Article by Erica K. Brockmeier Photos courtesy of Sagar Doshi | Photo illustration by Joy Smoker February 26, 2024
Whether you’re downloading a movie before your flight or making a FaceTime call from the park, our electronics work hard to meet our ever-increasing “need for speed.” Now, as researchers look toward a future with even faster transmission speeds, new devices will need materials and components that can handle the increased data rates and energy requirements. Bare Copper Ground Wire
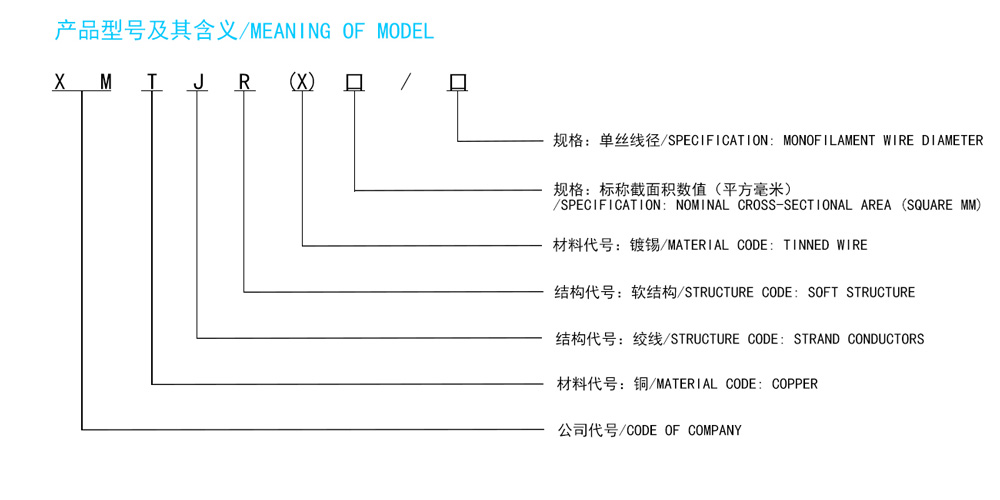
A new study conducted by researchers from the University of Delaware’s Center for Composite Materials (CCM) and DuPont Specialty Products now provides insights about one such composite material that can be used to make thin, flexible and durable circuit boards. Published in the journal ACS Applied Materials and Interfaces, this study describes how the components of the circuit boards can be more efficiently bound together and provides a framework for how to create new materials that are compatible with high-speed electronic applications.
The circuit boards used in this study are fabricated from thin sheets of copper foil laminated with polyimide, a high-performance polymer created by DuPont for electronic applications. The polyimide not only acts as the dielectric (or electric insulator) between each copper layer, but it also must maintain adhesion with the copper layers to ensure long-term durability.
In this study, the researchers were interested in gaining a fundamental understanding of the trade-offs between the effects of surface roughness on the transmission of electromagnetic waves and interfacial adhesion. This is especially crucial at the increased frequencies required for high-speed electronic devices.
“You can't get those transmission speeds unless the copper is smooth,” said Mark Lamontia, retired DuPont project manager and paper co-author. “But the smoother you make the copper, the adhesion between the copper and the polyimide gets tougher to achieve.”
To tackle this challenge, Lamontia reached out to Jack Gillespie, Donald C. Phillips Professor affiliated with the College of Engineering’s departments of Civil and Environmental Engineering, Electrical and Computer Engineering, Materials Science and Engineering, and Mechanical Engineering and the former director of CCM. Lamontia, who had worked with Gillespie and CCM on several other projects related to adhesion, wanted to tap into UD’s expertise once more so they could understand how to fabricate their final product more easily.
“DuPont was one of the founding members of our Industrial Consortium in 1978 and we have enjoyed working with Mark over the years,” Gillespie said. “It is very rewarding to translate industrial needs into fundamental research that is published in high impact factor journals. The success of our project was a team effort involving my research group at CCM with key DuPont scientists and engineers who were experts in materials, processing and characterization methods related to high speed electronic applications.”
The first step was to improve their procedure for measuring adhesion between the copper and the polyimide. To do this, the researchers developed a way to conduct the industry standard “peel test” (akin to pulling a piece of scotch tape from a surface) and collecting analytical chemistry data from the failure surface. This enabled them to gain deeper insights on the adhesion mechanisms between copper and polyimide through a process known as a failure analysis.
“This copper film and the polyimide bound to it is only 30 to 50 microns thick, so it’s a really thin and delicate material,” said Sagar Doshi, CCM associate scientist and first author of this paper. "For testing these highly specialized materials, we had to innovate and modify the typically used experimental setup and carefully preserve the tested samples for detailed failure analysis using different materials characterization techniques."
Armed with an improved way to measure adhesion, the researchers then used this technique to study the adhesion mechanism between the copper and the polyimide. What they found was surprising: As the highly viscous polymer infiltrated around the rough nodules on the copper’s surface, the compression molded polyimide/copper laminate formed a mechanical interlock.
“This is the first time in this industry that I've seen this happen,” added Lamontia about the evidence for this mechanical interlocking mechanism in this type of laminate material.
What was additionally surprising, added Doshi, is that the mechanical interlock was due to the overall structure, or topography, of those copper nodules.
“Once the polyimide goes into certain regions, it's locked in there. When we peel it off, it has to break through the copper in order to come off,” Doshi said. “Another key aspect of the study was the process modeling of the mechanical interlocking mechanism, where we predicted polymer infiltration into the surface pores as a function of process temperature, pressure and pore size. In this paper, we show that, when the material is optimized for mechanical interlocking, the peel strength increases by a factor of three.”
Not only did the researchers demonstrate the role of mechanical interlocking for these materials, they can now use this thorough mechanistic understanding of adhesion to study how different factors and experimental conditions impact the mechanical interlocking between polyimide and copper. This will allow researchers across the field to continue developing innovative materials that can meet the needs of current and future high-speed electronics.
This study is also a great example of how impactful research can be when industries and universities work together.
“At DuPont, we want to make this method be part of our everyday operation, because we have all kinds of programs where we have to bond copper to other materials,” Lamontia said. “We need new materials to achieve performance at higher frequencies, and that need is just going to increase more and more.”
“The needs of the electronic industry and the consumer are continuously increasing, and there’s always room to improve performance,” Doshi said. “In this study, we were able to use basic science to solve a complex problem for the industry. And now, our approach can be applied to other problems where we need to understand the mechanics that affect the properties and the performance. Then, once you understand that, you can plan, improve and optimize.”
This project was funded by DuPont Specialty Materials, USA.
The complete list of co-authors includes Sagar Doshi, Alexander Barry*, Alexander Schneider**, Nithin Parambil, and John Gillespie Jr. from the University of Delaware and Catherine Mulzer, Mobin Yahyazadehfar, Aref Samadi-Dooki, Benjamin Foltz, Keith Warrington, Richard Wessel, Lei Zhang, Christopher Simone, Gregory Blackman, and Mark Lamontia from DuPont Specialty Materials.
*Barry worked in CCM as a high school student intern; he is now a first year student at Cornell studying mechanical engineering.
**Schneider earned his master’s and bachelor’s degrees in mechanical engineering at the University of Delaware as part of a 4+1 program; he recently began working at Accudyne.
Article by Erica K. Brockmeier
Article by Karen B. Roberts
Contact us at ocm@udel.edu
Contact us at 302-831-NEWS or visit the Media Relations website

Tinned Copper Wind Power Busbar Office of Communications & Marketing 105 E. Main St. Newark, DE 19716 ocm@udel.edu Phone: 302-831-2792