Features | August 31, 2023 | By: Annemarie Mannion
Airport runways are not the same as roads. They need to be built smoother and stronger to support the loads of jet planes without buckling under the weight, which is no small task in areas that may be swampy; dry; or subject to heavy rains, earthquakes or myriad other challenging soil conditions. Pond Liner
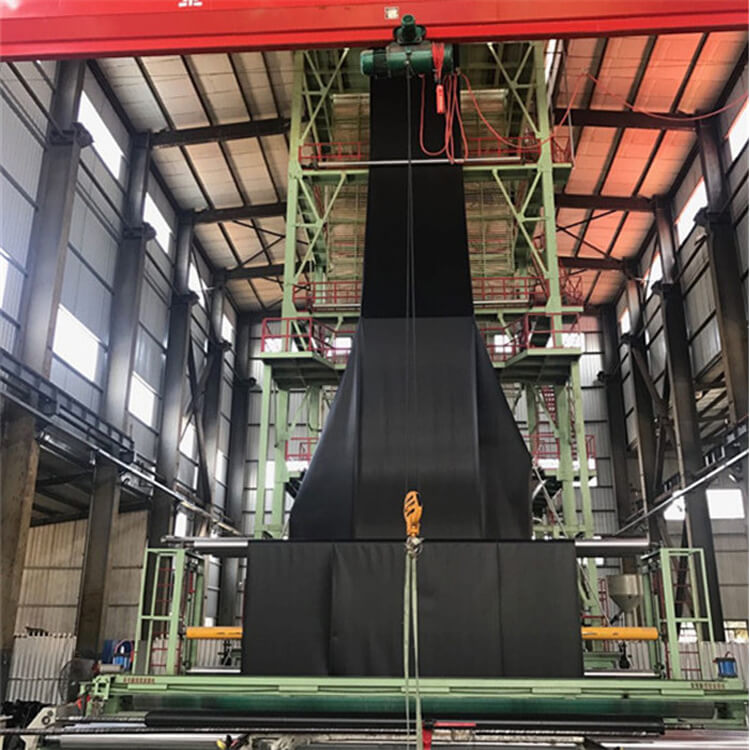
From the Himalayas to Montana and beyond, geosynthetics are the answer to many runway construction challenges: creating stable, flat platforms; preventing erosion; capturing stormwater; and protecting groundwater from jet fuel or other contaminants. They go in relatively quickly, meaning less disruption, and thus save projects time and money.
Specialty Fabrics Review is highlighting a few airport projects where geosynthetics are helping ensure the safety of cargo and the traveling public.
A runway at Toronto’s Pearson Airport in Mississauga, Ont., Canada, needed reconstruction, but it was in an area with soft and potentially contaminated soil, which made sub-excavation and removal of these soils cost prohibitive.
At the same time, stabilization of aggregate layers over the existing subgrade was deemed impossible without costly additional work, treatment and time.
For a solution, the airport pavement engineer turned to Tensar, a division of Commercial Metals Co. in Toronto. “Common practice would be to further excavate the soft soils and replace them with better-quality materials,” says Paul Hewgill, Tensar senior regional sales manager for Eastern Canada. “But there was nowhere on the airport property where they could put that soil, and they can’t just remove it and ship it somewhere off-site. There are a lot of regulations around that.”
Given Canada’s short construction season, time was of the essence. “Their goal was to get this runway rebuilt in one construction season,” Hewgill says. “It is also a very busy runway, so they had to get it done.”
Tensar worked with the pavement designers to mechanically stabilize the recycled concrete aggregate subbase so that sub-excavation and removal of the subgrade soil was not required. The project was originally specified with Tensar TX7 geogrid and a nonwoven geotextile for filtration. During the project, it became clear that another Tensar product, InterAx® NX750 geogrid, would provide better performance. Both are made from polypropylene.
“Tensar InterAx features an improved geometry that stabilizes a broader range of aggregate types,” says Hewgill. “Typically stone, sand or gravel are used in these projects. But in this case, a unique part of the project is that they ‘rubble-ized’ the existing concrete runway and reused it as the aggregate subbase and aggregate base below the new runway.”
Reusing the concrete was a plus. This move eliminated the need to further excavate the soils and truck in more aggregate to build the area up, saving time and carbon emissions.
Looking ahead, Hewgill says long-term viability of stabilization with geogrids is a focus. Tensar is researching how these products stand up to various types of uses and conditions.
“We’ve done additional research which quantifies how these products perform under heavily loaded situations or applications, and that’s allowed for more precise design to be carried out,” he says. “In addition, we have quantified volumetrics in every design module in our software so you can quantify the cost, time savings and the savings of embodied carbon.”
Establishing that these products benefit the environment is another focus. “The new trends are about quantifying sustainability, and that’s where we’ve achieved environmental product declarations on these products,” Hewgill says. “We are in a position to help clients who need to quantify a reduction of carbon.”
Hewgill believes the Toronto airport would not have reached its time or cost goals without InterAx. “They would have gotten into more excavation and more haulage of rock,” he says. “They could’ve extended this project by another few months. We can easily say that we reduced time by 25%.”
Pearson, he adds, has been satisfied with geogrid. “Toronto Pearson Airport has used geogrid almost every time they have ever reconstructed taxiways, runways and the areas around gates,” he says. “They’ve used it all the time over a long period of years because they don’t want to get into removing any material from their property.”
Tensar estimates that use of the company’s product at the airport saved millions of dollars for its customer.
In the mist-shrouded, lush green valleys of the towering Himalayas, an airport runway, terminal and apron are shielded by an earth embankment soaring above it.
The Pakyong Airport took nine years to build and is lauded as an engineering marvel. Removing the side of a mountain to create a flat platform for the runway was just one of the challenges of building one of the five highest airports in India.
Maccaferri, which provides solutions for civil, geotechnical and environmental construction markets, created a reinforced soil structure to serve as a retention embankment for the project’s north-south runway.
The region’s mountainous terrain, heavy rainfall, high seismicity, balance of cut and fill, and lack of land availability were other challenges of building the airport that stands at 4,500 feet.
The company’s Paramesh system was used in constructing the airport that needs to withstand earthquakes and monsoons. It comprises a high-strength geogrid (the polyethylene ParaLink®) along with fascia elements Terramesh® system (polymer-coated steel wire mesh) and Green Terramesh (a wire-reinforced biodegradable erosion control blanket that allows vegetation to grow through).
The original plan to use a reinforced concrete wall for the embankment was abandoned in favor of geotextiles and other geosynthetic products, which provided a more flexible, earthquake-resistant solution for the reinforced soil embankments. A wraparound double-twisted hexagonal wire mesh facing was used for less precipitous sections.
“Imagine importing the required amount of select backfill material and disposal of the excavated soil from the job site,” says Sachin Mandavkar, technical director at Maccaferri. “For this reason, one of the critical project requirements was to reuse the excavated soil from the job site to build the MSE [mechanically stabilized earth] structure.”
The team literally moved the mountain, carving away soil from above the runway and using it below. The base for the airport and runway became walls up to 72 meters (236 feet) high, reinforced by a high-strength geogrid.
“Backfilling was done in a 200-millimeter [8-inch] compacted lift thickness, and five layers of compacted soil measuring 1 meter [3.3 feet] high was installed behind each Terramesh unit. It took approximately five days to backfill each Terramesh lift along the wall length and ensure that geotextile would be held in position,” says Ratnakar Mahajan, technical manager at Maccaferri.
Geotextiles also addressed drainage. Nine streams—known as jhoras—cross the airport underground and impact ground stability.
“A geotextile was used for separation and filtration to replace graded filter,” says Mahajan. “With Terramesh being porous facia, there is possibility of soil loss from the facia. Hence, conventional graded filter could be an option behind Terramesh. Similarly for chimney drain, graded filter is required.”
Concrete culverts collect the drainage from the slopes and runway and divert the water off-site.
“When you cut into a mountain, you are going to encounter these streams, and the water from these streams needed to be collected and released at the front of the structure,” Mandavkar says. This protects the walls from water pressure building up behind them.
A geotextile also was used as a separator and filter wrapped around drainage pipes, which required binding wire for holding the geotextile around the pipes. The geotextile was cut in pieces to match the chimney drain height, which was wrapped to avoid clogging of the chimney drain.
The resilience of the MSE structure and other elements have been proven multiple times, including in April 2021 when a magnitude 6.4 earthquake struck northeast India; the wall stayed in place.
“The structures performed excellently under earthquake loading, due to their flexible nature,” Mandavkar says.
For runway reconstruction at the Billings Logan International Airport (BLI) on Montana’s dry eastern plains, a geotextile served in stormwater detention and erosion control on slopes.
“The airport is constructed on sandstone rock with little to no topsoil, making vegetation very difficult to establish and erosion prevalent,” says Cory Schneider, business development manager for Presto Geosystems in Appleton, Wis.
During storms, water streams through the facility’s stormwater pipes at high velocity. The detention ponds provide a buffer to control the rate of that discharge and prevent erosion.
“The engineer provided project-specific details such as velocity, unit discharge, bed slope and channel geometry for the channel and slope length and slope angle for detention pond slopes,” Schneider says. “Using this information, in conjunction with specialized calculation methods developed in collaboration with the Colorado State University hydraulics lab, we were able to recommend a cell size, cell depth, rock size and staking pattern that would be able to withstand the stated hydraulic conditions.”
The product selected was 3D GEOWEB® geocells, made of high-density polyethylene, which were used for open channel erosion protection and were placed over a geosynthetic clay liner (GCL) on the side slopes of two detention ponds.
“[GEOWEB is] a honeycomb-like, three-dimensional, cellular product,” says Joe Kaul, owner of Kaul Corp., an independent representative for Presto Geosystems. “In this case it was [placed] 6 inches deep. The cells are connected together to form a mat that has diamond-shaped cells that the rock goes into and has a hard time falling out of.”
One of the product’s benefits is that “It allows for use of less aggregate than normally would be required,” Kaul adds. “Normally, if they want to do this with just rock, it would have to be 4 to 8 inches of riprap. And it would have to be several feet deep. We used 1 to 2 inches of rock 6 inches deep. So there was a savings on natural resources and the cost.”
The product has evolved over the years. “During initial development of the product between Presto Geosystems and the U.S. Army Corps of Engineers, there was only one cell size and one cell depth,” Schneider says. “GEOWEB geocells are now available in three different cell sizes and five different depths.”
The range of cell sizes and depths allows the engineers to select the lowest-cost combination of cell size and cell depth that will be effective for an application. The company also has developed many different installation accessories for connecting the sections together as well as anchoring them, which provide for faster, stronger and safer installations.
Looking forward, sustainability is a goal. “There is a lot of focus on how geosynthetics make infrastructure more sustainable,” Schneider says. “They extend the service life of roads, reduce the use of aggregates, conserve and protect water, minimize land disturbance, and control soil erosion.”
According to Schneider, the ways that geosynthetics can be used to build the next generation of sustainable and resilient infrastructure and sustainability will be a hot topic for the foreseeable future.
Flying into the airport recently, Kaul was pleased with the project, completed in 2016. “I flew into Billings last fall and looked it over from the landing of the plane, and it all looked to be intact,” he says.
Annemarie Mannion is a freelance writer based in Willowbrook, Ill.
AI saves businesses time, but it needs to learn physics
Fabric structures provide crucial support in disasters
Small sustainability actions can make a big difference
Commercial renovations focus on comfort, the warmth of home
Rachal McCarthy builds on 40 years of progress at NTI Global
Specialty Fabrics Review is a publication of the Advanced Textiles Association
Copyright © 2024 Advanced Textiles Association. All rights reserved.
1801 County Road B W, Suite 100 Roseville, MN 55113-4052, USA
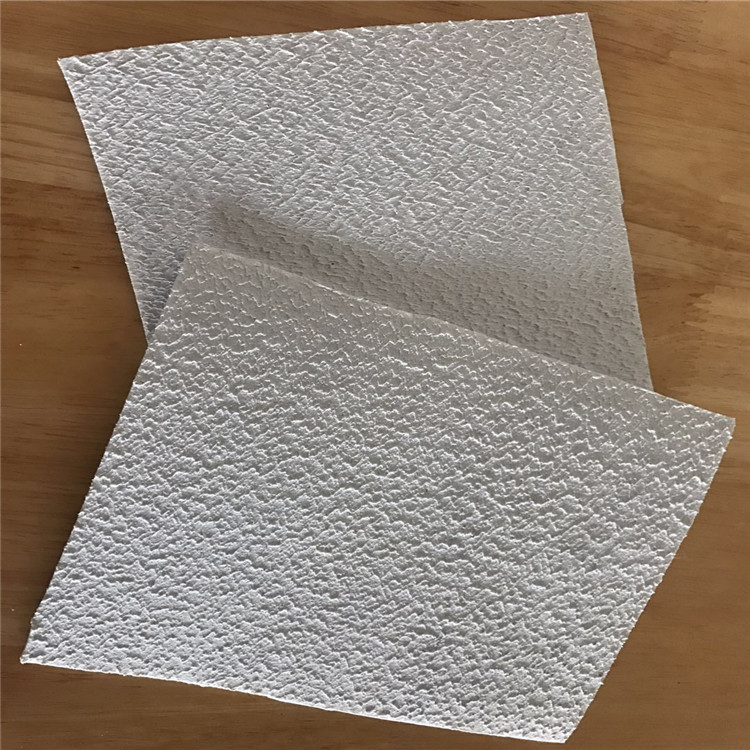
Pond Liner Seaming Tape Terms of Service Privacy Policy