This old industry standard is adapting to new applications.
Few technologies in semiconductor manufacturing have stood the test of time as steadfastly as wirebonding. This process, which involves electrically connecting semiconductor devices to their packages, has been a cornerstone of the electronics industry since the beginning of the electronics industry. Gps Module Factory
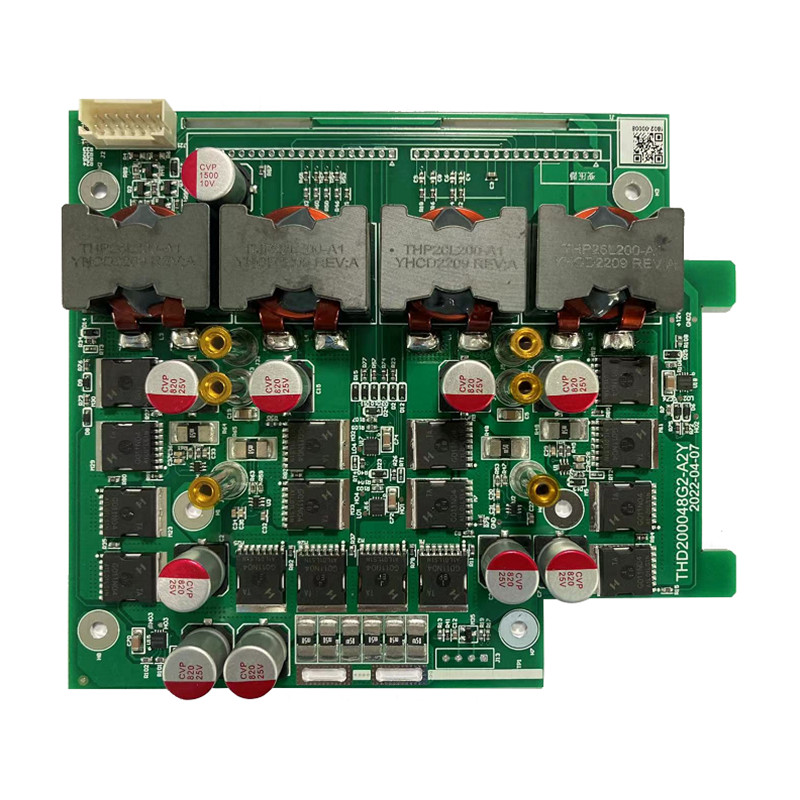
Like everything else in the semiconductor market, wirebonding technologies have changed over time to keep pace with shrinking architectures, chip complexity, and increasing density of interconnects. As transistors have shrunk and chips have become more complex, the need for finer pitch wire bonds, more reliable connections, and materials that can withstand the rigors of harsh environments has driven innovation. New materials, such as copper, copper alloys, and silver have started to replace traditional gold wires due to both cost and performance benefits.
“The major advances in wirebonding in recent decades have been in the support of cell phones and high-density electronics,” said Dick Otte, CEO of Promex Industries. “And the major advances include going to copper wire, which is a little more conductive, but a big savings over the cost of the gold. That’s been the most important change that I see in wirebonding in recent years.”
What is wirebonding? Wirebonding is a commonly used method for creating interconnections between an IC on a silicon die and its packaging, in which a thin wire is connected from a bond pad on the device to a corresponding pad (i.e. lead) on the package. This connection establishes the electrical path from the internal circuits of the chip to the external pins that connect to a printed circuit board (PCB).
The process begins by positioning a wire beneath the end of a slender bonding instrument. A precise force is exerted, pushing the wire against the electrode’s surface, leading to an initial deformation at the point of contact. This energy is derived from an ultrasonic device that produces mechanical oscillations around 60 kHz. These oscillations are channeled through the bonding instrument to the fusion zone for a duration of about 100 milliseconds.
The friction generated by the ultrasonic vibrations produces localized heating at the interface, which when combined with the pressure applied by the bonding tool, facilitates atomic diffusion across the interface. As the wire and substrate materials’ atoms come into close proximity due to the mechanical deformation and frictional effects, they begin to form intermetallic compounds. These compounds are often more stable than the parent materials and ensure a strong bond between the wire and the substrate.
There are two primary types of wire bonds, ball bonds and wedge bonds. Ball bonds are the most prevalent, constituting about 90% of all bonds, and are typically formed using a thermo-sonic bonding technique for gold and copper wiring. Wedge bonds, which are often created using ultrasonic or thermocompression techniques, are more common with aluminum alloy and gold wires and are frequently used in specific applications.
Fig. 1: A comparison of three types of wirebonding technologies. Source: NASA
Wirebonding runs out of steam at advanced nodes and in complex chips, however. As the number and density of bond pads increase, there’s limited space to ensure wires don’t touch or cause interference. This is where advanced packaging technologies, such as thermo-compression (TCP) bonding and flip-chip packaging techniques, come into play. These methods utilize solder or copper bumps to create direct connections between the chip and the substrate, eliminating the need for long wire interconnects. As a result, they offer a more compact, efficient, and high-performance solution for modern semiconductor devices, particularly those in high-frequency or high-performance applications.
“What’s really driving the transition from wirebonding to flip chip are increasingly high-speed requirements for the electronics,” says Jeff Schaefer, senior process engineer at Promex Industries. “Wires create inductance, and inductance causes electrical parameter issues for our high-speed world.”
Others agree. “As you go toward the hundreds, if not thousands of interconnects, then you’re going to start taking a hard look at whether it is still right to go with wirebonding versus moving to flip-chip,” says Frank Chen, director of applications and product management at Bruker. “But generally, most companies will still use wire bond over flip chip unless they have a high number of I/Os that push them into an array format.“
The evolution of wirebonding While there have long been predictions about the demise of wirebonding in favor of advanced packaging, wirebonding still is used to assemble more than 80% of semiconductor packages today.[1] Its proven reliability, cost-effectiveness, and well-established manufacturing processes for chips that don’t demand ultra-high densities of interconnects means it will likely be around for decades to come, as well.
According to a new report from Technavio, the wire bonder equipment market is expected to continue growing at a CAGR of 3.3% between 2022 and 2027, with the size of the market forecast to increase by $219.24 million over that period. This growth is being driven by the increasing electronics content in automotive applications and rapid growth of the OSAT industry, particularly in Asia-Pacific countries.
Gold (Au) bonding wire was the industry standard for decades, and for good reason. Its unparalleled chemical stability, corrosion resistance, and dependability made it the logical material for semiconductor packaging. That began to change as gold prices increased 478% in the decade between 2001 and 2011. Manufacturers began searching for viable alternatives that offered lower costs with similar or better conductivity.
Copper was the obvious choice, with its cost-effectiveness and superior electrical and thermal conductivity. While the price of copper jumped nearly 700% over the same period, It’s top price of $4.58 per pound is a pittance compared to the $2,100 per ounce of gold. Plus, copper’s ability to conduct the same current as gold with a smaller diameter wire, without succumbing to overheating, makes it highly attractive. Additionally, its slower reaction rate with aluminum enhances its reliability, especially under prolonged high-temperature storage conditions.
“You need to achieve a high quality and very reliable wire bond, and there’s so many factors influencing that goal,” says Per Viklund, director of IC packaging and RF product lines at Siemens EDA. “The right wire material needs to be chosen for both electrical and bonding performance, and the right metal bonding process needs to be used. What you’re after, of course, is a bond that stays and never loosens by itself.”
A key driver in the adoption of copper for wirebonding has been the growth of automotive electronics. New vehicles today can have more than a thousand ICs, and while gold is still used in some automotive applications, copper has proven more reliable over time in harsh environments and high temperatures due to its superior thermal conductivity and resilience.
“When you work with automotive power modules, you have special requirements for wirebonding, or very high current/very low inductance,” adds Viklund. “You can do some special tricks with those types of designs, but there are some physical limitations preventing you from adding an infinite number of wire bonds. It’s just not practical.”
The automotive industry, with its increasing reliance on advanced electronics for everything from engine control units to driver assistance systems, demands materials that can consistently perform under challenging conditions with defects under one part per billion, which translates to one defect per billion kilometers. Copper’s inherent properties, such as its high melting point and excellent electrical conductivity, make it particularly suited for these requirements.
“Traditionally, gold was the was the wire of choice,” says Prasad Dhond, vice president of Amkor‘s Wirebond BGA Products. “It’s easier to work with, it’s a softer material, but it has shown some issues during automotive reliability testing. And, of course, the cost is a big concern.”
The reliability issues for gold at high temperatures over an extended period of time include the development of Kirkendall voids in the joint between the wire and the aluminum pad on the die. Those voids don’t appear with copper-aluminum bonds.
However, copper isn’t without its challenges. While copper does offer advantages in terms of cost and thermal conductivity, the complexities associated with its use in wirebonding necessitate advanced equipment and specialized techniques. Some alternatives, like palladium-coated copper wire, have shown significant resistance to corrosion, albeit at a higher hardness and cost than pure copper, but still less than gold. Copper must also be worked in an oxygen-free forming gas environment (95% nitrogen and 5% hydrogen).
“You want to get a really good, strong bond between the materials,” says Chris Davies, product line manager for semiconductor products at Nordson. “But copper is known for corrosion, so you can’t use some other metals around it or you get galvanic corrosion. With gold and aluminum, you get purple plaque. Copper is the cheapest, gold is the most expensive, and aluminum is somewhere in between, but aluminum only tends to bond with specific processes and is quite tricky to bond because of the oxide layers on the surface. There are always tradeoffs.”
Automotive driving changes Until about 2010, the semiconductor industry mainly used gold wiring in wire-bond-based packages, but when gold prices spiked, the industry migrated from gold to copper wiring, enabling chipmakers to reduce their packaging costs. Automakers initially were reluctant to switch to copper due to its limitations, as well as the lack of long-term testing of copper wirebonding for critical applications in harsh environments. That has changed as copper has demonstrated to offer greater reliability in high heat and high vibration applications.
“In automotive, copper wires are the most popular now,” says Dhond. “From a reliability perspective, customers prefer it. Over the last 10 years there has been a huge shift toward copper, and almost all of our new product introductions for automotive use copper wire.”
One challenge with copper is that the heat required to achieve a bond makes it unsuitable for chips with fragile bond pads or sensitivity to high temperatures. Its stiffness also can lead to challenges in forming consistent and reliable loops, especially in fine-pitch applications. Additionally, the oxidation of copper can lead to reduced electrical performance and potential long-term reliability issues.
For these applications, a silver alloy can offer properties similar to those of gold with a cost similar to palladium-coated copper. Silver boasts superior thermal conductivity and reduced electrical resistivity compared to copper, making it an ideal choice for power electronics. Its elasticity and hardness strike a balance between gold and copper, simplifying the bonding process, and its lower melting point helps protect fragile bond pads. Silver wire bonds are also less susceptible to corrosion compared to copper.
Pure silver (Ag) is inherently soft, making it unsuitable for direct use in wirebonding applications. To address this limitation, silver is usually alloyed with palladium (Pd) and gold in varying proportions, depending on the specifications. Silver’s high reflectivity also makes it a preferred choice in LED packaging, where maximizing light output is a primary concern.
Finally, aluminum is an industry standard wirebonding material that has been used almost as long as gold and has unique properties that make it ideal for a wide range of applications. Its compatibility with aluminum pads on dies allows for bonding at room temperature with low energy levels, which helps prevent damage to sensitive devices.
Like pure silver, pure aluminum, while drawable, is relatively soft. To enhance its mechanical properties for specific applications, it is often alloyed with elements such as silicon, typically around 1%, or sometimes magnesium. These aluminum alloys result in wires with finer sizes and increased strength.
Aluminum’s high electrical and thermal conductivity make it a preferred choice in power devices and signal transmission. While it is commonly used in low-frequency applications like radio and audio equipment, power supplies, and thermostats, its versatility extends to a broad range of applications. Aluminum is bonded using wedge bonding techniques, which limits it use with very fine-pitch applications. Additionally, aluminum’s susceptibility to oxidation can make it unsuited for environments where high purity and corrosion resistance are paramount.
“There are different challenges for different materials, especially when you’re fusing one material to another,” adds Viklund. “ The wire material reliably bonds to whatever material you have on the top surface of your chip. It’s always been about how can we fuse the wire to the chip, and make sure that it stays there. And it’s pretty much been aluminum or gold and copper and various alloys. It comes down to electrical performance and bonding performance, and then at the end, cost. And you have to have the right balance between those or it won’t get adopted by your customer.”
Fig 2: Some characteristics of 0.7 mil gold, aluminum, copper and silver wire. Source: ASME
Memory Memory applications are another big driver for changes in wirebonding technology. With the introduction of multi-layer architectures in NAND flash memory, both the intricacy of wirebonding techniques and the associated testing challenges have escalated. Modern memory chips, especially in 3D NAND configurations, can comprise hundreds of layers, which are stacked in tiers.
“For some types of designs, like NAND memory, you do a lot of chip stacking and wirebonding,” says Viklund. “And the challenge is, of course, to do the wirebonding in a way where the wires are protected, because the next chip overlaps it.”
That’s where problems really begin. “Multiple layers is a killer,” adds Schaefer. “The biggest challenge when it comes to the number of wires is the increasing number of layers. We wire bond one layer, inspect, rework, wire bond the second layer, repeat, etc. And it’s virtually impossible to rework layers once you have layers on top.”
The more layers, the more difficult. “There can be a dozen or even more layers of wire bonds in today’s memory, so it can get very complex,” says Chen. “The question is, can wirebonding continue to scale? Is it feasible to keep up with the ever-increasing density? If wires are too close to each other, eventually with all the mechanical and thermal cycling that happens, it could be that the wires start moving and eventually short. The concern is how do we get enough margin between all the wires so we can handle some tolerances like that?”
Conclusion Wirebonding continues to demonstrate its adaptability and relevance in the face of evolving technological demands. As semiconductor devices have miniaturized and grown in complexity, wirebonding has innovated, incorporating new materials and refining techniques to meet the challenges of modern electronics. While alternative interconnection methods, such as flip-chip technologies, have emerged to address specific needs, wirebonding remains the dominant means of connecting chips to packages.
The industry’s shift from gold to copper, driven by both economic and performance factors, exemplifies the adaptability of wirebonding. Furthermore, the increasing complexity of memory applications, with multi-layer architectures, underscores the need for wirebonding solutions that can accommodate intricate designs without compromising reliability. As the semiconductor landscape continues to evolve, wirebonding’s legacy of resilience and innovation suggests that it will remain an integral part of the industry’s future, adapting and thriving amidst change.
References: Zhou, H.; Zhang, Y.; Cao, J.; Su, C.; Li, C.; Chang, A.; An, B. Research Progress on Bonding Wire for Microelectronic Packaging. Micromachines. 2023. ,14, 432. https://doi.org/10.3390/mi14020432
— Karen Heyman and Ed Sperling contributed to this report.
Related Reading 3D Structures Challenge Wire Bond Inspection Multiple layers of wires must be inspected layer by layer in the most cost effective way.
Name* (Note: This name will be displayed publicly)
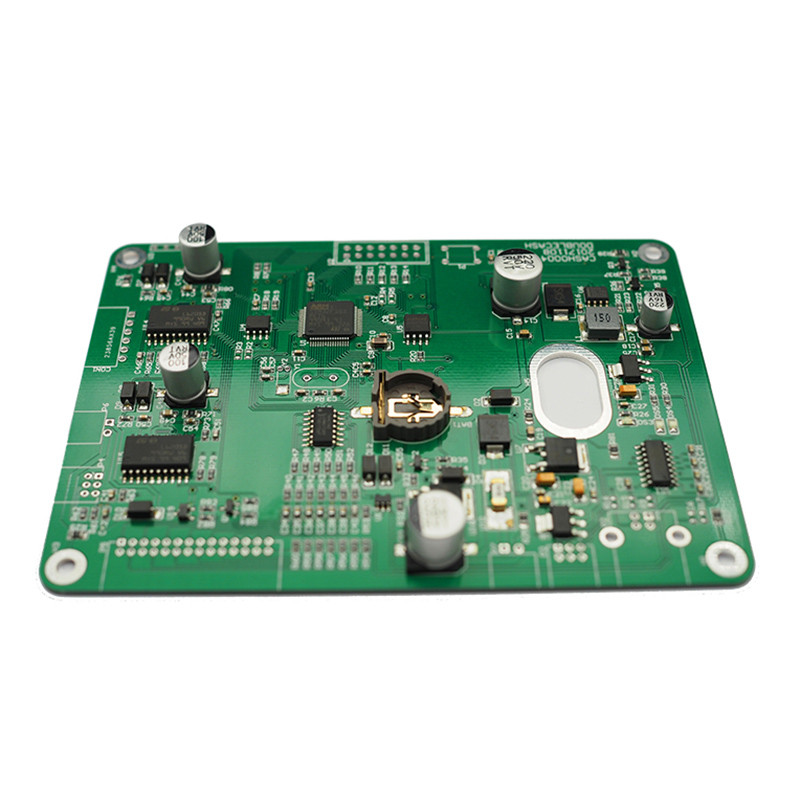
China Chip On Board Technology Email* (This will not be displayed publicly)