Given the rapidly accelerating pace of electrification, EV manufacturers need to strain every sinew to streamline the assembly process. Here’s an idea to speed up cable connection, explains Markus Häfliger.
Swiss cable gland specialist AGRO has developed a new solution for multi-conductor cables and high-voltage cables from 16-120mm2. The EVolution EMC cable gland is designed for reliable installation, and can be prepared by pre-assembling part of the gland on the cable, enabling it to be quickly plugged in on the vehicle. The cable connection is still achieved by means of a cable lug. 20mm Cable Gland
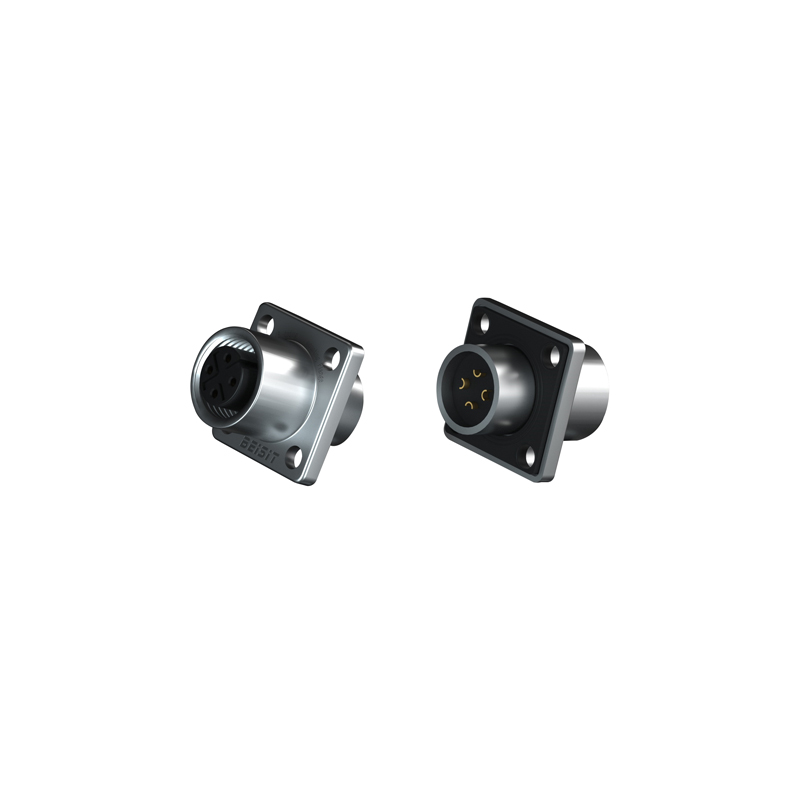
This new type of EMC cable gland has been developed with a particular focus on the requirements of the manufacturers of sophisticated commercial, special-purpose and sports vehicles, and construction machinery.
The compact cable gland ensures sealing in accordance with IP68 and IP6K9K protection classes, and it is future-proofed through the use of lead-free brass during manufacture.
Its operating temperature range is from -40°C to +140°C. When specifying cable glands, two important features are considered: EMC shielding effectiveness and shield current-carrying capacity. In the frequency range from 30MHz to 300MHz, shielding effectiveness of at least 86 dB is achieved, while the current-carrying capacity of the shield contacts ranges from 115A for size M20 to 195A for size M32.
Among the most important considerations in the vehicle manufacturing industry are process reliability and documentation of the individual work steps. Using the cordless hand-held Axi-Press tool, the assembly work can be carried out reliably and traceably. If not already taken care of in a previous cable assembly process, it can be done without difficulty during installation on the vehicle. The crimping of the shield contact sleeve takes just a few seconds, with traceability ensured by an integrated data interface. Traceability is also possible via the batch number of the EVolution EMC. The cable gland is designed in such a way that it can be repeatedly disconnected and reinstalled, while still maintaining its reliability. Where vehicles are mass-produced, short assembly times on the production line are an important objective.
This was given special attention during the development of the EVolution EMC cable gland, with the result that its use can now make a significant contribution towards reducing vehicle manufacturing costs. During installation on the vehicle, the cable lug is simply passed through the lower part of the cable gland, the shield contact sleeve is plugged in, the sealing insert is placed in position and the compression nut is fully tightened. Even without the use of a torque wrench, the IP degree of protection is ensured. The individual work steps have now become easier and more reliable, saving manufacturers time and money.
Markus Häfliger is an innovation driver for eMobility at AGRO
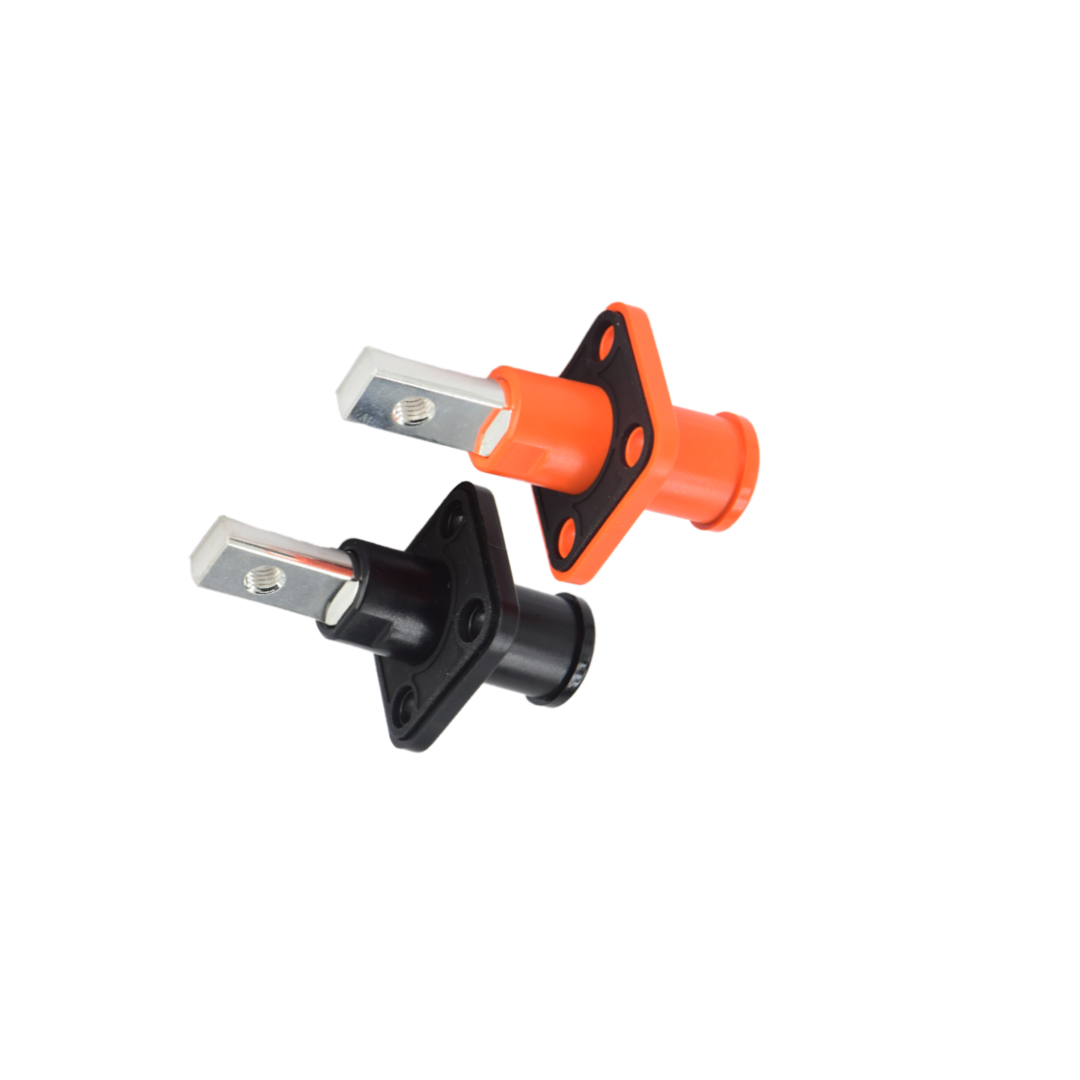
Metal Cable Conduit © Setform Limited 2019-2024 | Privacy policy | Archive