The options for cargo offloading crude oil from a floating storage and offloading vessel include the stem-in-tandem (bow-in-tandem), the remote offtake buoy, and the alongside configuration.
Each option should be comparatively evaluated against the relevant agenda, important from viewpoints of facility operation and maintenance. No single option fits all criteria for offloading. Silicone Elbow

The information presented here is from a study of a converted ultra-large crude carrier (ULCC) built in the 1970's or 1980's. During this era, ULCC were built usually with midship loading/offloading manifolds.
Crude oil is produced and processed from inland or subsea wellheads. The product crude oil is loaded onto the FSO vessel via a subsea pipeline, pipeline-end-manifold (PLEM) assembly, and underwater hoses which are pertinent parts of the crude oil exporting facility.
Cargo from the vessel is pumped through offloading hose-strings to a shuttle tanker berthed to the vessel in an arrangement of alongside, in-tandem, or remote buoy configuration.
There are several options for the vessel's cargo offloading configuration in relating to the mooring system. The agenda covers the following critical points:
The purpose of this study was to define the initial planning philosophy and to support the later engineering, operational, and maintenance efforts. The study did not work out detailed design, define detailed procedures for operation and maintenance, or determine the specific equipment needed.
The converted vessel can be moored through the bow or stem by an single point mooring (SPM) or spread mooring system. The main mooring structure can be a jacket, turret, or buoy for the SPM system. The SPM system allows the vessel to weathervane and thus minimize the mooring loads at all times, in contrast to the fixed vessel with the spread mooring system. The common mooring system associated in this study for an FSO vessel is:
For the SPM system, the vessel can be moored through either the bow or stern. There are several other applicable SPM systems, but they are out of the scope of this study. The spread mooring system, as described, is affiliated with a remote offtake buoy.
The cargo is offloaded from the FSO vessel to a berthed shuttle tanker through the export manifold and hose-strings. The configurations studied are limited to the stem-in-tandem (bow-in-tandem), remote offtake buoy, and alongside offloadings. The vessel's operations with an in-tandem offloading can sustain higher environmental limits than those with an alongside offloading.
The length of a hose-string is dictated by the offloading configuration. The FSO vessel can be 300,000+ deadweight tons (KDWT). Typical length of the 300 KDWT vessel is 1,115 ft overall. The 250 KDWT shuttle tanker is 1,141 ft overall.
The length of a hawser is assumed to be 200 ft. The export manifold location is selected to accommodate the offloading configuration and can be situated at various locations, such as:
Other agenda requirements associated with the FSO vessel's offloading configuration are as follows:
The accompanying table summarizes the comparative study of the following cargo offloading configurations discussed. Other relevant information from the study is included. Qualitative expressions such as major, moderate, and minor are used to designate results of the order-of-magnitude comparison. Each offloading configuration is assessed against the agenda as follows:
In this offloading configuration, the shuttle tanker is berthed by a hawser(s) and loaded through offloading strings from the FSO vessel's stern. Each offloading hose-string is about 1,000 ft long (for this study). The stern-to-bow distance between the FSO vessel and a shuttle tanker is about 200 ft, which is the length of hawser(s).
The hose-strings can be flushed even though they are lengthy. The flushing operation can be accomplished either through the crossover connection installed at the ends of hose-strings or through the existing (or spared) midship manifold on the vessel. The hose change-out will require a major offshore spread due to the very long hose-strings.
There is normally less chance for collision as well as fire spread between the vessel and tanker since they are some distance apart from each other. Minor oil spills or fire from the shuttle tanker will not interfere with or endanger the FSO vessel's operations since the tanker is always downstream of the prevailing current and wind. The spill can possibly be contained from the vessel. A tug may be required for maintaining the hawser's tension to avoid collision between the tanker and vessel, especially in adverse weather.
Future offloading expansion can be a second FSO vessel or a remote offtake buoy Within the limits of the mooring chain capacity and local weather, the vessel may offload alongside simultaneously.
There are minor efforts involved in removal of the offloading equipment since it is a part of the vessel. This configuration constitutes no problem for decommission, abandonment, and relocation.
A remote offtake buoy is affiliated with the spread mooring system for this study. The shuttle tanker is berthed by a hawser(s) to a remote offtake buoy and loaded through offloading strings at the buoy. Each offloading hose length is about 840 ft long (for this study). The buoy is located about one mile from the FSO vessel. The closest distance between the vessel and tanker is about 3,800 ft under any possible circumstance.
With this offloading configuration, the hose-strings cannot be flushed or changed out without extra equipment and assistance from an offshore spread. The long hose-strings aggravate the operational and maintenance problems.
Normally, there is minimal risk for collision as well as fire spread between the vessel and tanker since they are far apart. Minor oil spills or fire from the shuttle tanker may interfere with or endanger the vessel's operations and will depend on the direction of the prevailing wind and current. The spill cannot be contained easily from the vessel since it is far away. A tug may be required for maintaining the hawser's tension to avoid collision between the tanker and buoy, especially in adverse weather.
Several offtake buoys can be installed in the satellite pattern around the vessel for future offloading expansion. The number of buoys are limited by the FSO vessel storage and cargo pump capacities.
The offtake buoy requires major efforts for removal from the site. The under-buoy hoses and mooring chains need to be dismantled as well. Thus, this configuration can become a problem for decommission, abandonment, and relocation.
The shuttle tanker is berthed and loaded through offloading strings along the FSO vessel's side. Each offloading hose-strings is about 60 ft long (for this study). The side-to-side distance between the vessel and a shuttle tanker is about 10 ft which is the diameter of fenders.
With this offloading configuration, the hose-strings can be flushed easily and without an offshore spread. The flushing operation can be done between offloading flanges within the export manifold on the vessel. The change-out of the short hose-strings will require the least effort and no offshore spread.
There is normally a greater chance for collision as well as fire spread between the vessel and tanker since they are close-by. Minor oil spills or fire from the shuttle tanker can interfere with or endanger the vessel's operations. The oil spills can be contained since the vessel and tanker are in close proximity. No tug is required for maintaining the berthing line tension.
The future offloading expansion can be a second FSO vessel or a remote offtake buoy. Within the limits of the mooring chain capacity and local weather, the vessel may offload along both sides simultaneously.
There is no extra effort for removal of the offloading equipment since it is a part of the vessel. This configuration constitutes no problem for decommission and abandonment.
Each configuration is unique and has as many merits as disadvantages. For example, a stem (or bow) -in-tandem offloading configuration is a good selection for the vessel since it is relatively free from risks of fire spread and collision. However, the hose change-out and flushing operations require an offshore spread support
There is no definitive choice where one option is superior to others based on the agenda.
However, each option has been successfully applied to FSO vessels world wide. The selection of the offloading configuration for an FSO vessel is unique. The selection among options mainly depends on: the product crude oil's properties, local environmental conditions, original vessel arrangements, and construction costs.
The vessel's offloading and mooring are located opposite to each other and at ends of the vessel. After examining several FSO vessel applications, it can be loosely generalized:
Acknowledgment: The author wishes to thank Gulf Interstate Engineering Company for their generous support of this paper and Judy P. Chen for her proofreading the draft.
Texas Section of The Society of Naval Architects And Marine Engineers, FPSO Technology, Feb., 1993.
Chen, Bill C M., "Selection Of The Mooring System For An FSO Vessel," Pipelines, Terminals & Storage, Energy Week Conference & Exhibition, Jan., 1996.
Clarkson Research Studies, The tanker Register, 1992.
Chen, Bill C. M., "Cargo Oil Heating Requirements For An FSO Vessel Conversion," MTS/SNAME, Jan., 1996.
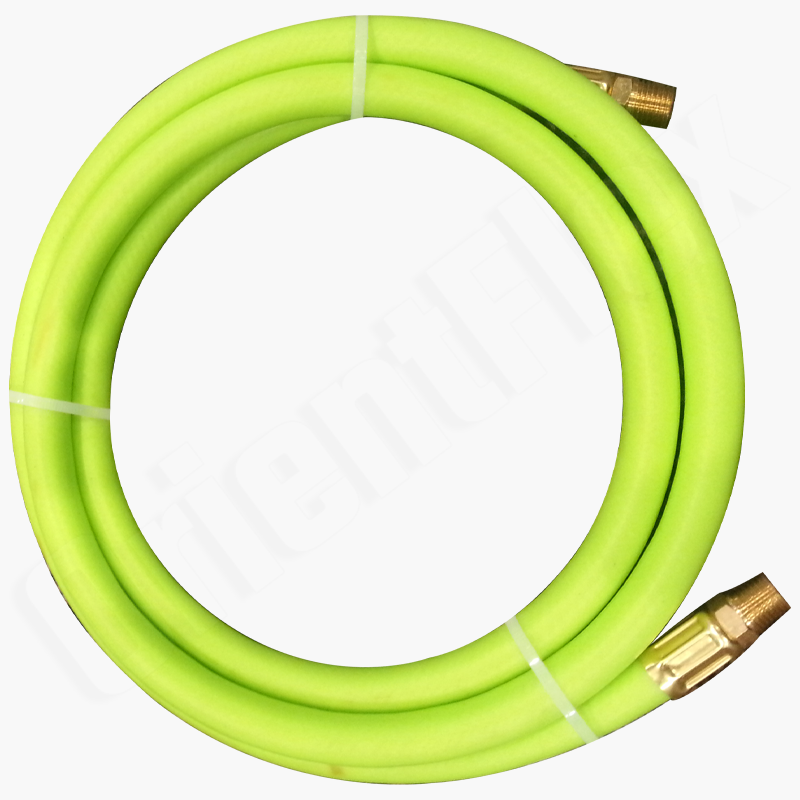
Fuel Truck Hose Copyright 1996 Offshore. All Rights Reserved.