Designed by Alberto Mattiello and Davide Anzalone of Davide Anzalone Industrial Design and manufactured by Metalco, the Urban Mirror is composed of monolithic elements made of HPC (High-Performance Concrete) and a steel sheet structure that serves as a frame for a stainless steel panel with a mirror finish.
The Urban Mirror has recently been awarded a 2022 Good Design Award by The Chicago Athenaeum: Museum of Architecture and Design and The European Centre for Architecture Art Design and Urban Studies. Stainless Steel Pipe
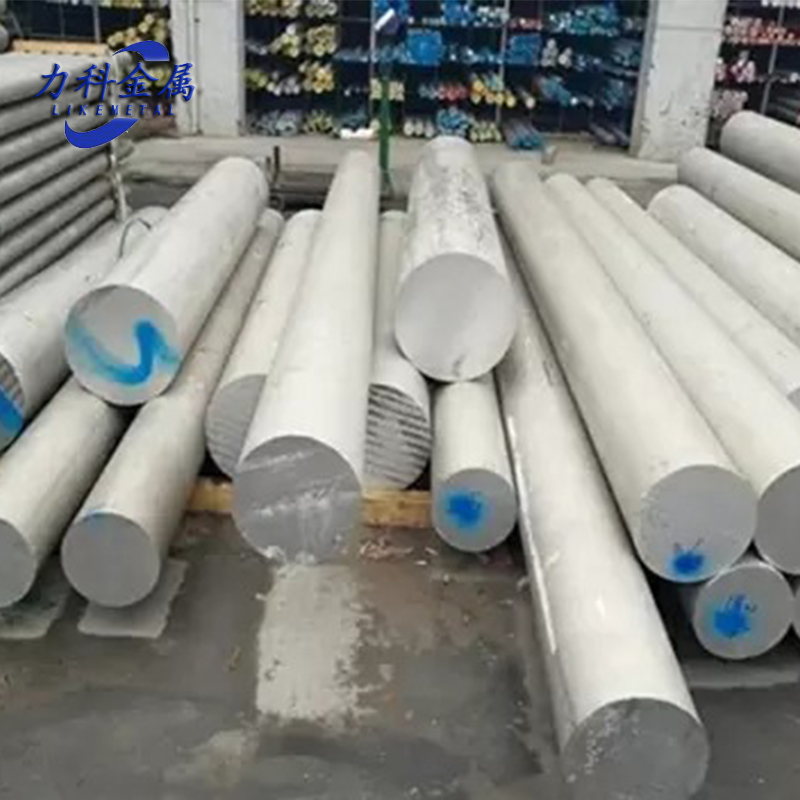
It embodies the ability of reflective surfaces to create innovative social languages and makes the mirror – which has always been a fundamental indoor design object – a “key” element for outdoor environments.
Urban Mirror is designed not only to amplify the architectural or natural beauty of the surrounding places but also to bring new energy and promote interaction and freedom of expression, transforming traditional places into meeting points and making the urban space a “stage” for street artists, local events and sports workouts.
Project: Urban Mirror Designers: Davide Anzalone Industrial Design Lead Designers: Alberto Mattiello and Davide Anzalone Manufacturer: Metalco Srl.
Input your search keywords and press Enter.
Reserve your place at Prize Designs for Modern Furniture and Lighting. 2023 Submissions are open
Welcome to Global Design News. Subscribe to our newsletter list to receive news and updates from Architecture and Design.
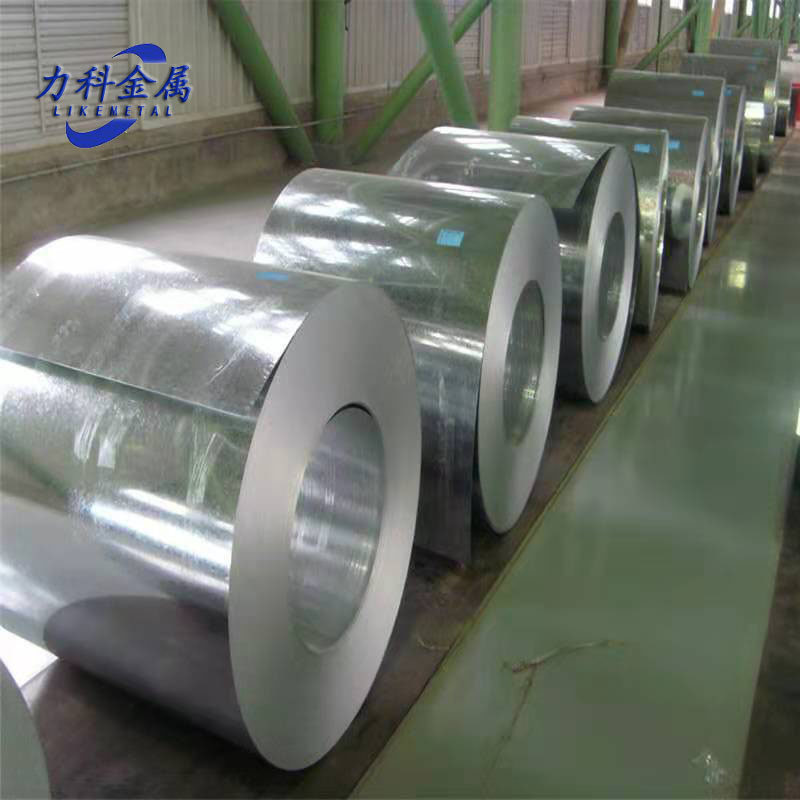
Polished Pipe You can see how this popup was set up in our step-by-step guide: https://wppopupmaker.com/guides/auto-opening-announcement-popups/