SPRAY FOAM MAGAZINE – Choosing the right air compressor for a spray foam rig is essential for reliability, productivity, and cost savings. Compressors need to produce enough airflow at the right pressure to power the air tools they are connected to. In the case of spray foam, there is a lot of equipment needing a steady flow of air. Spray Foam Magazine was therefore pumped up and ready to chat with Chicago Pneumatic (CP) to find out how their compressors can benefit the SPF contractor.
Chicago Pneumatic launched in 1901 when John W. Duntley met steel magnate Charles M. Schwab and the company was incorporated. They started by patenting the first single-valve pneumatic hammer and developed a new line of products including air tools, rock drills, and air compressors. Poly Resin Molds
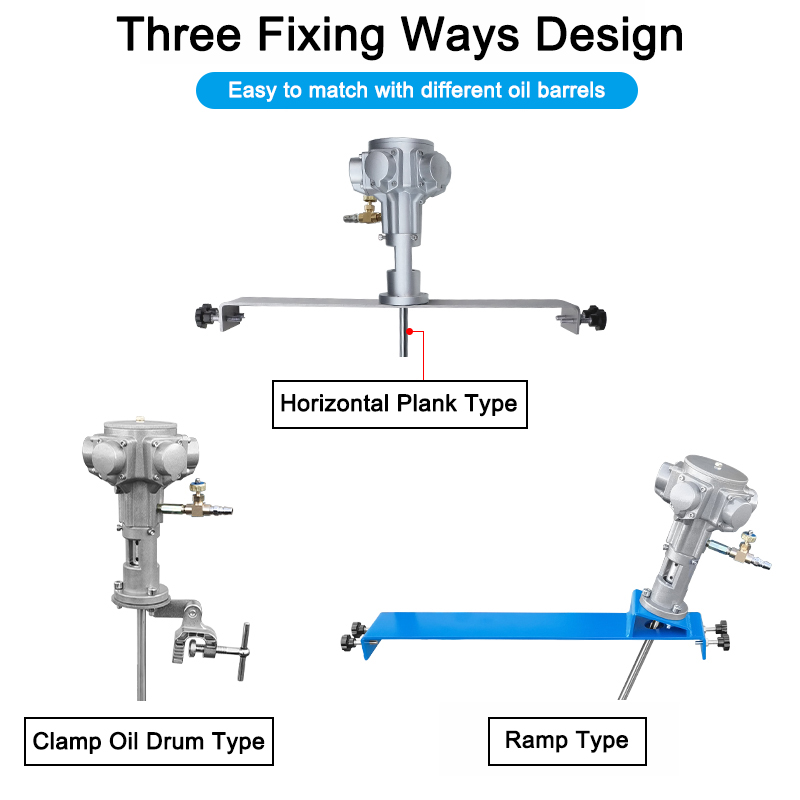
From designing the world’s first impact wrench, to playing a role in the Apollo 8 space mission and powering the construction of the Riyadh metro network, CP has evolved and transformed with every decade and for the future. Today, CP offers hundreds of compressor variants ranging from 2-340 hp to fit every application, including the Quiet Rotary Series (QRS) that is ideal for the spray foam industry.
CP specializes in compressors, compressor systems, dryers, filtration, and oil water separators with their main customer center in Rock Hill, SC. However, they sell through distribution all over the U.S. and Canada and their CP Compressor brand extends around the world with dealers in more than 100 countries.
Michael Campbell, President and General Manager, emphasizes, “Our slogan is ‘People. Passion. Performance,’ and we strive to make those the focal points of our organization. We make our partners and our customers our focus, and we aim to provide a high level of customer service with enthusiasm and passion for the compressed air industry. Our compressors speak for themselves in their reliability and technology, and we offer some of the toughest and most efficient compressor units on the market.”
CP sells into countless industries, some of which include the spray foam industry, food/beverage manufacturing, machine shops, paper production, plastics, and paint booths. When it comes to spray foam applications, they recommend their QRS compressor series due to their 100% duty cycle, long service life and quiet, reliable performance. According to CP, the heavy demand of constant air pressure for spray foam rigs is a real problem for many air compressor manufacturers. However, CP’s QRS compressors, which are suggested for use in a spray foam rig, are up for the challenge with tried and proven performance for the past few decades. With the air from the compressor used to actuate and/or purge the spray gun, mixer, or pumps and the spray foam machine itself, the rotary screw compressors provide the necessary air pressure for the SPF application process.
If there is not enough air pressure to the transfer pumps, it can decrease the capacity to a proportioner, which can result in off-ratio conditions with a reduced yield. If there is not enough compressed air to the SPF gun, the trigger can pause and minimize the neat-off ability. The crew will therefore waste time cleaning the tip. If there is not the correct amount of air pressure to the mixer, there is a much higher chance that it will reduce the yield and the material in the drum will not be mixed properly.
Spray foam applications typically need either a compressor with an integrated dryer, or an added stand-alone air dryer. This helps remove any moisture from the compressed air to ensure optimal performance of the spray foam system and helps reduce the chance of any inconsistencies in the application.
CP compressors have two categories, fixed or variable speed, and depending on the application will determine which compressor type is ideal. A variable speed air compressor is designed to be energy efficient as well as create energy cost savings for the contractor, when applicable. For fixed speed models, CP’s QRS series are ideal for the SPF industry. Each model is built with a low sound enclosure to provide sound dampening qualities. This makes the QRS sound level range from 61-71 decibels (dBA), comparable to the noise level of a household appliance.
Spray foam supplier, Profoam Corporation, choose CP compressors for their custom spray rigs. Profoam President, Ted Medford states, “We choose CP compressors for use in our Pro Series rigs because they are the absolute best-performing compressors. We have a reputation of being the best spray foam rig manufacturer and therefore cannot risk jeopardizing our reputation with inferior equipment.”
As the CP brand continues to grow and extend further into various markets, including spray foam, so does their portfolio and their passion for compressed air. CP will introduce more compressor product ranges this year that provide energy efficiency in smaller ranges. “We are excited for the future of CP and to be able to bring our reliable compressed air products further into the spray foam market,” says Maggie Rogers, Communications & Branding Marketing Manager. “We hope that when spray foam contractors are in need of a compressor for their operation, that the answer is always Chicago Pneumatic.”
For use by SprayFoamMagazine.com & Spray Foam Magazine
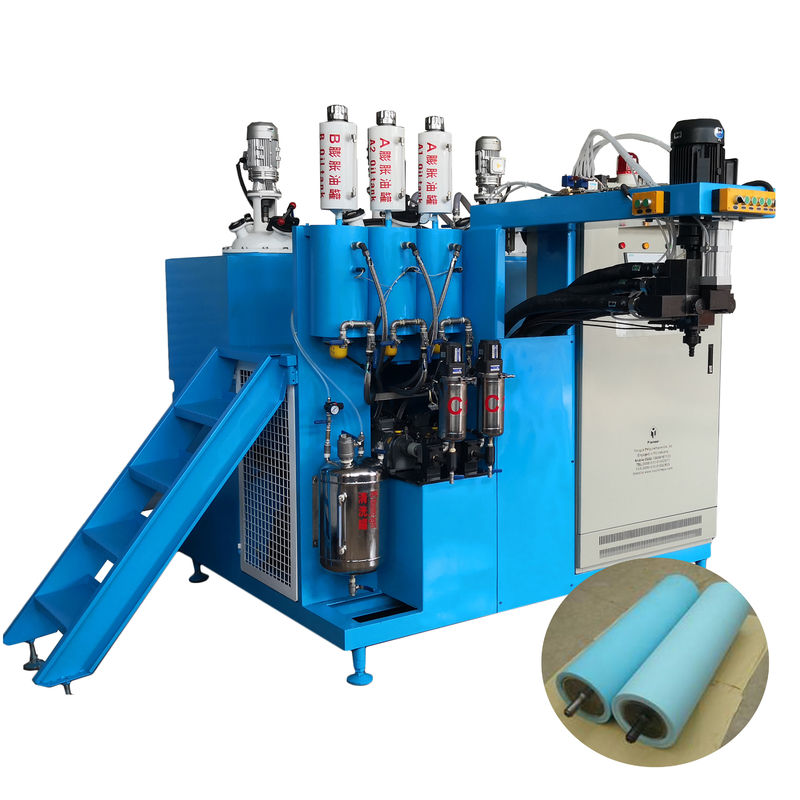
Polyurethane Foam Disqus website name not provided.