Comminution has become a topic of heightened interest for both the scientific and industry communities in recent years.
E&MJ highlights cutting-edge research in the field of comminution Heat Storage Balls
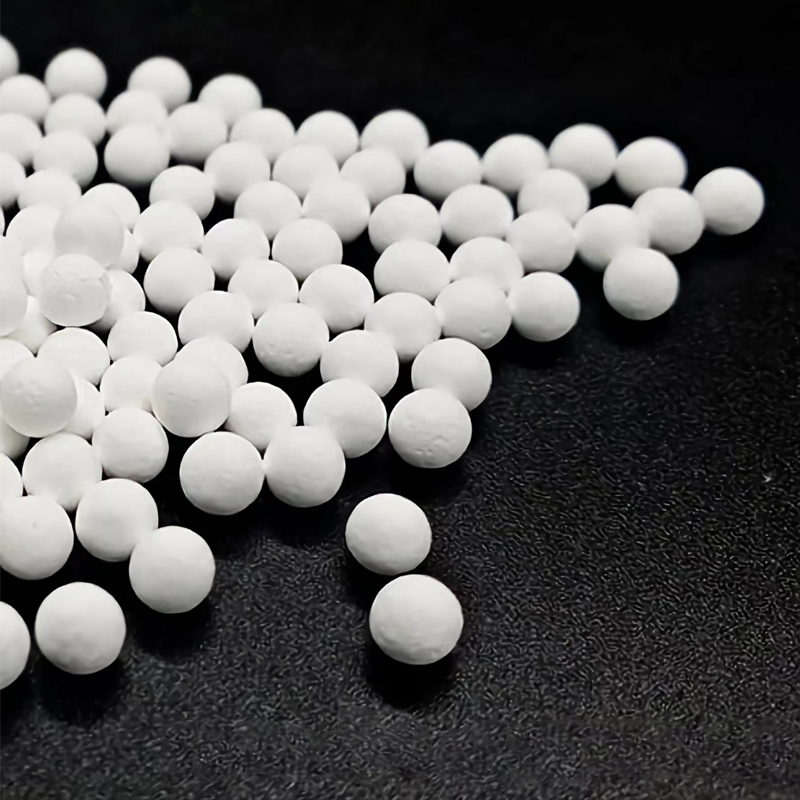
By Carly Leonida, European Editor
Although milling and grinding represent only a small number of steps within most mineral processing flowsheets, they are highly significant in terms of metals liberation and energy consumption. For example, a 2019 study by Bouchard et al. of three semi-autogenous grinding (SAG)/ball mill circuits (SABC) found that 91% of the energy input was lost, leaving only 9% available for ore breakage.
The opportunities for improvement in both areas are significant and, subsequently, comminution has become a topic of heightened interest for both the scientific and industry communities. A flurry of papers published and presented over the past 24 months have highlighted some innovative ways to achieve this, and the Coalition for Eco-Efficient Comminution (CEEC) has created a free-to-access online repository for these resources.
“The importance of improving grinding efficiency cannot be overstated,” Janine Herzig, executive president at CEEC International, told E&MJ. “By providing access to cutting-edge research findings, analytical tools, and fostering collaborative networks, CEEC empowers the sector to embrace eco-efficient grinding practices, ensuring that the production of essential materials aligns with the highest standards of environmental stewardship.”
Each year, the organization awards two medals that recognize outstanding research and field work on beneficial strategies for energy-efficient comminution, mineral processing, energy, water and tailings management.
The recipients of the 2022 technical research medal, Forster et al., summarized research undertaken as part of Natural Resources Canada’s Crush it! Challenge in their paper ‘Microwave heating behavior of ores and its application to high-power microwave assisted comminution and ore sorting’ (2021).1
As the authors explain, the utilization of microwave pretreatment offers a valuable option to reduce energy requirements in comminution. Microwaves can preferentially heat the valuable mineral phases in an ore, and the resulting differential thermal expansion leads to the formation of microfractures along the grain boundaries. As a result of the preferential heating, ore competency is reduced, mineral liberation is enhanced, a coarser grind size can be employed, and plant throughput can be increased. When combined with advanced ore sorting, microwave pre-treatment can also help to decrease the quantity of gangue material processed downstream and reduce tailings production.
“Conventional comminution circuits can be extremely inefficient…” stated Forster et al. “Given ever-increasing costs to mine depleting ore deposits coupled with more stringent environmental laws mandated by governments, it is exigent to develop more economic solutions. One possible solution is the application of microwaves for both assisted comminution and ore sorting.”
The paper explained how previous studies on the microwave treatment of ores over the past thirty years have mainly been limited to low power bench-scale studies and there is a lack of information on pilot and/or commercial scale studies. As part of their research, Forster et al. studied the microwave heating behaviors of 42 ore samples at bench-scale. The results were used to generate a database, from which a classification system was developed. This was used to rank the amenability of any given ore for microwave pretreatment.
“This knowledge can be employed to predict the performance of the ores in the high-power pilot scale tests and thus can be used as a pre-screening tool,” stated the authors.
They explained that many valuable minerals, such as sulphides and some metal oxides, heat well in response to microwave irradiation. Typical gangue minerals, especially those containing large quantities of silica (SiO2), are transparent to microwaves and do not heat. Selective heating causes differential thermal expansion, resulting in stress and strain across mineral grain boundaries, creating microfractures. It also generates distinctive heating patterns on the surfaces of the rocks.
Select ores from the test program were tested at the pilot-scale using a 150 kW microwave system to determine the effects of electromagnetic radiation on comminution, liberation of valuable minerals, and sorting potential. This involved treatment at high power for short amounts of time and resulted in reductions in the SAG WSDT values for three out of the four ores. The ore that did not achieve a reduction in grinding energy still demonstrated substantial improvements in the liberation of the copper sulphide mineral species.
“This reveals that while comminution test work may not immediately show energy savings, this loss can be reclaimed in downstream unit operations, providing sufficient liberation has been attained,” said the authors. “Monolayer ore sorting results for a blend of a nickel sulphide ore and gangue rock demonstrated that if a discrete heat signature is captured then the combination of microwave pretreatment with sorting has considerable potential.”
In their paper, Forster et al., noted that Anglo American is developing a microwave-assisted comminution project at its Amandelbult platinum mine in South Africa, as part of the FutureSmart Mining program.
“In some of their preliminary test work, they [Anglo American] reported hardness reductions of 5%-25% and 8%-12% for platinum and copper ores, respectively. The company is investigating installations at other facilities, starting with a pebble circuit at Los Bronces (Chile), followed by Mogalakwena (South Africa), Collahuasi (Northern Chile), and Quellaveco (Peru),” the authors said. “This effort speaks very highly of the potential for microwave-assisted comminution in the mining industry.”
Run of mine ore on its way to the mill.
Mont Wright Optimizes from Mine to Mill
Another excellent paper, ‘Mine-to-Mill optimization at Mont Wright’, by Hill et al., (2021)2 highlights the importance of holistic value chain optimization in achieving efficiency improvements in grinding. This details the recent Mine-to-Mill (M2M) integration and optimization project undertaken at the Mont Wright (MW) iron-ore complex in Canada. In 2019, ArcelorMittal Exploitation Miniere (AMEM) and Hatch conducted a study with the aim of increasing the mine’s production with little or no capital expenditure. In 2020 and 2021, the recommendations resulting from the M2M project were implemented by MW with assistance and refinement from Hatch.
“Throughout the M2M project, site-specific models of the mine and plant (blast fragmentation, crushing, grinding, gravity separation) were developed and calibrated based on historical data, and audits and surveys carried out by MW and Hatch personnel,” explained the authors. “The models were integrated and used to simulate and determine optimized strategies across the entire value chain from the mine through to the plant, to increase production while minimizing overall costs. Optimization strategies were trialed and refined during implementation, accounting for the limitations encountered in the mine and plant.”
The paper described how, during the project, ore domains were defined based on rock structure and strength, and blasting guidelines were developed for each to improve run-of-mine (RoM) fragmentation for production blasts across multiple pits and reduce feed variability. Crushing and grinding simulations were conducted to assess the impact of finer RoM fragmentation and to optimize operating strategies for the finer feed. Simulations indicated an expected throughput increase of 7%-26% for the different grinding lines depending on the ore domain.
One of the main recommendations in the plant was the conversion of Mill 7 from autogenous (AG) to SAG grinding to fully utilize the available power, capitalizing on the finer fragmentation from the mine and increasing throughput.
“Implementation of the new operating strategies began in late 2020, including additional ore characterization, refinement of domain definition, establishment of updated blasting guidelines to accommodate operational constraints, and conversion of Mill 7 to SAG (12% ball charge),” stated the authors. “A composite (rubber/steel) mill liner design was also investigated to allow a higher ball charge in Mill 7. Throughput improvements of up to 10% (overall, for all ore types) have been achieved to date and further benefits are expected when the refinements to blasting guidelines and all recommended M2M operating strategies are fully implemented.”
‘Replacement of wet ball milling with high-pressure grinding ahead of separation’ (2022) by Gagnon et al.,3 is another good read. Also undertaken as part of the Crush It! Challenge, for this study, Canadian R&D firm, COREM, partnered with the University of British Columbia to develop and demonstrate the use of high-pressure grinding rolls (HPGR) as a replacement for wet ball milling.
“Although HPGR has made inroads into the minerals industry, collectively the numerous challenges faced to replace fine, wet, closed-circuit ball milling have meant that it has not been seriously considered for this role,” said the authors, citing multiple unaddressed issues which required investigation before the economics of such a circuit could be determined.
Several Canadian mineral processing plant operators were approached as potential case studies, including the two ultimate project participants — Porcupine Gold Mine (PGM) and Copper Mountain Mine (CMM). Various OEMs also leant their expertise to the project, and the two plant comminution circuits were audited for performance evaluation and sample collection.
In the paper, the authors described the results: “Functional performance analysis of the high-pressure, open-circuit piston press testing provided the major discovery, and also quantified, that grinding efficiency on the coarse material (plus 150 and 250 microns, respectively) increased between 25% and 30% in the absence of the fines,” they said. “Apparently, breakage of coarse particles in the high-pressure, packed bed takes place far more effectively without the interference caused by the presence of fine particles between them.”
The discovery boded well for the project objective of maximizing energy savings and stressed the importance of good fines removal by the circuit classifier to achieve high machine grinding efficiency.
“This is, in addition to the desired classifier duty of not sending finished size material to the machine, which itself wastes its space and energy, and results in overgrinding,” added the authors. “It may be noted separately that CSE [classification system efficiency] increased from an average of 65%-80% (with fines removed) during the initial PGM piston tests, and from 72%-85% (with fines removed) during the initial CMM piston tests.”
In both cases, comminution equipment energy savings alone, and final stage total circuit energy savings, exceeded 60% and 50%, respectively and downstream mineral separation performance was the same or better; which, literally and figuratively, crushed the objectives of the challenge.
How to Better Size HPGRs
In his paper, ‘Helping to reduce mining industry carbon emissions: A step-by-step guide to sizing and selection of energy efficient high pressure grinding rolls circuits’ (2022),4 Stephen Morell of SMC Testing Pty Ltd. provided a new power-based methodology to assess and size HPGR closed circuits in hard-rock mining applications.
“HPGR circuits have the potential to reduce the mining industry’s CO2 emissions by up to 34.5 megatonnes/year, or 43.5% when compared to the established AG/SAG/ball mill circuit alternatives,” he stated. “However, uptake of HPGR technology has been relatively slow. This may be due in part to the fact that costly and time-consuming pilot testing is still the norm for assessing, selecting and sizing HPGR circuits. This is in contrast to AG/SAG/ball mill circuits where relatively cheap, fast and effective power-based methodologies are used.”
The research used recently published data from a number of operational full-scale circuits to prove its validity across HPGR-ball mill circuits, as well as the more energy efficient HPGR-HPGR alternative combination. Using a new equation that accounts for the influence of specific grinding force on HPGR energy efficiency, the ‘Morrell method’ was shown to predict closed circuit HPGR performance to within 6.5% on average, and ball mill circuit performance to within 3% on average.
“The results of this work suggest that power-based techniques, embodied in the Morrell method, are able to accurately predict HPGR/ball mill circuit performance and hence are a reliable approach for assessing, sizing and selecting suitable HPGRs and ball mills in greenfield design scenarios,” stated the author.
RELO tetrahedral grinding media. (Photo: Axora)
Grinding Media: New Shape, Better Results
The final paper that we’ll highlight (although there are many more excellent examples available at www.ceecthefuture.org) is ‘Rethinking Grinding Efficiency in Ball Mills’ (2021) by Chandramohan et al.5 This explained how, over the years, fundamental insights gained from ball mill operation have provided energy-efficient routes to increase throughput and reduce product grind size distributions through optimization strategies. These include controlling ball charge levels, media size distribution, liner designs, and changing operating parameters such as mill speeds, feed densities and classifier operations.
However, as the authors explained, one of the less explored strategies is understanding the effect of grinding media shape on grinding efficiency. Bulgarian startup, RELO, has developed a novel tetrahedral media that increases the charge’s packing density, resulting in higher grinding efficiency than spherical media in ball milling applications. Lab tests have shown a >10% reduction in the Bond Work Index for an equivalent ball mill operating with a spherical media charge.
“Detailed DEM [discrete element method] assessment comparing a conventional ball mill indicates that mill speed and shell liner design significantly impact the energy transfer for grinding, highlighting a potential combined benefit of using RELO media and optimized liner design for further improvements to the ball mill grinding efficiency,” stated the authors.
UK-based technology marketplace for heavy industries, Axora, is helping RELO to commercialize its solution. CEO, Dr Nick Mayhew, explained to E&MJ: “RELO grinding media can dramatically improve grinding efficiency without impacting the flowsheet or grinding equipment. The tetrahedron shape and application-specific construction materials (ceramic, high chrome etc.) increase the active surface area for the grinding process and create a hammering effect as well as crushing, making the process much more efficient.”
The increase in grinding efficiency essentially allows the SAG or ball mill to run at a lower speed, reducing energy consumption by up to 40% (and CO2 emissions), and a reduction in material recirculation means that throughout can be increased by 10%-40% for the same input parameters. The novel shape and lower mill speed also decreases the wear rate for both the mill lining and media which reduces the cost of consumables and downtime for maintenance.
“Mining companies are understandably wary of introducing new technologies that could interrupt their production, so we’re working with Wardell Armstrong and other independent labs to run trials for about 25 operations today, including three top 20 mining companies,” said Mayhew. “We are also supplying media samples so that operations can introduce to their plants to measure the impacts themselves.”
In time, the plan is to license the intellectual property to established grinding manufacturers to ensure high product quality and easy integration into mine supply chains.
1 , 2 , 3 , 4 and 5 : All papers referenced in this article are available at www.ceecthefuture.org.
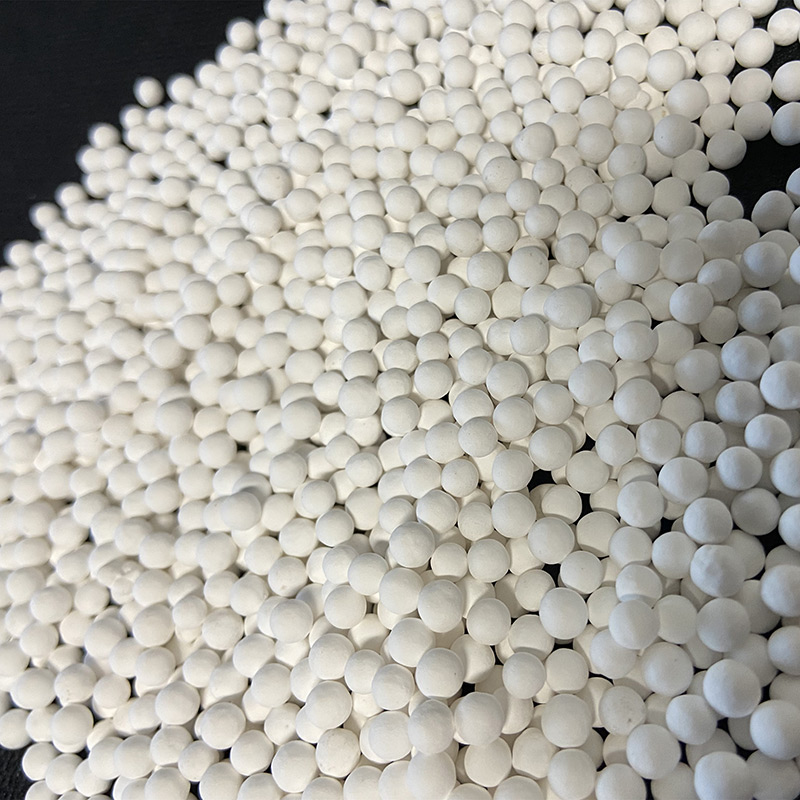
Catalyst Support We use cookies to enhance your browsing experience, serve personalized ads or content, and analyze our traffic. By clicking "Accept All", you consent to our use of cookies. Not consenting or withdrawing consent, may adversely affect certain features and functions.To provide the best experiences, we use technologies like cookies to store and/or access device information. Consenting to these technologies will allow us to process data such as browsing behavior or unique IDs on this site. Not consenting or withdrawing consent, may adversely affect certain features and functions.