Ned Galka and Abhishek Saxena of Lydall Filtration examine the growing impact of membranes in the high efficiency air filtration sector – and see what future developments may be in store.
Few mature industrial markets undergo the continued performance improvement and market growth typical in air filtration. In their most recent study, circa 2006, Frost & Sullivan projected the US Industrial Air Filtration market would grow at a compound average rate of 6.2% through 2012. Stricter environmental and safety standards led to higher performance filters in the traditional respirator and industrial air filtration markets that took hold in the second half of the 20th century. Over the last decade the growing individual knowledge and concern surrounding environmental and health issues gave rise to a host of new consumer applications. Membrane air filtration is an exciting recent development creating new opportunities through higher performing filter designs in the traditional industrial and newer consumer markets. This article explores the growing importance of membranes in high efficiency air filtration. As such it covers applications as defined by the EN1822 standard and US/MIL STD HEPA and ULPA classifications, as well as the higher efficiency classes of the EN779 and ASHRAE 52.2 (MERV ratings) standards. Eptfe Air Membrane
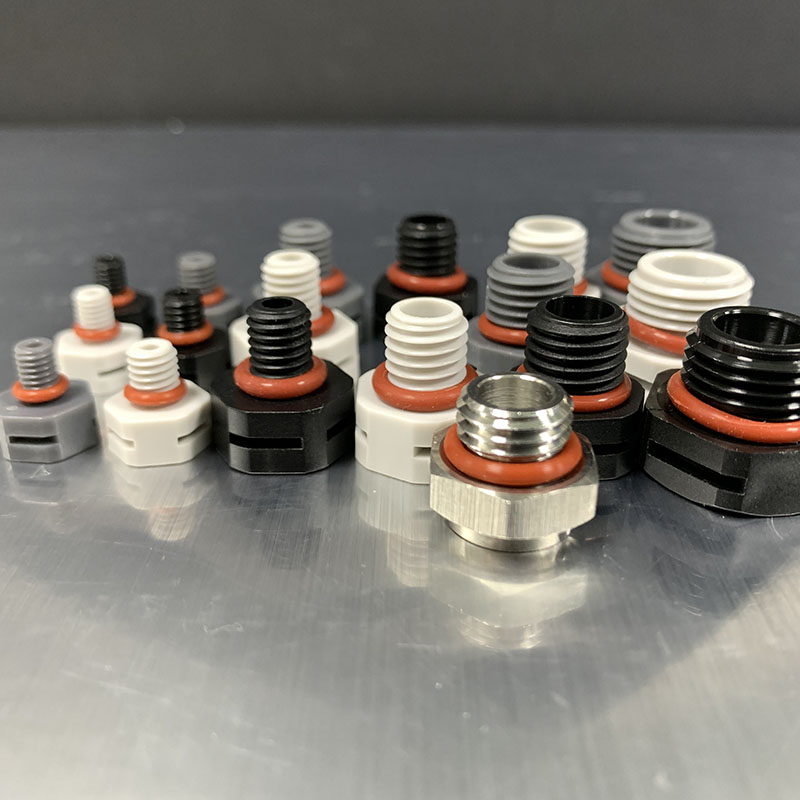
In applications where efficiency cannot be compromised, filter media that work solely via mechanical filtration mechanisms are required. The classical air filtration mechanisms of impaction, diffusion, straining and electrostatics have been well studied and documented1. Depth filters, microglass for example, operate through impaction, diffusion and straining. As these filters load with particles during use the three mechanisms are enhanced and filtration efficiency improves over time. Electrostatically charged media has gained popularity during the last decade. It is not treated in this article as its characteristics have largely limited its use to lower efficiency applications outside the scope of current membrane air filters. Electrostatic media offers the benefit of a very low initial pressure drop with high initial filtration efficiency. However, the primary mechanism works via attraction of charged particles. The media charge is often short lived. Various environmental factors such as salt and humidity, air borne oils and corrosive vapours can lead to premature discharge or a masking of the charge resulting in dramatic reduction of performance and efficiency. Hence for critical filtration applications mechanical type filtration is the preferred choice.
For many years microglass based media has been the preferred choice for high efficiency ASHRAE, HEPA and ULPA filtration. The media production processes are well established, drawing from years of experience with conventional paper formation and are scaled to the necessary volumes for an affordable end product. Filter manufacturers have developed a significant base of experience and their operations have been optimised around processing microglass. The depth, tortuous pore structure and high void volume of microglass media brings a few significant benefits; high efficiency, low pressure drop, high dust loading capacity and unsurpassed formation consistency.The performance quality of filtration media is typically characterised on the basis of resistance to air flow and the penetration of 0.3 micron particles at 5.3 cm/s. Often termed Alpha, this index is used to characterise and compare filtration media and finished filters. It is calculated as follows:Alpha = (−log10(Penetration (%) /100) × 100) / Resistance (mm H2O)where Penetration = The ratio of the number of particles downstream of the filter media to the number of particles upstream of the filter media.Resistance = (mm H2O) Pressure differential across the filter media.Improvements in Alpha have a significant benefit. Figure 1 shows the impact as new microglass filtration media designs reached an Alpha of 14, compared to the previous benchmark of 12. In typical HEPA filter media the resistance to airflow is reduced by 10%, from 30 to 27 mm H2O. This allows filter designers to improve the overall pressure drop across the finished HEPA filter, or reduce the amount of filtration media while maintaining the same filtration performance.A 2002 article in Filtration+Separation explored the life cycle cost (LCC) benefit of improving Alpha from 12 to 142. The article showed that if filter prices remained constant and maintenance and disposal costs were fixed, the improved energy consumption would result in a savings of approximately 8% over the lifecycle of the filter. The real currency savings in this example was more than 125% of the original filter cost. With the impact of rising energy costs the impact in the 2009 economy is greater still.
The use of membranes for air filtration has increased significantly over the past decade. Their unique performance, chemical/surface and physical properties are preferred in a number of air filtration applications. Expanded polytetrafluoroethylene (ePTFE) membrane filtration media has been used in air filtration products for over a decade. Recently new membrane air filters based on ultra-high molecular weight polyethylene (UPE) have been introduced into the market.
Air filters produced with ePTFE and UPE membranes exhibit exceptional efficiency and pressure drop, as measured using the Alpha index. Performance varies depending upon the exact efficiency class of the membrane. Commercially available ePTFE and UPE based products generally range between 20 and 30 (see Figure 2) when measured using Alpha. As the development of these membranes advances the potential for air filtration Alphas above 30 appears reachable.When viewed through the LCC model discussed earlier the resulting energy savings (assuming constant energy costs since 2002) is over 40% when alpha is increased from 14 to 25. The impact of higher 2009 energy costs would drive the savings even higher. ePTFE and UPE command a price premium as compared to microglass in square meters. At current price levels, the LCC savings can be realised in 3 to 5 years. But, as volumes scale further and the performance of the filter increases via higher Alphas, LCC savings will be realised with a payback in 12 to 24 months.
ePTFE and UPE membranes are suitable for a wide range of applications based upon their excellent chemical resistance (see Figure 3). ePTFE is nearly universally compatible with acids, bases, aqueous solutions and organic solvents. UPE has very good resistance but is susceptible to certain acids and organic solvents. Both types of polymers have very good bio-compatibility. UPE, for instance, is the material of choice for orthopedic implants. ePTFE and UPE membranes are used in a range of FDA approved filters and medical devices. Given their inert chemical properties these membranes have very low out-gassing.Both materials are naturally hydrophobic, eliminating the need for additional water repellency treatments. High efficiency ULPA filter media based on UPE has water repellency of greater than 1,500 mm water gauge as measured via MIL STD 282, while lower efficiency and highly permeable UPE membranes have a minimum repellency of 875 mm water gauge. ePTFE typically exhibits higher levels of water repellency at similar permeability levels.The strong carbon-fluorine bond in ePTFE provides excellent thermal resistance. Membranes based on ePTFE have a maximum use temperature of approximately 260°C. The backer and facer materials used to support and protect the expanded polymer become the limiting factor for maximum operating temperature of ePTFE air filters.The very long linear molecular chain of UPE (10 to 100 times greater than that of normal linear, or high density, polyethylene) and the absence of chemical groups give the polymer high resistance to radiation energy. UPE membranes can be sterilised using high doses of gamma radiation without significant degradation of structural or filtration properties. Figure 4 presents results from the sterilisation and testing of three different UPE air filtration membranes at baseline and two dosage levels (one time 50 kGy and two times at 50 kGy). With its simple structure of C and H based ethylene bonds UPE is an environmentally friendly “green” polymer and can be incinerated without the harmful by-products created by chemical groups within other polymers.
The unique physical properties of membranes give rise to certain advantages and disadvantages in air filters. High efficiency ePTFE membranes are very thin by their nature. A typical ePTFE membrane layer is 10 – 25 mm thick. Microglass filter media, by comparison, has a typical thickness of 300 – 400 mm. The thin network of fine filaments gives rise to the excellent alpha characteristics noted earlier, but creates dust loading, consistency and structural challenges.As they are thin and possess few layers of fibrils, ePTFE membranes filter via a surface exclusion mechanism. While highly porous they have little depth within which particles can be captured and retained. Most high efficiency air filters are dependant upon a high dust holding capacity (DHC) media for a reasonable operating lifetime. This has limited the adoption of membranes to critical applications, i.e. those where the expense of a high DHC pre-filter or where a limited operating lifetime can be justified.The other issue with very thin membranes involves their inherent physical properties. Consistency is a challenge as products become thinner. With little depth and few fibre layers the impact of manufacturing process variations is magnified. There is also little strength or stiffness. ePTFE membranes for high efficiency air filtration applications cannot be handled in freestanding form. They are stretched and concurrently laminated to a support layer to provide strength for handling. The requirements of this in-line process limit the types of supports that can be used. With the low abrasive strength of the thin ePTFE layer a protective facer is often implemented as well. The challenge of processing ePTFE filter media impacted the adoption rate. Processing these membranes on the existing installed pleaters has been challenging for some filter manufacturers.The new UPE air filtration products improve upon these issues by bridging the gap between membranes and non-wovens. These membranes vary between 40 and 150 mm thick depending upon efficiency class. The structure is unique as it is composed of a number of layers of fibrils (see Figure 5). It creates a surface loading structure for larger particles while providing depth for high capture and holding capacity of particles not filtered on the surface. The result is higher void space and loading capacity than ePTFE membranes. The new UPE membranes are 3 to 10 times thinner than microglass and are still unable to approach the inherent DHC of microglass media. The additional layers of UPE fibres provide for improved consistency in the machine and transverse directions when compared with ePTFE.An exciting aspect of the UPE air filtration membranes is its inherent structural integrity. This is a result of the combination of large structural and small filtering fibres (see Figure 6). With the high toughness and abrasive strength of UPE, a facer material is not required. UPE membranes are readily produced in roll form as stand alone films. This creates the flexibility to create composite constructions using a wide range of substrates. These support structures can be selected based upon their unique attributes. UPE/glass composites have been designed to readily process on the existing pleater infrastructure for microglass media. UPE/thin PET and UPE/high strength, high stiffness PET constructions are commercially available as well. Pleat packs of the UPE membranes on glass and thin PET substrates are shown in Figure 7. The UPE membranes, with or without backing substrate, can be directly formed into die-cut or pleated filters as well.To address the high performance and energy savings requirements in high efficiency air filtration applications, Lydall Filtration has recently commercialised Arioso™ composite air filtration media incorporating Solupor® UPE membrane technology. A range of filtration efficiencies are available incorporating a variety of functional support materials. These composites can be optimised for various applications and processing requirements.
Given their unique performance attributes membranes are finding use in a growing number of high efficiency air filtration applications. One example is in respirators and personal protective equipment. Applications where intense physical demands and risk of exposure to harmful contaminants are present demand the high efficiency/low pressure drop combination of ePTFE and UPE membrane filters. Examples are life saving vocations such as first responders or operators in industrial production in harsh environments. The premium for low breathing resistance is easily justified.Another set of common applications for membranes is consumer and industrial vacuum cleaners. There are two general types of filters in these applications: those that protect the equipment itself, i.e. the vacuum motor and those that filter the exhaust air. Vacuum cleaner filters run at very high airspeeds when compared to most air filtration applications. Face velocities of 10 to 20 cm/s are common. The ePTFE and UPE membranes provide high efficiency at these higher airspeeds and the low pressure drop enables the high airflow rates with reduced power consumption. A further advantage in vacuum cleaners is derived from the surface loading characteristics and robustness of membranes. After use, the dust cake loaded on the filter surface can be easily cleaned via shaking or water spray, and the membrane filters return to near their original pressure drop and efficiency.Membrane air filters are ideal in a number of medical and biopharmaceutical applications. The low pressure drop, ULPA efficiency and hydrophobic membrane properties are essential in surgical and hospital airway management, protecting both the patient and equipment. Those same properties are ideal for venting applications such as ostomy bags. The membrane is typically laminated to a carbon impregnated non-woven. The combined filter provides for pressure relief, an absolute barrier to liquid flow through the filter in both directions and odour reduction. Depending upon the particular requirements the membrane may be treated to enhance its oleophobic properties. In biopharmaceutical manufacturing ePTFE and UPE filters are used to vent gases produced during fermentation and cell culture. These vent filters require absolute barrier to microorganisms in aerosol and to bacteria in the event the filter is wet out. The gamma stable properties of UPE membrane provide significant benefit in single-use applications in the medical and biopharmaceutical fields.Cleanrooms and other industrial applications benefit from membranes as well. When combined with suitable support layers, membrane based filter media has very low off-gassing. This is essential in the critical microelectronic cleanroom environments. The inert ePTFE and UPE membranes are compatible with harsh industrial environments. In cleanrooms HEPA and ULPA filters provide absolute protection. They are designed to be installed for the lifetime of the cleanroom. Pre-filters are used to capture the majority of particles in the airstream and reduce the load on the membrane filters. High Alpha membrane filters lower the pressure drop leading to significant savings in energy consumption during cleanroom operation. Over the typical five year useable life of a filter the resulting savings easily outweigh the added cost for the membrane filter.
In high efficiency air filtration applications where performance is critical, microglass and membrane media (i.e. filters that work solely through mechanical means) are the preferred choices. Membrane-based air filtration media offer unique properties that make them suitable for a number of applications. This includes pulse cleaned industrial applications (bag house, airborne pollution control and gas turbine) in addition to the high efficiency applications covered in this article.The use of membranes in air filtration continued to grow over the last decade. New UPE based membranes, with their microfibrillar structure, bridge the gap between membranes and non-wovens. The inherent structural properties of UPE membranes enable flexible composites, enhanced pleat processing and new high performance filter designs.The combination of proven and new technologies promises for an exciting future in membrane air filtration. Being inert, cleanable and biocompatible, the advantages of membranes can be employed in nearly any environment. Their high efficiency at low pressure drops translates directly into energy savings, enhanced breathability and lower life cycle costs. The number of applications for membranes will continue to grow as more filter companies design in these advantages.Authors:Ned Galka (GM, Lydall Solutech)Abhishek Saxena (Development Engineer, Lydall Filtration)Contact:Geoff CrosbyMarket Manager, air filtrationLydall FiltrationEmail: gcrosby@lydall.comwww.lydall.com
(1) Dickenson, T.C, Filters and FiltrationHandbook, 4th Ed., Elsevier Science Ltd.,Oxford (1997)(2) Jan Gustavsson, Filtration & Separation,2002, vol. 39, pp. 22-26

Vent D17 Free access to this content is for qualifying individuals only. Corporate and institutional access requires an appropriate license or subscription. For more information contact institutions@markallengroup.com