A 360-degree look at resin conveying systems: types, operation, economics, design, installation, components and controls.
This Knowledge Center provides an overview of resin moisture and the drying process, including information on the best drying practices for your manufacturing facility. 3 Layer Extrusion Machine
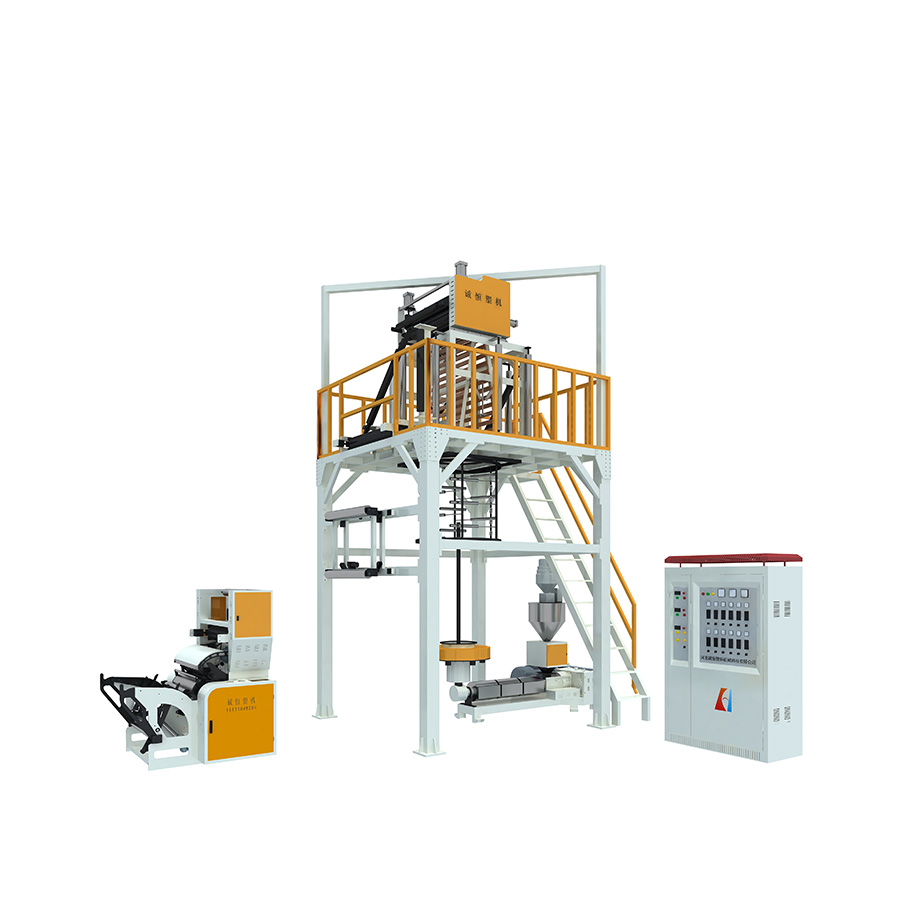
Combat the skilled labor shortage using this comprehensive resource to train your own plastics processing experts.
Deep dive into the basics of blending versus dosing, controls, maintenance, process integration and more.
This Knowledge Center provides an overview of the considerations needed to understand the purchase, operation, and maintenance of a process cooling system.
Learn about sustainable scrap reprocessing—this resource offers a deep dive into everything from granulator types and options, to service tips, videos and technical articles.
While the major correction in PP prices was finally underway, generally stable pricing was anticipated for the other four commodity resins.
Despite price increase nominations going into second quarter, it appeared there was potential for generally flat pricing with the exception of a major downward correction for PP.
First quarter was ending up with upward pricing, primarily due to higher feedstock costs and not supply/demand fundamentals.
Despite earlier anticipated rollover in prices for most of the volume commodity resins, prices were generally on the way up for all going into the third month of first quarter.
While price initiatives for PE and PVC were underway, resin prices had rollover potential for first two months of 2024, perhaps with the exception of PET.
Flat-to-downward trajectory for at least this month.
Resin drying is a crucial, but often-misunderstood area. This collection includes details on why and what you need to dry, how to specify a dryer, and best practices.
Take a deep dive into all of the various aspects of part quoting to ensure you’ve got all the bases—as in costs—covered before preparing your customer’s quote for services.
In this collection of articles, two of the industry’s foremost authorities on screw design — Jim Frankand and Mark Spalding — offer their sage advice on screw design...what works, what doesn’t, and what to look for when things start going wrong.
In this collection, which is part one of a series representing some of John’s finest work, we present you with five articles that we think you will refer to time and again as you look to solve problems, cut cycle times and improve the quality of the parts you mold.
Gifted with extraordinary technical know how and an authoritative yet plain English writing style, in this collection of articles Fattori offers his insights on a variety of molding-related topics that are bound to make your days on the production floor go a little bit better.
In this three-part collection, veteran molder and moldmaker Jim Fattori brings to bear his 40+ years of on-the-job experience and provides molders his “from the trenches” perspective on on the why, where and how of venting injection molds. Take the trial-and-error out of the molding venting process.
Mike Sepe has authored more than 25 ANTEC papers and more than 250 articles illustrating the importance of this interdisciplanary approach. In this collection, we present some of his best work during the years he has been contributing for Plastics Technology Magazine.
In this collection of content, we provide expert advice on welding from some of the leading authorities in the field, with tips on such matters as controls, as well as insights on how to solve common problems in welding.
Mold maintenance is critical, and with this collection of content we’ve bundled some of the very best advice we’ve published on repairing, maintaining, evaluating and even hanging molds on injection molding machines.
Thousands of people visit our Supplier Guide every day to source equipment and materials. Get in front of them with a free company profile.
NPE2024: Lowering barriers to additive manufacturing adoption in toolmaking.
Allegheny Performance Plastics turned to 1factory's cloud-based manufacturing quality control software for streamlined, paperless quality systems.
To design the best mixers for single screws, you must completely understand how polymer moves through a mixer channel or groove.
NPE2024: Focus is on additives for plastics including PVC and WPC industries.
At NPE2024, Novatec moves to rewrite the rules for material conveying with patent-pending smart-pump technology.
While the major correction in PP prices was finally underway, generally stable pricing was anticipated for the other four commodity resins.
With no minimum order and an impeccable record of on-time delivery, Precision Color Compounds is becoming a force in the color masterbatch business.
Thermosets were the prevalent material in the early history of plastics, but were soon overtaken by thermoplastics in injection molding applications.
After a six-year hiatus, this year’s show was a resounding success, with meaningful technologies on display that will help processors run their businesses more efficiently.
Key factors for the progress are innovative materials, advanced automation and precision engineering.
Topping five other entries in voting by fellow molders, the Ultradent team talks about their Hot Shots sweep.
Serendipitous Learning Opportunities at PTXPO Underscore the Value of Being Present.
Introduced by Zeiger and Spark Industries at the PTXPO, the nozzle is designed for maximum heat transfer and uniformity with a continuous taper for self cleaning.
Ultradent's entry of its Umbrella cheek retractor took home the awards for Technical Sophistication and Achievement in Economics and Efficiency at PTXPO.
technotrans says climate protection, energy efficiency and customization will be key discussion topics at PTXPO as it displays its protemp flow 6 ultrasonic eco and the teco cs 90t 9.1 TCUs.
Shibaura discusses the upcoming Plastics Technology Expo (PTXPO) March 28-30
Oerlikon HRSflow’s T-Flow HRS control has launched with three models that are configurable to multiples of six zones.
NPE2024: Dukane’s new Ultrasonic Thin Wall welding system is well suited for welding applications of PP to PP TD25 painted parts.
Series offers higher output, lower melt temperatures and energy savings.
Noting that geopolitical changes require new corporate strategies, European plastics and rubber machinery trade groups announced that incoming orders fell 22% in 2023.
System tracks, controls and saves everything from material recipes to process parameters, operator activity from logging on to start, to emergency stops and more.
Unit is designed to match the requirements of feeding low bulk density fillers and materials in the compounding process.
Mixed in among thought leaders from leading suppliers to injection molders and mold makers at the 2023 Molding and MoldMaking conferences will be molders and toolmakers themselves.
After successfully introducing a combined conference for moldmakers and injection molders in 2022, Plastics Technology and MoldMaking Technology are once again joining forces for a tooling/molding two-for-one.
Multiple speakers at Molding 2023 will address the ways simulation can impact material substitution decisions, process profitability and simplification of mold design.
When, how, what and why to automate — leading robotics suppliers and forward-thinking moldmakers will share their insights on automating manufacturing at collocated event.
As self-imposed and government-issued sustainability mandates approach, injection molders reimagine their operations.
August 29-30 in Minneapolis all things injection molding and moldmaking will be happening at the Hyatt Regency — check out who’s speaking on what topics today.
Get your clicking finger in shape and sign up for all that we have in store for you in 2023.
Molding 2023 to take place Aug. 29-30 in Minnesota; Extrusion 2023 slated for Oct. 10-12 in Indiana.
Join this webinar to learn about Conair's patented Conveying with Optimizer system, which utilizes artificial intelligence (AI) to overcome resin conveying issues automatically. Conveying with Optimizer uses valves, remote sensors and AI to eliminate conveying challenges that operators face daily throughout the plant. With this new fully-retrofittable solution, interruptions like clogged filters, air leaks, changes in density or distance, moisture changes, and operators making manual adjustments can all be eliminated with Conair's Conveying with Optimizer. Agenda: What exactly is Conveying with Optimizer? What are the benefits of using Conveying with Optimizer? What problems does Conveying with Optimizer overcome? How to upgrade your system
Cooling time is typically the longest step of the molding process. How can you make it more productive? Learn how cooling time can be turned into production time by running two molding processes simultaneously on a single molding machine. For longer cycles, this can mean twice the productivity. In this webinar, you'll learn more about the Shuttle Mold System and how to calculate its potential productivity impacts for your application. Agenda: Learn how the Shuttle Mold System can deliver value to your business See the recent technical updates made to the system Calculate the potential impact on productivity
Discover possible applications in large format printing including layup tools, transport modules, film fixation devices, design components and enclosures. These are used in various industries such as automotive, aerospace, architecture and many others. Agenda: Possible applications in large format printing: layup tools, transport modules, film fixing devices, design components and enclosures. Process reliability and component quality in component production Pros and cons of the technology Sneak peek into current development projects—What will the large format printing of tomorrow look like?
In this webinar, Cold Jet will discuss some of the ways processors use dry ice such as in-machine mold cleaning at operating temperatures, de-flashing or de-burring parts, improving OEE scores, extending mold life, cleaning parts before painting, post-processing 3D printed parts, lowering GHG emissions, and monitoring and reporting the process. Agenda: Cold Jet Overview & Dry Ice 101 Understanding the Process and Fine-Tuning Techniques Case Studies: Applications in Plastics Monitoring the Process Exploring the Importance of Dry Ice Cleaning in an ESG Era
Finding it hard to get technical talent? Experiencing the pain of a knowledgeable, long-term employee's retirement? Learn how plastics processors are training generative AIs on their operations and unlocking the value from their tribal knowledge. Plastics processors are training generative AI models on their operations — from machine manuals to tools, polymers, procedures, maintenance records and engineering projects. Applying generative AI in the right ways can lower plastics processors' costs, improve overall equipment effectiveness (OEE) and upskill teams. In this webinar, you'll learn how to deploy AI technical assistants to your teams, what works and what doesn't, and how to use AI to build an organization that never loses tribal knowledge and fosters inter-team collaboration. Agenda: What is generative AI and how can its cognitive abilities be applied to plastics? Case study: how an injection molder trained a large language model on manuals and maintenance records to reduce downtime Case study: using generative AI in engineering teams to improve product development Live demonstration of a generative AI deep-trained on plastics knowledge Looking to the future: five predictions for an AI-augmented workforce in plastics
Turnaround time can be as low as 24 hours, although two or three days might be more typical. Rapid prototyping like this is especially useful to quickly identify critical end-use part geometries that will work in the molding process. Key components include material choice, 3D printing technology selected, use of adaptable mold bases for the mold inserts and implementation of appropriate injection molding process conditions. This presentation will review work conducted toward the assessment of a high-stiffness, high-temperature-resistant ceramic modified urethane acrylate for injection molding inserts. Agenda: Guide for 3D-printed injection mold inserts Optimization of digital light processing (DLP) printing Compatibility with various thermoplastics Real-world application success stories
The Society Plastics Engineers (SPE) Extrusion Division and the SPE Eastern New England Section will co-host the Screw Design Conference-Topcon on June 19-20, 2024 @ UMass Lowell in Lowell, MA. This highly technical program will focus upon screw design principles for single and twin screw extruders with wide ranging topics relating to screw designs for feeding, melting, mixing, venting and pumping plastics products and parts. Areas of focus will include screw designs for melt temperature and gel management, gel minimization, bioplastics, recycled materials and foaming. In addition to the technical sessions, a tour of the UMass Lowel Plastics Processing Laboratories will be integrated into Day 2 of the event. This program is not just for screw designers, but to help anyone responsible for any type of extrusion operation to evaluate existing extrusion equipment; and also to prepare for future projects. Technical Chair: Eldridge M. Mount III, e-mail emmount@msn.com Corporate sponsorships - A limited # of corporate sponsorships (15) are available on a 1st come basis. Included is a 6’ tabletop display (must fit on table), denotation in all promotional activities, and 1 no charge registration. To become a sponsor contact: Charlie Martin, Leistritz Extrusion, e-mail cmartin@leistritz-extrusion.com, cell 973-650 3137 General information: A reception on Day 1 and a tabletop display area will allow the attendees to meet and discuss state-of-the-art screw technologies with industry experts. The SPE Extrusion Division will issue a “Screw Design Certificate” to all participants who have attended the program. Students are encouraged to attend and will receive a discounted rate. For additional information contact: Program Chair: Karen Xiao, Macro Engineering, KXiao@macroeng.com
Debuting in 2010, the Parts Cleaning Conference is the leading and most trusted manufacturing and industrial parts cleaning forum focused solely on delivering quality technical information in the specialized field of machined parts cleansing. Providing guidance and training to understand the recognized sets of standards for industrial cleaning, every year the Conference showcases industry experts who present educational sessions on the latest and most pressing topics affecting manufacturing facilities today. Discover all that the 2022 Parts Cleaning Conference has to offer!
Presented by Additive Manufacturing Media, Plastics Technology and MoldMaking Technology, the 3D Printing Workshop at IMTS 2024 is a chance for job shops to learn the emerging possibilities for part production via 3D printing and additive manufacturing. First introduced at IMTS 2014, this workshop has helped hundreds of manufacturing professionals expand their additive capabilities.
Formnext Chicago is an industrial additive manufacturing expo taking place April 8-10, 2025 at McCormick Place in Chicago, Illinois. Formnext Chicago is the second in a series of Formnext events in the U.S. being produced by Mesago Messe Frankfurt, AMT – The Association For Manufacturing Technology, and Gardner Business Media (our publisher).
Mulch films come in a dazzling array of colors and multi-layered structures designed to manipulate light, temperature, and moisture and repel insects. But high-tech films are expensive and have found only niche markets so far. Processors now think coextrusion, downgauging, and better field testing can put this market on a fast-growth track.
What color do strawberries like best? Experiments compare white and black mulch films for their effect on strawberry yield.(Photo: Pliant Corp.)
Highly reflective silver mulch film blinds disease-carrying white flies so they don’t see tomato plants. (Photo: David Schuster, Univ. of Florida)
Pliant’s new Black Clawson mulch-film line has such high output that only automatic roll changing can keep up. (Photo: Pliant)
Under clear mulch film, soil reaches extremely high temperatures that kill weeds. (Photo: Battenfeld Gloucester)
Test fields in Florida, Pennsylvania, and elsewhere are looking a lot like the Star Spangled Banner these days. They are bright with red, white, and blue experimental mulch films that are being tested for their impact on plant growth, crop yield, and even on the flavor and color of produce. But the main effect of colored mulch is to extend the growing season, so that domestic growers of tomatoes, melons, and eggplants can compete against the far longer growing season in Latin America.
These stripes of color on fruit and vegetable patches are signs of the widespread creative effort that processors, additive producers, and university researchers are devoting to agricultural films. Thinner gauges, higher line speeds, more complex multi-layer structures, and new pigment and additive formulations are some of the approaches being tested in the hope of persuading farmers to trade up from generic black and white films to more sophisticated—and pricier—products.
In the past decade, high-tech mulch films have been fine-tuned to manipulate light waves through different resin layers, colors, and additives. Wavelength-selective films can add days or weeks to a growing season and increase crop yields 20-30% more than conventional black mulch, which just retains moisture and warmth and keeps weeds down.
“In the Northeastern U.S. or Canada, the benefits can be very dramatic,” says Jodi Fleck-Arnold, senior product development engineer at Pliant Corp. in Schaumburg, Ill., a large producer of cast and blown mulch films. “Colored mulch films can add as much as one or two weeks to the growing season.” But they’re expensive and difficult to make, and the results have not been consistent. “One year you might get 20% greater productivity, and the next year not,” says Peter Bergholtz, owner of Ken-Bar Inc., an agricultural film dealer in Reading, Mass.
When mulch film first appeared in the early 1960s, it was a secondary product dreamed up by makers of PE diaper film because it could be made on the same cast-film lines and even on the same embossing rolls. Most mulch film is now blown, though some is cast. Either way, it is typically embossed with little bumps to give a rubbery feel and make it stretchable over the soil.
Mulch films are mostly blends of LDPE and LLDPE, though Sonoco Products in Hartsville, S.C., makes HMW-HDPE versions. Most mulch film is black for weed control, white for cooling, or black and white to do both.
Israel pioneered the first colored mulch films for light-spectrum modification to raise plant yields. “These films are how the Israelis made the desert bloom,” notes Bergholtz. Colors were first introduced in Europe a decade ago and were expected to take over 20% of the market. Instead, colored mulch film has remained largely developmental.
But that could change as results come in from new multi-year field testing of colored films. For example, masterbatch maker Ampacet Corp. is sponsoring testing of colored films at six sites, including Penn State Univ. in Rock Springs, Pa., and the Univ. of Florida in Apopka. These tests will help characterize when and where colored mulch film performs best.
Meanwhile, processors are downgauging mulch film from 3 mils to 1.5 mils or from 1-2 mils to fractional gauges. They are also busy developing new products such as “thermic” colors. Thermic films allow near-infrared light to pass through the film and into the soil, warming the soil more efficiently than does conventional IR-absorbent black film.
For example, Pliant is developing a fractional-gauge, multi-layer, cast mulch film that will be commercial next spring. The firm also plans to introduce blue and thermic-olive films next year. Sonoco is commercializing 0.4-0.5 mil black film and is developing a thermic olive-green film. Reyenvas S.A., a maker of three-layer blown mulch films in Seville, Spain, uses metallocene LLDPE to reduce film gauge from 2 mils to fractional gauge.
Processors are also raising outputs by increasing web widths and line speeds. Last spring, Pliant Corp. installed a $7-million Black Clawson coextruded mulch-film line at its Washington, Ga., plant. The line has such high output that it replaces several older lines. To take maximum advantage of that high productivity, Black Clawson designed a special automatic handling system that removes finished rolls from the winder and recores empty shafts.
Photo-selective mulch films let certain wavelengths of light through and absorb or reflect other wavelengths. These films are designed for a specific crop, time of year, climate zone, rainfall level, amount of sunlight, altitude, and exposure to insects. Photo-selective films include thermics, which pass IR heat into the soil, and selective-reflective mulches (SRM), which bounce uv light back into the plant while keeping the soil cool.
Thermic films are generally colored olive-green or brown. They can’t be black because carbon black effectively absorbs all light and then radiates up and down. Nor can thermics be white or silver, which tend to reflect all or most light.
Clear mulch films can be either thermic or just a “solarization” film that passes all light through. Either way, clear film creates extremely high temperatures underneath, which kill weeds.
SRM films can be colored or white. They incorporate clear chemical IR blockers, which don’t allow active photosynthetic radiation to pass through the film, so weed seedlings don’t grow.
Thermics are most applicable in the Northeast or during winter planting in the South. SRM films keep the soil cool and are most applicable to hot conditions in the South and mid-summer in the Northeast.
In a hot climate like Florida, with 140 kly (kilo-Langleys/year) of sunlight and 160 kly at the southern tip, a photo-selective colored mulch could make soil too warm. In Florida, growers use mulch film primarily to control weeds and hold moisture in the soil. A typical Florida film would be a monolayer white in summer to cool the soil and coextruded white over black in late summer. Both the black and white Florida films need a lot of uv stability to withstand high temperatures.
Pennsylvania, with only 120 kly of sunlight, is a good location for a thermic colored film that passes IR waves into the soil. Because the thermic color passes heat through rather than absorbing it, the film stays cooler than does a black film and needs less uv stabilizing. Therefore, film designed for Florida will survive in Pennsylvania, but not vice versa.
At high altitudes, where sunlight is more intense, films should absorb uv to avoid burning crops.
In cooler climates, mulch films are often used in greenhouses. A glass or plastic greenhouse cover can allow use of a less expensive mulch film that does not contain special additives. However, glass and plastic differ in the wavelengths they transmit. So the type of greenhouse cover must be taken into account when formulating a mulch film, says John Ven Meervenne, sales manager at Hyplast Ltd., a pioneer in colored mulch films, located in Hoogstraten, Belgium.
For reasons that are not fully understood, visible light reflected from colored films can enhance fruit and vegetable growth, strengthen plant stems, encourage fruit to grow lower down on plants, and keep insects away.
Development work at Penn State uses green mulch to encourage development of stronger plant stems to support more fruit. Red and blue mulch films apparently stimulate phytochromes, the mechanism in plant leaves that senses light in the 580-700 nm range. Different ratios of “far red” (700-740 nanometers) and “red” (580-640 nanometers) trigger different morphological responses in the plant and/or the fruit, which can help produce bigger fruit. The latest color research from the U.S. Dept. of Agriculture in Clemson, S.C., suggests that colored films can even enhance the flavor of some root vegetables like radishes.
The effect of color in mulch films is specific to particular plants. Sonoco has licensed a particular red hue patented by the USDA for its effect on tomatoes and peppers. Red mulch encourages tomato plants to produce more fruit by reflecting light in the red and far-red spectrum (580-700 nm) back onto the leaves and developing fruit.
“Green is best with peppers and melons. Red is doing well with tomatoes. Blue does well for squash and eggplant,” says Michael Orzolek, professor of vegetable crops at Penn State. He heads an Ampacet-funded color-research program. On the other hand, Prof. James Marion White at the Univ. of Florida, who also receives Ampacet funds to study color effects on plants, has found no benefit from red, green, or blue on crops in that state. Orzolek explains that colored films are most successful in cooler parts of the country. “We’re seeing responses to colors anywhere north of Virginia,” he says.
Silver is another story, however. Silver-sided mulch is popular for melons and strawberries in the Southeast, where in midsummer a red or black mulch would get so hot it could burn the fruit. Solplast S.A., a maker of three-layer blown mulch films in Lorca Murcia, Spain, sells a lot of silver/black film for melon growing in Spain and shies away from reds because of the hot climate.
Clarke Plastics in Greenwood, Va., makes a metalized silver mulch for vegetables. Highly reflective silver drives insects away, though the mechanism isn’t fully understood. It’s believed that reflecting uv “b” wavelengths makes plants invisible to pests like thrips, aphids, or white fly, so they don’t land on the plants and spread mosaic virus. But reflecting uv “b” wavelengths also makes it harder for bees to find the flowers and pollinate them. But Solplast in Spain says it found a way to create a balanced reflectance that “blinds” the white flies but not the bees. To help processors tailor silver films’ reflectivity, A. Schulman recently introduced two silver mulch-film concentrates designed to provide 35% to 55% reflectivity.
Coextruded yellow/brown mulch film is marketed in South America. Yellow side up attracts insects, while the brown side beneath retains heat. When the film heats up, it burns and kills the insects attracted to the yellow color. Farmers can also lay a band of yellow plastic down every fifth row in a field to draw the insects away from the plants. Then the farmers need spray only the yellow rows, using 80% less insecticide.
But plants and bugs aren’t the only ones affected by colors. Farm workers react too. Silver mulch can blind a tractor driver as well as a white fly, one researcher notes. Silver is also extremely hot to work near. Meanwhile, Belgium’s Hyplast found that using red film in greenhouses in Northern Europe gave workers headaches, even though the tomatoes liked it.
Creative coextrusion can also reduce film cost and add functionality. For example, Pliant recently launched a mulch film that’s black on one side and has a single wide white stripe on the other, putting the expensive TiO2 directly under the plants where it’s needed.
Penn State’s Orzolek proposes the idea of coextrusions in which the top layer or color breaks down and disappears by the end of the first planting to expose a second color underneath for a second planting. “You could have blue on top of white for spring planting. As the summer heats up, the blue layer could disappear, leaving the white layer, which keeps the soil cooler for a second planting in August,” he suggests. The white layer reflects IR rays, so new seedlings don’t get too warm under the film. Such a structure is more economical because it gets two plantings out of one installation of film.
Mulch films can also act as a barrier to contain methyl bromide, a poisonous gas injected into the soil to kill bacteria. Such soil fumigation is important for a number of crops, including tomatoes, strawberries, and tobacco. While good for crops, methyl bromide is harmful to the atmospheric ozone layer. Consequently, regulators in California and several European countries are trying to phase it out.
A high-barrier mulch film over the soil could allow farmers to use less methyl bromide. There are alternatives to methyl bromide that are less harmful to the ozone, but they are also less effective. An impermeable mulch film could improve the effectiveness of these gases by keeping them in contact with the soil longer.
In Europe, regulators have created a film classification called “VIF” (virtually impermeable film), which transmits no more than 0.2 g/hr of soil-sterilization gases. An example of VIF film is a product from Belgium’s Hyplast that is believed to be the only seven-layer, high-barrier mulch film in the world. This blown film uses double layers of mLLDPE around nylon in a structure of mLL/mLL/tie/nylon/ tie/mLL/mLL. Though it’s made in Europe, the product is marketed in the U.S. through a sister company, Klerks Plastic Products in Ridgeburg, S.C.
Processors are considering even more layers. For example, Pliant’s new high-output mulch-film line in Georgia is the first installation of Black Clawson’s new Microlayer feedblock, which can create up to 14 layers. Users multiply layers by changing pins in the feedblock to split existing layers into two. With it, Pliant has developed a new black/white film with zero light transmission and up to 60% reflectivity. The feedblock lets Pliant stack thin layers of up to four materials, increasing opacity in the black layer and reflectivity in the white, while permitting downgauging relative to traditional films. “In a film that thin, it’s hard to get zero transmission and not have the black layer show through the white,” says Pliant’s Fleck-Arnold.
Several smaller U.S. producers make three-layer barrier films of nylon/tie/PE or PE/nylon/PE. In the latter, the nylon is blended with a little adhesive. This diminishes the nylon’s barrier properties, but lets it adhere directly to PE, says William Hellmuth, senior product manager at Battenfeld Gloucester.
Extruder screws and barrels will wear over time. If you are seeing a reduction in specific rate and higher discharge temperatures, wear is the likely culprit.
Today, more than ever, granulation is an important step in the total production process. Our expert explains a few of the many common traps to avoid when thinking about granulators
Understanding how polymer melts in a single-screw extruder could help you optimize your screw design to eliminate defect-causing solid polymer fragments.
You can better visualize the melting process by “flipping” the observation point so that the barrel appears to be turning clockwise around a stationary screw.
Coverage of single-use plastics can be both misleading and demoralizing. Here are 10 tips for changing the perception of the plastics industry at your company and in your community.
Implementing a production monitoring system as the foundation of a ‘smart factory’ is about integrating people with new technology as much as it is about integrating machines and computers. Here are tips from a company that has gone through the process.
Driven by brand owner demands and new worldwide legislation, the entire supply chain is working toward the shift to circularity, with some evidence the circular economy has already begun.
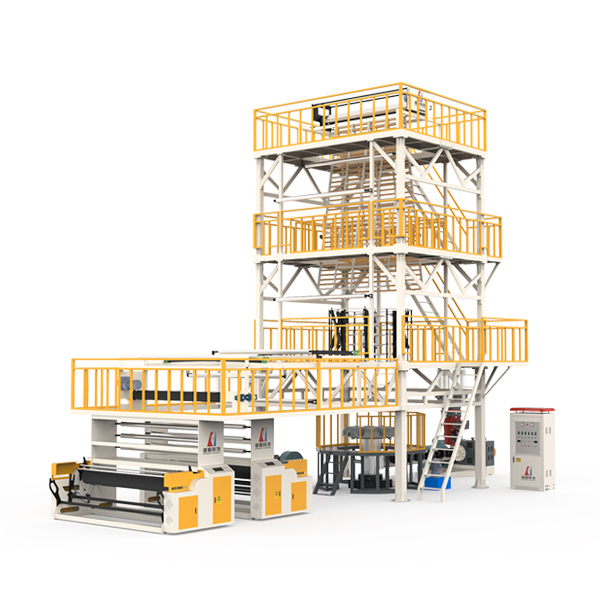
Blown Film Machine Plastics Technology covers technical and business Information for Plastics Processors in Injection Molding, Extrusion, Blow Molding, Plastic Additives, Compounding, Plastic Materials, and Resin Pricing. About Us