This paper was first presented at GPD 2023.
Link to the full GPD 2023 conference book: https://www.gpd.fi/GPD2023_proceedings_book/ Lightweight Sandwich Panels

Material efficiency and lightweight construction are increasingly required to meet the architect's desire for maximum transparency, homogeneous views and dematerialized façades. This motivates the development of innovative façade concepts using lightweight, thin glass-plastic composite panels as glazing. The sandwich panels consist of thin glass facings and a stiff and transparent polymer interlayer core. The lightweight polymer significantly reduces the dead weight of the glazing compared to conventional glass and provides high structural composite performance. In addition, the polymeric interlayer core allows for integrated mechanical joints with minimal mounting surface that go beyond conventional connection joints.
These properties enable new, unobtrusive methods of fixing in façade applications, accelerate the use of adhesive technology in façade construction due to minimal permanent loads, and pave the way for filigree substructure design. The innovative concept of NEERO-Façade exploits the low dead weight and the integrated mechanical joint design to develop a holistic, lightweight and highly transparent double-skin façade and was developed in joint research between KRD Coatings, Priedemann Fassadenberatung and TU Dresden. This paper describes the design concept and research process of NEERO-Façade, including the development of an integrated façade fixing and the slim substructure design. Furthermore, a case study demonstrates the design possibilities of NEERO-Façade for dematerialization and increase of transparency in façade design.
In modern architecture, the trend towards high quality glass façades with maximum transparency remains strong. Double-skin façade solutions with exceptional transparency are in demand, both for new buildings and as a protective envelope for energetic refurbishment and conservation of loadsensitive historic buildings.
A typical example of a highly transparent façade is a double-skin structure with a secondary glass skin as the outer shell for the entire building (Figure 1). The cavity between the primary inner layer of the façade and the secondary outer façade skin serves as a thermal and acoustic buffer zone. The secondary skin is responsible for dissipating environmental influences, while the primary skin maintains the separation. Doubleskin façades insulate the interior and allow windows to open for ventilation, even in harsh wind and weather conditions. In addition, the secondary skin protects the primary skin, which is important for energetic refurbishment and the conservation of valuable historic buildings.
Beyond their application in office buildings, the secondary skin can be used as a boundary and protection for courtyards, outdoor areas, lobbies, etc. The result is a significant increase in user comfort and energy savings paired with higher transparency and a shallow separation between interior and exterior spaces [1]–[3].
In particular, the dead load of the secondary skin and the acting wind loads are crucial for the dimensioning of the supporting structure. The high dead weight of conventional glass in conventional secondary skin layers require a strongly dimensioned substructure, immense brackets and a large number of glass fixings. These are costly due to their complexity, highly visible and result in loss of transparency.
Existing demands for maximum transparency, homogeneous views and dematerialized façade designs motivates innovative solutions and façade developments. One approach to maximum transparency with reduced substructure constructions is in the use of innovative lightweight, thin glass-plastic composite panels as glazing. The novel composite (NEEROGLAS® [5]) combines thin glass and a transparent polymeric interlayer core, which significantly reduces the dead weight of the glazing and provides high structural performance [6]. In addition, the polymer core allows for integrated mechanical joints with a minimal mounting surface that go beyond conventional adhesive or integrated connections in laminated glass [7].
These properties enable new, unobtrusive fixings in façade applications, accelerate the use of adhesive technology in façade construction due to minimal permanent loads and pave the way for filigree substructure design in highly transparent secondary glass skins.
The potential of dematerialization and transparent façade design has been investigated in a joint research project between KRD Coatings, Priedemann Fassadenberatung and TU Dresden. The innovative concept of NEERO-Façade chases three main design criteria: transparency, lightweight construction and slender design (Figure 2). Therefore, the low dead weight and mechanical joining method are used to design innovative integrated fixings. A slim substructure engineering leads to an overall lightweight and highly transparent façade construction.
This paper describes the design concept and research process of the NEERO-Façade project. First, the main features of the new composite panels as secondary skin are presented. Second, the development of a material-efficient integrated façade fixing is described. Third, the slim and modular design of the substructure is presented. A final case study demonstrates the design possibilities with NEERO-Façade.
The design concept of NEERO-Façade (Figure 3) is based on novel integrated façade fixings, enabled by the direct connection to the PMMA interlayer core and allowing for a homogeneous surface with an appealing design [7]. The substructure is designed in a slim version with a modular construction that exploits the reduced dead weight. The design results in overall dematerialization and increased transparency compared to conventional secondary glass layers in doubleskin façades.
2.2 Thin Glass-Plastic-Composite Panels as Secondary Skin Glazing
The new composite material (NEEROGLAS®) combines durable and scratch resistant thin glass facings with a stiff and transparent polymeric interlayer core made of polymethyl methacrylate (PMMA) (Figure 4). The lightweight interlayer core greatly reduces the dead weight compared to conventional laminated glass while still providing high structural performance. By using chemically strengthened glass, the panel strength can be increased significantly even beyond that of conventional thermally strengthened glass. The mechanical properties and composite behavior of the panels are extensively investigated in [8]. Accordingly, the composite material shows effective properties as a lightweight substitute for conventional glass in the building industry.
However, as the PMMA interlayer core fails brittle, the composite does not exhibit a satisfactory safe failure mode according to EN ISO 12543-2 [9]. To ensure a safe failure, two options were examined and optimized for the new composite material (Figure 5).
1) Lamination of an additional thin glass layer of 2 mm.
2) Applying a transparent multi-layer PET safety film (e.g. 3M™ Safety S70 Exterior Window Film [10]. Both options hold the fragments in place in the event of breakage and thus provide a safe failure mode [11]. This nominates the composite panels as suitable and durable secondary skin glazing with optical properties similar to conventional glass.
2.3 Integrated Façade Fixing
PMMA provides easy processing and machining. The higher ductility and impact strength allow for material efficient and unobtrusive punctual edge connections in the polymeric interlayer core. Investigations in [7], [13] demonstrate a high shear and tensile strength for mechanical screw- connections in relation to the embedding surface. The "Grande Arche" demonstrator at glasstec 2022 in Düsseldorf, Germany verifies the structural application as an ultra-lightweight segmented glass arch. The segments are connected by filigree edge connections to maximize transparency (Figure 6). This type of self-supporting installation with a very low dead weight and transparency has not been achievable with maximized conventional glass to any extent.
Based on the joining method, a new integrated façade fixing was developed as a singlepiece machined element as a combination of a mechanical and an adhesive joint. The development process (Figure 7) included various structural designs for an integrated and unobtrusive joint with a homogeneous exterior surface. In an adhesive selection study, six different transparent adhesives and their application methods were investigated. A numerical analysis of the façade fixing dimensions in [14] led to the final design parameters of the façade fixing (Figure 8). Supplementary experimental tests under bending and lateral forces verified high structural behavior and qualified the façade fixing for an effective load transfer even after glass breakage and failure of the adhesive joint [15]. The numerical and experimental investigations identified a room temperature curing two-component polyurethane adhesive (3M™ Scotch-Weld™ DP610 [16]) with a layer thickness of 0.5 mm as the most suitable. It offers high adhesion, strength and ductile failure with sufficient stiffness for increased load transfer. In addition, existing studies in [17], [18] confirm the adequate suitability of the two-component polyurethane adhesive for exterior applications.
In summary, the integrated façade fixing combines a mechanical edge connection with an adhesive joint at the back of the glazing. The permanent dead loads are transferred to the screwed edge connection, while the loads perpendicular to the surface are taken up by the adhesive point support. The adjoining construction can be either a rotationally fixed or a flexible connection that is attached to the façade fixing element. Following the new design of the façade fixing, the substructure and associated components were engineered.
The filigree substructure design is inspired by existing highly transparent double-skin façades. Design criteria such as the number of fixings, the structural connector bridging the gap between the primary and secondary skin and the integration with the primary façade influence the engineering. To provide a multifunctional design, the focus is on the use of commercial façade components from system suppliers. The modular approach (Figure 9) considers fixed and flexible connections to the façade attachment. Spider systems and L-bracket systems act as structural connectors. Integrated steel plate or bracket attachments anchor the secondary skin to the primary façade. For historic buildings an individual structural anchoring solution based on the wall or façade structure is required.
Due to the low dead weight of the secondary skin, commercial systems for solar shading or louvers combined with spider arms or L-brackets offer a complete range of connection solutions. This allows for a modular and simplified design that is adaptable to a wide range of primary façade types.
The developed façade solution is applied to a reference building within the scope of a case study analysis. In the investigated scenario, the building envelope consists of a double-skin façade with an outer NEERO-Façade level and a single-skin NEERO-façade in the courtyard area of the Figure 10a and b. In the case of the double-skin façade, the primary structure is a conventional stick system based on the catalog of a façade system supplier. As part of the case study design, different requirement scenarios, such as thermal expansion, wind- and seismic loads, as well as dead and live loads were considered. All loads were assumed within the framework of the investigated scenario, a reference office building located in Dresden, Germany with a height of 20 m.
The case study is investigated under the following considerations. A numerical study of the required number of fixings and the dimensions of NEEROGLAS® results in a minimum of four façade fixings per glazing in the dimensions of 1.2 m x 2.0 m. In order to meet the deflection requirements of 1/100 of span width according to DIN 18008 [19], a glass composition of at least 12 mm NEEROGLAS® (1 mm Thin Glass - 10 mm PMMA - 1 mm Thin Glass) is required. The stiffness is equivalent to a conventional 2 x 8 mm laminated glass with no shear interaction. For the chosen project scenario, the substructure is designed with a weld-on sleeve and an extension bar that connects the primary façade via a steel plate attachment system and a commercially available single or double leg spider system (Figure 10). The width of the cavity can be adjusted by the length of the bar. The use of NEEROGLAS® results in a unit weight of only 16.9 kg/m².
The digital visualizations (Figure 11) allow a qualitative assessment of the design, particularly in terms of transparency. The façade offers a homogeneous view with a limited number of unobtrusive elements in the substructure. The total weight of the secondary skin glazing is effectively reduced by 26% compared to a conventional glazing of laminated glass. The result is an aesthetically pleasing, slim design with increased transparency, slender construction and a dematerialized view of the double-skin façade.
The design is finally verified by the production of a first physical prototype by the means of a 1 m² façade cutout at a scale of 1:1 (Figure 12). It was exhibited at "Glasbau 2023" in Dresden, Germany, demonstrating the final design concept of the NEERO-Façade with lightweight, thin glass-plastic composite panels.
This paper summarizes the design concept and the research process of NEERO-Façade as a new concept of façade design with lightweight thin glass-plastic composite panels. The combination of the three main features: transparency, lightweight construction and slender design was evaluated.
The presented developments of NEEROFaçade confirm that the new design concept offers a suitable solution for maximum transparency, homogeneous views and dematerialized secondary skin. The dead weight can be reduced by 26% compared to conventional laminated glass. This allows for a slim substructure design. In addition, the integrated façade fixings result in an attractive design with minimal obtrusion. As a result, very high levels of transparency can be achieved in the secondary skin. Commercially available products from façade system suppliers allow for versatile and costeffective substructure solutions, both for new buildings and for energetic refurbishment and conservation of load-sensitive historic buildings with minimal changes to the existing appearance. Ease of assembly through lightweight panels and prefabricated integrated façade fixings enhances the construction.
The realized prototype has proven the technical feasibility of NEERO-Façade, that surpasses current design possibilities with conventional glass through its innovative design. The digital visualizations show the high transparency and aesthetics that can be achieved by using the new composite material NEEROGLAS® in the field of façade applications. According to the results of the NEERO-Façade research project, the most important design parameters in this context are the number and arrangement of the façade fixings as well as the dimensioning of the substructure. In particular, the weight reduction of the material has a positive effect on the slenderness and aesthetics of the overall construction. In the case study, only the use in double-skin façades and single glazing of intermediate temperature zones has been investigated. Due to the successful implementation, it is assumed that the material application can be transferred to other façade typologies, which has to be verified in further investigations. For final application, a project-related technical approval of the façade glazing with integrated fixings is essential. For this purpose, the existing results from experimental and numerical investigations within this research project serve as a comprehensive basis for the upcoming structural design.
The research is part of a joint project between Priedemann Fassadenberatung GmbH, KRD Coatings and the Technische Universität Dresden, supported by the German Federal Ministry of Economic Affairs and Climate Action. The authors thank KRD Coatings for the great collaboration within the research project.
[1] H. Poirazis, „Double Skin Façades for Office Buildings“, Lund Institute of Technology, Lund, Literature Review Report EBD-R--04/3, 2004. [2] A. Ghaffarianhoseini, A. Ghaffarianhoseini, U. Berardi, J. Tookey, D. H. W. Li, and S. Kariminia, „Exploring the advantages and challenges of doubleskin façades (DSFs)“, Renew. Sustain. Energy Rev., Bd. 60, S. 1052–1065, 2016, doi: 10.1016/j.rser.2016.01.130. [3] E. Souza, „How Do Double-Skin Façades Work?“, archdaily, 27. März 2023. https://www.archdaily. com/922897/how-do-double-skin-facades-work [4] U. Hestermann u. a., Baukonstruktionslehre. 1. Wiesbaden: Springer Vieweg, 2015. [5] R. Neeb, „EP 3 208 085 A1 Verbundscheibe“, EP 3 208 085 A1, 2017 [Online]. Verfügbar unter: https://register.dpma.de/DPMAregister/pat/PatAkteneinsicht?akz=1020160013818 [6] J. Hänig and B. Weller, „Load-bearing behaviour of innovative lightweight glass–plastic-composite panels“, Glass Struct. Eng., Bd. 5, Nr. 1, S. 83–97, 2020, doi: 10.1007/s40940-019-00106-5. [7] J. Hänig and B. Weller, „Integrated connections for glass–plastic-composite panels: an experimental study under tensile loading at +23, +40 and +60 °C and different glass build-ups“, Glass Struct. Eng., Bd. 7, Nr. 2022, 2022, doi: 10.1007/s40940-022-00174-0. [8] J. Hänig, „Development of Thin Glass-PlasticComposite Panels for the Building Industry“, Dissertation, Technische Universität Dresden, 2023. [9] EN ISO 12543-2, „Glass in building - Laminated glass and laminated safety glass - Part 2: Laminated safety glass“, European Standard, 2021. [10] 3M Germany GmbH, „3MTM Safety S70 Exterior Window Film Product Data Sheet“. 2018. [11] V. Puttakhun, J. Hänig, S. Natchai, and P.-R. Denz, „Visions of adhesive bonding – bonding techniques in facade applications“, in Klebtechnik im Glasbau, Berlin: Ernst & Sohn, 2021, S. 193–212. [12] EN 12600, „Glass in building - Pendulum tests - Impact test method and classification for flat glass“, European Standard, 2002. [13] E. D’Ettore, J. Hänig, und B. Weller, „Development of Novel Connection Joints for Glass-Plastic-Composite Panels“, in Engineered Transparency 2021, 2021, S. 237–250. [14] A. Abdirisack Musa, „Development of Façade Connections for Glass-Plastic-Composite Panels“, Master’s Thesis, Technische Universität Dresden, 2020. [15] M. Wittmann, „Development and Testing of Integrated Glass Fixings and Connections for Novel Glass-Plastic-Composite Panels“, Diploma Thesis, Technische Universität Dresden, 2021. [16] 3M Germany GmbH, „3MTM Scotch-WeldTM DP610 Product Data Sheet“. 2022. [17] F. Oikonomopoulou, T. Bristogianni, M. van der Velden, and K. Ikonomidis, „The adhesively-bonded glass brick system of the Qaammat Pavilion in Greenland: From research to realization“, Archit. Struct. Constr., Bd. 2, Nr. 1, S. 39–62, 2022, doi: 10.1007/s44150-022-00031-2. [18] C. Kothe, M. Kothe, J. Wünsch, and B. Weller, „Adhesive joints for bonded point fixings in façades and glass structures“, in Engineered Transparency 2016, 2016, S. 555–565. [19] DIN 18008-1, „Glass in Building - Design and construction rules - Part 1: Terms and general bases“, Beuth Verlag GmbH, German Standard, 2020.
2200 W. Salzburg Rd. Auburn , MI 48611 United States
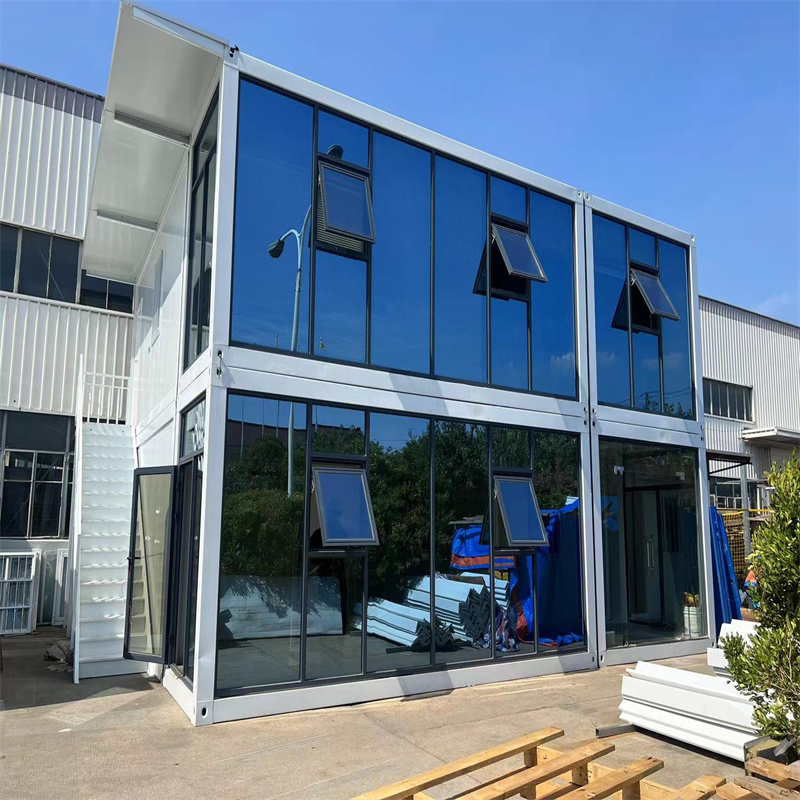
Prefabricated Sandwich Panels Log in or register to post comments