Air filter media built with PTFE, the synthetic fluoropolymer of tetrafluoroethylene, has many advantages when it comes to air filtration in cleanrooms and PPE. Robrecht Hendrikx, Market Manager for venting and filtration at Japanese manufacturer Nitto, explains
Air filtration is a key element in controlling the number and the size of particles permitted per volume of air in a cleanroom. As we know, the class of the cleanroom is defined by the level of impurities taken out of the air by the filter medium, and there are several filter media available on the market for this purpose. Filter Membrane Eptfe

Glass fibre, polyester felt or PTFE, all of them can be used for HEPA or ULPA class cleanrooms. The main difference between these materials is the filtration process itself. The filtration with glass fibre or polyester felt media is done within the material. With PTFE filter media, the filtration occurs on the surface and that leads to several advantages; high efficiency with a low-pressure drop and higher energy efficiency and smaller filters.
Polytetrafluoroethylene (PTFE) is a synthetic fluoropolymer of tetrafluoroethylene. PTFE is hydrophobic which means it is water repellent. On top of that, the material has a very low friction coefficient. Most people know PTFE as the non-stick material used in cookware.
Ultra-thin PTFE film can be made air permeable by controlled stretching. This process creates millions of micropores per sq cm offering a high air permeability.
Normally, high air permeability is considered to be related to lower dust collection efficiency. However, the micropore diameter in PTFE stretched film ranges from 0.1 µm to 10 µm. This is wide enough for air to pass freely but offers excellent dust particle collection.
The filtration process with PTFE stretched film is different to other materials such as glass fibre or polyester felt. Glass fibre and polyester felt need to be of a certain thickness to be efficient as they “trap” the dust particles within a maze of tunnels. The filtration with PTFE stretched film is done at the surface because the micropores act as a gatekeeper.
Thanks to this behaviour, the filter material is almost not contaminated, which offers a considerably lower pressure drop (see fig 1). In fact, the dust particles could be removed by vibration.
Temish is a PTFE stretched material manufactured by Nitto. As a Japanese company that produces industrial tapes, polarisation films, insulation materials, and several other products, Nitto's technology offers this solution as filter bags for the dust collector of incineration facilities.
The collected dust particles are filtered at the surface, then shaken off by vibration to keep the bags near full capacity. Benefits of PTFE-based filtration materials for cleanroom HVACs
High efficiency combined with a low-pressure drop is a feature of PTFE filter media and here, 99.99999% of filtration efficiency with ULPA grade PTFE stretched film is possible.
The pressure drop will increase at this extreme level of filtration, but the PTFE material still outperforms other materials like glass fibre in filtration efficiency and the all-important, energy efficiency (see fig.3).
Energy efficiency is becoming an important issue, as Alan Sweeney stated in his article “Air filtration to the test” featured in the February issue of CT.
In the article, Sweeny provided comment on the energy implications of the new standard ISO 16890 regarding air filters for general ventilation. Sweeny said: “It is well known that air filters result in a contribution to the energy consumption of the HVAC system. As the filter system becomes loaded the pressure drop will increase, raising the load on the fan and thus demanding higher energy consumption.”
Jan Nelissen, the CEO of construction company ABN, reaffirmed in his Cleanroom Technology article “Five forces driving energy efficiency in next-gen cleanroom design” that HVAC systems are responsible for 50-70% of the total energy consumption of a cleanroom system.
“Cleanrooms consume large amounts of energy compared with non-classified rooms; scientific literature and experience in the field show that cleanrooms use up to 25.3 times more energy (1.25kW/sqm vs. 0.06kW/sqm). The energy requirement of HVAC systems usually amounts to 50-75% of electricity consumption in a clean production space due to the high airflow rates needed for particular ISO classes,” he said.
The class of the cleanroom is defined by the level of impurities taken out of the air by the filter medium, as stated above. However, there is another source of contamination that is often not considered: the filter material itself.
Due to low mechanical resistance or outgassing of chemical components, the filtered air could be contaminated by fibres or gases coming from the filter material itself.
The ultrathin PTFE stretched film material is usually reinforced by a non-woven fabric offering excellent mechanical resistance (see fig. 4).
In combination with the material’s natural resistance to acids (such as hydrofluoric acid), alkalis and organic solvents, PTFE drastically reduces the risk of contamination of the cleanroom environment by the filter material itself (see fig. 5).
PTFE material shows excellent results when it comes to the outgassing of chemical components (see Table 1).
Tests performed by Nitto have shown that there is no trace of bibutyl phthalates, nor methyl ethyl ketone oxime or fluoro alkyl alcohol.
The total amount of outgassing is 461 ppm, which is only 6% of the 7,860 ppm measured with glass fibre material.
The high efficiency of PTFE-based filters has opened the door to other markets such as consumer electronics and personal protection equipment. Vacuum cleaners have become more powerful over the past decade.
Powerful used to be a synonym for higher energy consumption and larger devices. But lately, we have seen a growing demand for energy efficient and smaller devices as a result of the increased environmental consciousness of end-customers. This confronted the manufacturers of vacuum cleaners with a contradiction: how to design smaller and energy friendly devices that are powerful enough to answer the expectations of their customers?
PTFE-based filters offered a solution. The lower pressure drop of the material allowed the manufacturers to design more efficient yet smaller devices. The energy efficiency of the latest vacuum cleaners has even led to a new trend: battery driven vacuum cleaners.
Like this story? Subscribe to Cleanroom Technology magazine for incisive analysis of the latest news and developments in hi-tech industries manufacturing in controlled environments.
Next to energy efficient and smaller vacuum cleaners, the end-customer gets another benefit with PTFE-based filters. Because the filtration is done at the surface, the dust collected during the vacuum cleaning process can be easily removed by vibration or even rinsing it off. Using water will not damage the PTFE-based filter as the material is hydrophobic.
Face masks are an important part of the personal protection equipment (PPE) in many industries. Depending on the type of filtration needed, these face masks can become quite big. The link between the size of the face mask and the type of filtration needed is the pressure drop. The higher the pressure drop of the filter material, the bigger the face mask.
The main advantages are the high efficiency with low-pressure drop and the low risk of contamination by the filter material
The human factor is the reason for that. You can increase the power of an HVAC system to partly overcome the pressure drop, but you can’t use the same principle for a human being.
PTFE filter materials solved the dilemma between easy-breathing comfort but bigger filters or less comfort but smaller filters. The low-pressure drop of PTFE filter materials like Nitto’s Temish have helped the face mask industry to make smaller, yet highly efficient face masks that offer the user the comfort of easy breathing.
Alongside the low-pressure drop, the mechanical resistance and low outgassing of the PTFE filter materials are an important asset in creating safe and efficient face masks.
PTFE is a filtration material that offers interesting features for cleanroom filtration compared to a glass fibre or polyester felt.
The main advantages are the high efficiency with low-pressure drop and the low risk of contamination by the filter material. These benefits are the result of the material characteristics of PTFE and its typical surface filtration process by micropores. Such a higher throughput of air with a lower pressure drop is achieved even at ULPA-grade filtration.
The use of PTFE filtration materials in cleanrooms have opened the door to other industries and other applications like powerful battery-driven vacuum cleaners or smaller but highly efficient face masks.
The newest trend is the shift from clean air demand in cleanrooms to our homes. The indoor air quality is strongly influenced by the geographical location of the building and the performance of the ventilation system.
There is, however, a third option: air purifiers. The recent development of efficient yet energy friendly air purifiers for personal use increases the indoor air quality and improves the comfort of the residents. These air purifiers use the same filtration techniques as cleanrooms, based on Nitto’s Temish filtration materials.
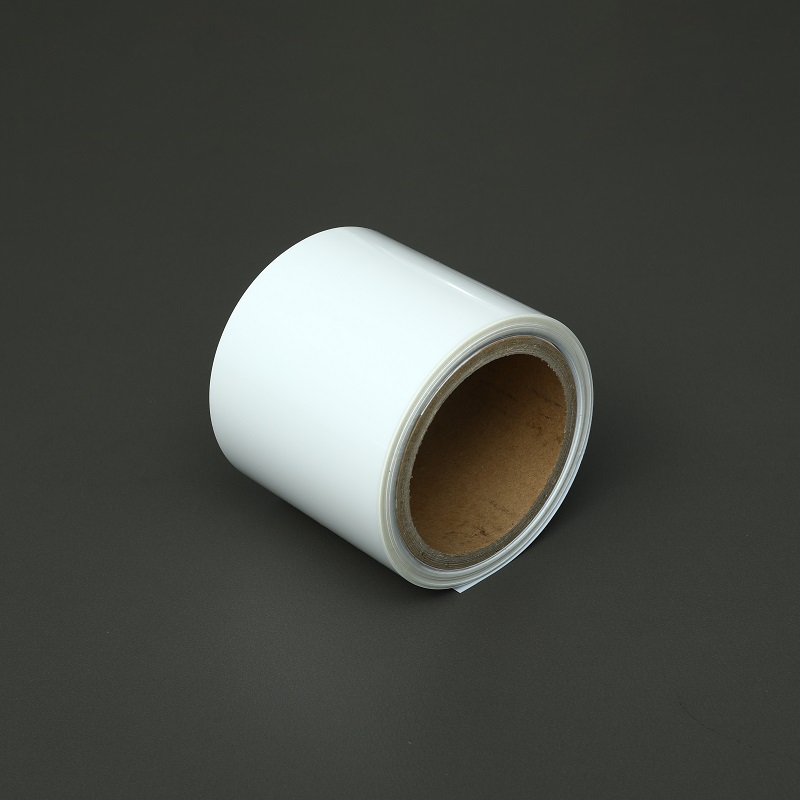
Valve Membran N.B. This article is featured in the April 2019 issue of Cleanroom Technology.