Anyone involved in the metal fabrication sector of manufacturing over the last 25 years has seen many changes. High-capacity plasma machines replaced oxyfuel cutting machines. CO2 lasers replaced punching machines. Now fiber lasers are replacing CO2 lasers.
With each change, you have sought to improve performance. The move to fiber laser cutting is no different. However, in the new rush to install these super-fast cutting machines, which are almost always accompanied by automated storage and retrieval towers to make the most of the equipment’s cutting capacity, you might be discovering that navigating such an implementation project is more than you expected. Robot Encoder Cable
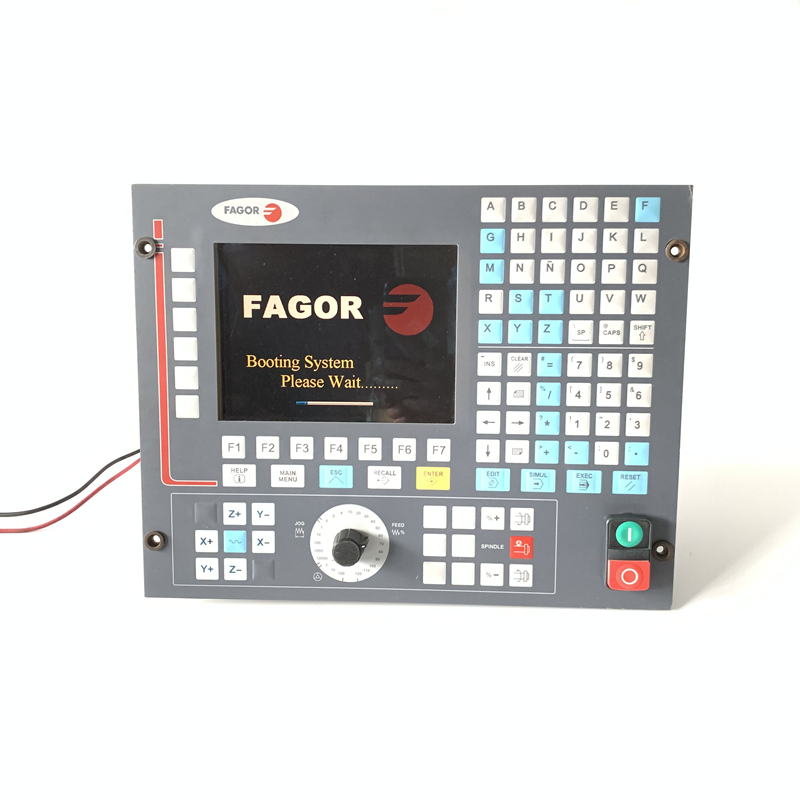
Help is available. Addressing these seven key areas can ensure that you don’t have anticipated return on investment (ROI) replaced by frustration about that capital investment.
This is where success begins. Solving complex shop floor production challenges has always been a team effort. Technology can’t change that.
Big technology implementations are demanding. When investing huge sums of money in fiber laser cutting machines with elaborate material management setups, you expect an advantageous ROI. Having a team with the right combination of expertise helps to drive the machine and achieve production goals. Without collaboration, machine performance risks becoming subpar, and any advancement stalls.
On both the vendor and customer side, each knows a different part of the path to success. It is essential they leverage that knowledge productively. Having a testing component covering the vendor’s technology and your production processes adds great value. After all, the ultimate goal is actually equal parts good ROI and finding a sustainable blanking operation.
Machine manufacturers are designing and building state-of-the-art equipment. To fit the ever-changing needs of fabricators, these modern marvels must have scalable components and technology that allow for customization and future business growth. With today’s manufacturing and fabrication environment shifting so quickly, you should be expecting machine manufacturers to be regularly prototyping and testing new equipment and techniques, and that is an excellent development.
Meanwhile, machine programmers and management teams need to own the fact that they are not just part of the process, but they likely are the process. Your shop’s knowledge and skill drive machine success, not the other way around.
Identify where your daily shop floor challenges lie. Know what your shop’s current top capacity is before the fiber laser arrives, and to prepare for the arrival of the new equipment, increase that current capacity tenfold.
With that in mind, plan a hypothetical run at 10 times your current speed. Plan each step of the work flow. Walk it through your operation. Document what happens on paper.
What might you find? Increasing speed at one workstation can cause issues such as:
Bottlenecks at the front end. Because of projected processing speed, material backups at the front end for programming and prenesting are likely. In fact, without proper organization, backups are inevitable.
Safety practices get overlooked. Material moving at such high speeds can cause personnel to focus on staying ahead rather than staying safe.
Bottlenecks at the back end. Material gets loaded into the fiber laser, cut, and sent downstream. Without proper planning, resources may not be available to denest and transport parts coming off the fiber laser, or the downstream processes in the shop may not be ready, which could result in work-in-process piling up in the aisles.
Throughout the 10-times test, identify, document, communicate, and begin to solve the issues at-hand. Many resolutions to issues will appear as a result of the enhanced information flow about the fabrication process.
Also, prioritizing how information is organized and distributed from initial order through shipping can be a critical step. The key area requiring focus often is how work flow is presented to operations.
Software providers involved in such a technology implementation need to see the big picture and the precise details of fabrication. This includes quoting, importing of files, nesting, creating NC, posting to the machine, processing options, handling parts, finishing, and managing remnants and stock. Software providers should consider mapping a project as part of the consultative process.
Interpreting test results realistically will lead to more practical expectations of any new technology, including fiber laser and the accompanying automated material handling capabilities. Consider the following as your team interprets the many challenges revealed during testing:
Again, communication is important. Both management and production teams need to have a solid sense of the fiber laser’s operational impact and production expectations; ROI expectation; specific challenges to all expectations; potential ways to overcome those challenges; internal and external resources; and an agreed-upon timeline for all of this to happen.
5: Recognize when you need outside expertise.
Knowledge drives success. Once you recognize that your team may not know how every feature of the technology investment can be applied and optimized, you need to reach out for help. Specific outside expertise geared toward production gains in automation is an option, and a single investment can drive years of measurable results.
In the software alone, one or two features can have a powerful impact:
Key practice No. 1: Integrate and mix work orders to increase productivity and capacity, driving ROI.
Key practice No. 2: Optimize nesting until you can’t optimize any more. For instance, using various lead-in locations increases yield and throughput. (Lead-in placement can require more space between parts, causing each part to require a bigger footprint on the sheet of material. When lead-ins are managed properly, this footprint is the smallest it can possibly be.)
Key practice No. 3: Optimize nesting by varying tabbing methods and types to increase yield and decrease production time. For example, tabs can be managed so that you can completely eliminate the need for time-consuming additional steps like grinding.
Key practice No. 4: Investigate machine motion options that may greatly increase productivity and throughput. Imagine a part tips up during cutting and collides with the cutting head, which is going to shut down the laser cutting machine and create unwanted downtime. Good NC code prevents those tipped-up parts.
Key practice No. 5: Review scrap-cutting practices annually. Simple process changes, such as trimming remnants to more manageable sizes either for recycling or for storage, can reduce waste.
Key practice No. 6: Next-process labeling approaches and procedures can greatly increase capacity and productivity.
In most cases, some level of customization is required if your fab shop wants to achieve Industry 4.0 automation. Customization approaches, such as plug-in packages that tailor the machine-driven software to your unique production environment, can be exceedingly helpful from both an investment and training perspective. Check with your fiber laser manufacturer or software provider about customized automation “smart” packages or bundles of features specifically chosen and programmed to optimize your fiber laser cutting cell.
Tracking and reporting are critical, even after goals are met and challenges conquered. Without quantifying each step in the process, it’s nearly impossible to build out the program over time. Once the implementation team has achieved one ROI benchmark, it’s time to set another.
As the fiber laser with its automation tower becomes less novel and more of a fixture in your company, tracking becomes even more important. New technology will come along to challenge its efficiency and capacity. Having full knowledge of how the fiber laser cutting cell performs via reporting history is the only way to know if that next new machine is worth your attention.
Brian Blair is director, west, Cornel Warren is director, marketing and inside sales, and Suzanne Warden is marketing coordinator, SigmaTEK Systems, 1445 Kemper Meadow Drive, Cincinnati, OH 45240, 513-674-0005, www.sigmanest.com.
For more in-depth coverage of these topics, listen to Blair’s webinar at www.sigmanest.com/webinars/. He can be reached at brian.blair@sigmanest.com.
See More by Brian Blair
See More by Cornel TerreBlanche
See More by Suzanne Warden
Read more from this issue
Find The Fabricator on Facebook
Find The Fabricator on X
The Fabricator is North America's leading magazine for the metal forming and fabricating industry. The magazine delivers the news, technical articles, and case histories that enable fabricators to do their jobs more efficiently. The Fabricator has served the industry since 1970.
Easily access valuable industry resources now with full access to the digital edition of The Fabricator.
Easily access valuable industry resources now with full access to the digital edition of The Welder.
Easily access valuable industry resources now with full access to the digital edition of The Tube and Pipe Journal.
Easily access valuable industry resources now with full access to the digital edition of The Fabricator en Español.
Jeff Cupples, the president of Jackson, Tenn.-based Cupples J&J Company, discusses his experience with laser cutting machines and...
© 2024 FMA Communications, Inc. All rights reserved.

Pro Face Touch Screen Not yet registered? Sign up