Let's begin with CHALLENGER, an electric straddle tool representing a significant leap in coiled tubing-conveyed multizone isolation for well stimulation, selective chemical placement, and diagnostics applications.
This enables the treatment of perforations, inflow control devices (ICDs), screens, and other relevant zones to boost production, apply water control chemicals, administer scale treatments, and conduct similar operations. This fully electric-operated tool ensures seamless communication between downhole operations and surface control, enabling real-time monitoring of well data to enhance treatment effectiveness and ensure 100% placement verification. UCBV (Unlimited-cycle Bypass Valve)
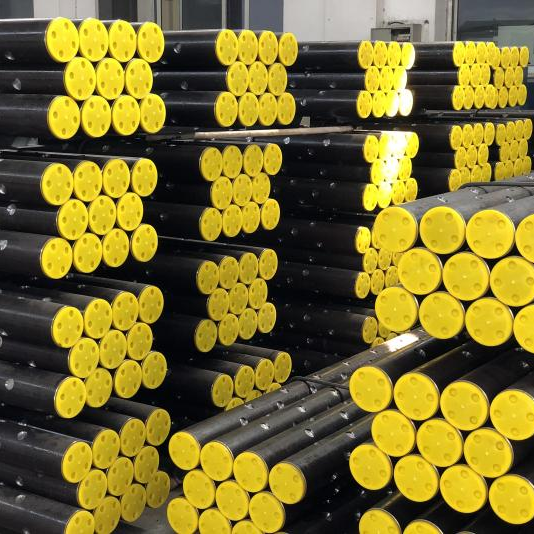
The CHALLENGER straddle tool's real-time, two-way communication system facilitates continuous monitoring of downhole pressure and temperature within the isolated zone, ensuring accurate placement verification throughout the injection treatment process. Real-time downhole sensor readouts enable on-the-fly decision-making based on actual observations, while precise depth control ensures optimal packer placement and treatment fluid distribution.
During a single operation, the CHALLENGER system was employed to acid-stimulate seven perforations within a carbonate reservoir, all accomplished in a single run. Precise depth control was imperative for setting the packers, especially given the short 2-ft blank pipe sections separating the perforation intervals. With multiset elements, multiple zones can be independently isolated and treated in a single run, streamlining operations and reducing stimulation costs by up to 90%.
Additionally, the CHALLENGER electric straddle tool offers unparalleled control and versatility. Its electrically activated packers eliminate the need for hydraulic or mechanical manipulation, minimizing wear on coiled tubing and reducing operational complexity.
In one application, CHALLENGER was used to investigate the status (open or closed) of ten ICDs. The capability to maintain the packers in a set position without requiring pumping through the coiled tubing was crucial for determining the status of the ICDs by monitoring the trapped pressure between the packers. Confirmation of the position of all ten ICDs was achieved in a single run.
Given the extended horizontal reach of the well, the CHALLENGER system was well-suited for the task, as no additional force manipulation from the surface was necessary to set and unset the packers.
As shown in Fig. 1, the tool comprises multiple modules, including two packer elements, valves, a tension/compression sub, an electronics module, and a CCPL for detecting casing collars and perforations, the integral downhole system is controlled electrically from the surface through the coiled tubing's acid-resistant internal cable. The distance between the two packers is adjustable, with fluid pumped through the coiled tubing exiting between them. Pressure and temperature sensors above, between, and below the packers continually relay real-time information to the surface.
The synergy of electric packer activation and sensor placement yields distinctive advantages over conventional systems, including:
1. Uninterrupted downhole pressure diagnostics between packers, as there's no need to pump through the coiled tubing for packer activation.
2. Packers remain set when pumping through the coiled tubing stops, enabling monitoring of pressure decline curves to gauge the reservoir's response to treatment.
3. Individual activation of one or both mechanical packers for enhanced operational flexibility.
4. Surface manipulation of the coiled tubing is unnecessary for packer setting and un-setting, extending the system's horizontal reach.
5. The sensor below the packers can detect pressure breakthroughs during treatment, often caused by inadequate cement quality around the casing.
6. Due to selective treatment fluid application and pressure monitoring during pumping, fluid volumes are typically smaller and thus more cost-effective compared to conventional systems.
Currently, the CHALLENGER system is compatible with 4.5-in. tubing/casing, and can withstand downhole ambient pressures of up to 10,000 psi and temperatures of 320°F (160°C).
DISCOVERY Conventional well testing operations involve setting up slickline and coiled tubing in different configurations based on the well conditions. This allows for tasks such as nitrogen lifting, acid stimulation via coiled tubing, gauge setting, and retrieval via slickline to be completed as needed.
DISCOVERY is a fully electric-operated coiled tubing-conveyed tool designed for well testing. Its unique design allows for buildup shut-in formation testing, well-flowing, acid stimulation, or nitrogen lift in a single-run operation.
By selectively stimulating specific zones through repositioning the e-DST tool on coiled tubing, the need for costly trips into the well is eliminated, and there's no longer a necessity to preplan flow test durations. DISCOVERY's nitrogen lifting feature facilitates testing of low bottomhole pressure wells, enhancing safety and flexibility during operations as circulation is always available above the packer. With the ability to transfer the well from dead to live status multiple times in a single run, DISCOVERY offers unprecedented control and efficiency in well testing operations.
With a multi-set packer and an electric shut-in valve, DISCOVERY not only saves significant time but also enhances test quality by allowing for instant shut-in of the well, with real-time pressure buildup curve display at the surface for continuous reservoir data evaluation. This enables early termination of unsuccessful tests or prolongation of promising ones.
The tool's superior accuracy, coupled with real-time data transmission, offers up to 60% time and cost savings and provides invaluable insights into reservoir behavior and stimulation effectiveness. Fig. 2 illustrates one such test conducted for an operator, including two shut-in and flow periods and one stimulation treatment, all in a single run.
EXPLORER Finally, let's explore EXPLORER, a high flow-thru instrumentation sub that enables real-time monitoring of downhole parameters such as pressure, temperature, CCL, gamma ray, torque, tension, compression, tool face, and inclination in any coiled tubing application. With its big-bore flow-thru capability and real-time data transmission, EXPLORER provides insights into downhole conditions, enhancing operational efficiency and reliability.
As shown in Fig 3, modular design allows for seamless integration into both conventional and electric applications. The unique design also allows for logging tools from other suppliers, offering increased flexibility and on-demand capability to meet diverse customer needs. The double flapper check valve (DFCV) is right below the connector.
In one challenging descaling application, EXPLORER was deployed to monitor the real-time downhole weight on bit and torque, allowing for an effective milling operation. Data from the real-time pressure and temperature sensors was used to select the ideal nitrified gel for lifting and optimizing the blasting operation. EXPLORER was able to detect the motors stalling due to decreased vibration. Overall, the ability to “see” downhole ensured the success of this operation and allowed the operator to regain well access and gas production.
In conclusion, TAQA's CHALLENGER, DISCOVERY, and EXPLORER technologies represent a leap in the oil and gas industry, ushering in a new era of efficiency, reliability, and cost-effectiveness. With their innovative features and advanced capabilities, these cutting-edge tools are poised to redefine the standards of well intervention, reservoir characterization, and production optimization, driving sustainable growth and maximizing returns on investment for operators worldwide.
References SPE 13184 Testing Exploration Wells by Objectives by R.S. Barnum and S. Vela.
SPE 164699 Maximizing Cost Efficiencies Through Real-Time Well Testing by A. Awara, C. Mansilla, and K. Fink.
SPE 181354 First Dual-Zone Drillstem Test With Acoustic Telemetry Using Multiple Retrievable Packers for Single-Trip Testing of Two Independent Reservoirs by G. Dolciani, S. Tiwari, O. Adewuya, and A. Mousa, et al.
PETSOC-96-774 Test, Treat, Test System Using a Concentric Coiled Tubing/DST Package by C. Hoyer, S. Fried, and D. Sask.
The Journal of Petroleum Technology, the Society of Petroleum Engineers’ flagship magazine, presents authoritative briefs and features on technology advancements in exploration and production, oil and gas industry issues, and news about SPE and its members.
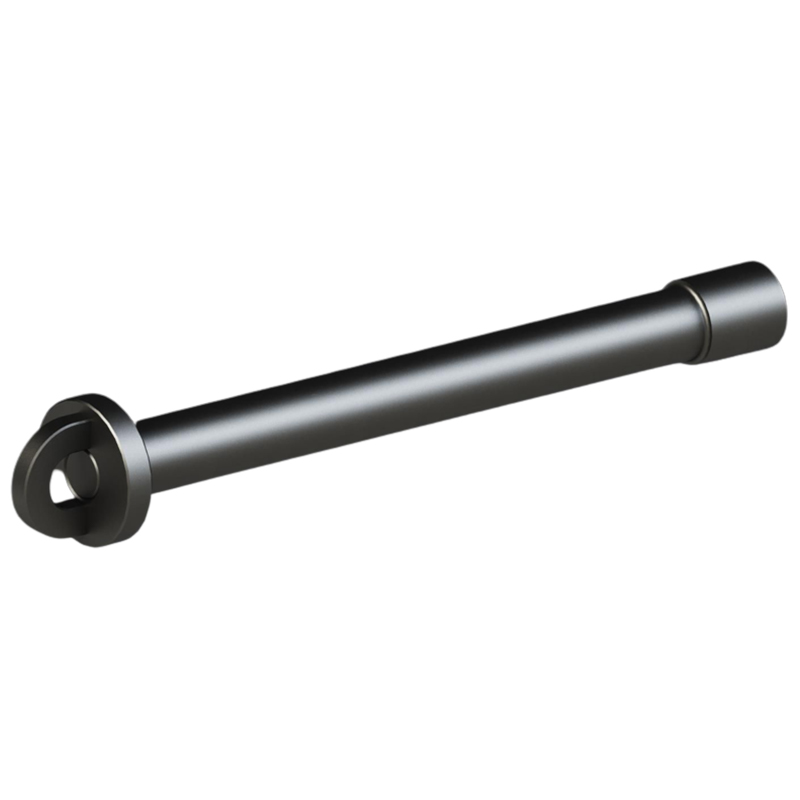
Cement Retainers ISSN: 1944-978X (Online) ISSN: 0149-2136 (Print)