Vielen Dank für Ihren Besuch auf nature.com.Sie verwenden eine Browserversion mit eingeschränkter CSS-Unterstützung.Um das beste Erlebnis zu erzielen, empfehlen wir Ihnen, einen aktuelleren Browser zu verwenden (oder den Kompatibilitätsmodus im Internet Explorer zu deaktivieren).Um weiterhin Support zu gewährleisten, zeigen wir die Website in der Zwischenzeit ohne Stile und JavaScript an.
Scientific Reports Band 14, Artikelnummer: 3861 (2024) Diesen Artikel zitieren Mobiler Signaldetektor
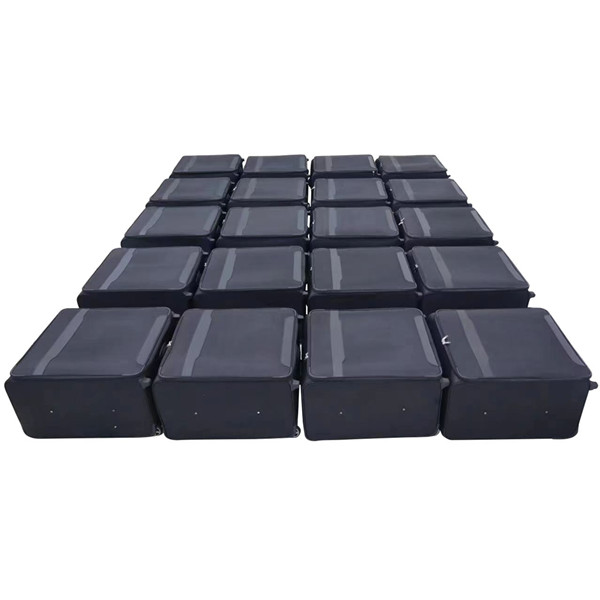
Laserstrahlgesteuerte Energieabscheidung (DED-LB) ist eine attraktive additive Fertigungstechnik, um bei Bedarf vielseitige und komplexe 3D-Strukturen herzustellen, eine Verkleidung aufzubringen oder lokale Defekte zu reparieren.Die Qualität der hergestellten Teile lässt sich jedoch nur schwer durch eine Inspektion vor der Fertigstellung beurteilen, und die Teile müssen nach der Produktion umfassend geprüft werden, um die Konformität sicherzustellen.Dadurch bleiben während des Baus auftretende kritische Mängel unentdeckt.In dieser Arbeit wird über ein neues Überwachungssystem berichtet, das drei Infrarotkameras entlang verschiedener optischer Achsen kombiniert und in der Lage ist, die Schmelzbadgeometrie und die vertikale Verschiebung während der Abscheidung zu überwachen.Durch die Kombination mehrerer Sensordaten wird ein automatisierter Algorithmus entwickelt, der in der Lage ist, die Entstehung von Strukturmerkmalen und Defekten zu erkennen.Mithilfe einer schneidenden, dünnwandigen Geometrie wird die Fähigkeit des Systems demonstriert, prozessbedingte Porosität in Proben mit engen Schnittwinkeln zu erkennen, was anhand von Mikro-CT-Beobachtungen validiert wird.Die aufgezeichneten Ergebnisse zeigen die Grundursache dieser prozessbedingten Porosität an der Schnittstelle und zeigen, dass eine fortschrittliche Werkzeugwegplanung solche Fehler beseitigen kann.Die vorgestellte Methodik zeigt den Wert der mehrachsigen Überwachung für die Identifizierung von Defekten und Strukturmerkmalen und stellt einen Fortschritt in Richtung automatisierter Erkennungs- und Warnsysteme im DED-LB dar.
Metall-Laserstrahl-gesteuerte Energieabscheidung (DED-LB/M) ist ein additives Fertigungsverfahren (AM), bei dem Metallteile durch Laserschmelzen von Ausgangsmaterial und Substrat hergestellt werden.Abhängig vom verwendeten System wird ein Laser auf ein metallisches Substrat gerichtet und bildet ein flüssiges Schmelzbad.Das Ausgangsmaterial in Pulver- oder Drahtform wird dann in den Laserpfad geleitet und erzeugt ein flüssiges Schmelzbad, das schnell zu einer Perle erstarrt.Während der Laser und das Ausgangsmaterial relativ zum Substrat bewegt werden, wird eine Metallperle abgeschieden, auf der weiter aufgebaut werden kann, um Verkleidungen zu erzeugen, Metallkomponenten zu reparieren oder ganze dreidimensionale Strukturen zu erzeugen.
DED-LB/M verbreitet sich zusammen mit anderen metallischen AM-Prozessen in Forschung und Industrie immer weiter, was zu einer raschen technologischen Entwicklung sowohl der Produktionsanlagen als auch der Anwendungen, für die es verwendet wird, führt.Da diese Entwicklung weiter voranschreitet, besteht ein zunehmender Bedarf an einer strengeren Kontrolle des AM-Prozesses, um die Wiederholbarkeit und Qualität der hergestellten Produkte sicherzustellen.Industriezweige wie die Medizin-, Energie- und Luft- und Raumfahrtbranche verwenden mittlerweile routinemäßig additiv gefertigte Komponenten im kommerziellen Maßstab und benötigen daher von Teilen eine konsistente und zuverlässige Leistung1,2,3.Metall-AM ist jedoch ein hochenergetischer Prozess mit einem hohen Maß an inhärenter Variabilität.Kleine Schwankungen des Ausgangsmaterials und seiner Lieferung, Wärmestau, Teilegeometrie oder andere Druckbedingungen können sich schnell häufen und zu Fehlern oder Schwankungen in den Teileeigenschaften führen4,5.
Das Auftreten von Fehlern und Leistungsinkonsistenzen sind anhaltende Hindernisse für die weitere Einführung von AM-Prozessen in der Industrie.Teile, die für leistungskritische Anwendungen hergestellt werden, erfordern vor der Verwendung umfangreiche Tests und Inspektionen, was den Wert des Teils erheblich erhöht.Insbesondere interne Defekte werden häufig mithilfe zerstörender Tests oder zerstörungsfreier Methoden wie der Mikro-Röntgen-Computertomographie (Mikro-CT)6 erkannt und charakterisiert.Beide Methoden können langsam und kostspielig sein, da das Vorhandensein von Mängeln erst erkannt wird, wenn das Teil fertig ist.
Eine Methode zur Minimierung des Auftretens von Fehlern und Schwankungen besteht darin, gut verstandene Verarbeitungsparameter zu verwenden. Um dies zu erleichtern, werden häufig Prozesskarten erstellt.Prozesskarten können verwendet werden, um Regime zu identifizieren und zu vermeiden, die häufig zu verschiedenen Fehlertypen führen können.Es ist beispielsweise gut dokumentiert, dass ein geringer Energieeintrag zu fehlenden Fusionsdefekten führen kann7,8.Allerdings wurde von Chen et al.9 vorgeschlagen, dass niedrigere Verfahrgeschwindigkeiten auch zu einem Mangel an Fusionsporosität führen können, indem sie eine Beschichtung aus gesinterten Partikeln erzeugen, die in zukünftigen Schichten nicht vollständig schmelzen.Ebenso kann ein hoher Energieeintrag zu Schlüssellöchern im Schmelzbad führen, die zur Bildung von Porosität führen können10.Prozesskarten sind zwar vorteilhaft, aber in der Regel zeitaufwändig zu erstellen, auf rechnerische Lösungen angewiesen und werden oft stark von der Teilegeometrie oder maschinenspezifischen Parametern beeinflusst11, noch garantieren sie tatsächlich fehlerfreie Komponenten12.
Um die Schwierigkeiten bei der Kontrolle der Teilequalität anzugehen und potenzielle Probleme in einem frühen Stadium des Bauprozesses zu erkennen, wenden sich viele Forscher und Industriebetreiber dem wachsenden Bereich der In-Prozess- oder In-situ-Überwachung zu13,14,15,16.Dies bezieht sich auf die Verwendung eines oder mehrerer Sensoren, die den additiven Fertigungsprozess während seines Ablaufs überwachen und es Benutzern ermöglichen, die Physik und Wechselwirkungen, die bei additiven Metallfertigungsprozessen auftreten, besser zu verstehen und Aufschluss darüber zu geben, wie sie mit der Fehlerbildung zusammenhängen17.Durch diesen Ansatz ist es seit kurzem möglich, die Entstehung von Defekten während des AM-Prozesses anhand aufgezeichneter Signale zu erkennen13,18, 19.
In der Literatur gibt es verschiedene Ansätze zur visionsbasierten Überwachung von DED-LB/M.Beispielsweise verwendeten Jeon et al.20 eine Mittelwellen-Infrarotkamera (IR) (3–5 μm), die koaxial mit dem optischen Strahlengang gekoppelt war, und einen Linienscanner, der 120 mm hinter der Abscheidungsdüse montiert war, um die zu messen Ablagerungsprofil der Proben aus rostfreiem Stahl (SS) 316L.Die Positionierung des Laserscanners schränkt jedoch die Komplexität und Größe der zu untersuchenden Proben ein, da sie vorwiegend linearer Natur und klein genug sind, um das notwendige Überfahren zu ermöglichen.
Es wurde auch eine außeraxiale visuelle Überwachung des Trockenen Auges durchgeführt, um sowohl die Temperatur als auch die Schichthöhe zu beobachten.Hagenlocher et al.14 nutzten eine stationäre IR-Kamera und konnten die Temperatur einer gesamten Seite eines AlMg5-Rechteckrohrs messen und so die Wärmeansammlung innerhalb des Teils analysieren.Allerdings ermöglicht diese Anordnung während des gesamten Bauprozesses nur ein einziges Sichtfeld.In Studien von Borovkov et al.21 und Lu et al.22 wurde die Höhe der abgelagerten Schichten mit außeraxialen Kameras gemessen, erforderte jedoch die Projektion eines Linienlasers auf die Spur hinter dem Schmelzbad, was die Überwachungsrichtung einschränkte.
Höhenmessungen können auch koaxial mittels optischer Kohärenztomographie (OCT)23,24 oder Lasertriangulation25,26 durchgeführt werden.Der koaxiale Charakter dieser Systeme ermöglicht Messungen der Oberflächenhöhe vom Schmelzbad aus und kann unabhängig von der Querrichtung verwendet werden.Bei diesen Systemen muss jedoch eine zusätzliche Lasersonde koaxial in den optischen Strahlengang eingekoppelt werden, die dann von einem koaxial gekoppelten Sensor überwacht wird. Falls nicht vorhanden, muss eine entsprechende Optik installiert werden.Darüber hinaus müssen die Laserwellenlänge und das Optikdesign sorgfältig überlegt werden, um Störungen durch den Prozesslaser oder die Emissionen aus der Prozesszone zu vermeiden23.Die Auswirkungen des Eintrags von Rohstoffen (insbesondere in Pulverform, was zu erheblichen Signalverzerrungen führt), des Oberflächenzustands und der Prozessfahne müssen für diese Überwachungstechniken von Fall zu Fall bewertet werden25.
Um die Vorteile sowohl außeraxialer als auch axialer Überwachungsmethoden zu maximieren, wurde in dieser Arbeit ein mehrachsiges Überwachungssystem mit einer koaxialen und zwei außeraxialen Infrarotkameras implementiert, um so viel Unabhängigkeit von der Ablagerungsrichtung wie möglich zu gewährleisten.Mit diesem Ansatz wurden mehrere geometrische Faktoren aus dem Video-Feed extrahiert, darunter häufig überwachte Signale wie Schmelzbadfläche, Länge und Breite27,28.Von größtem Interesse für diese Studie war jedoch die Verfolgung der Position des Schmelzbadschwerpunkts durch die Off-Axis-Kameras, um die Änderungen in der Oberflächenhöhe zu bestimmen und eine kontinuierliche Überwachung der Schichthöhe unabhängig von der Querrichtung zu ermöglichen.
Eine Reihe von Experimenten wurde entwickelt, um die Abscheidung von Ti6Al4V-Pulver in dünnwandigen Geometrien mit abgewinkelten Schnittpunkten zu überwachen.Diese Anordnung erfasst Ansichten des Schmelzbades von oben, von vorne und von der Seite in einem festen Beobachtungswinkel, um ein ganzheitliches Bild der Prozesszone zu liefern.Es wird gezeigt, dass die Implementierung einer mehrachsigen Beobachtung robuste Messungen und Merkmalserkennung ermöglicht.Durch die Verfolgung des Schmelzbades zwischen mehreren Kameras können geometrische Faktoren und die vertikale Höhenverschiebung während der multidirektionalen Abscheidung ohne Unterbrechung überwacht werden.Dieses System ist so konzipiert, dass es an verschiedene IR-Kameras und vorhandene Abscheidungsgeräte angepasst werden kann.Die Fähigkeit dieses Ansatzes zur Erkennung geometrischer Abweichungen durch die Überwachung der vertikalen Verschiebung wird demonstriert, indem die verschiedenen Verschiebungsmodi identifiziert werden, die auf Materialerschöpfung an der Schnittstelle und überschüssiges Material an den Laserumkehrstellen hinweisen.
Alle in dieser Studie durchgeführten Experimente wurden auf dem TRUMPF TruLaser Cell 7020 (TRUMPF SE + Co. KG, Ditzingen, Deutschland) durchgeführt.Dieses 5-Achsen-System liefert ein Pulver-Ausgangsmaterial über eine koaxiale Düse in das Schmelzbad, das von einem 1030-nm-Laser gebildet wird, der von einem TRUMPF TruDisk 3001-Lasermodul versorgt wird.Dieser Festkörper-Yb:YAG-Laser liefert einen kontinuierlichen Strahl mit Gauß-Verteilung und einer Leistung von 80–3000 W;Der Strahl wird über Glasfaserkabel transportiert.In allen Experimenten wurde die Koaxialdüse mit einem Abstand von 12 mm verwendet.
Das verwendete Ausgangspulver ist ASTM Grade 5 Ti6Al4V, geliefert von ECKART TLS GmbH (Hartenstein, Deutschland).Die Partikel werden durch Gaszerstäubung in Argon hergestellt und als kugelförmig mit einer Größenverteilung von 45–90 μm klassifiziert.Die Proben wurden auf sandgestrahlten Ti6Al4V-Substraten mit einer Mindestdicke von 10 mm abgeschieden.Weitere wichtige verwendete experimentelle Parameter sind in Tabelle 1 aufgeführt.
Für diese Studie wurde eine Reihe von neun sich kreuzenden dünnwandigen Geometrien in drei verschiedenen Designhöhen, 5, 10 und 20 mm, mit Schnittwinkeln von 90°, 60° und 30° erstellt, um gängige geometrische Formen darzustellen.Ein Beispiel dieser Geometrie ist in Abb. 1 dargestellt. Der Werkzeugweg der Maschine wurde aus einem CAD-Modell mit der Slicing-Software DCAM von SKM Informatik (Schwerin, Deutschland) generiert, was zu einer abwechselnden Scanrichtung für jede Schicht führte, während die Start- und Endpunkte fortschritten um den Umfang des Gebäudes herum.Aufgrund der Beschleunigung und Verzögerung des Lasers am Startpunkt kann der resultierende Schmelzfluss zur Bildung einer Ausbeulung führen, wenn jede Schicht an derselben Stelle beginnt29,30.Daher mildert die gewählte Scan-Strategie den kumulativen Effekt eines konstanten Startpunkts und einer konstanten Verfahrrichtung.Weitere drei Proben wurden später mit einem modifizierten Werkzeugweg hergestellt, eines an jedem Schnittwinkel, und werden im Abschnitt „Kameraeinschränkungen“ ausführlicher besprochen.
CAD-Modell, das die Geometrie von sich kreuzenden Wandproben zeigt, wobei der Schnittwinkel 30° und die Entwurfshöhe 20 mm beträgt.Zur Veranschaulichung der Abscheidungsstrategie werden die Scanpfade für die ersten beiden Schichten (Verrundungen nicht dargestellt) dargestellt.Die Koordinatenachsen für das Laserauftragssystem werden ebenfalls angezeigt.Die Orte von Interesse werden hier mit Nummern hervorgehoben, die Folgendes bezeichnen: 1. Wall-Mittelregionen;2. Wandwendepunkte;3. Wandanschluss.
Es wird angenommen, dass der Entwurf drei Hauptregionen mit unterschiedlichen thermischen Vorgeschichten schaffen wird, die unterschiedliche geometrische Merkmale erzeugen.Diese Aufbauteile sind: (1) die Mittelbereiche der dünnen Wände, in denen sich der Laser geradlinig bewegt und von der Abscheidung im stationären Modus ausgegangen werden kann;(2) die Enden jeder Wand, an denen der Laser langsamer werden und sich umdrehen muss, bevor er mit der linearen Verfolgung des Designs fortfahren kann, was zu einer längeren Verweilzeit an diesen Stellen führt;und (3) der Verbindungsbereich, in dem sich die Wände schneiden.Der Wandübergang ist von besonderem Interesse, da der Laser diesen Bereich dreimal durchläuft, während er jede andere Stelle im Teil zweimal durchläuft.
Die Beispielbezeichnungen haben die Form IW1, wobei die Buchstaben für „Intersecting Wall“ stehen und die Zahl sich auf die Entwurfshöhe und den Schnittwinkel bezieht.Sie sind in Tabelle 2 aufgeführt.
Der Aufbauprozess wird mit drei Infrarotkameras überwacht, die am Abscheidekopf der TRUMPF angebracht waren und sich beim Abscheiden mitbewegten.Der Versuchsaufbau umfasst die Wärmebildkameras Optris PI 05M und Optris PI 1M (Optris GmbH, Berlin, Deutschland), die auf einer seitlich montierten Halterung positioniert sind, und eine koaxiale Infrarot-Bildkamera, Control for Laser Additive Manufacturing with Infrarot (CLAMIR), geliefert von NIT ( New Infrarot Technologies, SL, Madrid, Spanien)).Die Anordnung dieser Kameras ist in Abb. 2a dargestellt, mit Beispielen der von den Kameras aufgenommenen Bilder in Abb. 2b–d.Diese Anordnung ermöglicht es, dass eine außeraxiale Kamera das Längsprofil des Schmelzbads überwacht, während die andere das Vorderprofil überwacht, oder umgekehrt.
Versuchsaufbau und Beispielbilder von der Herstellung einer 30°-Schnittwandprobe.(a) Installation von Wärmekameras am TRUMPF-Abscheidungskopf mit überlagerten Maschinenkoordinatenachsen.Die Hauptkomponenten sind nummeriert: (1) CLAMIR-Kamera mit Wasserkühlung und angeschlossenem Datenkabel.(2) Koaxialer Montageanschluss für CLAMIR-Kamera.(3) Wärmebildkamera Optris PI 05M, mit Datenkabel, im 55°-Winkel zur k-Achse.Befestigung über seitlich angebrachte Halterung.(4) Koaxiale Pulverdüse für DED-LB/M.(5) Wärmebildkamera Optris PI 1M, mit Datenkabel, im 55°-Winkel zur k-Achse.Befestigung über rückseitig angebrachte Halterung.(6) Stabilisierungsstrebe für seitliche Halterung.(b) Graustufenbild, aufgenommen mit der CLAMIR-Kamera.(c) Thermografisches Bild, aufgenommen mit der Kamera Optris PI 1M.(d) Thermografisches Bild, aufgenommen mit der Kamera Optris PI 05M.
Zur Überwachung geometrischer Eigenschaften muss die Perspektive jeder Kamera berücksichtigt werden.Die Koaxialkamera erfährt keine perspektivische Verzerrung und erfordert keine Korrekturfaktoren.Allerdings müssen die beiden Off-Axis-Kameras einer Perspektivkorrektur unterzogen werden, um die vertikale Verschiebung zu messen und das Pixel-Seitenverhältnis zu korrigieren.Wie im Abschnitt „Datenverarbeitung“ weiter erläutert wird, werden Messungen durch Schmelzbadverfolgung erhalten.Da die Abscheidungsoptik während der gesamten Probenherstellung die gleiche vertikale Ausrichtung beibehält, kann davon ausgegangen werden, dass das Schmelzbad um die vertikale Achse zentriert ist.Daher können Änderungen der Bildkoordinaten des Schmelzbadschwerpunkts auf der y-Achse des Bildes als vertikale Verschiebung von der ursprünglichen Fokusebene interpretiert werden.Punkte in der vertikalen Ebene werden in die Bildebene projiziert, wie in Abb. 3 gezeigt, und die tatsächlichen Abstände in der vertikalen Ebene oder die k-Achse des Abscheidungssystems gemäß Abb. 2a können mithilfe der trigonometrischen Beziehung berechnet werden , siehe Gl.(1),
Dabei ist \({R}_{v}\) der tatsächliche Abstand zwischen zwei Punkten in der vertikalen Ebene, \({y}_{v}\) der Abstand auf der y-Achse des Bildes und \(\theta\ ) ist der Winkel zwischen der optischen Achse der Kamera und der vertikalen Achse.Ebenso kann der Skalierungsfaktor der Pixel auf der y-Achse des Bildes mithilfe von Gl. bestimmt werden.(2),
Dabei ist \({R}_{h}\) der tatsächliche Abstand zwischen zwei Punkten in der horizontalen Ebene (der i-j-Ebene des Ablagerungssystems) und \({y}_{h}\) der Abstand in der y-Achse des Bildes.
Projektion vertikaler und horizontaler Ebenen auf die Bildebene für Off-Axis-Kameras.Die realen Punkte a und c werden auf die Bildpunkte b bzw. d projiziert, vorausgesetzt, dass eine Parallelstrahlannahme getroffen werden kann.Der Brennpunkt des Lasers wird als Ursprung O angenommen, der auf Punkt O' in der Bildebene abgebildet wird.Daher werden die tatsächlichen Abstände in der vertikalen Ebene (Rv) und der horizontalen Ebene (Rh) auf Abstände in der Bildebene (yv bzw. yh) abgebildet.Da sich die optische Achse des Lasers nicht ändert, kann davon ausgegangen werden, dass das Schmelzbad um die vertikale Achse zentriert ist, und Änderungen an der y-Achse des Schmelzbadschwerpunkts beziehen sich auf Änderungen der vertikalen Verschiebung, während die Ausdehnung des Schmelzbads in Die Y-Achse des Bildes kann mithilfe der Gleichung für den tatsächlichen Abstand in der horizontalen Ebene korrigiert werden.
Die koaxiale Überwachung des Schmelzbades erfolgt mit dem bildgebenden Kameramodul CLAMIR des NIT.Diese Kamera wird in den optischen Strahlengang des TRUMPF-Abscheidungskopfs über der Kollimationslinse eingekoppelt, wie in Abb. 2a, Position 1 dargestellt. CLAMIR ist eine Mittelwellen-Infrarotkamera, die Wellenlängen im Spektrum von 1–5 μm auf einem 64 × 64-Zoll-Objektiv erfasst Pixel-PbSe-Detektor mit einer maximalen Bildrate von 1 kHz.Ein Langpassfilter, ThorLabs (ThorLabs Inc., Newton, USA) FELH1100, ist installiert, um alle Wellenlängen unter 1100 nm zu blockieren und den Detektor vor Laserreflexionen zu schützen.Die Bilder wurden mit einer Frequenz von 1 kHz aufgenommen und eine Pixelauflösung von 9,0 px/mm (111 μm/px) erreicht.Während die CLAMIR-Kamera verwendet werden könnte, um die Laserleistung automatisch anzupassen, um eine Zielbreite eines Schmelzbades zu erreichen, wurde diese Funktion in der vorliegenden Studie aufgrund von Inkonsistenzen in den erhaltenen Ergebnissen nicht verwendet, und stattdessen wurden die generierten Sensordaten für 2000 aufgezeichnet -Hausbearbeitung und Auswertung.
Die Kamera ist mit einer Auto-Shutter-Funktion ausgestattet, um thermische Drift auf dem Sensor zu verhindern, die zu einer zunehmenden wahrgenommenen Intensität für alle Pixel führen würde.Während der Zeitspanne, in der der Verschluss aktiv ist, etwa 300 ms, ist das aufgezeichnete Bild leer, aber alle berechneten Metriken in der nativen Software werden als letzte aktive Instanz beibehalten.Der automatische Verschluss wurde während der Überwachung so eingestellt, dass er alle 30 Sekunden aktiviert wird, da interne Tests zeigten, dass innerhalb dieses Zeitraums nur eine minimale thermische Drift auftrat.Weitere Informationen können dem CLAMIR-Datenblatt31 entnommen werden.
Die erste Off-Axis-Kamera ist die Optris PI 1M-Kamera, die Wellenlängen im Bereich von 0,85–1,1 μm überwacht und einen maximalen gemessenen Temperaturbereich von 450–1800 °C aufweist.In dieser Studie liegt der Messbereich bei 575–1800 °C, was den Schmelzbereich von Ti6Al4V, also 1600–1650 °C, abdeckt32.In dieser Kamera ist ein Kerbfilter, ThorLabs NF1030-45, installiert, um Wellenlängen von 1030 ± 2 nm auszuschließen, mit einer Halbwertsbreite von 45 nm für den Sperrbereich.Dadurch wird verhindert, dass reflektierte Laserwellenlängen den Detektor beschädigen oder die Temperaturschätzung beeinflussen.Zur Befestigung der Kamera und zur Sicherstellung der Wiederholbarkeit der Experimente wurde eine eigens entwickelte und hergestellte Halterung verwendet, siehe Abb. 2a, Position 5. Der Betrachtungswinkel wurde auf 55° von der vertikalen Achse eingestellt und ergab eine Brennweite von 0,3 m .Die Bilder wurden mit einer Frequenz von 80 Hz und einer optischen Auflösung von 382 × 288 Pixel aufgenommen. Es wurde eine Pixelauflösung von 11,7 Pixel/mm (85,7 μm/Pixel) erreicht.Die Optris 1M-Kamera wurde auf die j-Achse des Abscheidungssystems ausgerichtet und betrachtete die sich überschneidenden Geometrien in positiver j-Richtung, senkrecht zur Rückseite der langen Wand.Weitere Informationen können dem Optris PI 1M Datenblatt33 entnommen werden.
Die zweite Off-Axis-Kamera ist die Optris PI 05M-Wärmebildkamera, die mit einer zweiten Halterung seitlich am Abscheidungskopf installiert wird, 90° von der PI 1M-Kamera in der horizontalen Ebene entfernt, wie in Abb. 2a, Position 3 dargestellt Der Neigungswinkel dieser Kamera war ebenfalls auf 55° zur Vertikalen eingestellt und hatte eine Brennweite von 0,2 m.Die 05M-Kamera überwacht Wellenlängen im Bereich von 500–540 nm und beobachtet einen Temperaturbereich von 950–2450 °C.Dieses kürzere Wellenlängenband macht auch die Notwendigkeit eines optischen Filters zum Schutz vor dem Laserlicht überflüssig.Die Bilder wurden mit einer Frequenz von 80 Hz und einer optischen Auflösung von 382 × 288 Pixel aufgenommen. Es wurde eine Pixelauflösung von 8,3 Pixel/mm (120 μm/Pixel) erreicht.Die Optris 05M-Kamera wurde gemäß Abb. 2a auf die i-Achse des Abscheidungssystems ausgerichtet und betrachtete die Schnittgeometrien in positiver i-Richtung, wobei sie auf die Innenseite des Schnittwinkels blickte.Weitere Informationen können dem Optris PI 05M Datenblatt34 entnommen werden.
Ähnlich wie die CLAMIR-Kamera sind beide Optris-Kameras mit einer Funktion zur Verhinderung thermischer Drift ausgestattet, die als „Flag“ bezeichnet wird.Hierbei handelt es sich wieder um eine physikalische Barriere, die kurzzeitig über der Optik geschlossen wird, um den Referenzpunkt des Detektors zurückzusetzen.Die Kamera aktiviert die Markierung automatisch, wenn die Software feststellt, dass sich die gemessenen Pixeltemperaturen zu stark verschoben haben.Es wurde eine Mindestzeit von 12 s zwischen Flag-Aktivierungen implementiert.Ein bemerkenswerter Unterschied besteht darin, dass das während der Flag-Aktivierung aufgezeichnete Bild statisch bleibt, im Gegensatz zur CLAMIR-Kamera, bei der das aufgezeichnete Bild während dieser Zeit leer bleibt.
Durch die Kombination der Perspektiven aller drei Kameras kann eine konstante Sicht auf das Schmelzbad gewährleistet werden, wobei Unterbrechungen durch automatische Kameraverschlüsse oder eine Selbstverdeckung des Schmelzbads durch Kanten der gefertigten Teile berücksichtigt werden.Darüber hinaus gewinnt die Erkennung von Merkmalen in den Daten an Bedeutung, wenn die Validierung mit mehreren Kameras statt mit einer einzelnen Kamera erfolgt, die aufgrund der Spritzer und der variablen Beschaffenheit des Schmelzbads selbst verrauschten Signalen ausgesetzt sein kann.
Die fertigen Proben wurden aus dem Hauptsubstrat herausgeschnitten und in ihrer Gesamtheit mittels Mikro-CT untersucht, um interne Merkmale aufzudecken.Zur Abbildung der Proben wurde ein Zeiss Pixelgröße von ca. 18–19 μm, abhängig von der jeweiligen Probe.
Topografische Bilder wurden von einigen Proben mit einem 3D-Digitalmikroskop Keyence VHX-5000 (KEYENCE CORPORATION OF AMERICA, Itasca, USA) aufgenommen.Topografische Bilder werden über ein vertikales Stitching-Verfahren erfasst, bei dem Bilder über einen bekannten vertikalen Bereich erfasst und zu einer Höhenkarte kombiniert werden.
Ein benutzerdefinierter Datenverarbeitungsalgorithmus wurde entworfen und in der MATLAB-Software implementiert, um Änderungen der Position, Form und Größe des Schmelzbads anhand der Ausgabe von drei Sensoren zu verfolgen.
Zu den aus den Videoaufzeichnungen extrahierten Funktionen gehören:
Die Position des Schmelzbadschwerpunkts in Bezug auf die X- und Y-Koordinaten des Bildes.
Der äquivalente Bereich des Schmelzbades im Bildrahmen (korrigiert um perspektivische Verzerrung).
Die Exzentrizität einer an das Schmelzbadobjekt angepassten Ellipse.
Ausrichtung der angepassten Hauptachse der Ellipse in Bezug auf die x-Achse des Bildes
Die Abmessung des Schmelzbades entlang der x-Achse des Rahmens für beide außeraxialen Kameras und die Abmessung sowohl auf der x- als auch auf der y-Achse der koaxialen CLAMIR-Kamera.
Die Position des Schmelzbadschwerpunkts wurde verwendet, um die vertikale Verschiebung der aktuellen Ablagerungsebene im Verhältnis zum vordefinierten Arbeitsabstand zu extrapolieren.Wie in Abb. 4 dargestellt, ist ein anfänglicher Arbeitsabstand \({w}_{0}\) in den Abscheidungspfad programmiert.Bei mehrschichtigen Abscheidungen ist die Düse so programmiert, dass sie sich für jede nachfolgende Schicht um einen festgelegten Schritt anhebt.Wenn das Höheninkrement von der Höhe der aufgetragenen Raupe abweicht, weicht die Oberfläche des Teils von der ursprünglichen Arbeitsebene ab und stellt einen neuen Arbeitsabstand dar, \({w}_{pos}\) oder \({w}_{neg} \) .In beiden Szenarien verringert sich die Erfassungseffizienz.Im Fall von \({w}_{neg}\) kann dies zu einer weiter verringerten Ablagerungshöhe und einem Run-Away-Effekt mit einer zunehmend negativen Verschiebung von der anfänglichen Arbeitsebene führen35.Im Fall von \({w}_{pos}\) kann jedoch die verringerte Ablagerungshöhe (aufgrund der verringerten Einfangeffizienz und/oder des Überschmelzens) verhindern, dass das Teil zu groß wird und die Ablagerung beeinträchtigt Düse.Dies führt zu einem stabilen Überbauzustand und ist oft ein wünschenswerter Bauzustand für den Betrieb35.
Abweichungen in der Werkstückoberfläche führen zu positiven und negativen Abweichungen vom idealen Arbeitsabstand.
Bei der Überwachung mit einer Off-Axis-Kamera kann die Verschiebung des Arbeitsabstands vom anfänglichen Arbeitsabstand mithilfe von Gl. berechnet werden.(1), wenn davon ausgegangen wird, dass Änderungen in der Lage des Schmelzbadschwerpunkts Verschiebungen in der Werkstückoberfläche entsprechen.Es wird angenommen, dass der Schwerpunkt des Schmelzbades vertikal bei jeder aufeinanderfolgenden Schicht um die Dicke der abgeschiedenen Schicht zunimmt und daher eine Methode zur Verfolgung der Änderung der Schichthöhe in Bezug auf die Brennebene bietet, die als durchschnittliche Vertikale definiert ist Position der ersten Schicht.
Im Falle der Schmelzbadabmessungen wird in den Optris-Kameras aufgrund sowohl perspektivischer Verzerrung als auch möglicher Selbstinterferenzen entlang der y-Achse nur die x-Achse berücksichtigt, aber beides kann extrahiert werden.Darüber hinaus bedeutet die gleichzeitige Messung durch beide Optris-Kameras, dass die unverzerrte Länge des Schmelzbades mit einer Kamera gemessen werden kann, während die zweite die unverzerrte Breite misst.In dieser Studie wurden jedoch nur die Positionsmerkmale untersucht, um geometrische Abweichungen vom Teiledesign zu erkennen.
Der zum Extrahieren der oben genannten Merkmale verwendete Videoverarbeitungsalgorithmus ist im Flussdiagramm in Abb. 5 zusammengefasst. In zukünftigen Studien könnten auch zusätzliche geometrische Merkmale durch Modifikation des Algorithmus extrahiert werden.Die Signalverarbeitung wurde nach Abschluss des Druckvorgangs durchgeführt.Es besteht jedoch die Möglichkeit, diesen Vorgang zu automatisieren und in Echtzeit durchzuführen, um eine mögliche Regelung im geschlossenen Regelkreis in der Zukunft zu ermöglichen.
Flussdiagramm, das den Algorithmus beschreibt, der zur Verarbeitung der Videodaten zu vektorisierten Schmelzpoolmetriken verwendet wird.*Wenn sich ein Frame in einer langen Folge leerer Frames befindet (normalerweise > 0,5 s entsprechend), deutet dies darauf hin, dass der Laser zur Zwischenschichtkühlung ausgeschaltet war.Dieser Schritt war notwendig, da die Übertragung der koaxialen Kamera durch die Einstellung „Auto-Shutter“ unterbrochen wurde und diese Intervallzeit nicht immer klar definiert war.
Um den Schwellenwert für jede der Kameradateien zu bestimmen, wurde ein Graustufen-Intensitätsprofil aus der Längsachse des Schmelzbades extrahiert.Der Schwanz des Schmelzbades weist eine charakteristische Abkühlungskurve auf, unterbrochen von einer flacheren „Schulter“ mit einem im Vergleich zum Rest der Kurve verringerten Wärmegradienten.Der untere Scheitelpunkt dieser Schulter wird als Solidustemperatur, 1600 °C für Ti6Al4V32, angenommen und zur Binarisierung der Rahmen verwendet.Eine ausführlichere Erläuterung dieses Prozesses finden Sie im Ergänzenden Hinweis: Bildverarbeitungsalgorithmus.
Nach der Binärisierung wurden die Bilder zugeschnitten und eine ROI-Maske (Region of Interest) angewendet, um jegliche überflüssige Eingabe zu eliminieren.Das größte Objekt, von der Softwareschnittstelle als „Partikel“ bezeichnet, wird mithilfe der MALAB-Funktion „bwpropfilt“ ausgewählt, um das flächenmäßig größte Objekt auszuwählen.Dadurch wird das Schmelzbad von weiteren Spritzern isoliert.Hier wird davon ausgegangen, dass das größte in einem Rahmen vorhandene Partikel das persistente Schmelzbad ist, was in den meisten Fällen zutrifft.Aufgrund der sporadischen Natur von Spritzerpartikeln kann es jedoch vorkommen, dass ein Partikel auf eine der außeraxialen Kameras zufliegt und im Sichtfeld vorübergehend größer wird als das Schmelzbad.Dies führt zu Rauschen bei der Aufnahme einer einzelnen Kamera, wird jedoch durch die Verfügbarkeit mehrerer Sensoren überwunden, wodurch das erzielte Ergebnis verbessert wird.
Sobald der Inhalt der Frames auf das größte Einzelpartikel reduziert wurde, werden die geometrischen Eigenschaften des Schmelzbads mithilfe der Funktion „regionprops“ analysiert.Mit dieser Funktion werden der Schwerpunkt, der Begrenzungsrahmen und die Fläche zurückgegeben.Darüber hinaus wird eine Ellipse an das Partikel angepasst und die Exzentrizität, die Ausrichtung (Winkel zwischen der Hauptachse und der horizontalen Bildachse) sowie die Länge der Haupt- und Nebenachsen zurückgegeben.Diese Werte werden dann weiterverarbeitet, um die zuvor identifizierten Metriken zu extrahieren.Weitere Informationen zur Implementierung dieser MATLAB-Funktionen finden Sie in der entsprechenden Dokumentation36.
Der Algorithmus schreitet Bild für Bild durch die Videosequenz voran und extrahiert bei jedem Schritt Metriken.Lange Sequenzen von Bildern, in denen keine Partikel vorhanden sind, können darauf hinweisen, dass der Laser für die Pause zwischen den Schichten ausgeschaltet wurde, während kurze Sequenzen darauf hinweisen können, dass die Kamera die „Flagge“ oder den „Auto-Shutter“ aktiviert hat.Daher werden Sequenzen von Frames, bei denen länger als 0,5 s kein Schmelzbad vorhanden ist, als Start- und Endpunkte für Schichten betrachtet und die dazwischen liegenden leeren Frames werden verworfen.Die Daten werden dann automatisch in ein schichtweises Strukturarray aufgeteilt und gespeichert, damit die Metriken später analysiert werden können.Eine kurze Diskussion der Recheneffizienz dieses Algorithmus finden Sie im Ergänzenden Hinweis: Bildverarbeitungsalgorithmus online.
Für die drei Schnittwinkel mit einer Bauhöhe von 20 mm sind in Abb. 6 Fotografien der gefertigten Teile dargestellt.
Bestandsmorphologien der Proben (a) IW1, (b) IW4 und (c) IW7.Der Einschub in (c) zeigt den Ort der Vertiefung, die sich während der Ablagerung gebildet hat.
Proben, die mit einem 90°-Schnittpunkt hergestellt wurden, Abb. 6a, weisen eine weitgehend ebene Oberfläche mit erhöhten Wandenden und einem flachen Übergangsbereich auf.Bei 60° (Abb. 6b) und 30° (Abb. 6c) hergestellte Proben weisen ebenfalls erhabene Wandenden und ebene Flächen zwischen der Verbindungsstelle und den Wandenden auf.Bei allen spitzwinkligen Proben bildet sich jedoch in der Mitte der Verbindungsstelle eine Vertiefung, gepaart mit einer Ausbuchtung im Inneren des Winkels.Die Vertiefung ist bei den um 30° abgewinkelten Proben am tiefsten (Abb. 6c) und weist eine Ansammlung anhaftender Partikel auf.
Diese Strukturmerkmale korrelieren mit den drei primär interessierenden Stellen, die in Abb. 1 dargestellt sind, und können wie folgt klassifiziert werden: die mittleren Bereiche, die Wandumkehrpunkte und der Verbindungsbereich.Die Besonderheiten dieser Strukturmerkmale beziehen sich nur auf den Schnittwinkel und nicht auf die Designhöhe, wobei die 5-mm- und 20-mm-Proben eine nahezu identische Oberflächentopographie aufweisen.Dies weist darauf hin, dass die Initiierung jeder Feature-Class früh im Erstellungsprozess beginnt.Die mittleren Bereiche, in denen sich das Schmelzbad in einer geraden Linie mit konstanter Geschwindigkeit bewegt, veranschaulichen eine stationäre Abscheidung mit geringem Einfluss anderer Teile des Aufbaus und ähneln der Erzeugung einer zweispurigen, breiten, dünnen Wand mit 50 % Überlappung.Die Wendepunkte befinden sich am Ende jedes Wandsegments, wo der Abscheidekopf seine Richtung umkehrt und zur benachbarten Spur zurückkehrt. Dadurch erhöht sich die Zeit, die für das Abscheiden von Material in der Nähe aufgewendet wird, was zu einer Ansammlung von Material und Hitze an diesen Stellen führt Standorte.Die Verbindungsstelle der Wände ist der dritte und variabelste zu analysierende Bereich.
Im Gegensatz zu den Mittelbereichen und Wendepunkten, die für alle Proben ähnlich sind, weist der Übergangsbereich abhängig vom Schnittwinkel zwischen den Wänden eine unterschiedliche Morphologie auf.Die DCAM-Slicing-Software, die zum Generieren des Werkzeugwegs für die Proben aus dem CAD-Modell verwendet wird, erstellt automatisch Verrundungen zwischen Wänden. Daher ändern die Verrundungen je nach Schnittwinkel den Grad der Überlappung der Laser- und Pulverpunkte im Verbindungsbereich.Bei den 90°-Proben ist die Überlappung gleichmäßig verteilt und es gibt nur minimale Höhenunterschiede an der Verbindungsstelle.Bei der 60°-Probe führt die Verrundung im Inneren des Winkels zu einer Ausbuchtung überschüssigen Materials im Vergleich zum umgebenden stationären Bereich.Darüber hinaus bildet sich auch in der Mitte der Verbindungsstelle eine Vertiefung, wo nun die Abdeckung durch Laser und Pulverfleck verringert ist.Dieses Paar aus Ausbuchtung und Vertiefung ist in der 30°-Probe deutlicher ausgeprägt, wo die tiefere Vertiefung auch eine Ansammlung teilweise geschmolzener Partikel enthält, ähnlich denen, die an den Seiten der dünnen Wände haften.Dies weist darauf hin, dass dieser Region nicht genügend Energie zugeführt wird, um diese Partikel effektiv zu schmelzen, was zur Bildung interner Defekte in dieser Region führt.
Für alle hergestellten Proben wurden Mikro-CT-Scans angefertigt.Ein repräsentatives Querschnittsbild aus dem Verbindungsbereich von Proben mit drei verschiedenen Schnittwinkeln ist in Abb. 7 dargestellt
Vergleich der Porosität in den Verbindungsbereichen der Proben (a) IW1, (b) IW4 und (c) IW7.Die IW7-Probe zeigt eine nahezu kontinuierliche Porosität entlang der Mittelachse der Verbindungsstelle.
Während sich in den 90°- und 60°-Proben (Abb. 7a, b) einige Poren bilden, sind diese typischerweise verteilt, abgerundet und sowohl in der Anzahl als auch in der Größe klein im Vergleich zu denen, die in den 30°-Proben gebildet werden (Abb. 7c).Während die größte Pore, die in den 90°-Proben entdeckt wurde, etwa 180 μm lang war, bilden die Poren in den 30°-Proben einen nahezu durchgehenden Hohlraum entlang der Mittelachse des Verbindungsbereichs.Einige weisen auch unregelmäßige Morphologien auf, was auf das Fehlen von Fusionsdefekten hindeutet.Das Vorhandensein anhaftender Partikel in der Vertiefung der 30°-Proben, jedoch nicht der 60°-Proben, weist darauf hin, dass die Wärme nicht ausreicht, um vollständig zu schmelzen, was zu dem in Abb. 7c gezeigten Mangel an Schmelzporosität führt.Wir gehen davon aus, dass dies auf die automatische Verrundung des Werkzeugwegs zurückzuführen ist, die die Laserüberlappung in der Mitte der Verbindungsstelle bei engeren Schnittwinkeln reduziert, und zeigen im Abschnitt „Beseitigung von Verbindungsfehlern mithilfe eines modifizierten Werkzeugwegs“, dass dies vermieden werden kann.
Die Porosität in der Verbindungsstelle der 30°-Probe tritt an derselben Stelle auf wie die in Abb. 6c beobachtete Vertiefung.Dies deutet darauf hin, dass die bei diesen Proben beobachtete Oberflächenvertiefung ein Hinweis auf interne Defekte ist, die durch die Erschöpfung von Pulver- und Laserenergie in der Mitte der Verbindung verursacht werden.Es ist jedoch auch klar, dass das bloße Vorhandensein einer Vertiefung keine Hohlraumbildung darstellt.Die 60°-Proben weisen eine flache Vertiefung auf, es gibt jedoch nur einen leichten Anstieg der Verbindungsporosität gegenüber den 90°-Proben.Die tatsächliche Bildung interner Defekte muss anderweitig bestätigt werden, entweder durch Inspektion nach der Abscheidung (z. B. durch Mikro-CT wie zuvor) oder durch Prozessüberwachung.
Die von jeder der beiden Off-Axis-Kameras gemessene vertikale Verschiebung ist in Abb. 8 als Funktion des Abstands vom Startpunkt jeder Schicht dargestellt.
Schichtweise Daten, die von den beiden Off-Axis-Kameras während der Herstellung der Probe IW7 von der letzten Schicht erfasst wurden.Die wichtigsten Merkmale wurden identifiziert und gekennzeichnet.(a) Vertikale Verschiebung von der Brennebene, gemessen mit der 1M-Kamera (Blick entlang der j-Achse).(b) Vertikale Verschiebung von der Brennebene, gemessen mit der 05M-Kamera (Blick entlang der i-Achse).(c) Beispiel einer symmetrischen Umkehrspitze für vertikale Verschiebung.Tritt auf, wenn die Kamera senkrecht zum Wandende steht.(d) Beispiel eines asymmetrischen Turn-Around-Peaks.Tritt auf, wenn die Kamera am Wandende ausgerichtet ist.
In den dargestellten Verschiebungsdiagrammen können charakteristische Merkmale identifiziert und den drei interessierenden Stellen der sich kreuzenden Wandproben zugeordnet werden.Erstens weisen die mittleren Bereiche der dünnen Wände einen überwiegend flachen Grundlinienwert auf, wie man es von einer stationären Abscheidung erwarten kann und in Abb. 8a, b zu sehen ist.Ähnliche Bereiche mit konstantem Basiswert werden auch bei den Schmelzbadbereichsmessungen mit der Koaxialkamera beobachtet (ergänzende Abbildung S1), obwohl das Rauschen dieses Sensors höher ist.Aus den Off-Axis-Kameras geht klar hervor, dass diese stationäre Abscheidung bei einer positiven Verschiebung von der Ebene des Düsenarbeitsabstands auftritt.Diese Überbauungen in den mittleren Bereichen wurden mit den beiden Off-Axis-Kameras für eine Spannweite von 5 mm zwischen den Wandenden und dem Verbindungsbereich entlang der längeren Wand gemessen und mit Messungen verglichen, die aus Mikro-CT-Scans an denselben Positionen entnommen wurden.Die durchschnittlichen Überbauungswerte sind in Tabelle 3 angegeben. Es ist ersichtlich, dass die Off-Axis-Kameras zwar ähnliche Messungen liefern, die Mikro-CT-Daten jedoch eine Überbauungsmessung liefern, die durchweg doppelt so hoch ist wie die Schätzung beider Off-Axis-Kameras.
Der Hauptgrund für die Diskrepanz zwischen den Überbauungsmessungen mittels Mikro-CT und den Schätzungen durch Schmelzbadverfolgung könnte in der Entwicklung der Aufbauform liegen.Als der Basiswert für den Schwerpunkt in der ersten Schicht genommen wurde, war das Substrat flach und der Schmelzbereich war auf seine Oberfläche beschränkt.Während der Bau fortschreitet, besteht die Möglichkeit, dass frühere Schichten schmelzen und sich der Schwerpunkt im Verhältnis zur eigentlichen Bauoberfläche nach unten verschiebt.Obwohl die Schwerpunktverfolgung zwar gute Informationen über die Oberflächentopographie liefert, kann es sein, dass sie die tatsächliche Überbauungsschätzung nicht vollständig erfasst, ohne diesen Versatz anzupassen.Für die in dieser Studie erstellten Proben berücksichtigt ein konstanter Korrekturfaktor von 2,1 den Versatz genau.Möglicherweise sind jedoch weitere Arbeiten erforderlich, um weitere Beziehungen zwischen der Schwerpunktposition und dem Oberflächenhöheninkrement aufzuklären.
Insgesamt geht der Trend zu einer zunehmenden Überbauung bei größeren Bauhöhen, es wird jedoch erwartet, dass dieser Trend nicht unbegrenzt weiter zunimmt, sondern einen stabilen Überbauungszustand erreicht, wie von Donadello et al.26 diskutiert.
In Abb. 8a und b sind zwei weitere Klassen von Merkmalen zu erkennen, nämlich Spitzen und Täler, die den stationären Zustand unterbrechen.Bei den Umkehrspitzen handelt es sich bei den Messungen der Off-Axis-Kameras stets um die höchsten Werte der Verschiebung, wobei die Werte aller drei Umkehrpunkte in etwa gleichwertig sind.Sie zeichnen sich auch durch die größten Flächenwerte aus, die von der Koaxialkamera erhalten wurden (Ergänzende Abbildung S1).Bei näherer Betrachtung können diese Peaks anhand ihrer charakteristischen Formen weiter klassifiziert werden, da sie in Dubletts aufgeteilt sind, die eine symmetrische oder asymmetrische Form haben können, wie in Abb. 8c bzw. d dargestellt.Die asymmetrische Peakaufspaltung resultiert aus der Selbstblockierung, die auftritt, wenn sich das Schmelzbad entlang der optischen Achse der Kamera bewegt.Während sich das Schmelzbad von der Kamera entfernt, wird der heißeste und größte Teil des Schmelzbades teilweise durch das Ende der abgelagerten Spur verdeckt, was zu einem niedrigeren Unterpeak führt.Das lokale Minimum bildet sich dann, wenn das Schmelzbad das äußerste Ende der Wand erreicht und teilweise unter den Rand absinkt, wodurch es von der Kamera noch weiter verdeckt wird und die vertikale Verschiebung abnimmt.Während das Schmelzbad seine Richtung ändert und sich auf die Kamera zubewegt, ist das Schmelzbad im Blickfeld der Kamera nun am größten und es hat sich mehr Material abgelagert, was zu dem höheren Unterpeak im Dublett führt.In ähnlicher Weise kommt es auch zu einer symmetrischen Peakaufspaltung, weil das Schmelzbad an den Enden teilweise über den Rand der Wand eintaucht. In diesem Fall ist die optische Achse der Kamera jedoch senkrecht zur Querrichtung des Schmelzbades ausgerichtet.Daher gibt es kaum Unterschiede in der Ansicht der Schmelzbadposition und beide Peaks weisen äquivalente Werte auf.
Im Zusammenhang mit der Bildung von Hohlräumen an Verbindungsstellen in filetierten Proben, die im Abschnitt „Bildung von Hohlräumen an Verbindungsstellen in filetierten Proben“ beschrieben wird, können in einigen Proben auch kleinere Einzelpeaks vorhanden sein.Diese deuten typischerweise auf das Vorhandensein einer Ausbuchtung im Inneren des abgewinkelten Übergangs zwischen den Wänden hin und sind daher bei den 90°-Proben nicht vorhanden, am deutlichsten jedoch bei den 30°-Proben.Abhängig von der Betrachtungskamera und der Querrichtung kann dieser Gipfel isoliert sein oder an ein scharfes Tal angrenzen.Diese Mulde tritt bei Proben auf, die in der Mitte des Verbindungsbereichs eine Vertiefung aufweisen, wenn sich das Schmelzbad in diese Vertiefung bewegt.Die Reihenfolge von Spitzen und Tiefen in diesen gekoppelten Signalen zeigt den Querweg des Laserpunkts an diesem Punkt an, unabhängig davon, ob er zuerst die Ausbuchtung oder die Vertiefung passiert.
Das Erscheinungsbild des Trogs ist auch in der Ansicht der außeraxialen vertikalen Verschiebungsdiagramme (Abb. 8a, b) ausgeprägter als im koaxialen Flächendiagramm (ergänzende Abbildung S1).Dies weist darauf hin, dass sich die Fläche des Schmelzbads zwar beim Passieren der Vertiefung verringern kann, diese Änderung jedoch gering ist im Vergleich zu der starken scheinbaren Flächenzunahme bei Umkehrspitzen, die auf eine längere Verweilzeit des Lasers und eine höhere Höhe zurückzuführen ist diese Punkte.Beim Passieren der Vertiefung ändert sich die Verweilzeit im Vergleich zu den Mittelbereichen nicht, sondern nur die Verringerung der vertikalen Verschiebung, was einen geringen Einfluss auf die sichtbare Fläche für die Koaxialkamera hat.Dies verdeutlicht, dass die Koaxialkamera zwar in der Lage ist, die Geometrie des Schmelzbads ohne perspektivische Verzerrung zu überwachen und auch die Lage von Wendepunkten deutlich anzuzeigen, andere geometrische Merkmale jedoch weniger deutlich zu erkennen sind als bei Aufnahmen mit der Off-Axis-Kamera Kameras.
Diese Merkmale in den Kamerasignalen und ihr Zusammenhang mit physikalischen Phänomenen in den hergestellten Proben legen die Möglichkeit einer frühzeitigen Erkennung von Hohlraumdefekten nahe.Durch die Untersuchung der von den Kamera-Feeds erzeugten Signale ist es möglich, das Auftreten ähnlicher Datenmerkmale in Schichten weiter unten in der Probe und damit früher im Aufbau zu identifizieren.Von besonderem Interesse ist das Vorhandensein der Vertiefungsmulde, die im vorherigen Abschnitt darauf hingewiesen wurde, dass sie mit der Bildung von Hohlräumen innerhalb der Verbindungsregion zusammenhängt.Wie in Tabelle 4 gezeigt, kann das Tief der Vertiefung bei einer frühen Schichtzahl im Verhältnis zur Gesamtzahl der Schichten in der Probe identifiziert werden.Es ist zu beachten, dass es sich bei der hier angegebenen „Schichtentfernung“ um die Entfernung handelt, die das Schmelzbad zurückgelegt hat, seit die Kamera es erstmals erkennen konnte, und dass sich die Startposition jeder Schicht von der der anderen Schichten unterscheidet.Ein Beispiel für die Früherkennung ist für die Probe IW7 in Abb. 9 dargestellt.
Früherkennung von Fehlern in der Probe IW7 (Leistung: 480 W, Verfahrgeschwindigkeit: 800 mm/s).Vertikaler Querschnitt der Verbindung mit Mikro-CT-Scan (mit Angabe der ungefähren Höhe der Probe bei Schicht 7) (a), Messung der Schmelzbadfläche mit der CLAMIR-Kamera (b), vertikale Verschiebung von der Brennebene in der 1M-Kamera (c) und 05M-Kamera (d), alle auf Schicht 7. Die deutlichsten Hinweispunkte für die Senke sind in den vertikalen Verschiebungsdiagrammen mit einem grünen Kreis markiert.
Tabelle 4 zeigt, dass es möglich ist, das Vorhandensein der Vertiefung zu einem frühen Zeitpunkt während der Herstellung dieser Proben zu erkennen, und dass es offenbar eine bevorzugte Scanrichtung für die Identifizierung dieser Mulde mit beiden außeraxialen Kameras gibt.Die früheste Erkennung erfolgt immer auf einer Schicht mit ungerader Nummer, wobei sich der Laser gegen den Uhrzeigersinn bewegt;Daher beobachtet die 05M-Kamera das Ende des Schmelzbades, während es den ununterbrochenen Scan des langen Wandabschnitts durchquert.Wenn das Schmelzbad die Vertiefung erreicht, wird die Vorderseite des Schmelzbades teilweise verdeckt und der Abfall der Schwerpunktposition ist für die Kamera deutlicher.Auf Schichten mit gerader Anzahl würde sich das Schmelzbad in Richtung der 05M-Kamera bewegen, und die helle Vorderseite des Schmelzbades vergrößert die Größe des erkannten Partikels, wodurch die Empfindlichkeit der Schwerpunktpositionsverfolgung verringert wird.
Der Mikro-CT-Scan der Probe, Abb. 9a, bestätigt, dass sich an der Stelle der erkannten Vertiefung ein Hohlraum gebildet hat.Im Fall der Probe IW7 erfolgt die erste Detektion der Vertiefung bei Schicht 7, wo die erwartete Höhe der Probe und damit die Brennebene auf 1,5 mm über dem Substrat gestiegen ist.Die hier sowohl von der 1M- als auch der 05M-Kamera erfasste Mulde (Abb. 9c,d) zeigt eine vertikale Verschiebung von 0,1 mm über dieser Ebene.Wie in Abb. 9a dargestellt, befindet sich eine Pore 1,6 mm über dem Substrat. Diese Pore ist jedoch weder die größte noch die erste, die bis zu diesem Punkt aufgetreten ist.Dies deutet darauf hin, dass möglicherweise eine Mindesthöhe erforderlich ist, die der Körper der Probe erreichen muss, bevor eine Vertiefung erkennbar ist.Abbildung 9b zeigt die von der Koaxialkamera während derselben Schicht gesammelten Daten, und obwohl der Porendefekt in diesen Daten nicht klar erkennbar ist, entsprechen die scharfen Spitzen den Umkehrstellen, an denen das Schmelzbad im Blickfeld der Kamera größer ist .
Um die vom Überwachungssystem erhaltenen Informationen zu verstehen, müssen die Einschränkungen und Sichtbedingungen der Kameras berücksichtigt werden.
Eine wichtige Einschränkung der Koaxialkamera besteht darin, dass die Düsenöffnung das Sichtfeld (FOV) auf einen Bereich von etwa 5 mm Durchmesser beschränkt.Das Sichtfeld kann daher den für die Bearbeitung verwendeten Laserpunktdurchmesser bestimmen.Internen Studien zufolge hatte der verwendete Laserpunkt einen Durchmesser von 1,5 mm, sodass der Schmelzbadschweif unter den meisten Bedingungen innerhalb der Öffnung sichtbar war.Eine weitere Einschränkung der Koaxialkamera besteht darin, dass IR-Licht von der Innenseite der Düse reflektiert und gestreut werden kann, wodurch ein Lichtring um den gewünschten interessierenden Bereich entsteht, wie in Abb. 2b dargestellt, der die Bildanalyse beeinträchtigen kann.Dies führt auch zu einer weichen Grenze für die Energiedichte, die der Prozesszone zugeführt wird.Höhere Energiedichten führen zu höheren Schmelzbadtemperaturen und größeren Größen.Dies erhöht auch die Menge der von der Innenseite der Düse reflektierten IR-Strahlung und verringert das Sichtfeld der Kamera weiter.Ebenso können auch längere Schmelzbadschwänze abgeschnitten werden.Während daher die unverzerrte koaxiale Ansicht für genaue Messungen der Schmelzbadfläche und -geometrie bei kleineren Schmelzbadgrößen vorteilhaft ist, erfordert jede Erweiterung der Verarbeitungsparameter über einen begrenzten Bereich hinaus die Hinzufügung mindestens einer weiteren außeraxialen Kamera.
Die außeraxialen Kameras unterliegen perspektivischen Verzerrungen, wie im Abschnitt „Geometrische Korrekturen“ erläutert, die berücksichtigt werden müssen.Darüber hinaus kann die Beobachtung des Schmelzbades aus einem Winkel zu einer vorübergehenden oder teilweisen Blockierung des Schmelzbades während der Abscheidung führen.Blockierungen können durch andere Objekte in der Bauumgebung, wie etwa die Abscheidungsdüse, oder andere Bereiche derselben Probe verursacht werden.
Das Problem der perspektivischen Verzerrung bei einer außeraxialen Kamera lässt sich durch einen Vergleich der Länge des Schmelzbads veranschaulichen, die im Profil (Querrichtung des Schmelzbads ausgerichtet mit der Kameraachse) und im Querformat (Querrichtung des Schmelzbads senkrecht zur Kameraachse) gemessen wird.Nehmen Sie als Beispiel die erste Schicht der IW2-Probe, um die Auswirkungen von Teilüberwuchs auf Messungen zu eliminieren.Wenn sich das Schmelzbad im Profil befindet und sich auf die Optris 1M-Kamera zubewegt, beträgt die mittlere Länge über eine Strecke von 10 mm etwa 1,9 mm (korrigiert um den perspektivischen Winkel), während die unverzerrte Ansicht von Optris 05M und CLAMIR diesen Wert mit 1,6 misst mm bzw. 1,3 mm.In gleicher Ausrichtung beträgt die Schmelzbadbreite, gemessen im unverzerrten Profil mit der Optris 1M-Kamera, ebenfalls 1,3 mm und stimmt mit der CLAMIR-Messung von 1,3 mm überein, während die verzerrte Ansicht der Optris 05M-Kamera die Breite bei 2,4 mm misst.
Im Allgemeinen liefert die Messung der Länge oder Breite entlang der y-Achse des Bildes für die abgewinkelten Kameras oft eine Überschätzung der gleichen Werte, die von der Begleitkamera längs gemessen werden, wenn keine Selbstblockierung auftritt (d. h. Ablagerung hinter einer benachbarten Spur, die zuvor abgelagert wurde). eine Kamera, die nicht von Verzerrungen betroffen ist.Allerdings wird dies mit der Geometrie des Bauteils immer komplexer, sodass mehrere Kameras erforderlich sind, um Messungen entlang mehrerer Achsen zu erfassen.
Um zu bestätigen, dass die Kameraerkennung nicht allein ein Artefakt des Schnittwinkels war und dass die Bildung der Verbindungslückenfehler aufgrund der Werkzeugwegplanung der engwinkligen Schnittpunkte auftrat, wurde ein weiterer Satz von Proben mit modifizierten Werkzeugwegen erstellt, die diese beseitigten Filets an der Kreuzung.Diese Modifikation sollte theoretisch im Vergleich zu den Originalproben ein gleichmäßigeres Maß an Laserpunktüberlappung an der Verbindungsstelle aufrechterhalten.Diese modifizierten Proben wurden alle mit der gleichen Designhöhe von 20 mm hergestellt, da nur die Bildung von Verbindungsdefekten untersucht wurde und die vorherigen Proben gezeigt hatten, dass diese von der Designhöhe der Proben nicht beeinflusst wurden.Für die Verbindungsbereiche wurden mit dem Keyence-Digitalmikroskop topografische Bilder erstellt und an den Proben wurde eine Mikro-CT durchgeführt. Die Ergebnisse sind in Abb. 10 dargestellt.
Vergleich des Verbindungsbereichs in 30°-Proben mit topografischen Bildern von (a) Original-, IW7- und (b) modifizierten, IW7-Mod-Werkzeugwegen, aufgenommen mit dem 3D-Digitalmikroskop Keyence VHX-5000 bei 50-facher Vergrößerung.Mikro-CT-Bild, das den Querschnitt des Übergangsbereichs in IW7-Mod ohne die gleiche Porosität wie in IW7 zeigt.Der Verbindungsbereich ist in beiden (a,b) hervorgehoben und zeigt das Fehlen der Vertiefung in der IW7-Mod-Probe.
Die modifizierten Werkzeugwegproben zeigten eine Oberfläche, die den Originalproben ähnelte, mit Ausnahme des Fehlens der Vertiefung in der Mitte der Verbindungsstelle, wie im Vergleich von Abb. 10a, b zu sehen ist, obwohl sich immer noch eine Ausbuchtung bildete das Innere der Winkelschnittpunkte für die 60°- und 30°-Proben.
Eine Untersuchung der aus dem Überwachungsaufbau extrahierten Signale zeigt ebenfalls keine Anzeichen einer Vertiefungsbildung in den modifizierten Werkzeugwegproben, weist jedoch auf die Bildung einer Ausbuchtung hin, die immer noch in den 60°- und 30°-Proben auftritt.Bei der Prüfung der Mikro-CT-Ergebnisse wurde letztendlich bestätigt, dass im Verbindungsbereich der 30°-Proben keine Defekte vorhanden waren, Abb. 10c.Zusammengenommen veranschaulichen die Beobachtungen dieser modifizierten Proben zwei wichtige Erkenntnisse.
Erstens wurde festgestellt, dass der Entstehungsmechanismus für die Hohlraumdefekte an der Verbindungsstelle darauf zurückzuführen ist, dass der Werkzeugweg die Verbindungsstelle sowohl an Laserbestrahlungsstärke als auch an Ausgangsmaterial erschöpft, was zu einer verringerten Materialablagerung führt.Daher müssen bei der Werkzeugwegplanung die Auswirkungen reduzierter Überlappungen an Verbindungsbereichen in Bauteilen mit komplizierten Geometrien berücksichtigt werden.Schnittwinkel von weniger als 60° können zu einer erhöhten Porosität führen, wenn Eckrundungen eine vollständige Überlappung der Pfade verhindern.Da Verrundungen eine Methode zur Minimierung scharfer Ecken in Geometrien sind, ist es oft nicht praktikabel, diese von Strukturbauteilen zu entfernen, da sonst ein erhöhtes Risiko eines Versagens der Teile aufgrund von Ermüdung oder Rissbildung besteht37.Daher müssen je nach geplanter Konstruktion andere Methoden in Betracht gezogen werden, um eine vollständige Durchschmelzung an engwinkligen Kreuzungen sicherzustellen.Dazu kann die Einbeziehung eines zusätzlichen Innenscans in der Mitte der Verbindungsstelle gehören, sofern dadurch die Hitze- und Materialansammlung an dieser Stelle nicht übermäßig erhöht wird.Alternativ könnte vorgeschlagen werden, den Werkzeugweg zu ändern, um den Abstand vom Schnittpunkt, an dem die Verrundungen implementiert werden, zu vergrößern und so die Auswirkungen einer längeren Laserverweilzeit im Schnittbereich zu verringern.Dies könnte mit einem internen Scan gekoppelt werden, um die Verbindung weiter zu verstärken;Allerdings wäre dies mit einem höheren Zeit-, Gewichts- und Materialaufwand verbunden.
Zweitens wird gezeigt, dass die Erkennung dieser Vertiefung im bildbasierten Trackingsystem unabhängig vom Schnittwinkel erfolgt und kein Artefakt in der Bildgebung als eine falsche Korrelation zwischen Winkel und Vertiefungssignalisierung angesehen werden kann.
Diese Arbeit stellt ein mehrachsiges Infrarot-Vision-basiertes System zur In-situ-Überwachung der lasergesteuerten Energiedeposition mit drei Kameras vor.Es wird ein Videoverarbeitungsrahmen zur Verfolgung der Entwicklung des Schmelzbades während der Abscheidung beschrieben, um Verschiebungs- und geometrische Informationen zu extrahieren.Es wird gezeigt, dass Schwankungen bei der Überwachung der vertikalen Verschiebung die Bildung von Strukturmerkmalen wie Vertiefungen und Ausbuchtungen in dünnwandigen Strukturen mit sich kreuzenden Wänden in verschiedenen Winkeln erkennen können.Die Vorteile der Multisensorüberwachung bei der Erkennung und Identifizierung dieser Merkmale werden demonstriert, wobei Merkmale unabhängig über mehrere Sensorkonfigurationen hinweg erkannt werden und gleichzeitig unterschiedliche Prozessinformationen bereitgestellt werden.
Es wird gezeigt, dass eine verringerte Laserpunktüberlappung aufgrund der automatischen Verrundung bei der Werkzeugwegplanung zu Bereichen mit verringerter Abscheidungsqualität führt, die durch Oberflächenvertiefungen gekennzeichnet sind, was zur Bildung interner Defekte führt, die bei Proben mit einem 30°-Schnittpunkt am deutlichsten hervortreten.Die Prävalenz dieser inneren Porosität wird mittels Mikro-CT nachgewiesen.Ebenso wird die Änderung des Werkzeugwegs zum Entfernen automatischer Verrundungen gezeigt, um diese innere Porosität zu beseitigen.Die der Oberflächenvertiefung entsprechenden Signale werden vom Algorithmus identifiziert und verdeutlichen die Fähigkeit des Systems zur Früherkennung von Defekten, beispielsweise bei Proben mit einem 30°-Schnittpunkt.Dies ermöglicht die Integration eines Inline-Frühwarnsystems zur Erkennung von Defekten und geometrischen Merkmalsbildungen, das in der zukünftigen Arbeit implementiert wird.Abschließend wird empfohlen, bei der Werkzeugwegplanung für komplexe Geometrien mit engen Schnittwinkeln die Auswirkungen der Verrundung auf die Laserbestrahlungsstärke von Teilen zu berücksichtigen.
Zukünftige Arbeiten werden die Ergebnisse dieser Studie erweitern, indem sie die Beziehungen zwischen anderen extrahierten Metriken und potenziellen Defektzuständen in deponierten Proben analysieren.Durch Rationalisierung und Downsampling der Datenübertragung kann dieses System für eine Echtzeitüberwachung realisiert werden.
Die im Rahmen der aktuellen Studie generierten und/oder analysierten Datensätze sind nicht öffentlich zugänglich, da sie derzeit im Rahmen weiterer Studien ausgewertet werden und auch aufgrund des proprietären Dateiformats vieler der aufgezeichneten Videodateien.Auf begründete Anfrage werden die Daten beim entsprechenden Autor zur Verfügung gestellt.
Blakey-Milner, B. et al.Metalladditive Fertigung in der Luft- und Raumfahrt: Ein Rückblick.Mater.Des.209, 110008. https://doi.org/10.1016/j.matdes.2021.110008 (2021).
Salmi, M. Additive Fertigungsverfahren in medizinischen Anwendungen.Materialien 14, 191 (2021).
Artikel CAS PubMed PubMed Central ADS Google Scholar
Hensley, C. et al.Qualifizierungswege für additiv gefertigte Komponenten für nukleare Anwendungen.J. Nucl.Mater.548, 152846. https://doi.org/10.1016/j.jnucmat.2021.152846 (2021).
Thompson, SM, Bian, L., Shamsaei, N. & Yadollahi, A. Ein Überblick über die direkte Laserauftragung für die additive Fertigung;Teil I: Transportphänomene, Modellierung und Diagnostik.Zusatz.Hersteller8, 36–62.https://doi.org/10.1016/j.addma.2015.07.001 (2015).
Tan Zhi'En, E., Pang, JHL & Kaminski, J. Auswirkungen der gerichteten Energieabscheidung auf die Steuerung des Aufbauprozesses auf die Mikrostruktur und das Zugversagensverhalten.J. Mater.Verfahren.Technol.294, 117139. https://doi.org/10.1016/j.jmatprotec.2021.117139 (2021).
du Plessis, A., Yadroitsava, I. & Yadroitsev, I. Auswirkungen von Defekten auf mechanische Eigenschaften in der additiven Metallfertigung: Eine Übersicht mit Schwerpunkt auf Erkenntnissen der Röntgentomographie.Mater.Des.187, 385. https://doi.org/10.1016/j.matdes.2019.108385 (2020).
Scharowsky, T., Bauereiß, A. & Körner, C. Einfluss der Schraffurstrategie auf die Konsolidierung beim selektiven Elektronenstrahlschmelzen von Ti–6Al–4V.Int.J. Adv.HerstellerTechnol.92, 2809–2818.https://doi.org/10.1007/s00170-017-0375-1 (2017).
Shao, J. et al.Prozesskarten und optimale Verarbeitungsfenster basierend auf dreidimensionalen morphologischen Eigenschaften bei der lasergesteuerten Energieabscheidung von Ni-basierten Legierungen.Opt.Lasertechnologie142, 107162. https://doi.org/10.1016/j.optlastec.2021.107162 (2021).
Chen, Y. et al.Synchrotron-Röntgenbildgebung der additiven Fertigung durch gerichtete Energieabscheidung der Titanlegierung Ti-6242.Zusatz.Hersteller41, 101969. https://doi.org/10.1016/j.addma.2021.101969 (2021).
Svetlizky, D. et al.Additive Fertigung mit gerichteter Energieabscheidung (DED): Physikalische Eigenschaften, Defekte, Herausforderungen und Anwendungen.Mater.Heute 49, 271–295.https://doi.org/10.1016/j.mattod.2021.03.020 (2021).
Bontha, S. Die Auswirkung von Prozessvariablen auf die Mikrostruktur in laserabgeschiedenen Materialien Doktorarbeit der Philosophie, Wright State University (2006).
Shamsaei, N., Yadollahi, A., Bian, L. & Thompson, SM Ein Überblick über die direkte Laserauftragung für die additive Fertigung;Teil II: Mechanisches Verhalten, Prozessparameteroptimierung und -kontrolle.Zusatz.Hersteller8, 12–35.https://doi.org/10.1016/j.addma.2015.07.002 (2015).
Herzog, T., Brandt, M., Trinchi, A., Sola, A. & Molotnikov, A. Prozessüberwachung und maschinelles Lernen zur Fehlererkennung in der laserbasierten additiven Metallfertigung.J. Intell.Herstellerhttps://doi.org/10.1007/s10845-023-02119-y (2023).
Hagenlocher, C. et al.Prozessüberwachung des thermischen Profils während der Erstarrung bei der lasergesteuerten Energieabscheidung von Aluminium.Zusatz.HerstellerLette.3, 100084. https://doi.org/10.1016/j.addlet.2022.100084 (2022).
Feng, S. et al.Vorhersage von Laser-Pulverbett-Schmelzfehlern durch In-Prozess-Überwachungsdaten und maschinelles Lernen.Mater.Des.222, 111115. https://doi.org/10.1016/j.matdes.2022.111115 (2022).
Friel, RJ & Harris, RA Ultraschall-Additive Fertigung – Ein hybrider Produktionsprozess für neuartige funktionale Produkte.Procedia CIRP 6, 35–40.https://doi.org/10.1016/j.procir.2013.03.004 (2013).
Zhao, C. et al.Echtzeitüberwachung des Laser-Pulverbett-Fusionsprozesses mithilfe von Hochgeschwindigkeits-Röntgenbildgebung und -beugung.Wissenschaft.Rep. 7, 2. https://doi.org/10.1038/s41598-017-03761-2 (2017).
Artikel CAS ADS Google Scholar
Baumgartl, H., Tomas, J., Buettner, R. & Merkel, M. Ein Deep-Learning-basiertes Modell zur Defekterkennung bei der Laser-Pulver-Bettfusion mittels in-situ-thermografischer Überwachung.Prog.Zusatz.Herstellerhttps://doi.org/10.1007/s40964-019-00108-3 (2020).
Gonzalez-Val, C., Pallas, A., Panadeiro, V. & Rodriguez, A. Ein Faltungsansatz zur Qualitätsüberwachung für die Laserfertigung.J. Intell.Hersteller31, 789–795.https://doi.org/10.1007/s10845-019-01495-8 (2020).
Jeon, I., Yang, L., Ryu, K. & Sohn, H. Online-Schmelzbadtiefenschätzung während der gerichteten Energieabscheidung unter Verwendung einer koaxialen Infrarotkamera, eines Laserlinienscanners und eines künstlichen neuronalen Netzwerks.Zusatz.Hersteller47, 102295. https://doi.org/10.1016/j.addma.2021.102295 (2021).
Borovkov, H. et al.Inline-Höhenmesstechnik für gerichtete Energiedepositionsprozesse.J. ManufakturMater.Verfahren.5, 85 (2021).
Lu, Y., Sun, G., Xiao, X. & Mazumder, J. Online-Spannungsmessung während der lasergestützten metallischen additiven Fertigung.Wissenschaft.Rep. 9, 1. https://doi.org/10.1038/s41598-019-39849-0 (2019).
Stehmar, C., Gipperich, M., Kogel-Hollacher, M., Velazquez Iturbide, A. & Schmitt, RH Inline optische Kohärenztomographie zur multidirektionalen Prozessüberwachung in einem koaxialen LMD-w-Prozess.Appl.Wissenschaft.12, 2701 (2022).
Becker, D. et al.Einfluss eines regelkreisgesteuerten Laser-Metalldrahtabscheidungsprozesses von S Al 5356 auf die Qualität gefertigter Teile vor und nach der anschließenden Bearbeitung.Prod.Ing.https://doi.org/10.1007/s11740-021-01030-w (2021).
Donadello, S., Motta, M., Demir, AG & Previtali, B. Überwachung der Lasermetallauftragshöhe mittels koaxialer Lasertriangulation.Opt.Laser-Ing.112, 136–144.https://doi.org/10.1016/j.optlaseng.2018.09.012 (2019).
Donadello, S., Furlan, V., Demir, AG & Previtali, B. Zusammenspiel zwischen Pulvereinfangeffizienz und Schichthöhe bei der selbststabilisierten Lasermetallabscheidung.Opt.Laser-Ing.149, 106817. https://doi.org/10.1016/j.optlaseng.2021.106817 (2022).
Ocylok, S. et al.Korrelationen von Schmelzbadgeometrie und Prozessparametern beim Laserauftragschweißen durch koaxiale Prozessüberwachung.Physik.Procedia 56, 228–238.https://doi.org/10.1016/j.phpro.2014.08.167 (2014).
Ye, J. et al.Vorhersagen geometrischer In-situ-Schmelzbadsignaturen mithilfe maschineller Lerntechniken für die Lasermetallabscheidung.Int.J. Computer Integr.Herstellerhttps://doi.org/10.1080/0951192X.2022.2048422 (2022).
Liu, FQ, Wei, L., Shi, SQ & Wei, HL Über die Vielfalt der Aufbaumerkmale bei der mehrschichtigen lasergesteuerten Energieabscheidung.Zusatz.Hersteller36, 101491. https://doi.org/10.1016/j.addma.2020.101491 (2020).
Wei, HL, Liu, FQ, Liao, WH & Liu, TT Vorhersage räumlich-zeitlicher Variationen von Ablagerungsprofilen und Zwischenspurhohlräumen während der lasergesteuerten Energieabscheidung.Zusatz.Hersteller34, 101219. https://doi.org/10.1016/j.addma.2020.101219 (2020).
Boivineau, M. et al.Thermophysikalische Eigenschaften der festen und flüssigen Ti-6Al-4V (TA6V)-Legierung.Int.J. Thermophys.27, 507–529.https://doi.org/10.1007/PL00021868 (2006).
Artikel CAS ADS Google Scholar
Optris.Technische Daten des Optris PI 1M.https://www.optris.com/en/product/infrared-cameras/pi-series/pi-1m/.Abgerufen 2023.
Optris.Technische Daten des Optris PI 05M.https://www.optris.com/en/product/infrared-cameras/pi-series/pi-05m/.Abgerufen 2023.
Haley, JC et al.Passive Stabilität des Arbeitsabstands in der additiven Fertigung durch lasergesteuerte Energieabscheidung.Mater.Des.161, 86–94.https://doi.org/10.1016/j.matdes.2018.11.021 (2019).
MATLAB-Version: 9.12.0.1884302 (2022a) (The Mathworks, Inc., 2022).
Diegel, O., Nordin, A. & Motte, D. Ein praktischer Leitfaden zum Design für die additive Fertigung (Springer, 2019).
Die Autoren danken den Mitarbeitern der Digital Manufacturing Facility (DMF) der RMIT University für die technische Unterstützung bei der Vorbereitung der Proben und der Entfernung vom Substrat.Die Autoren möchten auch Dr. Sheridan Mayo, Emma Regos und Sherman Wong vom CSIRO für ihre Unterstützung bei der Durchführung der Mikro-CT-Scans der hergestellten Proben danken.
School of Engineering, Centre for Additive Manufacturing, RMIT University, Melbourne, VIC, 3000, Australien
T. Herzog, M. Brandt, C. Hagenlocher & A. Molotnikov
CSIRO Manufacturing, Clayton, VIC, 3168, Australien
T. Herzog, A. Trinchi & A. Sola
Sie können diesen Autor auch in PubMed Google Scholar suchen
Sie können diesen Autor auch in PubMed Google Scholar suchen
Sie können diesen Autor auch in PubMed Google Scholar suchen
Sie können diesen Autor auch in PubMed Google Scholar suchen
Sie können diesen Autor auch in PubMed Google Scholar suchen
Sie können diesen Autor auch in PubMed Google Scholar suchen
TH: Schreiben – Originalentwurf, Software, Methodik, Untersuchung.MB: Betreuung, Ressourcen, Schreiben – Überprüfung und Bearbeitung.AT, AS: Supervision, Schreiben – Überprüfen und Bearbeiten.CH: Schreiben – Rezension und Bearbeitung, Methodik.AM: Supervision, Methodik, Schreiben – Überprüfung und Bearbeitung.
Korrespondenz mit T. Herzog oder A. Molotnikov.
Prof. Andrey Molotnikov ist Co-Autor dieses Manuskripts und Herausgeber dieser Sammlung.Keiner der anderen Autoren hat konkurrierende Interessen zu erklären.
Springer Nature bleibt neutral hinsichtlich der Zuständigkeitsansprüche in veröffentlichten Karten und institutionellen Zugehörigkeiten.
Open Access Dieser Artikel ist unter einer Creative Commons Attribution 4.0 International License lizenziert, die die Nutzung, Weitergabe, Anpassung, Verbreitung und Reproduktion in jedem Medium oder Format erlaubt, sofern Sie den/die Originalautor(en) und die Quelle angemessen angeben. Geben Sie einen Link zur Creative Commons-Lizenz an und geben Sie an, ob Änderungen vorgenommen wurden.Die Bilder oder anderes Material Dritter in diesem Artikel sind in der Creative Commons-Lizenz des Artikels enthalten, sofern in der Quellenangabe für das Material nichts anderes angegeben ist.Wenn Material nicht in der Creative-Commons-Lizenz des Artikels enthalten ist und Ihre beabsichtigte Nutzung nicht gesetzlich zulässig ist oder über die zulässige Nutzung hinausgeht, müssen Sie die Genehmigung direkt vom Urheberrechtsinhaber einholen.Um eine Kopie dieser Lizenz anzuzeigen, besuchen Sie http://creativecommons.org/licenses/by/4.0/.
Herzog, T., Brandt, M., Trinchi, A. et al.Fehlererkennung durch mehrachsige Infrarot-Prozessüberwachung der laserstrahlgesteuerten Energiedeposition.Sci Rep 14, 3861 (2024).https://doi.org/10.1038/s41598-024-53931-2
DOI: https://doi.org/10.1038/s41598-024-53931-2
Jeder, mit dem Sie den folgenden Link teilen, kann diesen Inhalt lesen:
Leider ist für diesen Artikel derzeit kein Link zum Teilen verfügbar.
Bereitgestellt von der Content-Sharing-Initiative Springer Nature SharedIt
Durch das Absenden eines Kommentars erklären Sie sich damit einverstanden, unsere Nutzungsbedingungen und Community-Richtlinien einzuhalten.Wenn Sie etwas als missbräuchlich empfinden oder etwas nicht unseren Bedingungen oder Richtlinien entspricht, kennzeichnen Sie es bitte als unangemessen.
Wissenschaftliche Berichte (Sci Rep) ISSN 2045-2322 (online)
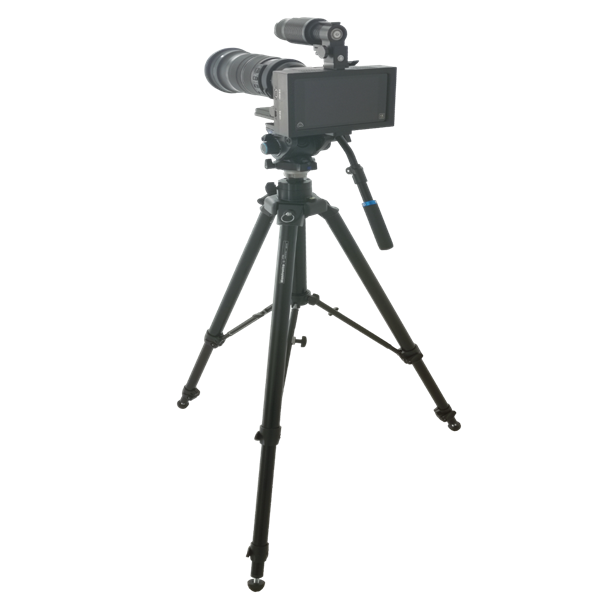
Gepäck-Scanner-Maschine Melden Sie sich täglich kostenlos für den Nature Briefing-Newsletter an – „Was in der Wissenschaft zählt“.