ATMOsphere, publisher of R744.com, has launched the voting process for the ATMO 2023 Innovation of the Year Award for North America, which is given to the company that has produced a natural refrigerant-based product that has had, or is expected to have, a significant impact on the market.
The short list of candidates for the award consists of products from Energy Recovery, OLAB and Danfoss. Butterfly Valve With Pneumatic Device
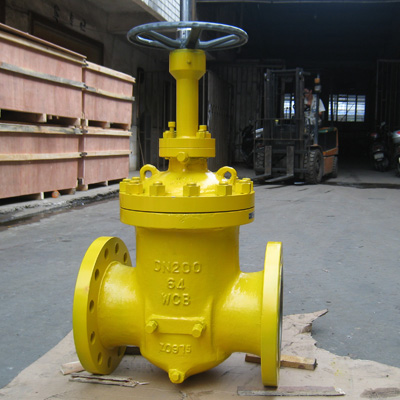
Energy Recovery’s product is the PX G1300 pressure exchanger, designed to improve the efficiency of transcritical CO2 (R744) refrigeration systems.
OLAB’s product is the Series Revolution stainless-steel flanged ball valve, designed to eliminate leaks in transcritical CO2 systems.
Danfoss’s product is the Heat Recovery Unit (HRU), designed to eliminate the technical challenges of managing heat recovery from a CO2 refrigeration rack.
Vote for one of these products – described in detail below – here.
Voting will take place online the week of June 5–11 and in-person on June 12 in Washington, D.C., at the ATMOsphere (ATMO) America Summit 2023 on natural refrigerant-based HVAC&R. The winner will be announced at the conference during the ATMO Awards/North America ceremony beginning at 5 pm EDT on June 12. Other ATMO awards will include Best in Sector/Retail, Best in Sector/Industrial and Person of the Year.
This 12th annual edition of the ATMO America conference will be held Monday, June 12, and Tuesday, June 13, 2023, at the Mayflower Hotel in Washington, D.C. The event, addressing applications of the natural refrigerants CO2, hydrocarbons and ammonia, is organized by ATMOsphere.
You can register for the event here and find the program and other information on the event website. End users can register for free, and contractors/installers of HVAC&R systems are eligible to receive one free ticket per organization, with a 50% discount on additional tickets.
ThePX G1300 device is able to improve the efficiency of a transcritical CO2 system. It does this by harnessing the high-pressure CO2 fluid (liquid, gas or supercritical) coming from the gas cooler to increase the pressure of low-pressure suction gas coming from the evaporator and flash gas coming from the receiver. It then returns the now higher-pressure gas to the gas cooler instead of to the compressors, reducing the work required of the compressors. This reduces energy costs and lengthens the life of the compressors, reducing Capex costs, the company says.
At the same time, the high-pressure fluid from the gas cooler exits the PX device as a low-pressure CO2 liquid/gas mixture, moving onto the receiver where the flash gas recirculates to the PX while the liquid is piped to the cooling load (evaporators).
The PX device can accommodate capacities of 205–409MBH/17.1–42.7TR (60–150kW) and pressures up to 2,030psi (140bar). It is feasible to go much larger in capacity by banking PX devices together, the company said.
The PX G1300 device reduces the work done by compressors in a way similar to that of a parallel compressor. The PX G1300 also competes with other components designed to improve the efficiency of transcritical CO2 systems, such as ejectors and adiabatic gas coolers.
When operating in ambient temperatures above 40°C (104°F), an Italian supermarket using the PX G1300 pressure exchanger realized more than 30% efficiency improvements in its Epta CO2 refrigeration system compared to a standard CO2 booster system.
“By integrating the PX G1300 into the CO2 refrigeration system, high-temperature rack stability was also achieved,” the company said, adding that the device allowed the store’s refrigeration system to handle summer heat waves with “smooth” operation beyond its original design.
Given the efficiency gains, the PX device is priced to deliver a two-to-three-year payback for the end user, the company said.
Headquartered in San Leandro, California, Energy Recovery started its business with pressure exchangers for desalination operations, which today save approximately US$3.9 billion (€3.5 billion) annually in energy costs, the company says on its website.
OLAB, an Italian refrigeration component manufacturer, has developed what it calls a “revolutionary” stainless-steel flanged ball valve for high-pressure CO2 systems that addresses the leakage issues commonly associated with traditional ball valves.
OLAB’s new patent-pending Series Revolution ball valve has been designed to eliminate leaks in transcritical CO2 systems for commercial and industrial installations.
The Series Revolution ball valve is rated for 150bar (2,176psi), with a safety factor of three (450bar/6,527psi). It accommodates piping from 10 to 60.3mm (0.4 to 2.4in) in diameter with flow rates of 4 to 175m3 (141 to 6,180ft3)/h, at temperatures ranging from -50 to 150°C (-58 to 302°F).
The ball valve is designed to avoid the need for TIG welding in the ball-valve body. Welding of tubes onto the flange (made of stainless steel or brass) on both sides of the valve is initially done at two points with the flange connected to the valve to ensure a proper fit. Then the flanges are disconnected, and the welding is completed; each welded flange is then attached to the ball valve with Class A2 stainless-steel screws in a very simple operation. Two O-rings are used between the valve and the flanges to ensure the seal.
Leaks in brass ball valves for refrigeration systems are attributable to welding on the ball-valve body, and even in traditional stainless-steel versions there is a risk of damaging the seals by welding the pipes directly to the valve, the company said. The Series Revolution ball-valve body is weld-free and solves the problems associated with traditional ball valves with welded or threaded ODS (oxide-dispersion-strengthened alloy) connections, says OLAB in its product brochure.
In addition, this design allows for the “interchangeability of the flanges to change the type of device connections without having to change the entire valve,” says the product brochure. It also enables the valve body to be easily replaced without having to cut the connecting pipes.
Moreover, the valve body can be updated and reused rather than discarded; this is an ecologically friendly practice that also saves the end user money.
The Danfoss Heat Recovery Unit (HRU) helps to eliminate the technical challenges of managing heat recovery from the CO2 refrigeration rack in supermarkets. It is an integrated solution managing and buffering the heat from the CO2 refrigeration system – to be reused for space heating, hot tap water or even sold to neighbors or district heating grids.
System efficiency ensures short return of investment time – one to three years depending on the current heating source.
In addition, the HRU is designed as floor station and it is delivered in one piece with the option to be split into three parts, which allows the HRU to be transported through narrow corridors.
All heat exchangers are produced with micro-plate technology develop by Danfoss, which significantly increase substation performance and lifetime, the company said. Standard unit layout allows the end user to prepare connection piping inside the building before the station is delivered.
A Danish supermarket uses the HRU to recycle the waste heat from its refrigeration system, reducing its annual heating bill by 89.7% and its CO₂ footprint by 6.7 metric tons a year. The HRU now recycles the waste heat to heat the store’s 1,900m2 (20,41ft2) and provide hot tap water year-round.
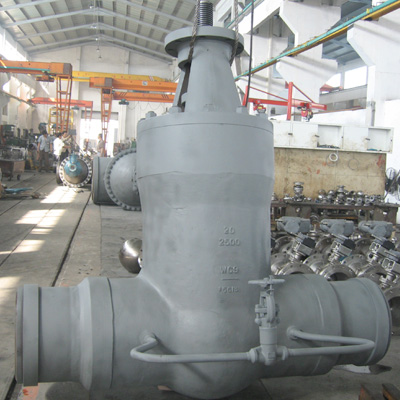
Swivel Plug Globe Valve Username or email address *