy savings that come along with that,” said Erica Redd, business development manager at Lenzing. Filament Pa6
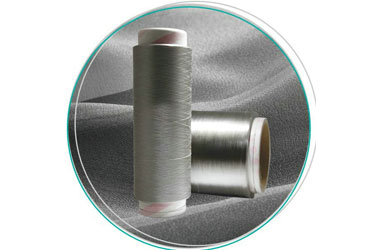
Lenzing’s recent dope-dyed launch is LENZING™ ECOVERO™ black viscose. This is the first spun-dyed fiber within the LENZING™ ECOVERO™ fiber family, giving manufacturers and brands a new, even lower-impact option within the viscose line. Related Stories Topics How 'Made in India' Supports the Industry's ESG Efforts Topics Source Fashion to Spotlight Diversity, Ethical Sourcing at February Show
Aside from the sustainability benefits of dope dyeing, the process is more cost effective and can cut wet processing spend by up to 80 percent2. Spin dyeing also provides inherent quality advantages. For one, there are no concerns with overdyeing. Additionally, because the fibers are dyed during production, the color is embedded in the fibers, which leads to long-term color retention, even when up against sweat, light and heat. Some black garments gray over time as the white core of yarn becomes exposed with wear, but since LENZING™ ECOVERO™ black viscose is black all the way through, this does not occur, and it continues to have a rich, black hue.
Since the color is locked in, it is also colorfast. Textiles made of LENZING™ ECOVERO™ black viscose won’t stain, and the color won’t rub off on other garments during laundering or wear. Conventionally dyed dark fabrics can also be discolored by peroxides in products used for teeth whitening, bleaching hair or acne treatments, but LENZING™ ECOVERO™ black viscose is not affected. “This durability results in clothing being worn longer, contributing to less waste and higher wear per garment, aligning with a more sustainable fashion industry,” said Redd.
Once consumers do decide to part with their LENZING™ ECOVERO™ black viscose textiles, the fibers including the dye will biodegrade. They are certified for biodegradability in soil, marine environments, fresh water and home and industrial composts.
Like all LENZING™ ECOVERO™ viscose, the spun-dyed fibers are made from PEFC- or FSC-certified wood. They are also backed by a fiber identification technology that physically verifies the fibers’ authenticity at each step in production. “Our fiber ID differentiates LENZING™ ECOVERO™ from a generic viscose,” said Redd.
LENZING™ ECOVERO™ black viscose began production at Lenzing’s headquarters in Austria. Starting later this year, it will also be manufactured at South Pacific Viscose in Purwakarta, Indonesia.
Innovation is constant at Lenzing, and spun-dyed fibers have been a key area for R&D. Prior to LENZING™ ECOVERO™ black viscose, Lenzing launched TENCEL™ Modal with Eco Color technology and TENCEL™ Modal with Indigo Color technology, the latter of which is geared toward the denim industry.
Picking a wood-based fiber for textile production largely comes down to personal preference and use cases. Viscose, modal and lyocell can all be used for knitting or weaving, but they have slightly different hand feels and aesthetics. This new launch opens the door for viscose users to have a dope-dyed solution in their fiber of choice.
LENZING™ ECOVERO™ can be blended with other fibers like cotton, polyester, wool, silk, linen and acrylic to provide characteristics such as breathability, hand feel and sheen. “LENZING™ ECOVERO™ viscose fibers bring a pleasant softness into fabrics, and they also create an airy, flowy drape,” said Redd. “This opens up a wide range of possibilities.”
In addition to LENZING™ ECOVERO™ black viscose, the fiber family is also growing with the recent launch of LENZING™ ECOVERO™ with REFIBRA™ technology. REFIBRA™ technology uses textile scraps as inputs for new fibers, creating a circular path for fabric waste. Previously, REFIBRA™ technology was only available for TENCEL™ Lyocell fibers. “The extension of REFIBRA™ technology is a really big accomplishment for the ECOVERO™ brand, making ECOVERO™ REFIBRA™ more circular,” said Redd.
Although the two fiber types are offered separately, there is an opportunity to combine them in a single product. For instance, companies could develop a mélange fabric using LENZING™ ECOVERO™ black viscose and LENZING™ ECOVERO™ viscose with REFIBRA™ technology, blending both yarns’ sustainability benefits in one.
LENZING™ ECOVERO™ fibers have a wide presence at retail, with more than 500 brands using the fibers for a range of categories including innerwear, loungewear, hosiery, tops and bottoms.
“Co-branding programs using LENZING™ ECOVERO™ have grown exponentially from 2019 to 2022,” noted Redd. “So we foresee brand partners’ interest in LENZING™ ECOVERO™ viscose fibers continuing to rise.”
Click here to learn more about LENZING™ ECOVERO™.

Spandex Lycra Material Receive Our Daily Newsletter & Special Offers