The facility in Andover houses a microelectronics and power device engineering team of 30 engineers and the cleanroom production facility houses a further 20 persons in a highly automated production facility.
The company is to expand both the staff and facilities this month to include a volume surface mount SMT PCBA production facility to feed into the microelectronics facility. This will be both Chip-on-board (COB) assemblies going into the cleanroom for die assembly and also PCBA’s being assembled using devices packaged in the cleanroom to give CIL’s customers an advanced UK assembly facility. China Smd Board Suppliers
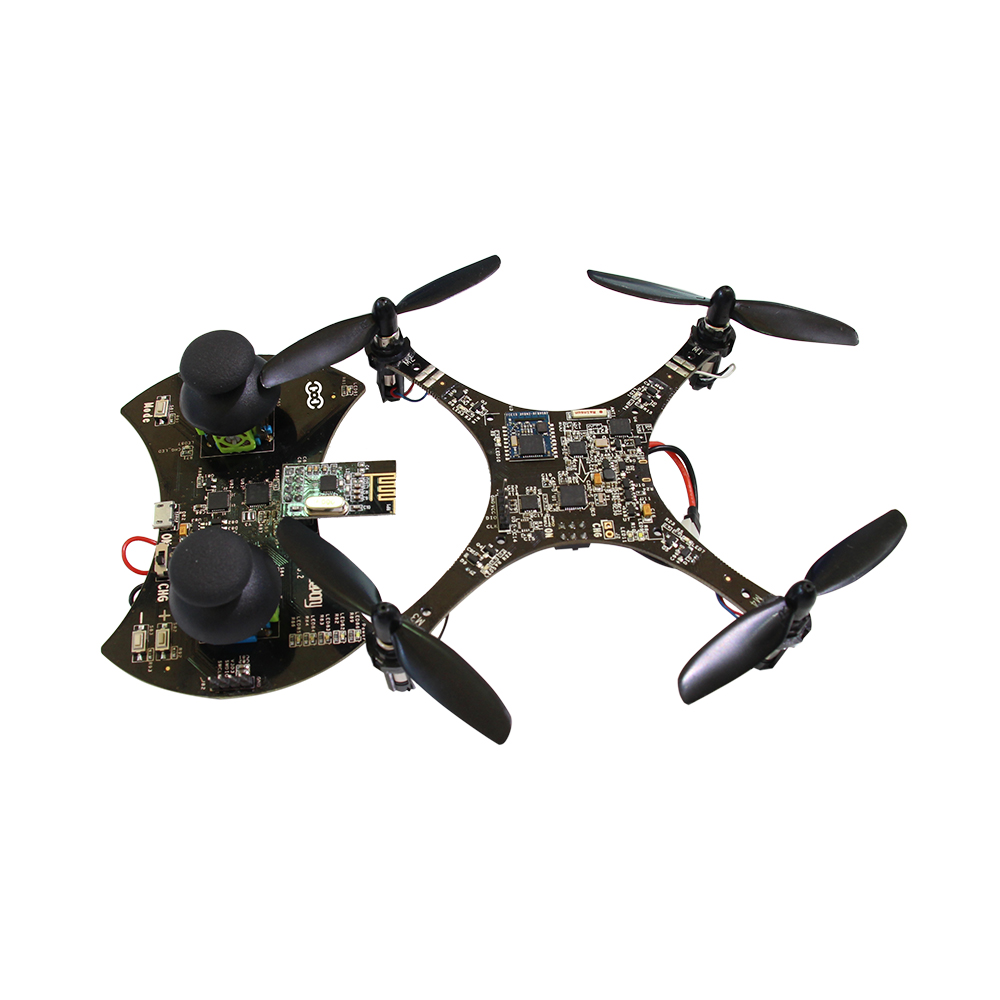
Contained within the 15,000sq ft ISO7 cleanroom is a segregated room with specialist LED lighting to house CIL’s wafer dicing capability complete with DISCO DAD3361 dicing saw, water treatment and wafer mounting equipment.
CIL is now receiving custom die from its customers, dicing and then providing full assembly services either into custom packaging solutions or bespoke devices for SMT assembly within CIL.
Further equipment already on order and due to be delivered in 2023 includes a DATACON 2200EVO Auto die bonder, bringing the number of auto die bonders to five, as well as the ninth ASM 589 Auto Al wedge wire bonder and fifth Nordson Asymtek S2-920 Auto dispense system.
CIL says it is now on an almost permanent recruitment drive for engineers, technicians and staff to ensure that the UK has a premium world class semiconductor packaging facility to allow its customer to develop and manufacture in the UK.
The 15,000sq ft ISO7 cleanroom is stage 1 of a 5 stage fit out on the new premises and stage 2 comes on-line in Nov 2023. Th facility is in addition to CIL’s existing CIL House facility which houses a dedicated prototype SMT PCBA line and a further five production SMT PCBA lines for small to medium complex PCBA assemblies. It now means CIL is able to offer a dedicated prototype SMT line, five lines for small to medium volumes and in the BP2 facility, volume production capability.
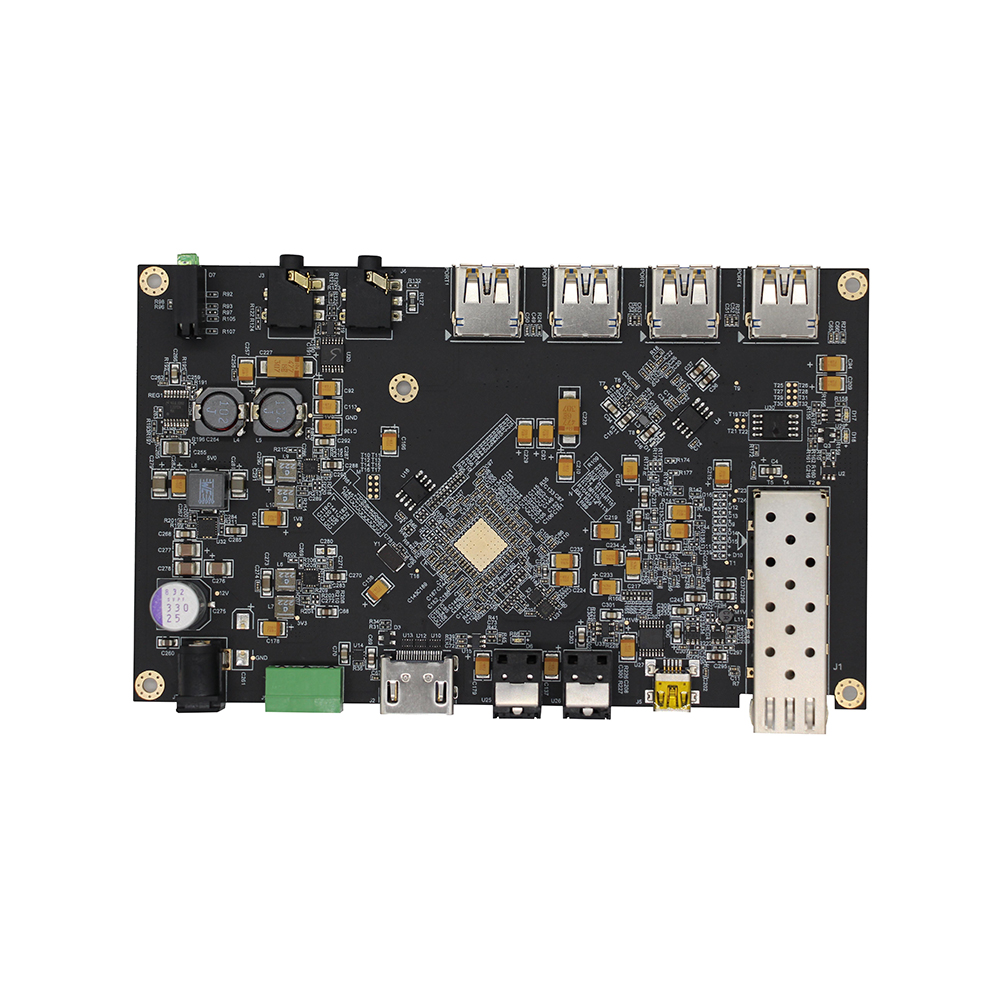
China Smd Circuit Suppliers All material on this site Copyright © 2022 European Business Press SA. All rights reserved.