The DSLC200 Slit Lamp Imaging Module and DEM100 Dry Eye Module can be used in combination as a dry eye platform
You must be logged in to join the discussion. Log in Eyebrow Blades Safe Mesh
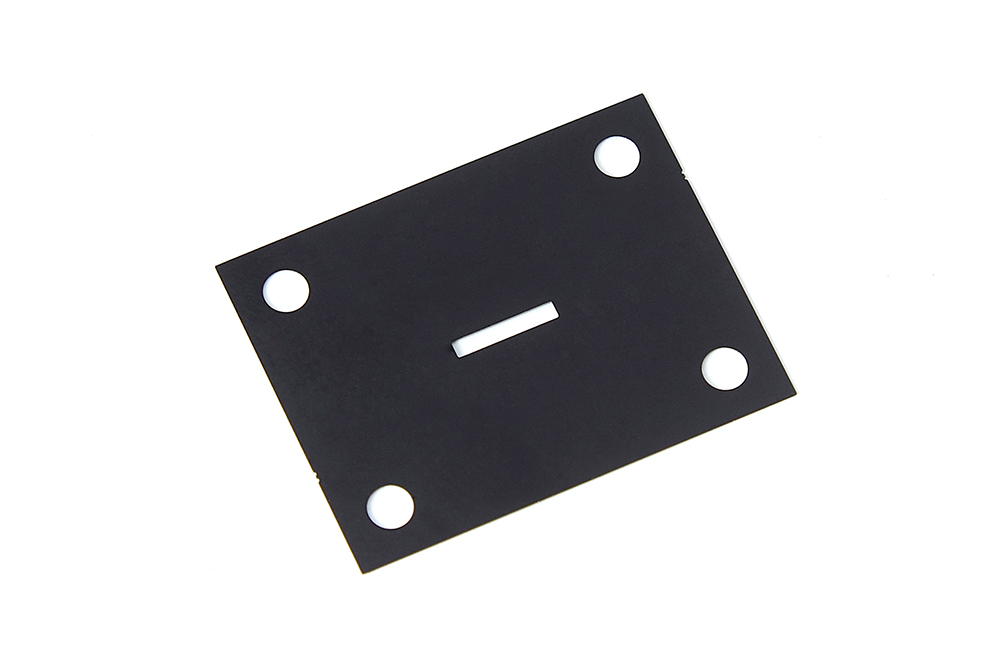
T: 020 7549 2070 E: [email protected] F: 020 7251 8315
Company registered in England and Wales - number 404790
The Association of Optometrists is authorised and regulated by the Financial Conduct Authority (FCA) - reference number 313444
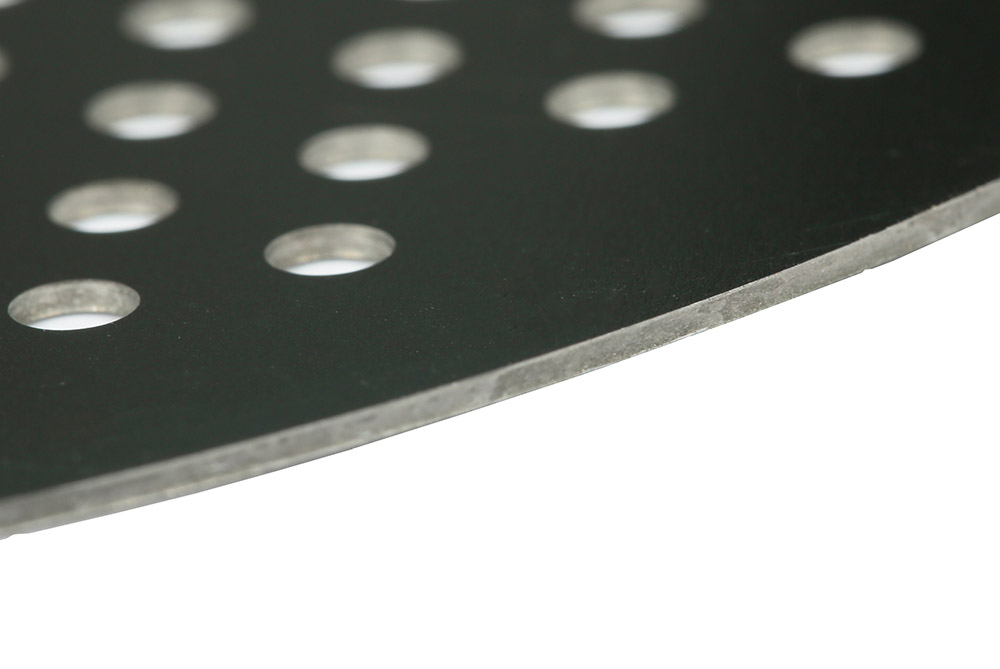
Copper Plate Etching Acid Website terms and conditions Cookie policy Privacy policy