Global Ammonium Polyphosphate Market 2023-2030 Adaptive Research Report covers a wide range of factors, including detailed information on Types [APP I, APP II, Others], Applications [Liquid Fertilizer Industry, Flame Retardant Industry, Others], customer needs, wants, and expectations, as well as competitor analysis, Ammonium Polyphosphate market size, analyzing industry trends and growth potential. The purpose of Ammonium Polyphosphate market research is to solve complex questions around Developing New Product, Latest Technology development, Emerging Market Exploration, Technology Scouting/Landscaping and MandA (Mergers and acquisitions in strategic management), GTM Strategy (go-to-market strategy - target market profiles, a marketing plan, and a concrete sales and distribution strategy) and Competitive Landscape to stay ahead of the product life cycle and innovation curve. [116 No. of Pages]
Get a Sample PDF of report - https://www.researchreportsworld.com/enquiry/request-sample/18471797 Flame Retardant For Polypropylene
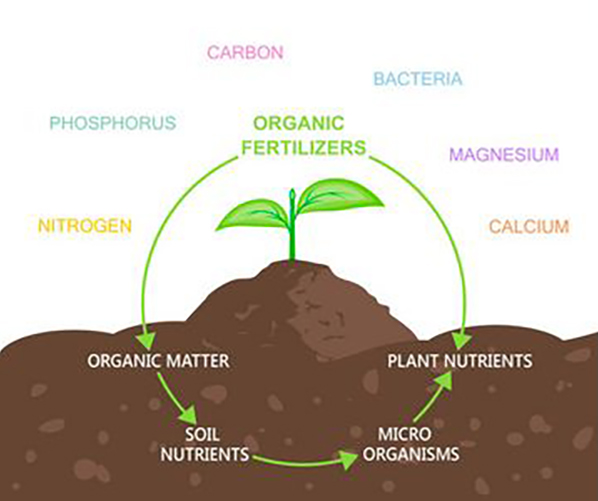
Moreover, Ammonium Polyphosphate market research deeply focuses on geographical segmentation such as North America, Europe, Asia-Pacific, South America, Middle East and Africa, and Others. As well as in this research report focuses on industry scope and objectives which helps to find the conclusion.
This research report is helpful by businesses, entrepreneurs, organizations and startups to gain insights into Ammonium Polyphosphate industry, target markets, and consumers. These reports can help make important decisions like creating new products, planning advertising, and expanding into new markets. Also, investors and experts might use these reports to decide where to invest, investment decisions and financial analysis. Also, this research report is based on experimental research. Experimental research gives you the advantage of controlling extraneous variables and manipulating one or more factors that influences the process being implemented.
Clariant Perimeter Solutions Nutrien JLS Chemical Budenheim Changfeng Chemical Sanwa Flame Retardant Technology Jingdong Chemical Kingssun Group Lanyang Chemical Zhejiang Longyou GD Chemical Shian Chem Chuanhong Phosphorus Chemical Plant Food Company
Get a Sample Copy of the Ammonium Polyphosphate Market Report 2023-2030
The global Ammonium Polyphosphate market was valued at USD million in 2020, and MAResearch analysts predict the global market size will reach USD million by the end of 2030, growing at a CAGR of between 2021 and 2030.
Since the COVID-19 virus outbreak in December 2019, the disease has spread to all countries and territories around the world and 2 international conveyances. The global impacts of COVID-19 are already starting to be felt, and will significantly affect this industry in 2020 and 2021.
This report analyses the impact of COVID-19 on this industry. COVID-19 can affect the global market in 3 ways: by directly affecting production and demand, by creating supply chain and market disruption, and by its financial impact on enterprises and financial markets.
This report provides detailed historical analysis of global market for Ammonium Polyphosphate from 2017-2020, and provides extensive market forecasts from 2021-2030 by region/country and subsectors. It covers the sales volume, price, revenue, gross margin, historical growth and future perspectives in the Ammonium Polyphosphate market.
Market segmentation has long been a fundamental strategy for businesses looking to understand their audience better. Ammonium Polyphosphate Market Segmentation, a cutting-edge methodology that takes market research to the next level. In this section, the report includes different segmentations such as market types, applications, geographical areas covered, and more.
Enquire before purchasing this report- https://www.researchreportsworld.com/enquiry/pre-order-enquiry/18471797
Liquid Fertilizer Industry Flame Retardant Industry Others
APP I APP II Others
Regional Areas Covered in Ammonium Polyphosphate Market Report
Geographic Scope: This market research report focuses on the global market landscape. We will examine regional variations and trends, but the primary scope is international in nature.
Industry Focus: The research primarily centers around the [Chemical and Material], with a keen focus on understanding market dynamics, emerging trends, key players, and factors influencing the industry's growth.
Time Frame: The study covers historical data analysis, current market dynamics, and future projections. The historical data spans the past five years, while the forecast period extends to [2023-2030].
Long-term Growth Planning: Developing strategies and tactics for sustained growth and competitiveness in the market.
Innovation Curve Analysis: Assessing where a company falls on the innovation curve to determine its innovation strategy and potential disruption.
COVID-19's Impact: The pandemic disrupted supply chains, shuttered businesses, and changed how we work and live. It led to economic ups and downs, with some industries like healthcare and tech thriving while others, like travel and hospitality, struggling. Governments worldwide implemented stimulus packages to support their economies, influencing market dynamics. People's behavior shifted, with online shopping and remote work becoming the norm. These changes continue to reshape markets as businesses adapt to new demands and uncertainties.
Russia-Ukraine War's Influence: The conflict's impact on markets is complex. Energy markets felt ripples due to Russia's role as a major gas supplier, causing fluctuations in prices. Geopolitical tensions also affected global trade and investment, leading to increased uncertainty for businesses. Sanctions against Russia impacted various industries, and geopolitical instability introduced an element of risk for investors. Understanding and managing these interconnected challenges is vital for businesses and investors as they navigate an evolving market landscape shaped by both the pandemic and geopolitical events.
TO KNOW HOW COVID-19 PANDEMIC AND RUSSIA UKRAINE WAR WILL IMPACT THIS MARKET - REQUEST SAMPLE
In the world of business, we encounter two critical forces: market drivers and restraints
Market drivers are like wind in the sails of a business. They are the positive factors that push industries forward. It includes, incorporating cutting-edge AI technology, new product sets a benchmark in efficiency and performance in the Chemical and Material sector, new technologies, rising customer demands, friendly government policies, globalization, or groundbreaking innovations.
These are the challenges and obstacles that slow down progress. Economic downturns, pesky regulations, and unexpected hurdles are common restraints.
Purchase this report (2500 USD for a single-user license): https://www.researchreportsworld.com/purchase/18471797
Table of Contents Chapter 1 Ammonium Polyphosphate Market Overview 1.1 Ammonium Polyphosphate Definition 1.2 Global Ammonium Polyphosphate Market Size Status and Outlook (2015-2030) 1.3 Global Ammonium Polyphosphate Market Size Comparison by Region (2015-2030) 1.4 Global Ammonium Polyphosphate Market Size Comparison by Type (2015-2030) 1.5 Global Ammonium Polyphosphate Market Size Comparison by Application (2015-2030) 1.6 Global Ammonium Polyphosphate Market Size Comparison by Sales Channel (2015-2030) 1.7 Ammonium Polyphosphate Market Dynamics (COVID-19 Impacts) 1.7.1 Market Drivers/Opportunities 1.7.2 Market Challenges/Risks 1.7.3 Market News (Mergers/Acquisitions/Expansion) 1.7.4 COVID-19 Impacts on Current Market 1.7.5 Post-Strategies of COVID-19 Outbreak Chapter 2 Ammonium Polyphosphate Market Segment Analysis by Player 2.1 Global Ammonium Polyphosphate Sales and Market Share by Player (2018-2020) 2.2 Global Ammonium Polyphosphate Revenue and Market Share by Player (2018-2020) 2.3 Global Ammonium Polyphosphate Average Price by Player (2018-2020) 2.4 Players Competition Situation and Trends 2.5 Conclusion of Segment by Player Chapter 3 Ammonium Polyphosphate Market Segment Analysis by Type 3.1 Global Ammonium Polyphosphate Market by Type 3.1.1 APP I 3.1.2 APP II 3.1.3 Others 3.2 Global Ammonium Polyphosphate Sales and Market Share by Type (2015-2020) 3.3 Global Ammonium Polyphosphate Revenue and Market Share by Type (2015-2020) 3.4 Global Ammonium Polyphosphate Average Price by Type (2015-2020) 3.5 Leading Players of Ammonium Polyphosphate by Type in 2020 3.6 Conclusion of Segment by Type Chapter 4 Ammonium Polyphosphate Market Segment Analysis by Application 4.1 Global Ammonium Polyphosphate Market by Application 4.1.1 Liquid Fertilizer Industry 4.1.2 Flame Retardant Industry 4.1.3 Others 4.2 Global Ammonium Polyphosphate Revenue and Market Share by Application (2015-2020) 4.3 Leading Consumers of Ammonium Polyphosphate by Application in 2020 4.4 Conclusion of Segment by Application Chapter 5 Ammonium Polyphosphate Market Segment Analysis by Sales Channel 5.1 Global Ammonium Polyphosphate Market by Sales Channel 5.1.1 Direct Channel 5.1.2 Distribution Channel 5.2 Global Ammonium Polyphosphate Revenue and Market Share by Sales Channel (2015-2020) 5.3 Leading Distributors/Dealers of Ammonium Polyphosphate by Sales Channel in 2020 5.4 Conclusion of Segment by Sales Channel Chapter 6 Ammonium Polyphosphate Market Segment Analysis by Region 6.1 Global Ammonium Polyphosphate Market Size and CAGR by Region (2015-2030) 6.2 Global Ammonium Polyphosphate Sales and Market Share by Region (2015-2020) 6.3 Global Ammonium Polyphosphate Revenue and Market Share by Region (2015-2020) 6.4 North America 6.4.1 North America Market by Country 6.4.2 North America Ammonium Polyphosphate Market Share by Type 6.4.3 North America Ammonium Polyphosphate Market Share by Application 6.4.4 United States 6.4.5 Canada 6.4.6 Mexico 6.5 Europe 6.5.1 Europe Market by Country 6.5.2 Europe Ammonium Polyphosphate Market Share by Type 6.5.3 Europe Ammonium Polyphosphate Market Share by Application 6.5.4 Germany 6.5.5 UK 6.5.6 France 6.5.7 Italy 6.5.8 Russia 6.5.9 Spain 6.6 Asia-Pacific 6.6.1 Asia-Pacific Market by Country 6.6.2 Asia-Pacific Ammonium Polyphosphate Market Share by Type 6.6.3 Asia-Pacific Ammonium Polyphosphate Market Share by Application 6.6.4 China 6.6.5 Japan 6.6.6 Korea 6.6.7 India 6.6.8 Southeast Asia 6.6.9 Australia 6.7 South America 6.7.1 South America Market by Country 6.7.2 South America Ammonium Polyphosphate Market Share by Type 6.7.3 South America Ammonium Polyphosphate Market Share by Application 6.7.4 Brazil 6.7.5 Argentina 6.7.6 Colombia 6.8 Middle East and Africa 6.8.1 Middle East and Africa Market by Country 6.8.2 Middle East and Africa Ammonium Polyphosphate Market Share by Type 6.8.3 Middle East and Africa Ammonium Polyphosphate Market Share by Application 6.8.4 UAE 6.8.5 Saudi Arabia 6.8.6 South Africa 6.9 Conclusion of Segment by Region Chapter 7 Profile of Leading Ammonium Polyphosphate Players 7.1 Clariant 7.1.1 Company Snapshot 7.1.2 Product/Service Offered 7.1.3 Business Performance (Sales, Price, Revenue, Gross Margin and Market Share) 7.1.4 COVID-19 Impact on Clariant 7.2 Perimeter Solutions 7.3 Nutrien 7.4 JLS Chemical 7.5 Budenheim 7.6 Changfeng Chemical 7.7 Sanwa Flame Retardant Technology 7.8 Jingdong Chemical 7.9 Kingssun Group 7.10 Lanyang Chemical 7.11 Zhejiang Longyou GD Chemical 7.12 Shian Chem 7.13 Chuanhong Phosphorus Chemical 7.14 Plant Food Company Chapter 8 Upstream and Downstream Analysis of Ammonium Polyphosphate 8.1 Industrial Chain of Ammonium Polyphosphate 8.2 Upstream of Ammonium Polyphosphate 8.2.1 Raw Materials 8.2.2 Labor Cost 8.2.3 Manufacturing Expenses 8.2.4 Manufacturing Cost Structure 8.2.5 Manufacturing Process 8.3 Downstream of Ammonium Polyphosphate 8.3.1 Leading Distributors/Dealers of Ammonium Polyphosphate 8.3.2 Leading Consumers of Ammonium Polyphosphate Chapter 9 Development Trend of Ammonium Polyphosphate (2021-2030) 9.1 Global Ammonium Polyphosphate Market Size (Sales and Revenue) Forecast (2021-2030) 9.2 Global Ammonium Polyphosphate Market Size and CAGR Forecast by Region (2021-2030) 9.3 Global Ammonium Polyphosphate Market Size and CAGR Forecast by Type (2021-2030) 9.4 Global Ammonium Polyphosphate Market Size and CAGR Forecast by Application (2021-2030) 9.5 Global Ammonium Polyphosphate Market Size and CAGR Forecast by Sales Channel (2021-2030) Chapter 10 Appendix 10.1 Research Methodology 10.2 Data Sources 10.3 Disclaimer 10.4 Analysts Certification
Research Reports World is the credible source for gaining the market reports that will provide you with the lead your business needs. At Research Reports World, our objective is providing a platform for many top-notch market research firms worldwide to publish their research reports, as well as helping the decision makers in finding most suitable market research solutions under one roof. Our aim is to provide the best solution that matches the exact customer requirements. This drives us to provide you with custom or syndicated research reports.
Website:https://www.researchreportsworld.com/
Industrial Cooling Tower Market Analysis Research Report 2023-2030
Mobile Point-of-Sale Market Size, Share, Growth | Research Report [2030]
Water Wood Coating Market Size and Growth | Forecast Report 2023-2030
Big Data as a Service Market Size, Share| Analysis Report, 2030
High Security Locks Market Size, Trends and Opportunities, 2023-2030
Low-Code Application Development Platform Market Size, Share | Growth, Report [2023-2030]
[Latest News] Ship Repair and Maintenance Services Market Size and Analysis Report 2023-2030 | 125 Pages Report
Atorvastatin Calcium Market 2023-2030 [Adaptive Report] Geographical Analysis and Industry Scope
Mountain Bike (MTB) Trials Market Size, Trends and Opportunities, Research Report 2023-2030
[Latest News] Dairy Ingredients Market Size and Share, Forecast Report 2023-2030
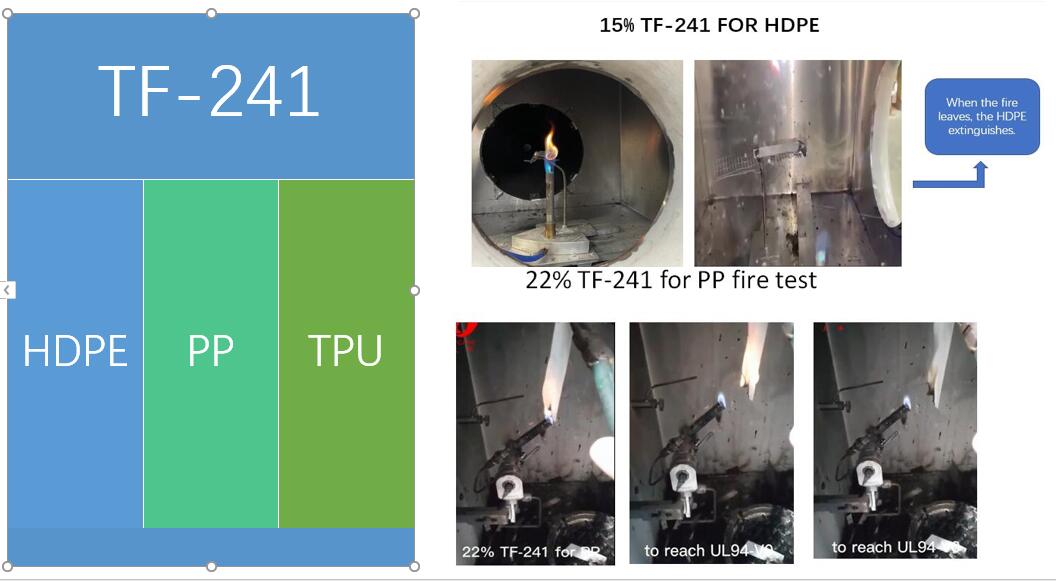
Ammonium Polyphosphate Fire Retardant © 2023 Benzinga.com. Benzinga does not provide investment advice. All rights reserved.