The Colonial Pipeline tank farm along I-40 in Greensboro (Photo: Clayton Henkel)
State regulators have cited Colonial Pipeline for discharging MTBE, a toxic gasoline additive, at levels 312% above its permit limit from the company’s tank farm in Greensboro. It is the third such violation in less than 18 months. 304 Square Tube
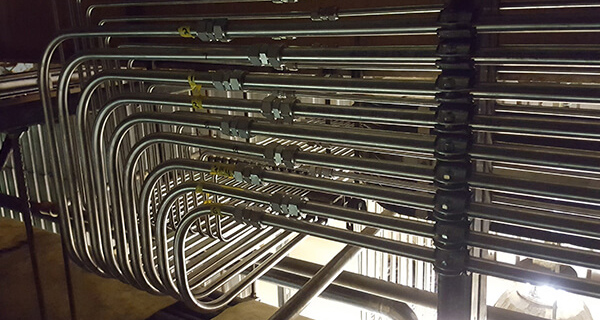
The most recent exceedances occurred in February 2023 and were included in the EPA’s latest compilation of violations, available through ECHO-Notify, a free email service. Previous violations happened in February and March 2022, state records show.
MTBE is a flammable liquid that was widely used as an additive for unleaded gasoline. Chronic exposure to MTBE can cause dizziness, irritate the throat, cause headaches and nausea, and harm the liver and kidneys. The compound has been found to cause cancer in animals, but it’s uncertain if that effect extends to humans.
Colonial’s water quality permit limits the amount of MTBE that can be discharged at 19 parts per billion, both as a daily maximum and monthly average. In February 2023, the daily maximum reached 78.3 ppb — more than 300% above the allowable maximum. Likewise, the monthly average of 35.5 ppb exceeded the permit limit, state records show.
In February 2022, the daily maximum reached 45 ppb, more than 200% legally allowed. Lower levels were recorded in March 2022, but still above the permit limit.
The discharge flows through Outfall No. 4 on Colonial property and enters a catchment pond that drains to the East Fork of the Deep River. Urban pollution has already damaged aquatic habitat in that portion of the East Fork of Deep River — from near the Piedmont International Airport, and south past the Colonial tank farm — earning it a place on the federal list of impaired waters.
Farther downstream, the main branch of the Deep River is the drinking water supply for the City of Sanford.
Colonial Pipeline officials believe the source of the contamination is a 25-year-old groundwater plume upstream of Outfall No. 4, state records show. MTBE clings to water, and unlike gasoline, which usually spreads slowly, it “moves rapidly with groundwater and can render groundwater unpotable at low levels,” according to the EPA. The company installed a groundwater treatment system in June 2022.
Now Colonial is considering installing an aeration unit at the catchment pond to remove the MTBE before it reaches the outfall.
There have been 12 reported petroleum spills at the tank farm since the 1980s, according to state records.
MTBE has contaminated groundwater and drinking water supplies throughout the U.S., prompting many states to ban its use. North Carolina lawmakers banned the use of MTBE in gasoline in 2008. However, it is legal to transport fuel containing MTBE through the state, such as via pipeline, rail or truck.
by Lisa Sorg, NC Newsline July 10, 2023
by Lisa Sorg, NC Newsline July 10, 2023
State regulators have cited Colonial Pipeline for discharging MTBE, a toxic gasoline additive, at levels 312% above its permit limit from the company’s tank farm in Greensboro. It is the third such violation in less than 18 months.
The most recent exceedances occurred in February 2023 and were included in the EPA’s latest compilation of violations, available through ECHO-Notify, a free email service. Previous violations happened in February and March 2022, state records show.
MTBE is a flammable liquid that was widely used as an additive for unleaded gasoline. Chronic exposure to MTBE can cause dizziness, irritate the throat, cause headaches and nausea, and harm the liver and kidneys. The compound has been found to cause cancer in animals, but it’s uncertain if that effect extends to humans.
Colonial’s water quality permit limits the amount of MTBE that can be discharged at 19 parts per billion, both as a daily maximum and monthly average. In February 2023, the daily maximum reached 78.3 ppb — more than 300% above the allowable maximum. Likewise, the monthly average of 35.5 ppb exceeded the permit limit, state records show.
In February 2022, the daily maximum reached 45 ppb, more than 200% legally allowed. Lower levels were recorded in March 2022, but still above the permit limit.
The discharge flows through Outfall No. 4 on Colonial property and enters a catchment pond that drains to the East Fork of the Deep River. Urban pollution has already damaged aquatic habitat in that portion of the East Fork of Deep River — from near the Piedmont International Airport, and south past the Colonial tank farm — earning it a place on the federal list of impaired waters.
Farther downstream, the main branch of the Deep River is the drinking water supply for the City of Sanford.
Colonial Pipeline officials believe the source of the contamination is a 25-year-old groundwater plume upstream of Outfall No. 4, state records show. MTBE clings to water, and unlike gasoline, which usually spreads slowly, it “moves rapidly with groundwater and can render groundwater unpotable at low levels,” according to the EPA. The company installed a groundwater treatment system in June 2022.
Now Colonial is considering installing an aeration unit at the catchment pond to remove the MTBE before it reaches the outfall.
There have been 12 reported petroleum spills at the tank farm since the 1980s, according to state records.
MTBE has contaminated groundwater and drinking water supplies throughout the U.S., prompting many states to ban its use. North Carolina lawmakers banned the use of MTBE in gasoline in 2008. However, it is legal to transport fuel containing MTBE through the state, such as via pipeline, rail or truck.
NC Newsline is part of States Newsroom, a nonprofit news network supported by grants and a coalition of donors as a 501c(3) public charity. NC Newsline maintains editorial independence. Contact Editor Rob Schofield for questions: info@ncnewsline.com. Follow NC Newsline on Facebook and Twitter.
Our stories may be republished online or in print under Creative Commons license CC BY-NC-ND 4.0. We ask that you edit only for style or to shorten, provide proper attribution and link to our web site. Please see our republishing guidelines for use of photos and graphics.
Assistant Editor and Environmental Reporter Lisa Sorg helps manage newsroom operations while covering the environment, climate change, agriculture and energy.
NC Newsline is a Raleigh-based nonpartisan, nonprofit newsroom dedicated to fearless reporting and hard-hitting commentary that shines a light on injustice, holds public officials accountable, and helps improve the quality of life throughout North Carolina.
DEIJ Policy | Ethics Policy | Privacy Policy
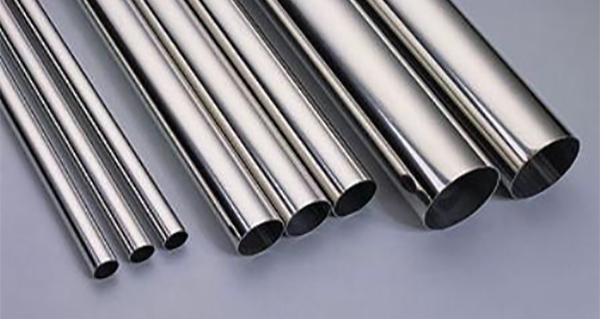
Stainless Steel Cleaning Tube Our stories may be republished online or in print under Creative Commons licence CC BY-NC-ND 4.0. We ask that you edit only for style or to shorten, provide proper attribution and link to our web site.