Strongwell is the largest producer of FRP or fiberglass products in the world and utilizes a pultrusion manufacturing process to fabricate its products. In addition to their other product lines, Strongwell produces a wide range of FRP guardrail/handrail products.
Metallic products utilized as handrails are generally affected by corrosion. In the case of steel, this metal has to be constantly maintained due to scaling, rust, and similar issues. Conversely, a virtually maintenance-free product is fiberglass handrail (Figure 1). Frp Grating
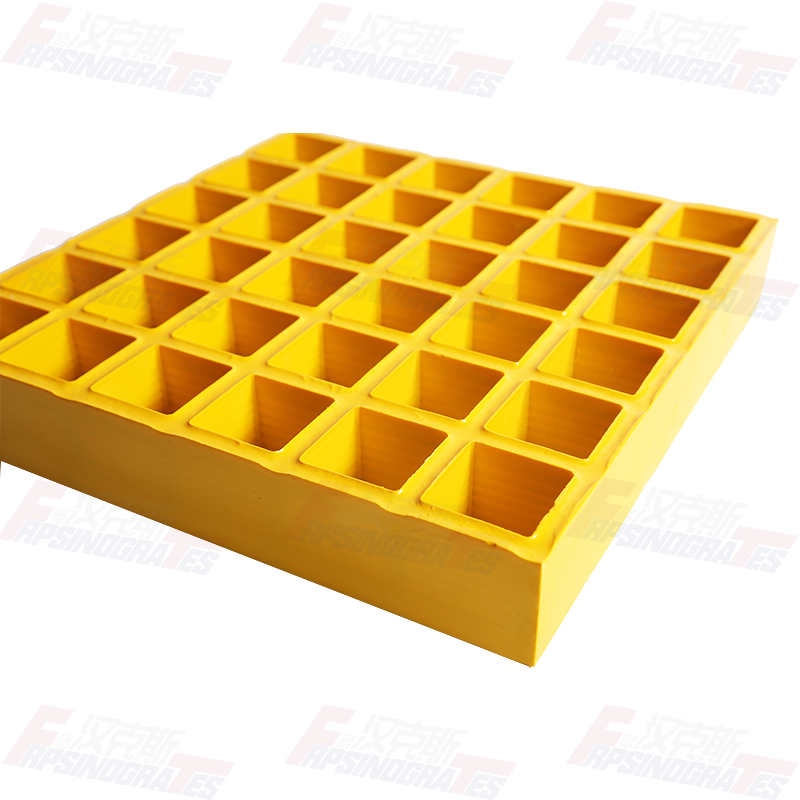
Based on the installation location, weight is another typical problem. Fiberglass can weigh just one-fourth of steel railings with similar performance properties. Unique instruments are required for fabrication of metal handrails. Basic carpenter’s tools are usually adequate in the case of fiberglass.
Figure 1. Fiberglass handrail is a virtually maintenance-free product
A range of SAFRAIL™ fiberglass handrails is available based on the type of site conditions (Figure 2). It can be as basic as pre-fabricating depending on the particular drawings of customers, or may require customers to do a large part of the fabrication process in the field.
The “alternate handrail” design from Strongwell can be considered in the latter case. It employs a 2-3/8-inch post and can be bought either with or without baseplates to provide suitable mounting options according to a customer’s specific installation location. The 2-3/8-inch post in the alternate handrail design is routed out to accommodate a mid-rail and a top rail.
In the manufacturing facility, these are pre-routed and fabricated but knocked down to facilitate easy delivery. The mid-rail and top rail are 2-inch square tubes that are deployed as lineal sections, cut to size, embedded inside the routed posts, and fixed in place.
This process resolves the need for epoxy and other supplementary attachments in majority of cases, making it easier to place these together in the field whenever there is a requirement for it. The posts can be simply set up wherever they will accommodate within the loading needs, reverting back to thread the mid or top-rails, and then filially fixing the kick plate. Only basic tools are required, regardless of the installation technique: a rivet gun, a drill, and may be a circular saw with a customized blade. A bonding agent is only utilized only there is a need to field-fabricate a return towards the end of a section and to utilize 90-degree fittings.
Figure 2. There are so many different types of SAFRAIL™ fiberglass handrail, depending on what the site conditions are.
Most of the handrails supplied by Strongwell are pre-fabricated to meet specific application needs (Figure 3). Normally Strongwell takes the customers’ contract drawings, performs a layout, submits the same for field corroboration, and then finally fabricates them in sections for delivery.
With regard to the field usage, the sections have to be simply fixed in place, whether it be base mounting sections to concrete, side mounting sections to an existing structure, or pocket mounting sections within sleeves of some sort. Customers can buy sections that would be fixed either as separate finished sections or to one another. In certain instances, customers would not wish to attach the sections to one another, like during replacement in the event of damage, or certain installs for maintenance or similar aspects.
Strongwell delivers the largest section that measures 20' long. For customers who wish to field splice the sections together to make an incessant run, Strongwell can designate those with a splice section. On the whole, everything is based on the customers’ requirements and the codes in their particular area.
Figure 3. The majority of Strongwell handrail comes pre-fabricated to fit your specific application
Fabrication of fiberglass rail can be relatively easier and requires less specialized labor, which would eventually translate into a reduced cost. Customers who have utilized fiberglass rails have confirmed that they involve minimum specialty labor. With regard to steel, inspectors, grinders, welders, painters etc. have to be considered to perform the same process.
In the case of a fiberglass rail, a person with a standardized skill set is sufficient - someone with an ability to read and follow drawings to drill or cut and along with the fundamental construction know-how can install fiberglass railings.
To illustrate this point consider a straight run of 100 linear feet of handrail with posts 5' on center. The expenditure involved for such a project in fiberglass would be four times higher than the cheapest steel option when only the initial cost of materials is considered. However, if the reduced cost of shipping is taken into account, faster and easier installation, and the maintenance cost savings, then fiberglass would turn out to be a cheaper option, compared to stainless steel and usually not much more than that of galvanized steel handrail.
If frustrations related to ongoing maintenance needs are also considered then FRP railing can serve as a suitable option, even when it comes to basic installations. The cost factor is even closer when there are customized environments where design and fabrication can be done more easily and with a lower cost with FRP than when metals are used.
UV is another thing that is a factor. For instance, if a yellow fiberglass rail is purchased it will be yellow all of the way through and not coated. However things exposed to sunlight will gradually fade in color, including fiberglass railings. However, unlike metals, FRP durability is not negatively impacted when the rail fades. This is because during the manufacturing process, a polyester surfacing veil is used to cover the glass fibers so that they are suitably protected from UV degradation. All metal handrails are painted adequately. As anticipated, a painted surface will always possess a longer and brighter-looking surface when compared to a non-painted one. However, in the case of metal railing, painting has to be done to delay the degradation and corrosion of the rail. The coating applied in fiberglass rails only improves the duration of time the rail looks bright and colorful.
If metal handrails are meeting the specified requirements, the use of fiberglass could be debated. Here, thinking about the long-term would show the value of fiberglass.
Fiberglass can last relatively longer than that of metals in many environments, particularly in places where the rails have to be continuously maintained. There are handrails that have been neglected for a long time and there are also railings where they no longer appear to be safe to use.
All metals, including high-end alloys, will rust in one way or other and degrade over time. This means that rails would need to be inspected, cleaned, and repainted on some kind of schedule. Compared to metals, the life span of fiberglass is much longer in adverse environments. In the case of steel, it would need to be replaced fully once in three to five years, and at times every year.
SAFRAIL™ product lines supplies by Strongwell have been utilized in analogous environments and these have lasted for more than 25 years without any maintenance (Figure 4). In fact, they were untouched from a maintenance standpoint.
Figure 4. Strongwell’s SAFRAIL™ product lines have been used in similar environments that have weathered 25+ years with no maintenance required.
Certain metallic alloys provide an alternative to conventional aluminum and steel handrails. Here, the comparison of fiberglass against higher-end metallic options in terms of durability, cost, and overall performance provides another new perspective.
While there are many types of alloys that perform relatively better than that of traditional aluminum or steel, they are still metals, meaning a higher price will be paid out only to delay rust and the other issues experienced by metals. Also, metallic railings would still need to be coated or painted, and material degradation and corrosion would still be encountered with further possibilities of galvanic corrosion problems.
In addition, customers will have more detailed fabrication/installation tasks, higher weight issues, heat conductivity, and electrical issues etc.
There is a place for using both FRP railing and metal handrail. While FRP is not a perfect solution, even high-end alloys will merely prolong the issues experienced by the more basic metals. The following sections discuss more aspects about weight with certain examples where weight would matter a lot. Some comparison is also made between steel and FRP handrail.
Generally, FRP railing weighs just 25% of steel railing with similar performance weighs. When an extra walkway or other type of structure is being added or an existing structure is being refurbished, the existing structure cannot be reinforced to manage more weight or the inclusion of a structural support can prove to be too costly.
There would also be times when a railing section has to be removed for one reason or another, like equipment moves or scheduled maintenance. However, when it comes to FRP, less equipment and manpower would be required when shifting as it is relatively lighter.
In specific industries like offshore oil and gas, the money saved on a floating oil platform is integral to the performance efficiency of that particular rig. Shipping costs related to fiberglass are often much less, regardless of the type of industry. In other words, weight is a bigger factor when considering handrail.
Another point of perspective is that if fiberglass weighs just one-fourth as much as steel and can be designed from traditional carpenter’s tools, then it would be considerably weaker than metal railing. This concept is not true because fiberglass is stronger much before a failure occurs. For instance, in steel, when a sufficient amount of load is applied to promote failure and bend the rail, then that bend will remain there eternally. The standard practice would to be either to re-form steel railing or substitute it, which is a frustrating and an expensive proposition.
Conversely, fiberglass railing has “memory”, which means it has some give to it. While the fiberglass rail will deflect like steel, it can take a relatively heavier load before actual failure occurs. Instead, the rail will be deflected by the heavier load but as soon as the load is taken off the rail will revert back to its original position and will not remain bent. Separate testing data to substantiate these claims is provided on all the numerous configurations of Strongwell’s SAFRAIL™, with summary data of this nature available on the company’s website. Strongwell also has a wide range of in-house testing capabilities if SAFRAIL™ has to meet certain test requirements that have not been tested.
There is no major difference when specifying fiberglass handrail against metal railing in terms of drawings and comparable submittals for a quote. It would be the same type of contract drawings which customers would be submitting and Strongwell will then work with the available drawings. In case the drawings have been earlier detailed as steel, then Strongwell will change them to fiberglass. The company typically works from parameters when it comes to construction drawings. Customers can specify the areas they are working on and where exactly they want the handrail to be installed, and Strongwell can then detail it out in the most optimum way to meet the customers’ requirements.
Metals can have different shapes of rails, different rail spacing between center and top rails, 3-rail, and 2-rail configurations etc. Fiberglass rails are available in different types of configurations. For instance, Strongwell has basic “standards” detailed and defined in its literature and brochures, however for specific needs of the customer Strongwell can tailor the design to suit their rail spacing, post spacing, rail shape, etc. The company pre-fabricates most of its rails and has directions on the highest post spacings in its field fabrication guides, which are available on its website. A standard request is to make sure that the railing meets OSHA standards, meaning it should endure a 200 lbs load in various without failure. Strongwell is used to these requirements and works with customers to ensure that they are fulfilled. The company can customize almost anything to meet its customers‘ requirements.
If customers are considering using fiberglass handrails, they can visit the Strongwell website and view the resources available there. The company’s SAFRAIL™ brochure contains good foundational data for customers who wish to know the options provided by Strongwell and also the fundamental configurations proposed by the company. Fabrication worksheets are also available on the website that can initiate the discussion between the customers and Strongwell if they have a certain project on hand.
Alternatively, customers can get in touch with Strongwell‘s regional sales managers or call its facility to speak to a product expert who can answer their questions. Strongwell takes steps to educate customers who are interested in deploying fiberglass railings. The company’s website has a detailed Corrosion Resistance Guide for those wishing to know the performance of the materials against different corrosive agents.
Qualified fabricators of products are one major aspect that Strongwell always looks out for. Fabricators who wish to learn about the Strongwell’s products can contact the company to discuss how they can add the company’s fiberglass products to their line of offerings for customers. While it is not a difficult fabrication procedure, it is always good to learn the most effective means for working with fiberglass structural products.
This information has been sourced, reviewed and adapted from materials provided by Strongwell Corporation.
For more information on this source, please visit Strongwell Corporation.
Please use one of the following formats to cite this article in your essay, paper or report:
Strongwell Corporation. (2023, May 18). The Importance of Selecting the Correct Handrail to Minimize Costs. AZoM. Retrieved on February 13, 2024 from https://www.azom.com/article.aspx?ArticleID=12843.
Strongwell Corporation. "The Importance of Selecting the Correct Handrail to Minimize Costs". AZoM. 13 February 2024. <https://www.azom.com/article.aspx?ArticleID=12843>.
Strongwell Corporation. "The Importance of Selecting the Correct Handrail to Minimize Costs". AZoM. https://www.azom.com/article.aspx?ArticleID=12843. (accessed February 13, 2024).
Strongwell Corporation. 2023. The Importance of Selecting the Correct Handrail to Minimize Costs. AZoM, viewed 13 February 2024, https://www.azom.com/article.aspx?ArticleID=12843.
Do you have a question you'd like to ask regarding this article?
AZoM.com - An AZoNetwork Site
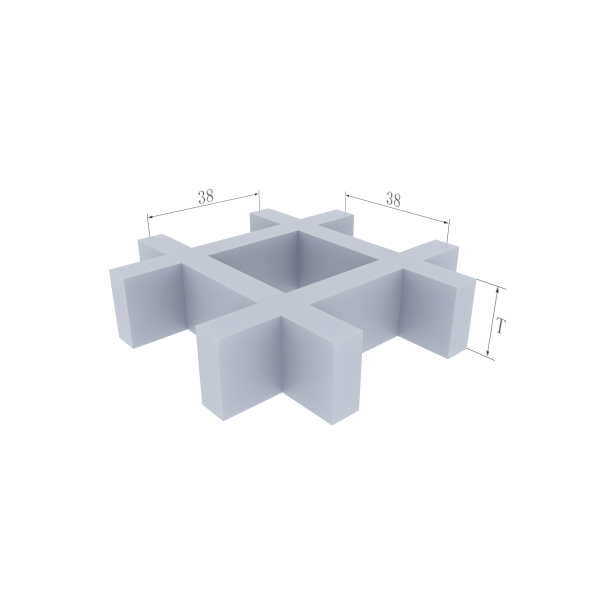
Frp Rectangular Tube Owned and operated by AZoNetwork, © 2000-2024