Stratus webinar - watch now
22/05/2024 FLIR Systems UK (*Teledyne FLIR) Engine Oil For Diesel Engine
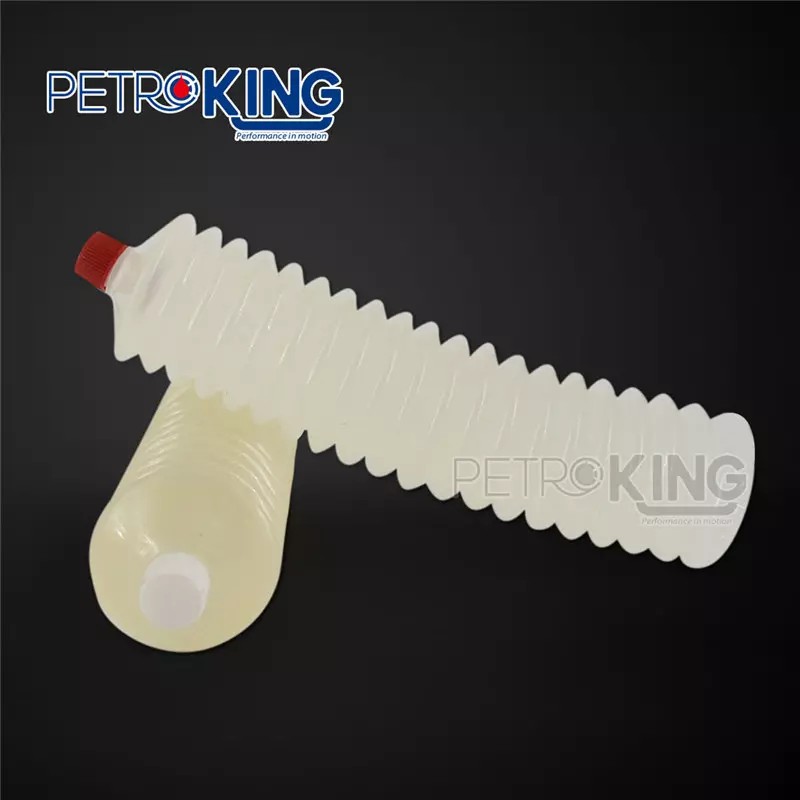
Contamination in a vacuum chamber can result in dangerous chemical reactions and unwanted side effects. The Princeton University office of Environmental Health and Safety (EHS) highlights that vacuum work can lead to implosions and potential dangers of airborne contaminants, glass, chemicals splattering and fire. Here, Chris Johnson, managing director at specialist bearing supplier SMB Bearings, explains what to consider when choosing lubricants and bearings for vacuum environments.
Vacuum chambers require a high level of cleanliness, extending down to the molecular scale. This is crucial to ensure the reliable operation of critical equipment, such as semiconductor manufacturing equipment, space simulation chambers and plasma research devices, to name a few.
Managing a vacuum chamber system is crucial due to the substantial risk that contaminants pose to safety, reliability, sustainability and environmental impact. One significant cause of contamination in vacuum systems is outgassing, which occurs when volatile substances like gasses or vapours are released from materials exposed to reduced pressure.
This phenomenon can significantly impact the performance and cleanliness of the system. Outgassing reduces the vacuum chamber’s purity, leading to changes in pressure within the chamber while contaminating other equipment.
Bearings are susceptible to outgassing because of the materials used in their construction and surrounding environmental conditions. Outgassing in bearings can lead to a host of risks and challenges, gradually compromising their performance through increased friction, accelerated wear, and the potential for failure.
Bearings are typically composed of a variety of materials, including metals, plastics and lubricants. Some of these materials may contain unpredictable compounds or trapped gasses, such as lubricants with volatile additives or solvents and plastics with residual processing chemicals.
When bearings are exposed to a high-vacuum environment, the lower external atmospheric pressure compared to the internal pressure of the material can cause these substances to vaporise and escape into the chamber.
Temperature plays a significant role in the outgassing process. Higher temperatures can expedite the release of hazardous compounds from materials and temperature fluctuations during operation in a vacuum chamber, can further worsen the issue.
To address these concerns, it’s key to choose bearing materials that are less prone to this phenomenon. For instance, stainless steel bearings and ceramic bearings are well-suited for high-temperature chambers. Options like 316 grade stainless steel bearings are capable of withstanding extreme temperatures as low as -200°C and as high as 500 °C, albeit with a reduced load capacity.
Stainless steel offers the advantage of minimal outgassing when used in the construction of bearing components. This includes the rings, balls and retainers. Consequently, stainless steel bearings, whether open or shielded, are a preferred choice over nitrile rubber sealed bearings. The latter are commonly used in vacuum applications but can introduce contamination risks, particularly on delicate surfaces like optical components.
In addition, many plastic bearings are unsuitable because of high outgassing rates, but plastic bearings made from PEEK have minimal outgassing attributes, making this material a suitable choice for use in vacuum and reduced-pressure environments.
Bearings often rely on lubricants to reduce friction and wear. In vacuum environments, the selection of suitable bearing lubricants requires careful consideration. This is primarily due to the tendency of most greases to vaporise excessively, resulting in potential contamination and ineffective lubrication. Bearing lubricant choice must therefore be suitable for all specified environmental conditions considering operating factors such as speed, load and temperature.
However, in many high vacuum chambers, bearings operate at very low speeds and are either used without any lubrication or have a dry coating, such as molybdenum disulfide (Mos2). In cases where lubrication is necessary, it’s essential to opt for a low-outgassing specialist vacuum grease.
Additionally, there is a risk of cold-welding in completely unlubricated bearings, as steel behaves differently in ultra-high vacuum (UHV) conditions. The bearing’s steel oxide layer, which can regenerate in air to prevent cold-welding, does not have the same protective effects in an industrial vacuum environment, potentially leading to atomic metal-to-metal contact between rings, balls and the retainer.
For this risk to be reduced, bearings in UHV chambers are often dry coated with Mos2 or tungsten disulfide (WS2). Specialist vacuum greases can also prevent this issue. To effectively manage outgassing concerns in vacuum applications, choosing materials specifically designed with low-outgassing properties, along with appropriate lubrication is needed.
Regular maintenance and monitoring of the vacuum system is necessary to address outgassing related problems promptly. For optimal performance, specialised low volatility perfluorinated greases with minimal outgassing rates are available and widely used in applications like semiconductor manufacturing and deep space equipment.
SMB Bearings supplies stainless steel unlubricated bearings, bearings with dry coatings or relubricated with vacuum greases and bearings with specialist retainers such as PEEK for use in UHV chambers.
For more information, please contact: SMB Bearings Ltd Unit 8 West Oxon Industrial Park Brize Norton Oxon OX18 3YJ Tel: 01993 842 555 Email: sales@smbbearings.com Web: https://www.smbbearings.com
Schaeffler expands its portfolio of bearing tools for industrial maintenance
Process and Control Today are not responsible for the content of submitted or externally produced articles and images. Click here to email us about any errors or omissions contained within this article.
Sign-up for our weekly eNewsletter
Advertise with us | Media pack

All Purpose Lithium Grease © Copyright 1999-2024 Process and Control Today Ltd Registered in England No. 3733110 - studio44