Ruben Garcia has been welding since he was in high school. He received his first welding certificate in 1997 for tank building under American Society of Mechanical Engineers Boiler and Pressure Vessel Code. A couple of years later he went to work for Las Cruces Utilities,
In all, Garcia has been welding for 27 years. Three years ago, after earning his certified welding inspector license, Garcia became a gas system compliance inspector for LCU. But he wasn’t done! One year ago, this passionate welder earned his certified welding educator license and is now teaching other LCU and public works associates to become welding inspectors. Foldable Plastic Soccer Training Wall Football
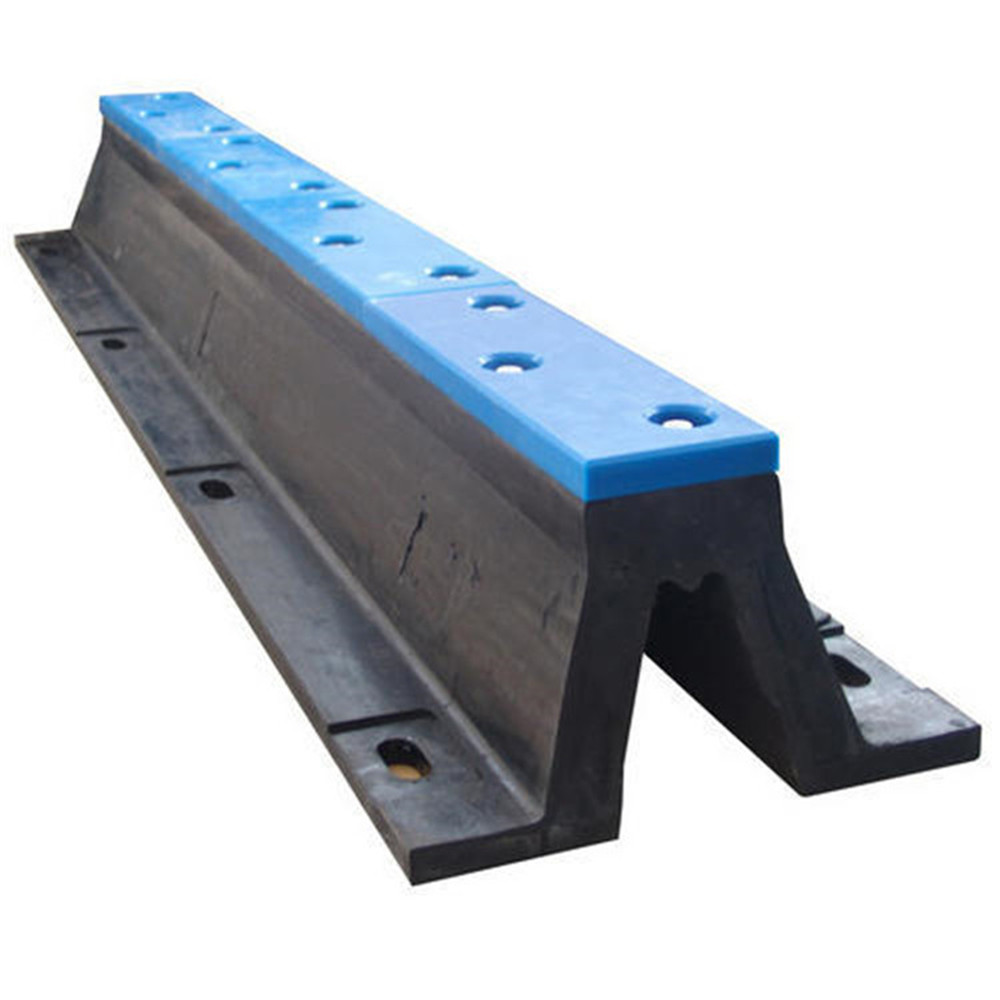
The CWE license allows Garcia to share a lifetime of experience with other welders.
“I love to weld,” he said, “but getting back behind the hood to teach others — it’s the best.”
Garcia has now trained other welders to qualify to American Petroleum Institute 1104 code and other gas inspectors to inspect steel pipe welds to API 1104 code.
In March, LCU hosted a day-long welding training for city associates. There were two sessions: In the morning, Jim Whitaker, a trainer from Albuquerque, demonstrated fusion welding on yellow polyethylene pipe used for gas service lines to homes and businesses. In the afternoon Garcia took the lead and began teaching a 32-hour Steel Pipeline Welding Inspection Course.
Some welders in the field don’t know that Garcia has been in their place.
“Many don’t realize that back in the tank building day we used to burn through 50 pounds of welding rod a day," he said. "Now, I’m also up-to-date on all the compliance and federal regulations.”
“Having Ruben teach not only our staff, but also associates of other city departments has been invaluable,” said Ramiro Pereyra Jr., LCU gas interim operations and compliance coordinator. “We have a highly trained system of welders and operators and seek to spread the knowledge we accumulate as a team to serve the greater need of the city. That ultimately serves each and every resident of Las Cruces.”
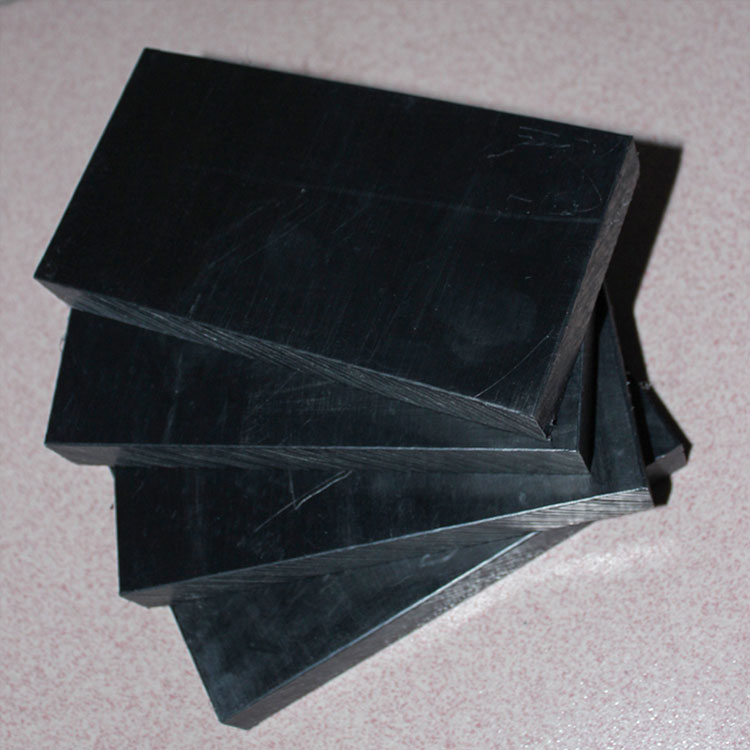
20% Borated PE Sheet You can reach Las Cruces Utilities at 528-3500 from 8 a.m. - 5 p.m. Monday through Friday. Las Cruces Utilities provides GAS – WATER – WASTEWATER – SOLID WASTE services to approximately 100,000 Las Cruces residents and businesses.