The aerospace industry has long depended on gundrilling and deep hole drilling to manufacture many critical components used in commercial and military aircraft. Deep hole drilling is used for landing gear, cylinders, actuators, piston rods, fittings, shafts, pins and even fasteners. Long, deep holes in parts made from exotic materials are common, and many of these parts have challenging features such as thin wall sections, stepped bores, internal contours and blended transitions.
Businesses change based on customer demands, and the aerospace industry is experiencing a host of changes related to growth in many global regions that are flying more. And more is expected from suppliers, including greater fuel economy, passenger comfort and the never-ending quest for safety, all of which drive engineering and design. As a result, short-flight regional aircraft and long-haul aircraft are evolving to meet the challenges. But what does this mean for deep hole drilling? Hydraulic Drill Machine
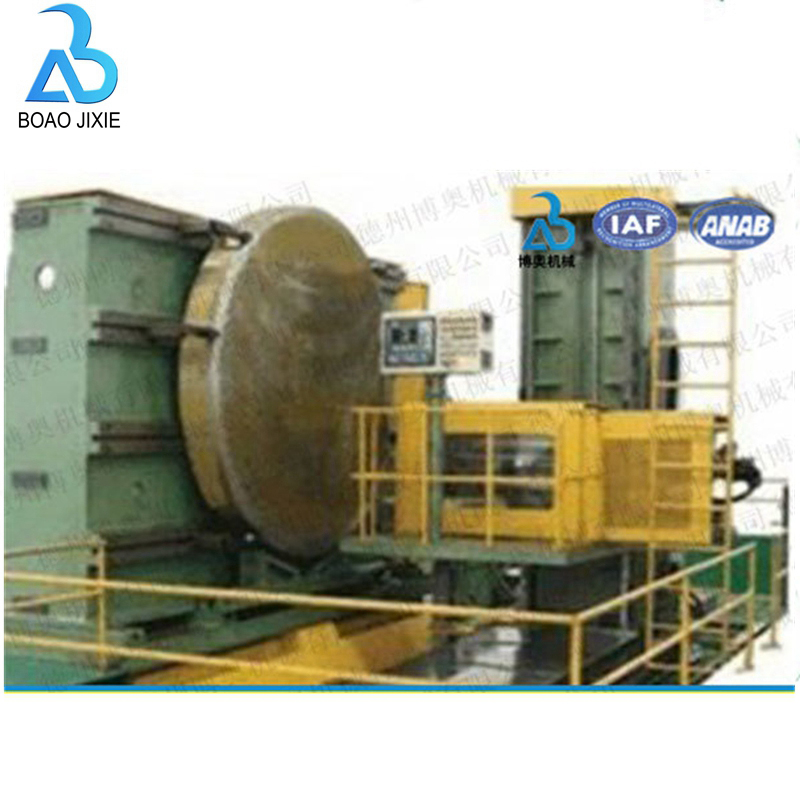
The fundamentals of gundrilling and Boring and Trepanning Association (BTA) drilling have not changed much over the years. The tools have off-center tips to create forces against guide pads. This, in turn, helps generate precise holes and ensures straightness and accuracy while providing good surface finishes, roundness and consistency—making deep hole drilling a value-added process. The cutting tool design execution, however, has changed to keep pace with advances in modern metal cutting.
Indexable tools, for instance, have been in use for a long time. Over the years, indexable tooling has advanced in terms of carbide grades, coatings, edge geometry, and improved head design to boost the strength and accuracy of the insert seat and clamp. These improvements have allowed smaller, deeper holes to be drilled with indexable tools for better accuracy over previous generation tools. Indexable tools are particularly desirable when special forms are required in the workpiece and multiple hits for each hole are required to create the finished profile.
Often referred to as bottle boring, internal contouring with a CNC-controlled axis is becoming mainstream. While the process used to be exclusive for large OEMs with the budget and product line to justify the startup investment, UNISIG GmbH now offers standard machine configurations, tooling and application support that make it accessible to all manufacturers—and even job shops—that want to grow their aerospace business.
Along with tooling advancements, tool presetting is also becoming a necessity when approaching difficult-to-manufacture components. The head setup and form measurement are much more controlled when using a laser pre-setter or high-resolution camera to eke out the last few tenths or microns from a process. RFID automates communication with the gundrilling or BTA drilling machine CNCs, and reduces the risk of human error.
Deep hole drilling machines are becoming smarter, which is critical when the bores produced are difficult to measure or operators are unable to see what is happening at the cutting tool to make adjustments. Accurate, real-time process feedback from the spindle and servo loads, as well as feedback on vibration, temperature, coolant flow and pressure, are necessary to establish a reliable manufacturing plan for aerospace components. Data collection and connected machines provide information that can then be used for analysis and process improvements.
The materials selected for aerospace parts are often exotic and difficult to machine—stainless steels, nickel alloys, titanium and proprietary high-strength alloys are common. Deep hole drilling machines must be engineered to handle these materials and the future materials developed for extreme applications. The motion controllers on the machine—motors, drives, feedback devices and high-speed processors—must maintain exact position and velocity control even when the material and tools are pushing the limits.
Automation is another advancement in aerospace machine technology, with every machine, process and application begging the question: Can we automate all or part of this? Automation often starts by creating a reliable machining process through machine monitoring and adapting, then applying in-machine automation and moving to external part handling robotics.
As the aerospace industry changes, so too must the tooling and machines used for generating deep holes in parts. Whether gundrilling or BTA drilling, today’s advanced tooling provides aerospace manufacturers with much-needed accuracy, while innovative deep hole drilling machines allow for process optimization through critical data collection and automation.
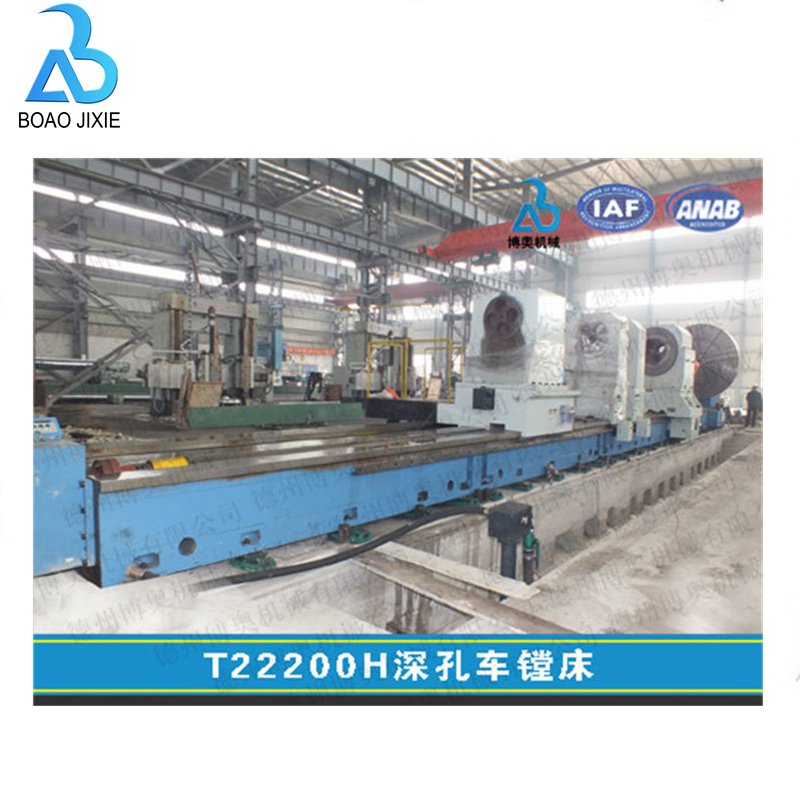
Horizontal Honing Mill The aerospace industry has strong growth potential, particularly around deep hole drilling. CNC machining centers and multi-tasking machines are often used to drill deep holes, but some of our most successful projects have involved introducing a gundrilling or deep hole drilling machine to complement the machining centers, unloading long cycle times and eliminating problems from a manufacturing process.