www.forconstructionpros.com is using a security service for protection against online attacks. The service requires full cookie support in order to view this website.
Please enable cookies on your browser and try again. MP Planetary Concrete Mixer
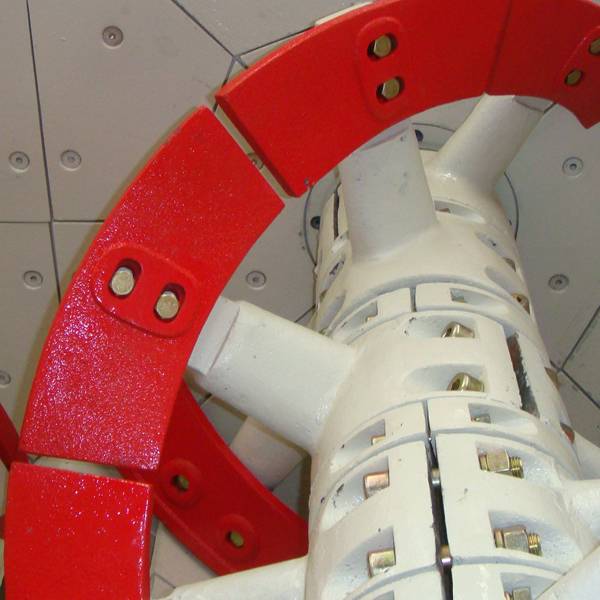
www.forconstructionpros.com is using a security service for protection against online attacks. The service requires full JavaScript support in order to view this website.
Please enable JavaScript on your browser and try again.
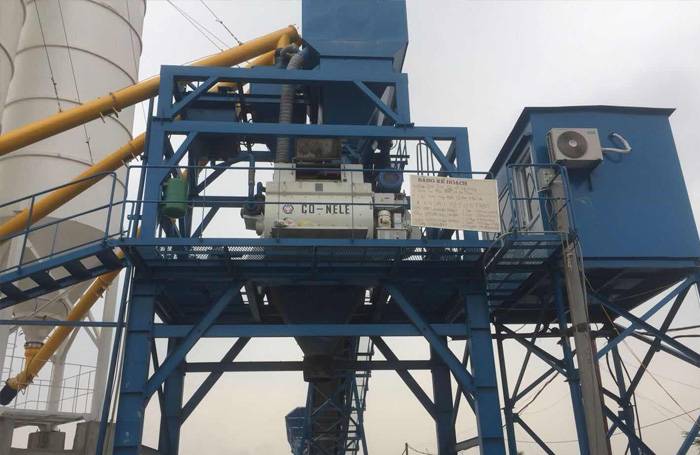
Mp1000 Planetary Concrete Mixer www.forconstructionpros.com is using a security service for protection against online attacks. This process is automatic. You will be redirected once the validation is complete.