Positive progress during eVTOL prototype testing approaches full transition to forward flight, aids in final full-scale aircraft design for completion and testing in 2026.
Lilium is keen to expand its industrial footprint through leveraging of France’s aerospace heritage and vast supplier base in aerospace and electrification, in preparation for the eVTOL aircraft market demand. Grp Pultruded Window Frames
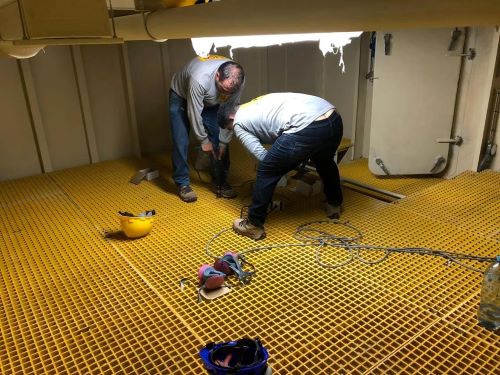
Test results exceeded expectations regarding holding hard vacuum, heat load, rapid chill-down and hydrogen fraction goal, leading to flight prototype fabrication.
“Automotive-style” line has the capability of producing up to 15,000 battery packs — complete with composite enclosures and cylindrical cells — per year to keep up with eVTOL aircraft production goals.
Alberta Innovates initiative selected 20 applicants, including Luxfer, to advance hydrogen production, storage, transmission, distribution and use.
In addition to providing a controlled environment for conducting restrained eVTOL aircraft operation, NIAR provides material development and other testing options.
Nesting, design, GUI and viewing features have been improved or added to the composites design software tool.
Ingersoll Masterprint LFAM printer will be used to produce and demonstrate 100% recyclable tooling that could cut large composite blade development cycles and tooling costs by as much as 50%.
Key structural elements for a 6-meter section of the Airbus biomimetic wing were undertaken by NCC engineering specialists to produce 28 one-off flying parts.
Pioneer in mandrel-based reinforced rubber and composite products, TANIQ offers TaniqWindPro software and robotic winding expertise for composite pressure vessels and more.
Designer and builder of compression molds for composite structures installs seven-axis CNC deep-hole drilling and milling machine to improve productivity.
Strategic MOU initially introduces SikaBiresin CIM 120 and SikaBiresin CIM 80 to serve crucial composites market needs for 3D printing tooling, prototyping and more.
The Visa Cash App RB Formula 1 team is collaborating with Roboze to reduce weight and create parts with complex geometries via carbon fiber/PEEK.
In addition to its aesthetic qualities, the novel colored natural fiber is waterproof, 100% biodegradable and features enhanced manufacturing attributes thanks to Hypetex’s coloring process.
Steptics industrializes production of CFRP prostheses, enabling hundreds of parts/day and 50% lower cost.
A 10-year agreement between the partners’ Salt Lake City, Utah, facilities will build upon previous agreements for responsible environmental stewardship in industry.
Venox Systems was brought into the fold to deliver a 3D printed continuous carbon fiber/PEKK pedal for the TU Wien Racing Team that exceeded its aluminum counterpart.
Carbon fiber composites market report provides statistics, analyses and trends regarding 2023 demand in China and around the world.
The Visa Cash App RB Formula 1 team is collaborating with Roboze to reduce weight and create parts with complex geometries via carbon fiber/PEEK.
Steptics industrializes production of CFRP prostheses, enabling hundreds of parts/day and 50% lower cost.
Venox Systems was brought into the fold to deliver a 3D printed continuous carbon fiber/PEKK pedal for the TU Wien Racing Team that exceeded its aluminum counterpart.
Launched as part of a Clean Sky 2 program, a compound design — rotor, split fixed-wing, propulsive propellers — uses composites to cut fuel consumption and emissions by 20%.
CEAD Flexbot print cell demonstrations and industry presentations showcased the emerging options in 3D printing for polymers, composites and more at AES’ Akron facility.
Novel platform involving digital twin and human-robot collaboration succeeded in cutting a component from the 19th section of an A350 wing, highlighting its ability to enable composite structure recycling.
Increasingly, prototype and production-ready smart devices featuring thermoplastic composite cases and other components provide lightweight, optimized sustainable alternatives to metal.
CW explores key composite developments that have shaped how we see and think about the industry today.
Knowing the fundamentals for reading drawings — including master ply tables, ply definition diagrams and more — lays a foundation for proper composite design evaluation.
Performing regular maintenance of the layup tool for successful sealing and release is required to reduce the risk of part adherence.
With COVID in the past and passengers flying again, commercial aircraft production is ramping up. The aerocomposites supply chain is busy developing new M&P for an approaching next-generation aircraft program.
Electrification and a focus on sustainability lead to opportunities and innovations in composites, from battery enclosures to structural components and more.
KraussMaffei will explain in-situ polyurethane (PUR) overmolding of injection-molded and composite parts and the development of this technology over the last decade. Waruna Seneviratne, director of the Advanced Technologies Lab for Aerospace Systems (ATLAS), will discuss how aerospace and advanced air mobility (AAM) markets can capitalize on this high-rate manufacturing solution. Agenda: What is ColorForm: process, equipment and tooling Pros and cons of the technology High technology solution examples: ColorForm automotive Market references in automotive Demand for future commercial aviation and both AAM and urban air mobility (UAM) What aerospace can learn from automotive for addressing demand for high-rate manufacturing Technological advances enabling material and process improvements for the future Role of ATLAS manufacturing innovation center for promoting advanced manufacturing and workforce development Road map for certification through manufacturing demonstrations
Thermoplastic material systems have been used in aerospace for decades. Their use and adoption continues to grow and Trelleborg has been on the leading edge of development for many of these systems. In this webinar, Trelleborg will be presenting a range of topics from the use of in-situ, automated fiber placement of thermoplastics prepreg for structural and functional products to complex injection molding of thermoplastic interior pieces. It will explore some of the benefits these products provide and the potential for future growth and development. Agenda: Current state of thermoplastics in aerospace Thermoplastic composite use cases for high-performance electric motors and torque tubes Injection-molded thermoplastic interior pieces The future of potential for thermoplastic applications for aerospace
Find out how outsourced, costly tooling can be produced in-house to overcome bottlenecks, reduce costs and protect IP. Agenda: Explore durable casting materials that can be 3D-printed in complex designs Discover industry-proven Sika materials now available for high-speed, additive tooling Explore the benefits of thermoset molds that ensure uniform expansion, optimum bonding with the end part, as well as high durability
Explore next-gen composites engineering solutions in this webinar. Uncover the capabilities of Fives' Composite Optical Automated Surface Tracking (COAST) platform and Advanced Composites Environment Suite (ACES) software, optimizing design, production and quality control. Gain insights into how these end-to-end solutions enhance productivity and deliver measurable results. Join Fives to discover the transformative benefits of a fully-integrated digital solution for revolutionizing manufacturing processes. Agenda: Digital suite: CAD, CAM, robotic automated fiber placement (RAFP) and COAST Video demonstration Value propositions: maintenance and root cause analysis Product offerings (price, etc.) Customer use case
After having established a strong foundation in kinetic models in a previous webinar, part two delves into the exciting realm of machine learning and its transformative potential for composite manufacturing. While kinetic models have served the industry well, the growing complexity of composite manufacturing demands more sophisticated approaches. In this session, sensXPERT will explore innovative pathways to supercharge your production efficiency and enhance sustainability beyond the limits of traditional models. See how machine learning empowers composite manufacturers to achieve unprecedented accuracy in predicting key production parameters such as temperature, pressure and cure time. This translates to reduced cycle times and waste while increasing production throughput to maximize efficiency. SensXPERT will provide concrete examples and case studies demonstrating how to bridge the gap between meticulously-controlled laboratory experiments and the realities of the production floor, overcoming the limitations of kinetic models. Agenda: Define machine learning, its applications and their impact on composite manufacturing Explore real-world case studies in diverse composites manufacturing applications and how they exploit integration options Correlation analysis: uncovering hidden relationships between process parameters and product outcomes Time series analysis: forecasting production trends Anomaly detection: identifying irregularities
This webinar will cover a range of honeycomb products, how to best select the right honeycomb for particular applications and design guidelines for honeycomb-cored structures. Agenda: Honeycomb overview Configuration and applications General considerations and quality standards Methods and methodology for shaping core Core forming Stabilization CNC machining Case studies Cost progression
ILA Berlin brings the world's aerospace industry to the center of Europe every two years - next time from June 5 to 9, 2024.
The JEC Forum Southeast Asia is an event organised by JEC The JEC Forum Southeast Asia is organised on June 11 and 12, 2024, by JEC, in partnership with the Thai Composites Association (TCA), bringing together the composite materials community in Southeast Asia.
The 14th edition of the Graphene Conference will take place June 25-28, 2024, in Madrid, Spain. The international gathering includes thematic workshops, B2B networking and an Industrial Forum that dives into a variety of topics, including the latest developments in graphene production methods towards wide scale commercialization and examples of graphene in electronics, energy storage, aerospace and barrier applications.
The International Composites Summit (ICS) is renowned as the only solely focused UK event for professionals involved in the composites industry. ICS promises to be a unique platform for knowledge sharing, networking, and exploring the latest advancements in composite materials internationally, bringing people together to do business.
Thousands of people visit our Supplier Guide every day to source equipment and materials. Get in front of them with a free company profile.
Jetcam’s latest white paper explores the critical aspects of nesting in composites manufacturing, and strategies to balance material efficiency and kitting speed.
Arris presents mechanical testing results of an Arris-designed natural fiber thermoplastic composite in comparison to similarly produced glass and carbon fiber-based materials.
Cevotec, a tank manufacturer, Roth Composite Machinery and Cikoni, have undertaken a comprehensive project to explore and demonstrate the impact of dome reinforcements using FPP technology for composite tanks.
Initial demonstration in furniture shows properties two to nine times higher than plywood, OOA molding for uniquely shaped components.
The composite tubes white paper explores some of the considerations for specifying composite tubes, such as mechanical properties, maintenance requirements and more.
Foundational research discusses the current carbon fiber recycling landscape in Utah, and evaluates potential strategies and policies that could enhance this sustainable practice in the region.
Novel reinforcing patch uses braided sleeve to boost the load-carrying capacity of composite bolted joints.
Workforce pain points and various logistical challenges are putting operations resilience and flexibility to the test, but Industry 4.0 advancements could be the key to composites manufacturers’ transformation.
A fiberglass and carbon fiber composite wrap system enabled an Australian nickel mine to quickly repair a stainless steel ammonium sulphate feed tank and protect against future corrosion.
While the Composites Fabricating index still contracted in April, it continues to close in on a reading of 50, which indicates expansion.
Powered by an 85% air/15% pure polyimide aerogel, Blueshift’s novel material system protects structures during transient thermal events from -200°C to beyond 2400°C for rockets, battery boxes and more.
When you’re a tourist with a background in writing for manufacturing it’s impossible not to notice all of the ways in which composites have resulted in significant milestones in the U.S. — historically and in the present.
Themes at the forefront of JEC World 2024 included solutions for mobility applications and sustainable materials, technologies and processes for composites manufacturing.
CW technical editor Hannah Mason discusses trends seen at this year’s JEC World trade show, including sustainability-focused technologies and commitments, the Paris Olympics amongst other topics.
Automotive technology supplier Forvia shares sustainability goals and recent developments aimed at bio-based and recycled materials and ramping up hydrogen tank production for clean mobility.
Customer decarbonization goals demand supply chains with sustainable business practices. Here are four considerations for supporting those goals discussed at CW Tech Days: Sustainability.
Airbus subsidiary CTC uses new technology to measure energy use in machine components and processes to optimize equipment, production lines and guide decisions for future composites.
Three materials — bio-based carbon fibers, natural stone and biochar — act as an alternative to reinforced concrete in a house wall demonstrator in the DACCUS-Pre project.
CW’s editors are tracking the latest trends and developments in tooling, from the basics to new developments. This collection, presented by Composites One, features four recent CW stories that detail a range of tooling technologies, processes and materials.
The composites industry is increasingly recognizing the imperative of sustainability in its operations. As demand for lightweight and durable materials rises across various sectors, such as automotive, aerospace, and construction, there is a growing awareness of the environmental impact associated with traditional composite manufacturing processes.
In the Automated Composites Knowledge Center, CGTech brings you vital information about all things automated composites.
Closed mold processes offer many advantages over open molding. This knowledge center details the basics of closed mold methods and the products and tools essential to producing a part correctly.
CompositesWorld’s CW Tech Days: Infrastructure event offers a series of expert presentations on composite materials, processes and applications that should and will be considered for use in the infrastructure and construction markets.
Explore the cutting-edge composites industry, as experts delve into the materials, tooling, and manufacturing hurdles of meeting the demands of the promising advanced air mobility (AAM) market. Join us at CW Tech Days to unlock the future of efficient composites fabrication operations.
Thermoplastics for Large Structures, experts explored the materials and processing technologies that are enabling the transition to large-part manufacturing.
Explore the technologies, materials, and strategies that can help composites manufacturers become more sustainable.
A report on the demand for hydrogen as an energy source and the role composites might play in the transport and storage of hydrogen.
This collection features detail the current state of the industry and recent success stories across aerospace, automotive and rail applications.
This collection details the basics, challenges, and future of thermoplastic composites technology, with particular emphasis on their use for commercial aerospace primary structures.
This collection features recent CW stories that detail a range of tooling technologies, processes and materials.
Constructed of fire-retardant fiberglass-reinforced polyurethane walls and pultruded beams, the self contained living unit is designed to withstand extreme Antarctic weather conditions.
Fibreglass Developments Ltd. (Feilding, New Zealand) has manufactured a composite living module for Scott Base, New Zealand’s Antarctic research station. The company was contracted to build the first mobile habitat in a new, more durable construction design that is being trialed by research institute Antarctica New Zealand. The self-contained living unit is designed to withstand the extreme environment, which can experience conditions of 200 kilometers per hour winds and 60°C temperatures. Strength, rigidity and insulation were all taken into consideration for the design.
The team at Fibreglass Development prepare to send the “Big Green Box” on its journey. Source | Fibreglass Development Ltd.
According to Fibreglass Developments general manager Steve Bond, the design of the module, which is affectionately nicknamed the “Big Green Box,” was based on the company’s experience designing and building freezer bodies for trucks, and so is well-suited for travel across the icy landscape.
Measuring 8.2 meters by 3.2 meters by 2.7 meters, the habitat consists of fire-retardant, fiberglass-reinforced polyurethane walls and pultruded beams. For strength and rigidity, 150-millimeter-deep pultrusion is used throughout the construction. To provide stiffness, I-beams run across the diameter of each panel. Channels surround each panel, and were also doubled up to form the two main structural beams through the floor that attach to a 2.4-meter-wide mobile sled on-site. The beams carry the load from the outside walls to the sled and would also support the sled should it drop into a hollow when moving.
A peek inside the mobile Antarctic living unit. Source | Fibreglass Developments Ltd.
In between the beams and forming the bulk of the wall is PIR polyurethane, which provides insulation from both cold and sound. The exterior and interior face skins are a combination of chopped strand mat (CSM), biaxial and double bias fiberglass cloth laminated with fire retardant resins. The separate panels are bonded together with a combination of Plexus structural adhesive and hand lay of similar laminate to the linings.
Currently, many of the other buildings at Scott Base have been built using Polypanel, Ali skinned EPS. With the extreme temperature changes, these can be prone to movement, loosening riveted jointing systems until eventual failure. To prevent this, Fibreglass Developments’ Big Green Box is covered in a monolithic skin with no exposed joints.
MTorres seeks to enable next-gen aircraft and open new markets for composites with low-cost, high-permeability tapes and versatile, high-speed production lines.
Composite technologies are growing in use as suppliers continue efforts to meet more demanding requirements for EV battery enclosures.
Compared to legacy materials like steel, aluminum, iron and titanium, composites are still coming of age, and only just now are being better understood by design and manufacturing engineers. However, composites’ physical properties — combined with unbeatable light weight — make them undeniably attractive.
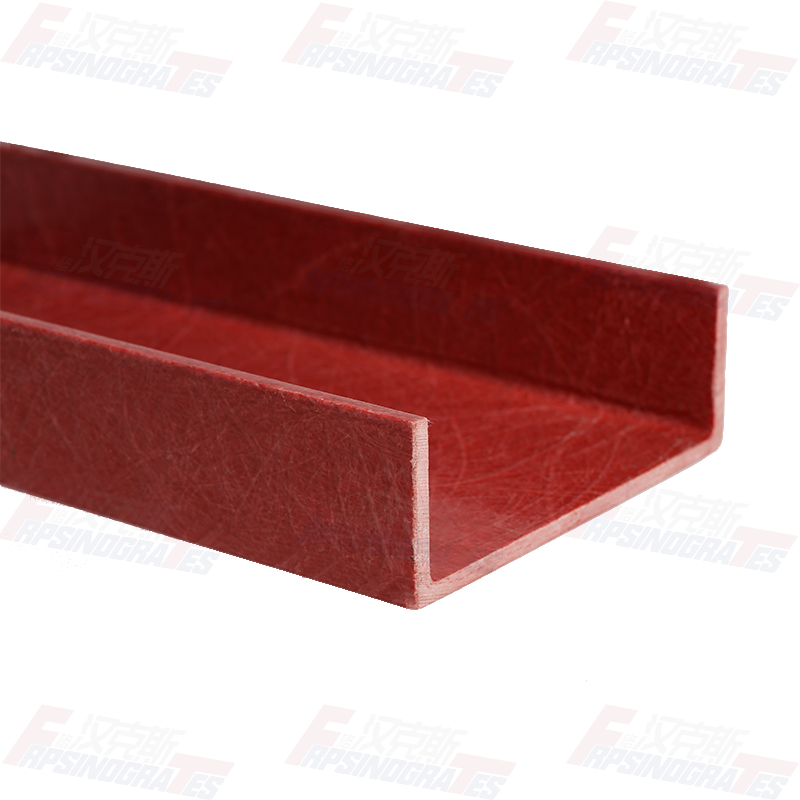
Fiberglass Channels CompositesWorld is the source for reliable news and information on what’s happening in fiber-reinforced composites manufacturing. About Us